
книги / Прогнозирование долговечности и диагностика усталости деталей машин
..pdfу поверхности, что ограничивает контроль небольшими глубинами залегания трещин.
В процессе регистрации представляет интерес анализ показаний токовихревых датчиков с разложением вих ревого сигнала в гармонический ряд. Так, предлагается [197] анализировать первую, третью, пятую и седьмую гармоники и использовать первую гармонику для регистрации роста усталостной трещины, седьмую гармонику для регистрации момента образования устойчивых полос скольжения, а третью и пятую — для регистрации момента пересечения полосами скольжения границ зе рен металла.
Для диагностирования усталости могут быть исполь зованы акустические методы [194] регистрации ульт развуковых волн (от 2-104 до 109 Гц): эхо-импульсный и эмиссионный. При использовании эхо-импульсного ме тода возбуждение и регистрация ультразвуковых коле баний осуществляются с поверхности детали одной ис кательной головкой. Изучаемые зондирующие импуль сы упругих волн, оставив след на экране регистрирую щей электронно-лучевой трубки, проходят через деталь и отражаются от противоположной поверхности (донный импульс на экране) или от внутренней несплошности (импульс на экране от дефекта). Подбором угла ввода ультразвуковых волн и перемещением искательной го ловки определяется не только положение, но и протя женность несплошности материала детали.
Основными достоинствами метода являются незави симость от электромагнитных свойств материала дета ли, возможность контроля усталостного повреждения деталей без демонтажа и разборки узлов машин и большая проникающая способность зондирующих им пульсов. Применение метода не опасно для обслужива ющего персонала. К его недостаткам следует отнести повышенные требования к шероховатости и отсутствию загрязненности поверхностей, контактирующих с иска тельными головками, а также возможность существо вания незондируемых зон.
Чувствительным спутником усталости является аку стическая эмиссия — упругие волны, генерируемые про цессами деформации и локального разрушения [198— 200]. Основной трудностью при регистрации акусти ческой эмиссии процесса усталости является отделение
14* |
211 |
|
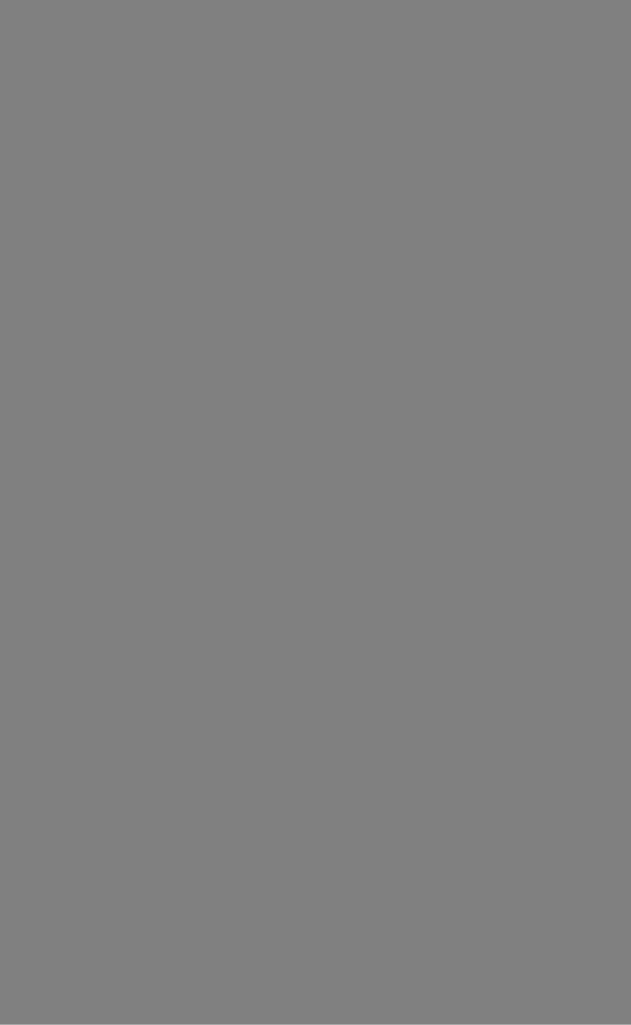
цию. Отработка проводится с целью уточнения конст рукции средств регистрации и технологии измерений, а при необходимости и тарировки средств регистрации; изучения особенностей распространения усталостных трещин в контролируемых деталях; разработки методи ки анализа информации о процессе усталости контро лируемых деталей.
В качестве примера рассмотрим отработку акустиче ского метода диагностирования усталости листов зад ней рессоры автомобиля-самосвала Минского автозаво да [2 0 1 ].
Из рассмотренных в подпараграфе 4.1.1 методов с учетом необходимости контроля листов в условиях ав тохозяйств без демонтажа и разработки рессоры наибо лее приемлемым оказался акустический ультразвуковой контроль. Для обнаружения и регистрации степени пов реждения отработан эхо-импульсный метод с использо ванием дефектоскопа ДУК-6 6 П. Отработка проводилась на стенде (см. параграф 3.4), моделировавшем крепле ние рессоры к раме и заднему мосту автомобиля, а так же схему нагружения рессоры в условиях эксплуатации.
Для ввода импульсов ультразвуковых колебаний бы ли выбраны боковые поверхности листов, так как верх ние и нижние поверхности листов, собранных в пакет, недоступны для контроля, а их торцы имеют фигурный профиль и значительные неровности после вырубки. В качестве датчиков использованы призматические ис кательные головки с фигурной контактной поверхностью по форме поверхности боковых сторон рессорных ли стов. Учитывая высокую шероховатость и вертикальное расположение рабочих поверхностей, для улучшения акустического контакта поверхности смазывали высо ковязким минеральным маслом.
Были исследованы возможности использования по верхностных и сдвиговых волн. При изменении угла па дения продольных волн экспериментально был найден критический угол падения (64°), при котором прелом ленные волны распространяются по поверхности. Для рессорных листов с надрезом получили тарировочный график, позволяющий по положению импульса на экра не дефектоскопа с точностью ± 1 мм определять поло жение трещины. При этом регистрировались дефекты (усталостные трещины) протяженностью 1/3 от толщи-
213
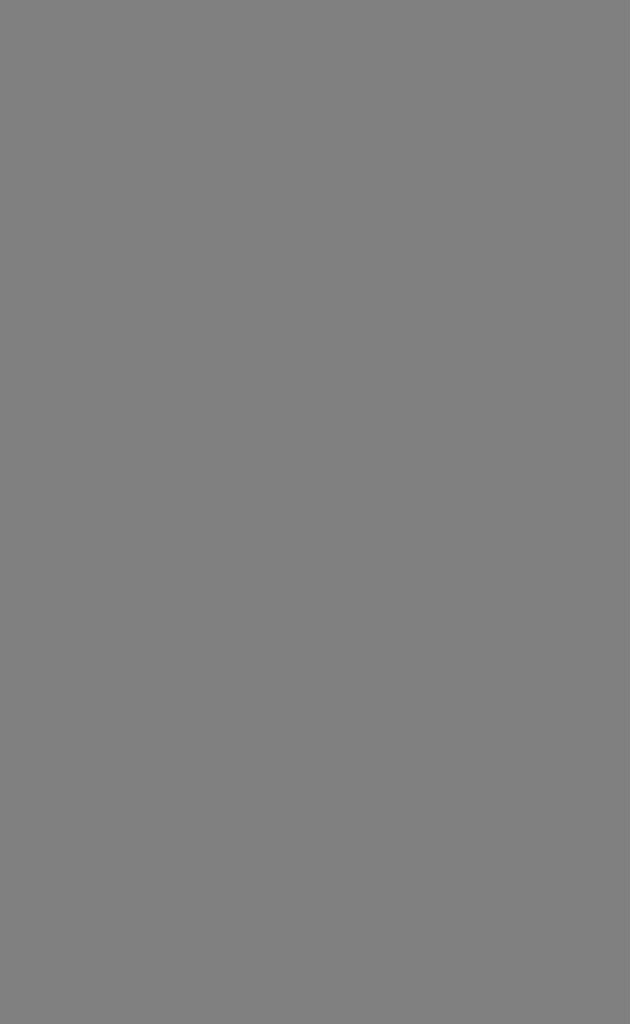
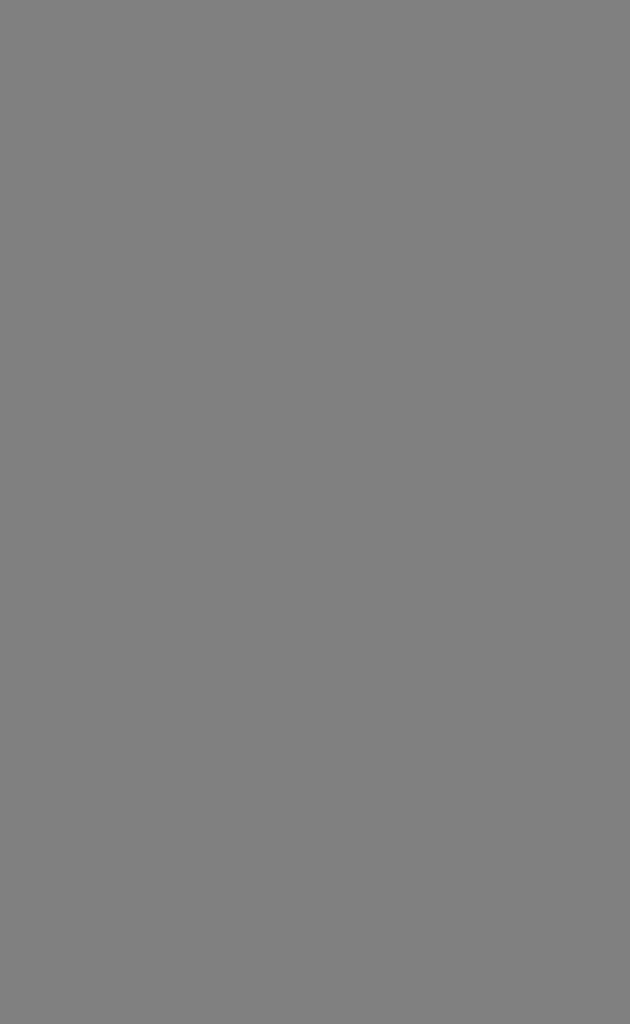
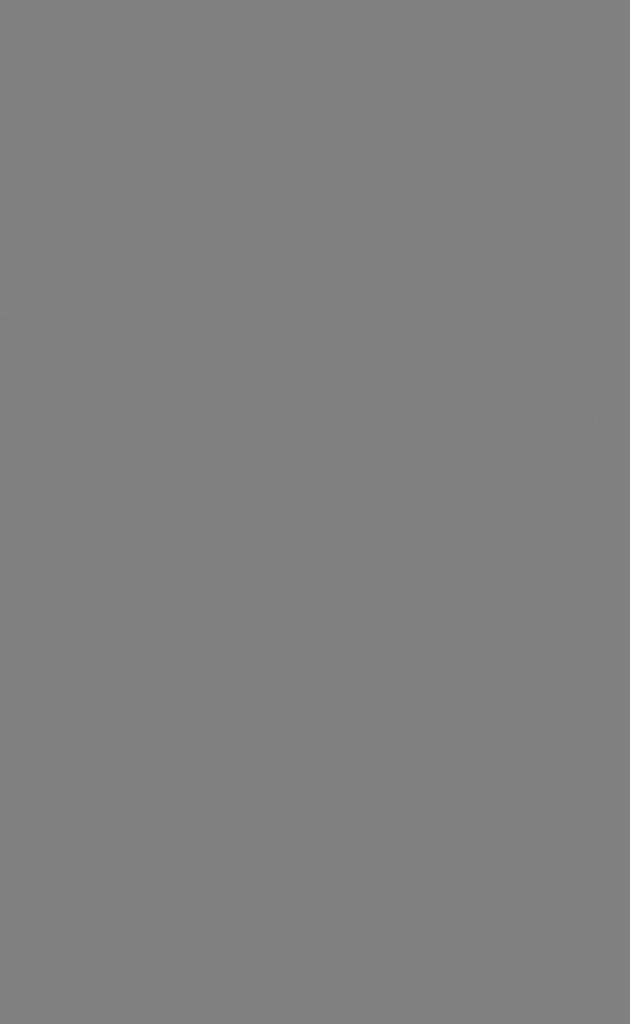
Обработка результатов регистрации повреждения с использованием С-критерия велась методом поиска та кого значения сr/f, при котором
|
|
|
|
2;= 1 |
2 |
min, |
|
|
|
|
|
= |
|||
|
|
|
|
|
|
||
где |
С0г — частные |
значения; С0 |
— среднее значение |
||||
критерия |
при D = D 0. Расчетом получены значения D0= |
||||||
=0,01422 |
и |
o/f= 1,056. На |
|
||||
рис. |
4.4 |
сплошной |
линией |
|
|||
показана |
расчетная зависи |
|
|||||
мость D от NT/N , |
получен |
|
|||||
ная с использованием |
С-кри |
|
|||||
терия, |
а штриховой — зави |
|
|||||
симость D от NT/N , получен |
|
||||||
ная с использованием |
С-кри |
|
|||||
терия |
(G=0,873 |
и |
GK= |
|
|||
=0,091). Сравнение показы |
|
||||||
вает |
|
хорошую сходимость |
|
||||
расчетных |
зависимостей |
|
|||||
между собой, а также с ре |
|
||||||
зультатами |
измерений. |
|
|||||
Таким |
образом, |
анализ |
|
||||
предварительной |
информа- |
|
Рис. 4.4. Зависимость степени
повреждения первого (коренного)
листа рессоры от доли вырабо танного ресурса долговечности
ции о процессе усталости рессорных листов позволяет сде лать вывод о том, что процесс усталости рессорных ли стов при регулярном нагружении хорошо описывается критериями сопротивления усталости, линеаризующими данный процесс. Это в значительной мере облегчает ре шение задачи прогнозирования остаточных ресурсов долговечности как в тех случаях, когда известно экви валентное напряжение (С-критерий), так и в тех слу чаях, когда эквивалентное напряжение трудно оценить (G-критерий).
217
Отработка метода и средств диагностики усталости наиболее слабой детали узла в условиях, моделирующих эксплуатацию узла, позволяет также оценить влияние процесса усталости одной детали на повреждение дру гих деталей узла [2 0 1 ].
4.1.3. Прогнозирование остаточной долговечности
Выбор метода прогнозирования существенным обра зом зависит от регулярности или нерегулярности нагру жения контролируемых деталей.
В случаях, когда регулярное нагружение характери зуется параметрами, не изменяющимися в процессе эксплуатации, при отработке метода и средств диагно стирования достаточно ограничиться испытаниями де талей в условиях моделирования фиксированной экс плуатационной нагрузки. Полученный ряд значений степени повреждения и соответствующий ряд значений чисел нагружений являются достаточной информацией для описания кинетики процесса с помощью критериев сопротивления усталости.
При использовании С-критерия определяется пара метр f (см. гл. 1 ), а при использовании G-критерия со противления усталости вычисляется конечное значение критерия GK. Критерии дают возможность определить расчетным путем остаточную долговечность:
N# = N - N ri
для любого фиксированного значения степени повреж дения Di.
Схема прогнозирования для рассматриваемых слу чаев регулярного нагружения изображена на рис. 4.4. В процессе эксплуатации регистрируются значения сте пени повреждения детали (Du D2» D3 и т. д.) и соответ ствующие им наработки (WT1»-Мтг» Мтз и т. д.). Затем оп ределяются значения критериев сопротивления устало сти {Си С2, С3 и т. д. или Gь G2, G3 и т . д .) и с исполь зованием метода наименьших квадратов исходные зна
чения критериев (С0 или Go).
Оценка остаточной долговечности до долома контро лируемой детали N р< при использовании С-критерия
218
производится при любой степени повреждения Z), по формуле
Ntt = N - N Ti = ■ С‘ |
Nrt , |
с 0 |
с,- |
где Сг и N n — значения критерия и срока службы дета ли в момент оценки остаточной долговечности. Исполь зование С-критерия предпочтительно в тех случаях, ког да известно действующее напряжение.
В случае использования G-критерия остаточная дол говечность определяется по формуле (рис. 4.5)
N m = N - N Ti = N Tl
Go — Oi
где Gi и N n — значения критерия и срока службы дета ли в момент оценки остаточной долговечности.
Разрушение (долом) контролируемой детали может быть причиной разрушения или ускоренного поврежде
ния других деталей узла |
[2 0 1 ], а |
иногда |
и |
причиной |
||||
аварии, |
поэтому замену контролируемой |
детали |
необ |
|||||
ходимо |
производить при степени |
повреждения Dni ко |
||||||
торая меньше степени |
повреждения в момент |
долома. |
||||||
Так как |
контроль степени |
повреждения |
производится |
|||||
периодически и при каждом контроле оцениваётся |
как |
|||||||
остаточная |
долговечность, |
|
|
|
|
|||
таки вероятное приращение |
|
|
|
|
||||
степени повреждения AD* за |
|
|
|
|
||||
период эксплуатации до сле |
|
|
|
|
||||
дующего |
контроля, то пре |
|
|
|
|
|||
дельным повреждением, при |
|
|
|
|
||||
котором |
необходимо |
произ |
|
|
|
|
||
водить замену детали, явля |
|
|
|
|
||||
ется следующее: |
|
|
|
|
|
|
Рис. 4.5. Прогнозирование оста точного ресурса долговечности с
использованием (5-крнтерия
219
DK— (А Д —i + А Д ) <С Dn <С DK— А Д .
В случаях, когда такой параметр регулярного нагру жения, как максимальное напряжение цикла, изменя ется при эксплуатации, отработка метода и средств ре гистрации степени усталостного повреждения деталей требует изучения процессов усталостного повреждения деталей во всем диапазоне эксплуатационных значений действующих напряжений с тем, чтобы иметь возмож ность воспроизвести кинетическую диаграмму устало сти (рис. 4.6), каждая кривая которой характеризует долговечность детали при фиксированной степени пов реждения. Так как конечная степень повреждения DK зависит от величины действующего напряжения и уменьшается с увеличением напряжения, в качестве об щего конечного значения степени повреждения берется
минимальное |
соответствующее максимальному |
||
напряжению. На любом уровне напряжений |
исходный |
||
ресурс N оценивается |
от начала испытаний деталей до |
||
момента |
достижения |
конечной степени повреждения |
|
Д { min- |
построении кинетической диаграммы целесооб |
||
ПрИ |
|||
разно использовать критерии сопротивления |
усталости, |
с помощью которых определяются ряды значений оста точных ресурсов (N ft= N —N>n), соответствующие теку щим значениям степени повреждения в исследуемом диапазоне напряжений. Для каждого текущего значения степени повреждения, исходя из напряжений и соответ
ствующих долговечностей, |
определяются параметры |
Vi и он и строятся кривые |
усталости равной степени |
повреждения (рис. 4.6). Так |
как напряжения а* в усло |
виях эксплуатации могут быть меньше исходной величи ны предела выносливости, при построении кинетической диаграммы усталости необходимо учитывать снижение предела выносливости в процессе повреждения и воз можность повреждения контролируемой детали этими напряжениями при а > о н .
Схема прогнозирования, которая может быть реали зована как аналитически, так и графически, представ лена на рис. 4.6. Например, на первом этапе эксплуата ции регулярное нагружение характеризуется макси мальным напряжением цикла сгь При достижении сте пени повреждения D2 остаточный ресурс на том же
220