
книги / Прогнозирование долговечности и диагностика усталости деталей машин
..pdfпроисходить в основном из-за усталостного разрушения штуцеров.
С ростом числа нагружений вероятность неразрушения уменьшается, достигая в пределе для штуцеров 0,979, а для соединений 0,970. Это обусловлено тем, что с ростом числа нагружений среднее значение разрушаю^ щих напряжений для элементов снижается (см. рис. 3.35), достигая величин средних значений пределов выносливо-
Рис. 3.36. Зависимость вероятности неразрушения от числа нагру жений штуцеров (J) и соединений В-Г91-11 (2) при вибрации тру бопроводов в линии управления гидроагрегатов ПА-476
сти. Предельные значения вероятностей неразрушения характеризуют надежность соединений и их элементов при длительной эксплуатации прессов.
Второй случай. Рассмотрим случай вибронагружения соединений с изменяющимися во времени параметрами цикла на примере расчета соединений В-Г91-15 в магист рали обратного хода ползуна пресса ПД-476. При анали зе используем результаты регистрации нагруженности штуцера и результаты испытаний (см. табл. 3.7) штуце ров из стали 35 и ниппелей из стали 20.
Распределение напряжений во времени в опасном се чении ввертной части штуцера описывается экспонен-
191
-цйалыюй функцией с параметрами сгМакс=73,6 МПа, <7мин=6,87 МПа, (Тс=9,53 МПа. Рассматривая соединение в сборе, по нагруженности штуцеров можно определить распределение во времени напряжений в опасных сече ниях ниппелей. Оно также описывается экспоненциальной
функцией с |
параметрами сгМакс= 38,7 МПа, аМш= |
= 3,63 МПа, <тс=5,00 МПа. |
|
Результаты |
испытаний дают следующие параметры |
уравнения кривой усталости для штуцеров: v = 50,5 МПа,
<тг=262 МПа, No=431 тыс. циклов, огк=5,83 МПа. Ко нечное значение предела выносливости при сг=сгМакс определено с использованием уравнения (6). Довери тельные интервалы для параметров распределения зна чений предела выносливости с доверительной вероят ностью 0,99 для среднего значения составляют 240—
.284 МПа; для квадратичного отклонения 27,3—59,8 МПа. Параметры уравнения кривой усталости для ниппелей
о0=74,5 МПа, стг=94,4 МПа, М0=314 тыс. циклов, агк= =2,94 МПа. Доверительные интервалы параметров рас пределения значений предела выносливости ниппелей с
.доверительной вероятностью 0,99 для среднего значения равны 86,8—102 МПа; для квадратичного отклонения 5,79—19,1 МПа.
Приведенная информация о нагруженности и вынос ливости элементов соединений дает возможность характе ризовать вероятность неразрушения соединений в про цессе эксплуатации. Когда действующие напряжения по величине меньше пределов выносливости, элементы соединений не повреждают*»: При рассеянии значений пределов выносливости час'1 ~ элементов имеет значения предела выносливости выше максимального значения дей ствующих напряжений. Эту часть в процентах можно ха рактеризовать исходя из квантили нормального распре деления
+ _ °макс |
ОУ min |
• |
1 |
с |
|
|
‘-’max |
|
Для штуцеров вероятность |
неразрушения при неограни |
ченно большом числе циклов вибронагружения, найден ная по приведенной выше формуле, равна 0,9974, для ниппелей — 0,9941, а для соединений — произведению этих вероятностей, или 0,9915.
Следовательно, не менее 99,74% штуцеров, 99,41%
192
ниппелей или 99,15% соединений в целом в анализируе мых условиях нагружения не будет разрушаться от ви брации в течение всего времени эксплуатации прессов.
Чтобы характеризовать безотказность соединений и их элементов в широком диапазоне работы прессов, используем уравнение (15). При этом учитываем, что конечные значения пределов выносливости штуцеров и ниппелей I ниже минимального значения действующих
Рис. 3.37. Зависимости вероятности неразрушения от числа рабо чих ходов прессов для штуцеров (1), ниппелей (2) и соединений В-Г91-15 (3)
напряжений. Поэтому повреждающими будут все напря
жения в диапазоне от crMai --до ампн.
На рис. 3.37 с исполь.. анием уравнения (15) пред ставлены зависимости вероятности неразрушения соеди нений от числа рабочих ходов пресса для штуцеров и нип пелей. Так как усталостные повреждения этих элементов являются независимыми событиями, вероятность нераз рушения соединения В-Г91-15 после фиксированного чис ла рабочих ходов пресса определяется произведением вероятностей неразрушения штуцеров и ниппелей. Из графика следует, что анализируемое соединение обладает достаточно высокими показателями безотказности и дол говечности. Однако для обеспечения' таких показателей необходимо, чтобы характеристики сопротивления уста лости элементов были не ниже указанных в табл. 3.8. Кроме того, из уравнения (15) следует, что ресурс соеди-
13. Зак. 1797 |
193 |
нений существенным образом зависит от максимальных напряжений экспоненциального блока нагрузок. В связи с этим при сборке трубопроводов необходимо контроли ровать уровень вибраций с тем, чтобы напряжения в опасных сечениях элементов соединений не превышали максимальных расчетных. Так, в данном случае для шту церов максимальные напряжения не должны превышать 73.6 МПа, а для ниппелей они должны быть не более 38.7 МПа.
3.4.ИСПЫТАНИЯ НА УСТАЛОСТЬ
ИПРОГНОЗИРОВАНИЕ ДОЛГОВЕЧНОСТИ
АВТОМОБИЛЬНЫХ РЕССОР
Анализ результатов эксплуатационных наблюдений за отказами несущих систем автомобилей семейства МАЗ500 показал, что узлами, наиболее лимитирующими на дежность автомобиля, особенно автомобиля-самосвала, являются листовые рессорные подвески. В сравнении с другими типами листовые рессорные подвески менее сложны по конструкции и более технологичны, имеют относительно невысокую стоимость изготовления и тре буют небольших затрат на текущее обслуживание. Все это определило широкое применение листовых рессорных подвесок на большинстве современных грузовых авто мобилей.
Существенным недостатком рессорных подвесок явля ется значительная металлоемкость. Так, например, для ГАЗ-51А [187] масса комплекта рессор составляет 12% от массы всех металлических деталей автомобиля. Вто рым существенным недостатком подвесок является их невысокая надежность по условию прочности. В сочета нии со значительной относительной продолжительностью движения автомобилей по дорогам второй и третьей категории '[«185—193] этот недостаток становится причи ной частых отказов и значительных затрат на ремонт авто мобилей. Так, за амортизационный срок в 8 лет автомо биль ГАЗ-51 А требует использования пяти комплектов рессор |[|187]. При этом только общие затраты рессорной стали на один автомобиль составляют 8 кН. Средняя на работка на отказ для передних рессор ГАЗ-51А порядка 32 тыс. км, а для задних 66 тыс. км.
Исследования [,187] показывают, что более 10% от
194
казов и неисправностей и до 8% стоимости ремонта гру зовых автомобилей приходится на их подвески и на за пасные части, для рессор расходуется более половины рессорной полосы, поставляемой для автомобильной промышленности. Для автомобилей завода им. Лихачева в опорных автохозяйствах Москвы получены следующие данные ,[(187] о средней наработке подвесок на отказ за пробег 250 тыс. км: бортовой автомобиль ЗИЛ-130—
15.5тыс. км; автомобиль самосвал ЗИЛ-ММЗ-555 —
12.5тыс. км.
Исследования, проведенные Белорусским научно-ис следовательским технологическим институтом автомо бильного транспорта и Институтом проблем надежности и долговечности машин АН БССР, выявили значительное число отказов подвесок автомобилей Минского автозаво да в условиях эксплуатации. Особенно много отказов у подвесок автомобилей-самосвалов. Так, например, у ав томобилей-самосвалов МАЗ-503 на подвеску приходится 23,4%, а у MA3-503A — 24,7%’ от всех отказов, в то время как на двигатель приходится 13% отказов, а удельный вес отказов других узлов еще меньше. Средняя наработка на отказ для задних подвесок автомобилей MA3-503A в Белоруссии составляет 52,93 тыс. км.
Основной причиной отказов подвесок автомобилей является усталостная поломка рессорных листов. Значи тельно меньшее число отказов происходит из-за поло мок кронштейнов крепления рессор, центровых болтов и т. д. Следовательно, листовые рессорные подвески отече ственных грузовых автомобилей (ГАЗ, ЗИЛ, МАЗ) лими тируют надежность машин и требуют совершенствования конструкции, технологии изготовления и методов инже нерной отработки.
Работоспособности подвесок автомобилей уделяется значительное внимание {,185—193]. Однако описанное выше состояние вопроса говорит о необходимости даль нейшего развития исследовательских работ примени тельно к подвескам автомобилей и в первую очередь исследований, направленных на повышение их надеж ности.
Ниже на примере задней подвески автомобиля-само свала MA3-503A рассматривается метод исследования долговечности листовых рессорных подвесок.
195
13*
3.4.1. Испытания на усталость рессорных листов
Как показывает анализ результатов эксплуатацион ных наблюдений, основной причиной отказа подвесок у автомобилей-самосвалов MA3-503A является усталостная поломка рессорных листов. При этом более половины всех отказов подвесок происходит из-за усталостных разрушений листов задней подвески.
Чтобы получить информацию, необходимую для оцен ки фактической нагруженности и расчета ресурса рессор, были проведены испытания рессорных листов на уста лость. Испытания велись на универсальной машине ГРМ-1 с частотой нагружения 6,67 Гц. Конструкция мо дели рессоры (рис. 3.38) определялась возможностями испытательной машины и состояла из десяти листов серийной задней основной рессоры. Материал листов — сталь 60С2. Листы скреплялись центровым болтом и стя гивались через накладки и прокладки болтами для вос произведения затяжки рессоры на автомобиле стремян ками.
Разрушение листов наблюдалось в зоне их выхода из-под накладок. Испытания велись до разрушения одно го из десяти листов, т. е. до фиксированной степени по вреждения. Напряжения, действовавшие в опасных в смысле усталости зонах, оценивались с помощью тензорезисторов.
Партия из девяти объектов испытаний была разделе на на две группы. Первая группа (шесть моделей) испы тывалась при коэффициенте асимметрии цикла нагрузок 0,3 и снижении максимальной нагрузки в диапазоне 220— 160 кН от объекта к объекту. Результаты испытаний этой
Рис. 3.38. Модель рессоры и схема ее нагружения
196
группы были использованы для определения параметров уравнения кривой усталости. Вторая группа (три модели) испытывалась при коэффициенте асимметрии цикла на грузок 0,235 и максимальной нагрузке 167 кН. Эти ре зультаты применяли для оценки чувствительности мате риала рессорных листов к асимметрии нагружения.
Схема эксперимента с соблюдением постоянства коэф- . фициента асимметрии по нагрузкам определялась сило-
Рис. 3.39. Кривые усталости задних рессор MA3-503A: / — серий ный вариант (/ — первые поломки натурных конструкций; II — последующие поломки; III — поломки моделей); 2 — рекомендуе мый вариант (IV — первые поломки; V — последующие поломки)
измерительным устройством универсальной испытатель ной машины. Для перехода от нагрузок к напряжениям в опасных зонах была проведена статическая и динамиче ская тарировка, которая показала нелинейность зависи мости напряжения от вертикальной силы. При оценках напряжений учитывалась также предварительная затяж ка рессорных листов, имеющих различную кривизну до сборки, стяжными болтами.
Кроме испытаний на ГРМ-1, проведены усталостные испытания задних рессор в сборе с подрессорниками, кронштейнами и элементом рамы на специальном стенде, описание которого дано в подпараграфе 3.4.2. Испытания велись при высоких уровнях нагрузки, близких к пробою рессоры. Регистрировался выход из строя первого и по следующих листов рессоры. При обработке результатов испытаний учитывались фактические коэффициенты
197
асимметрии нагружения разрушившихся рессорных листов и результаты испытаний приводились к отнулевому циклу.
Обработка результатов проводилась с использованием методик, изложенных в гл. 2. Получены следующие ха рактеристики сопротивления усталости серийных рессор заднего моста_ автомобиля МАЗ: N0—420 тыс. циклов,
i> o= 313 МПа, о о = 3 6 1 МПа, 'ij)a=:0,33.
На рис. 3.39 представлена первичная кривая устало сти серийных рессор при коэффициенте асимметрии, рав ном нулю, и вероятности разрушения 0,5.
3.4.2. Исследования нагруженности рессорных листов
На подвеску автомобиля в дорожных условиях дейст
вуют:
вертикальные силы, создаваемые массой подрессорен ной части автомобиля вместе с грузом и вертикальными колебаниями подрессоренных и неподрессоренных масс; скручивающие моменты, создаваемые колебаниями относительно продольной оси автомобиля подрессорен
ных и неподрессоренных масс; продольные силы и реактивные моменты, возникаю
щие при разгонах, торможениях и движении на подъемах и спусках;
поперечные силы, возникающиепри изменении на правления движения и движении по дорогам с попереч ным уклоном.
Для оценки сил и моментов, действующих на подвеску автомобиля-самосвала MA3-503A в дорожных условиях, были проведены испытания автомобиля без груза, с по ловиной номинальной нагрузки (40 кН) и с полной на грузкой (80 кН ). Исследованы режимы прямолинейного движения по асфальтобетону, булыжнику и в карьере при разных скоростях, а также повороты, разгон, торможение, переезд единичных препятствий, погрузка и разгрузка.
Раздельная регистрация сил и моментов производи лась с помощью специальных динамометрических опор и кронштейнов. Передняя и задняя рессоры правой сторо ны автомобиля с помощью динамометрических опор крепились к картеру заднего моста и балке переднего моста, а с помощью динамометрических кронштейнов_к раме автомобиля.
198
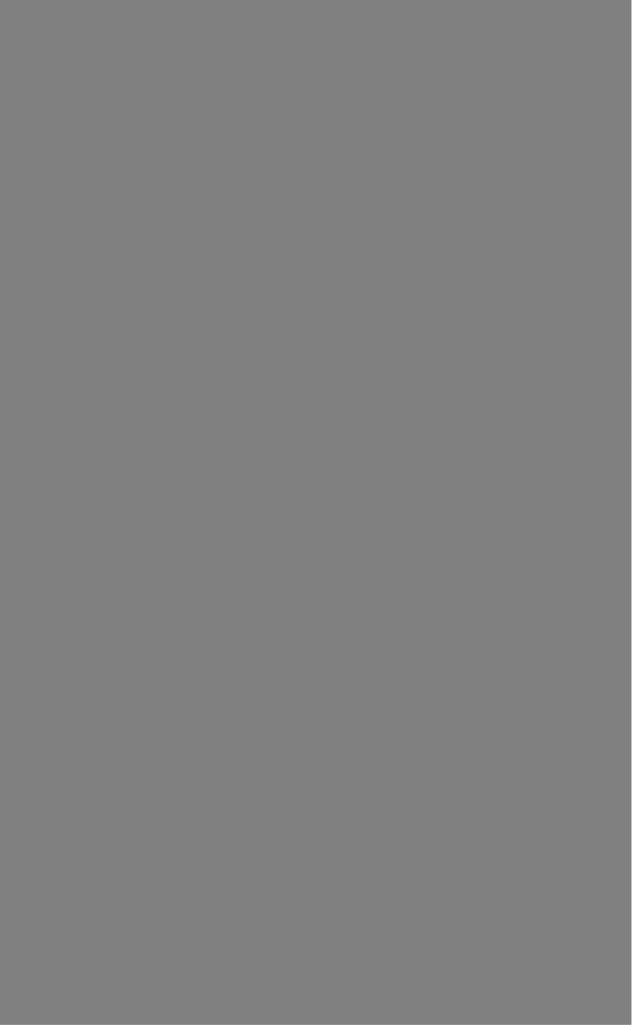
При вертикальном положении и одинаковом давле нии в цилиндре рессора нагружается только вертикаль ной нагрузкой. Продольные силы создаются поворотом цилиндров на угол а, а скручивающие моменты — раз ными по величине давлениями в цилиндрах.
На рис. 3.41 показано распределение продольных напряжений в коренном листе рессоры при действии вертикальных нагрузок. По оси абсцисс отложено рас-
Рис. 3.41. Распределение продольных напряжений в коренном лис те основной рессоры: 1 — при отсутствии внешних сил; 2 — при номинальной статической нагрузке (50 кН); 3 — при максималь ном прогибе рессор
стояние от ушка рессоры до точки регистрации напря жения. Крайние правые точки соответствуют выходу коренного листа из-под прокладки. Напряжение в ко ренном листе возникает при сборке листов рессоры, имеющих разную кривизну, за счет того, что кривизна коренного листа меньше кривизны более коротких ли стов.
Анализ графика показывает, что если принять напря жения от номинальной статистической нагрузки за средние, а напряжения при максимальном прогибе за максимальные напряжения цикла, амплитуда напряже ний по длине рессоры от ушка к прокладке будет расти до 363 МПа. Максимальное значение амплитуды дости гается на расстоянии порядка 400—450 мм от ушка и не изменяется до прокладки. Среднее напряжение цикла сначала растет, а затем с расстояния 400—450 мм от ушка уменьшается. Исходя из влияния асимметрии на гружения на выносливость рессорной стали, молено сде
200