
книги / Синергетика и усталостное разрушение металлов
..pdfАи*,Дж/мм3
Рис. 4. Изменение критической плотности внутренней энергии Ли,в зависимостиот мощности шлифования W
1 —сталь УвА,2 —чугун СЧ18-36,3 —сталь 40Х,4 —бронза ОЦСЗ-12-6,3 —латунь Л-68,6 —алюминиевый сплав АО9-2
ГДв |
, № , |
г |
, |
ч |
|
|
|
Г |
Uo(pa,T) |
1 |
(37) |
||
л'г-л г К1’-г>«р[- |
„ |
Ч |
||||
|
||||||
Ul(?a,Т)= U'a +AU'(T)+?y- - у'о\ , |
(38) |
|||||
/-* * (-* - ±—). M r-— - |
|
(39) |
||||
|
, |
9 / |
So. |
|
|
На рис. 1представлены кинетические кривые изменения в деформи руемых объемах образца плотности скрытой энергии стали 45 в отож женном состоянии. Аналогичные кинетические кривые получены для других исследований сталей и режимов ихтермообработки.
Анализ этих данных показывает,что процесс накопления скрытой энер гии Аие, а следовательно, и повреждаемости материала во времени про текает с переменной скоростью ие и носит затухающий характер, что на ходится в хорошем соответствии с кинетическим уравнением повреж
даемости (10).
41
Таблица 3 Значениятермоактивационныхпараметров усталостного разрушения для стали
Материалы,термическая обработка |
А0• 1(Га, |
U'ot МДж/м3 |
У • м*. |
|
МВт/м3 |
15983 |
мм4/кгса |
Сталь40Х,отжиг |
6,323 |
0,721 |
|
Сталь45, |
0,703 |
16546 |
1,365 |
отжиг |
|||
закалка |
0,0268 |
17718 |
0,578 |
Сталь 25,отжиг |
0,161 |
16932 |
1,724 |
Всвязи с этим представляют интерес экспериментальные зависимос ти скорости изменения в деформируемых объемах образцов йе от ве личины текущих значений изменения плотности скрытой энергии Аие. Графики этих зависимостей для сталей 45 и 40Х в отояокенном состоянии представлены в координатах йе -Аие (рис. 5,д, б) и lntie—Аие (рис.5,а , б) соответственно. Анализ этих графиков, а также аналогичных графи ков для других исследованных материалов показал, что они хорошо опи сываются кинетическими уравнениями повреждаемости (10), (33) и (34). Анализ графиков показывает, что в полулогарифмических коор динатах lniiе—Аие (см. рис. 5,а,б’) экспериментальные данные хоро шо укладываются на веер прямых, угол наклона которых к оси Аие за висит от амплитуды напряжений и температуры образцов, с увеличением которых наклон прямых уменьшается, что находится в хорошем соот
ветствии с кинетическими уравнениями (10), (35), (36). Сцельюопределения параметров кинетического уравнения (36) экспе
риментальные данные, представленные для сталей 45 (см. рис. 5,д,а') и 40Х (рис. 5,б,б'), а также аналогичные данные для других материалов, подвергнуты статистической обработке по методу наименьших квадратов.
Результаты статистического анализа экспериментальных данных [3] с использованием кинетического уравнения повреждаемости (36) (см. рис. 5 и табл. 3) позволяют произвести оценку активационных парамет ров процесса усталостного разрушения исследованных металлов. При
квазиизотермическом рассмотрении процесса (Г = 0О= const) пара метр Ав уравнении (36) зависит от амплитуды напряжений и темпера туры и хорошо описывается экспоненциальной зависимостью от квад рата амплитуды напряжений
А(оа,Г)=Л0ехр(у'оI).
Анализ этих данных показывает, что для исследованных сталей в отож женном состоянии значения энергии активации процесса усталостного раз рушения изменяютсяв сравнительно узких пределах (U0 = 15 157— 16 106 МДж/м3) и близко совпадают с универсальным энергетическим параметром для Feyq = 15 235 МДж/м3 (26 227 кал/г-атом), предложен ным в работе [10], и хорошо коррелируют с энергией активации образова ния вакансий [11, 12]. Параметр у1изменяется при этом в широких преде
лах у = (0,721-1,724)102в зависимости от физико-химической природы и структуры сплава.
42
Рис. 5. Зависимость скорости йе накопления в деформируемых объемах образцов из стали 45 (а, а1) и стали 40Х(б, б1) скрытой энергии от текущих значений измене ния плотности скрытой энергии Аие и амплитудынапряжений аа
При аа, МПа: а,а1\1 - 253, 2 - 240, 3 - 239, 4 - 281, 5 - 225;б,б : 1- 289, 2 - 387,3 - 270,4 - 264,5 - 238,6 - 250
Если рассматривать процесс усталостного разрушения неизотермическим и учитывать при статистическом анализе экспериментальных данных тем пературу разогрева материала Д7у, то полученные по уравнениям (36), (37) значения энергии активации процесса U'0(oa, Т) существенно зависят от температуры Ту и амплитуды циклических напряжений оа. При этом для всех исследованных сталей наблюдается возрастание энергии активации процесса усталостного разрушения с увеличением амплитуды циклических напряжений. При низких напряжениях, близких к величине предела вы носливости, когда температура разогрева материала ATfстремится к нулю, значения энергии активации процесса усталостного разрушения исследо ванных сталей становятся минимальными и по своей величине близко совпадают с энергией активации разрыва (диссоциации) межатомных свя-
43
зей для чистого железа U0 = £>„/4 = 13 650-14380 МДж/м3 (23,5— 24,75 ккал/моль), что хорошо согласуется с теоретическими представле ниями,изложенными в работе [3] (где D0 - энергия сублимации).
Была также произведена оценка активационных параметров процесса усталостного разрушения сталей по феноменологической зависимости долговечности образцов от амплитуды циклических напряжений [3]. Ана лиз полученных результатов показал, что для исследованных сталей значе ния энергии активации процесса повреждаемости Uq в этом случае изме няются в пределах 17 037-20 137 МДж/м3и хорошо совпадают с энергией активации образования вакансий в железе и его сплавах 18 700—
19 720 МДж/м3 (23,8-34,0 ккал/г-атом) [13].
Анализ результатов оценки эффективных значений энергии активации
процесса повреждаемости и усталостного разрушения конструкционных сталей двумя независимыми методами свидетельствует о том, что в иссле дованном диапазоне условий процесса (в0 = 293К,область многоцикловой усталости) основным механизмом, контролирующим повреждаемость и усталостное разрушение сталей,является вакансионный.
Полученные результаты также свидетельствуют о том, что в процессе циклических деформаций в материал закачивается избыточная энергия, которая аккумулируется в деформируемых объемахв виде возбужденных атом-вакансионныхсостояний [1].
Совпадение численного значения критической плотности внутренней энергии ы* с энтальпией плавления, а также вакансионный механизм зака чивания энергии деформации свидетельствуют также о том, что в локаль ных объемах материала, ответственных за разрушение, металл находится в квазиаморфном состоянии, а между процессами механического разру шения и плавления металлов и сплавов существует структурно-энергетиче ская аналогия.
ЛИТЕРАТУРА
1.Панин В.Е., Егорушкин В.Е.,Хон ЮЛ., Еасукова Т.Ф.Атом-вакансионные со стоянияв кристаллах //Изв.вузов.Физика.1982.№12.С 5-28.
2. Федоров В.В. Термодинамические аспектыпрочности и разрушения твердых тел.Ташкент:Фан,1979.186 с.
3. Федоров В.В.Кинетика повреждаемости и разрушения твердых тел. Ташкент: Фан,1985.167 с.
4. Федоров ВЯ. Эргодинамическая концепция прочности и разрушения твердых тел ЦМатериалыVI Всесоюэ.съезда по теорет.и прикл.механике.Ташкент: Фан,
1986.С 610-611.
5.ПланкМ.Принципсохраненияэнергии.М.;Л.:ГОНТИ,1938.235 с. 6.УмовН.А.Избранные сочинения.М.:Изд-во АНСССР,1950,151 с.
7. Иванова В.С.Структурно-энергетическая теория усталости металлов // Цикли ческаяпрочностьметаллов.М.:Изд-во АНСССР,1962.С 11-12.
8.ИвановаВ.С.Усталостное разрушение металлов.М.:Металлургиздат,1963.272 с. 9. Федоров В.В., Хачатурьян С.В., Коршунов ВЯ. Исследование взаимной связи закономерностей износа металлов с энергетическими характеристиками процесса
внешнего трения.//Вести.Всесоюэ.науч-исслед.ин-та ж.-д.трансп.1977.№14.
10. Осипов К.А.Вопросытеории жаропрочности металлов и сплавов. М.: Метал лургия,1975.285 с.
И. Новиков И.И. Изв.АНСССР.Металлы.1976.№4.С.172-174. 12.Дехтяр ИЯ. ИИзв.вузов.Физика.1958.№5.С.81-89.
13. Криштап М.А. Механизмдиффузии в железных сплавах. М.: Металлургия,
1972.399 с.
УДК621.539.212
АМОРФИЗАЦИЯ КРИСТАЛЛИЧЕСКИХ МАТЕРИАЛОВ ВЗОНЕ ПЕРЕД ВЕРШИНОЙРАЗВИВАЮЩЕЙСЯ ТРЕЩИНЫ
А.А. Тутнов,В.М.Доровский,Л.А.Елесин
Исследованиям механизмов зарождения и распространения микро трещин при деформировании металлов посвящено большое число работ. Однако до настоящего времени не найдено объяснение некоторым физи ческим процессам, предшествующим появлениюв материале субмикро трещин (СМТ) и скачкообразному подрастаниюмикротрещин.
Как известно, в пластичных материалах рост микротрещин происходит за счет слияния с образующимися передихфронтом СМТ [1]. Согласно существующим представлениям о механизмах разрушения.пластичных металлов, образование СМТ происходит по<ре достижения в локальных областях пороговой концентрации дислокаций. Это противоречит экспери ментальным данным последних лет, согласно которым до начала продви жения трещины перед ее вершиной возникает зона, свободная от дислока ций, а затем появляются СМТ [2-5]. Данная статья посвящена изучению указанной бездиспокационной зоны.
Методика эксперимента. Исследования микропроцессов разрушения проводились на электронном микроскопе Темскан-lOOCX. Исследуемые образцы деформировались в колонне электронного микроскопа. Впроцес се деформирования велась видеозапись и фотографирование зоны перед фронтом микротрещины. Использовались образцы,полученные электроли тическим утонением массивных заготовок и вакуумным напылением ис следуемого материала на кристаллы каменной соли. Впервом случае цен тральная часть пластинчатого образца с помощью электрополировки утоня лась до толщины, обеспечивающей прозрачность этого участка для элек
тронов с энергией 100 кВ.
Образцы другого типа, полученные напылением на кристалл,отделялись от последнего в ванночке с дистиллированной водой такимобразом,чтобы образец удерживался поверхностным натяжением на зеркале воды. Затем он вылавливался на специальнуюподложку, имеющую отверстия в зоне предполагаемого разрыва образца. Подложка была необходима для пред отвращения повреждений образца пинцетом. Вместе с подложкой образец помещался в приставку для деформирования. Толщина напыленныхобраз цов, а также утоненной части образцов из массивных заготовок составляла
0,1—0,3 мкм.
Полученное видеоизображение обрабатывали, измеряя размеры микро трещины, расстояние от вершины до ближайшей зародышевой СМТ, расстояние между СМТ.Наряду с этимопределялись кристаллографические направления распространения СМТ. Сэтой цельюфотографировали верши
ну СМТ в режиме ”SA-mag”. Вэтом режиме, согласно инструкции,отсут ствует разворот относительно эпектронограммы. При съемке на экран вводили репер-метку. Далее с этого участка снимали электронограмму
в присутствии той же метки.
Полученную ,электронограмму расшифровывали, используя методы,
45
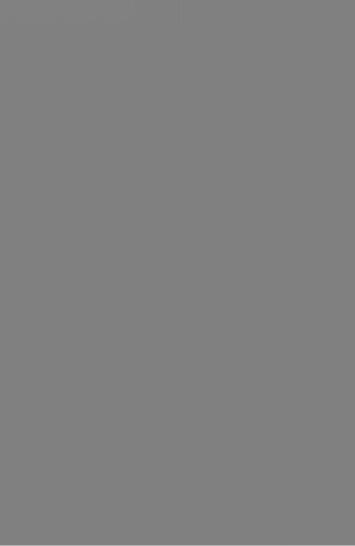
Таблица 1 Результатыизмерения длиныберегов субмикротрещины,мкм
СМТ |
Светло- |
Темнопольныизображения в рефлексах |
|
|||||
|
польное |
200 |
002 |
131 |
131 |
131 |
131 |
004 |
|
изобра |
|||||||
|
жение |
|
|
|
|
|
|
|
Длина берегов |
0.727 |
0,729 0,724 0.750 |
0,749 |
0,725 |
0,729 |
0,745 |
темнопольные и светлопольные изображения,можно получить дополнитель нуюинформацию о зонах в районе СМТ.Спомощьюрежима микродифрак ции можно получить электронограмму с участка образца около СМТ и микротрещины в центральном и дифрагированных пучках. Рассмотрим подробно результаты таких электронно-микроскопических исследований области передвершиной микротрещины в образцах из алюминия.
На рис.2 приведены электронные микроскопические фотографии верши ны микротрсщины в светлопольноми темнопольномизображениях.Темно польное изображение получено путем выведения в центр диффузионного кольцевого рефлекса с помощью наклона осветительной системы.Дифраги рованный пучок выбирался по электронограмме с таким расчетом,чтобы темнопольное изображение формировалось в одном из рефлексов матрицы.
Спомощью курвиметра были измерены длины берегов микротрещины (между характерными ее точками) в светлом и темном полях. Разница между длинами берегов микротрещины составила 0,012-0,014 мм.Профи ли микротрещины в темном и светлом полях, наложенные друг на друга, показаны на рис. 3. Втабл. 1приведены результаты измерений длины бере гов СМТ между двумя характерными точками на светлопольном и темно польном изображениях в различных рефлексах участка образца,содержа щего СМТ после выдержки образца под нагрузкой в 1ч.
Как видно из табл. 1, отличие в линейных размерах на изображениях СМТ в светлом и некоторых темных полях достигает ~3%.Вто же время пятикратное повторение съемки в одном и том же рефлексе не дает воз
можности обнаружить различия в профилях трещины на разных негативах. Это позволяет отклонить колебания напряжений в электросети как воз можную причину отличия размеров СМТ от снимка кснимку.Характерно, что чем.дальше рефлекс от центра пучка, тем большими оказываются раз меры изображений СМТ в темном поле. Полученный результат можно объ яснить эффектом аморфизации материала вокруг СМТ.
На рис. 4, б представлена электронограмма с участка образца, содержа щего вершину микротрещины после выдержки образца при постоянной нагрузке в течение 50 ч. Если выделить с помощью апертурной диафрагмы область у вершины микротрещины, в несколько раз меньшую, чем в пре дыдущих случаях, то на электронограмме появляются размытые дифрак ционные кольца, присущие либо чрезвычайно мелкозернистым, либо аморфным материалам (см. рис.4, б). Одновременное присутствие на элек тронограмме точечных рефлексов может быть связано с тем,что полностью отделить область аморфного материала от поликристаллических областей не удается, так как для этого потребовалось бы применить диафрагмы
47
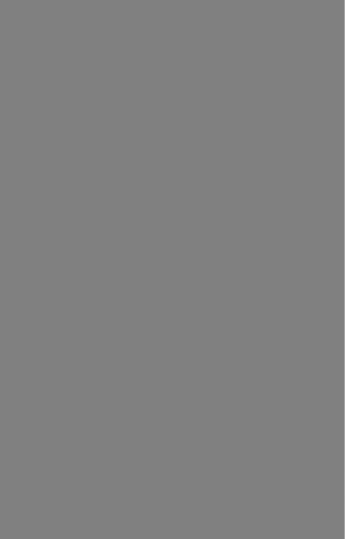
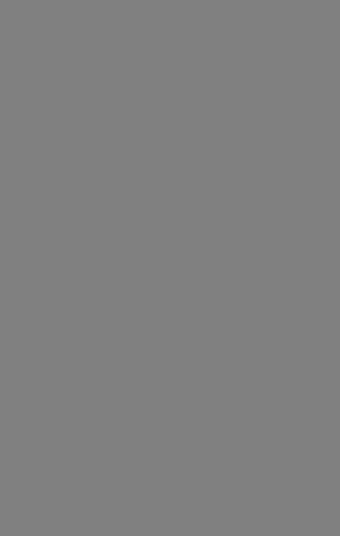
них точечных рефлексах матрицы изображение субмикротрещины может иметь большую длину, чем на светлопольном изображении. Это под тверждается результатами измерения длины субмикротрещины по темно
польным изображениям (см.табл. 1).
Получив темнопольное изображение в кольцевых дифракционных
отражениях, можно разграничить области, дающие те или иные кольца. На рис. 5 представлены темнопольные электронно-микроскопические фотографии вершины микротрещины и области, примыкающей к ней, снятые в дифракционных кольцевых отражениях внутреннего, среднего
и внешнего кольца. На темнопольных изображениях, сформированных таким образом, светлой будет часть образца, дающая конкретный дифрак ционный рефлекс, а сама микротрещина и другие части окажутся темны
ми и серыми.
Как видно на рис. 5, а, дифракционное внутреннее размытое кольцо определяется вкладом небольшой области у места, откуда начала прорас тать микротрещина. Среднее, более резкое кольцо формируется мелкими кристаллитами (размером < 0,015 мкм), располагающимися в вершине микротрещины, затянутой тонкой пленкой. Внешнее кольцо формируется областью, непосредственно примыкающей к берегам микротрещины. Гра ницы этой области удалены от микротрещины на расстояние до 1мкм.Тон кая пленка непосредственно в вершине микротрещины также дает светлое поле и,следовательно, формирует внешнее кольцо.
К сожалению, ввиду ограниченности минимального размера диафрагмы объектива электронного микроскопа и малой яркости дифракционных колец на электронограмме не удалось более четко разделить темнопольные
изображения от каждого кольца отдельно. Поэтому не исключено, что при наклоне осветительной системы для получения темнопольного изображения в поле зрения диафрагмы линзы объектива попадало не одно кольцо или диафрагма захватывала часть рефлекса от матрицы.
Тем не менее можно сдостаточной уверенностью сказать,что диффузные кольцевые рефлексы на электронограмме соответствуют областям материа ла, расположенным непосредственно у вершины микротрещины (на рас стоянияхдо 1мкм).
Следует отметить, что зоны утонения, в которых зарождаются СМТ, для разных материалов имеют существенно различные размеры. Так, в
циркониевых и алюминиевых сплавах некоторых марок сталей ширина зоны утонения составляет 5-10% от ее длины в направлении роста трещины. Внержавеющей стали 0Х16Н15МЗБ соотношение между шири ной и длиной утоненной зоны перед микротрещиной близко к 1:100.
На рис. 6 представлена электронограмма, полученная с участка сталь ного образца вблизи вершины микротрещины, на которой присутствует размытый рефлекс. Это может быть объяснено только образованием в вер шине микротрещины аморфных участков.
На рис. 7 представлена рассчитанная электронограмма. Направление стрелки соответствует кристаллографическому направлению (002).
После увеличения общей деформации микротрещина изменила направле ние распространения на 45° (рис. 8). Произошло это следующим образом. При дополнительном увеличении деформации образовалась новая утонен ная зона, расположенная под углом 45° к направлению движения перво-
50