
книги / Сопротивление материалов деформированию и разрушению. Ч. 1
.pdfских задач. Наибольшие успехи в этой области получены при создании волокни стых композиционных материалов. Высокая прочность в этом случае достигается путем армирования нитевидными кристаллами, имеющими весьма высокую проч ность, металлической или неметаллической матрицы более низкой прочности.
Прочность такого композита будет определяться |
соотношением наполнителя |
и матрицы. |
|
Приведенные выше характеристики прочности материалов получены при моно |
|
тонном кратковременном нагружении. В зависимости |
от длительности и режима |
нагружения они могут существенно уменьшаться. |
|
При нагружении в условиях комнатной температуры наиболее существенно |
|
прочность снижается при длительном циклическом нагружении, вызывающем ус |
|
талость металлов. |
|
На рис. 2.5 показано соотношение пределов прочности и выносливости, характе ризующих прочность в случае усталостного разрушения для сплавов на основе же леза 1170]. На рисунке линия 1 соответствует 50 % отношения предела выносливости
к пределу прочности, линия 2 — пределам выносливости гладких полированных |
||||
образцов (штриховкой показаны области рассеяния), |
область 3 — результатам ис |
|||
пытания надрезанных образцов, а область 4 — результатам испытаний в |
условиях |
|||
коррозии, приводящей к появлению коррозионных язв.. |
|
|
|
|
2.1.2. |
Удельная прочность. Во многих случаях (летательные аппараты, детали, |
|||
эксплуатирующиеся в поле центробежных сил и т. п.) важно не столько достижение |
||||
высоких абсолютных значений прочности, сколько достижение высоких |
удельных |
|||
значений прочности, т. е. значений прочности сгв, отнесенных к их плотности |
у*- |
|||
В табл. 2.2 выполнено сравнение удельной прочности углеродистой |
стали |
10, |
||
высокопрочной стали ЗОХМА, алюминиевых сплавов |
Д16 и В95 и магниевых спла |
|||
вов МА2-7 и ВМ65-1, полученных на образцах, вырезанных из различных полуфаб |
||||
рикатов [84]. Как видно из таблицы, удельная прочность таких сравнительно низко |
||||
прочных сплавов, какими являются магниевые сплавы, |
значительно выше, чем проч |
ность сталей, и не уступает прочности алюминиевых сплавов.
На рис. 2.6, по данным работы [172], приведены кривые изменения за послед ние 75 лет удельной прочности сталей (-/), сплавов алюминия (2) и титана (3) и ком позитов, армированных волокнами стекла, бора и углерода (4). Из рисунка видно, что для таких материалов, как сталь, алюминиевые и титановые сплавы, удельная прочность находится в стадии насыщения, в то же время, используя композицион ные материалы на основе волокон стекла, бора, угларода и других элементов, можно существенно увеличить удельную прочность.
Композиционные материалы имеют большие перспективы дальнейшего увели чения удельной прочности и жесткости на основе использования различных комбина
ций матрицы и наполнителя.
Сопоставление удельных прочностей ojy* и удельных модулей упругости первого рода
Рис. 2.7. Сопоставление удельных прочностей и удельных модулей упругости различ ных материалов
Рис. 2.8. Зависимость удельной прочности некоторых тугоплавких металлов и ид сплавов от температуры (листы в рекристаллизованном состоянии)
Рис. 2.9. Зависимость вязкости разрушения различных материалов от предела те кучести (а) и предела прочности (б):
J — титановый сплав ВТЗ-1; 2 — титановые сплавы; 3 — стали J66...J88; 4 — стали 60С2ХГ 40С2Х; 5 — сталь Ni—Сг—Mo—У; 6 — сталь 5 % Сг—Mo—V; 7 — стали 50, Н57; 8 — стали
НР-9-4-25, НР-9-4-35, НР-9-4-45 |
|
|
|
к |
|
Ely*, характеризующих удельную |
жесткость материала, |
выполнено |
на рис. 2.7 |
||
(172), где в дополнение к приведенным там обозначениям: |
Î — сталь, |
титан; 2 — |
|||
стекло — смола; 3 — бор — смола, |
4 — углерод — смола. |
композитов значитель |
|||
Из приведенных данных видно., что область расположения |
|||||
но удалена от начала координат по |
сравнению |
с обычными материалами. Это сви- |
|||
«ic, KQ, MH/ MW |
детельствует |
о лучших характеристиках |
|||
композитов. |
2.8 |
показано |
соотношение |
||
|
На |
рис. |
удельных прочностей некоторых тугоплав ких металлов и их сплавов в зависимости
от температуры |
при испытании их в ва |
|||||||
кууме |
[177], где: |
1 — ниобиевый |
сплав |
|||||
(Nb — 10 % Ti — 5 % Zr); |
2 — молибде |
|||||||
новый сплав (Mo — 0,5% |
Ti — 0,1 |
% Zr); |
||||||
3 — танталовый |
сплав |
(Та — 10 % W); |
||||||
4 — тантал; |
5 — вольфрам. |
|
|
|
||||
Из рисунка видно, что в связи с раз |
||||||||
личным характером |
изменения |
прочности |
||||||
тугоплавких металлов и сплавов в зависи |
||||||||
мости от температуры соотношение удель |
||||||||
ных |
прочностей |
в |
разных |
температур |
||||
ных диапазонах различно, что необходимо |
||||||||
учитывать |
при |
рассмотрении |
удельных |
|||||
прочностей |
материалов в конкретных ус |
|
ловиях эксплуатации. |
|
|
|
|
|
2.1.3. |
Низкая чувствительность к тех |
|||
|
нологическим и другим дефектам. Высокие |
||||
|
характеристики предела |
прочности мате |
|||
|
риала, полученные при испытании лабора |
||||
|
торных образцов, не всегда соответствуют |
||||
|
высоким |
характеристикам |
сопротивления |
||
|
деформированию и разрушению |
материа |
|||
Рис. 2.10. Зависимость между преде |
лов конкретных деталей определенной гео |
||||
метрии, |
изготовленных |
по |
определенной |
||
лом текучести и вязкостью разруше |
технологии и эксплуатирующихся |
в опре |
|||
ния для сталей и чугунов |
деленных условиях. |
|
|
|
Один из определяющих факторов в этом случае — зависимость прочности от раз личного рода дефектов, какими являются микро- и макроскопические трещины, ше роховатость поверхности, дефект сварки и литья, поры и включения и другие, а также от остаточных напряжений, возникающих в процессе изготовления деталей. Наибо лее существенно проявляется роль дефектов при наличии факторов, способствующих
хрупкому разрушению |
(острые трещины, низкие |
температуры, высокие скорости |
||
нагружения), и в условиях повтор |
|
|
||
но-переменного нагружения, приво |
T a б л и ц a |
2.3. Диапазоны значений |
||
дящего к усталостному разрушению. |
для различных типов дефектов |
|||
В этих случаях, |
если |
не принять |
||
дополнительных |
мер, |
увеличение |
|
|
прочности (предела |
прочности) ма |
Тип дефекта |
|
|
териала может привести не к увели |
|
|||
|
|
|||
чению, а наоборот,— снижению та |
Поры |
2...3 |
||
ких характеристик, |
как |
ударная |
||
вязкость, вязкость |
разрушения, |
Включения |
3...5 |
|
предел выносливости и т. п. |
шлаковые |
|||
На рис. 2.9, по данным работы |
острые шлаковые |
5...7 |
||
[1091, приведены результаты анали |
цепочные шлаковые и поры |
6,5...9 |
||
за зависимости вязкости |
разруше |
Непровар |
9...15 |
ния /<1с от предела текучести и пре
дела прочности для различных сплавов. Несмотря на некоторый разброс, который имеет место в этом случае, наблюдается четкое существенное снижение вязкости разрушения сталей с увеличением их предела прочности и предела текучести.
Детально взаимосвязь характеристик вязкости разрушения металлов и их пре делов текучести была проанализирована в работе [219]. Некоторые результаты этого анализа приведены на рис. 2.10, где заштрихованные области (1...I6) соответ ствуют различным маркам сталей, а область 17 — чугунам; сплошные линии соответ ствуют постоянным значениям, указанным на рисунке, произведений пределов теку*
честип! коэффициентов интенсивности напряжений. Около этих линий |
указаны |
года, |
||
когда были достигнуты соответствующие зна |
|
|
||
чения |
произведений. Наиболее высокие зна |
|
|
|
чения этих произведений соответствуют аусте |
|
|
||
нитным марганцево-азотистым сталям. |
|
|
||
На рис. 2.11 показана зависимость кри |
I |
|
||
тических температур хрупкости для сталей |
|
|||
ЭИ802 |
(/), |
1Х11МФ (2) и ЭП428 (3) |
|
|
от предела |
текучести по различным кри |
I |
|
|
териям (ак = |
0,3 МДж/ма, аТ Цр= 0,2 МДж/м2, |
|
||
26 и 50 % волокон излома) [184]. Из рисунка |
|
|
||
|
|
' |
" |
I |
|
|
|
|
i i |
|
|
|
|
$ |
Рис. 2.11. Зависимость переходных температур хрупкости, определенных по различ ным критериям, от предела текучести сталей
Рис. 2.12. Развитие трещины в однородном изотропном материале (а) и волокнистом композите (б)
Рис. 2.13. Сопоставление коэффициентов концентрации деформаций |
/Cg и эффектив |
||
ных коэффициентов концентрации напряжений |
/Са для различных |
типов |
дефектов |
видно, что для всех рассмотренных критериев |
хрупкого разрушения с |
увеличе |
нием предела текучести критическая температура хрупкости исследованных мате риалов существенно увеличивается.
Повышение сопротивления материалов развитию трещин как при статическом, так « динамическом нагружениях возможно путем их армирования волокнами (или слоями). Как видно из рис. 2.12, при армировании направление развития трещины в образце изменяется, развитие трещины сопровождается большими потерями энер гии, и характеристики вязкости возрастают.
Взаимосвязь предела выносливости o _ j и предела прочности < в для сталей схе
матически представлена на рис. 2.5.
Видно, что при наличии концентраторов напряжений и коррозионных сред су щественное увеличение предела прочности не приводит к увеличению предела вы носливости, а в некоторых случаях, если не принять специальных мер для подавле ния их отрицательного влияния, приводит даже к снижению предела выносливости.
В работе [48] сделаны попытки оценить коэффициент концентрации деформа ций Kg для различных видов сварочных дефектов и связать их со значением эффек
тивных коэффициентов концентрации напряжений при испытаниях |
на |
усталость |
|
К0. Рассчитанные коэффициенты концентрации деформаций приведены в |
табл. 2.3. |
||
Сравнение численных значений |
и соответствующих им значений |
К0 показано |
|
на рис. 2.13, откуда видно, что |
имеет место соответствие между значениями Kg |
и К а ,
Важно также отметить существенное снижение пределов выносливости до 12 раз при наличии дефектов, имеющих место в сварных соединениях.
2.1.4. Прочность в условиях высоких температур. Создание материалов, способ ных работать в условиях высоких температур,— одна из наиболее актуальных задач для многих направлений развития современной техники. Это — тепловая и атомная
энергетики, авиация и авиационное газотурбостроение, двигатели внутреннего сго рания, космическая и ракетная техника и т. д. Во всех этих случаях уровень рабочих температур определяет экономичность, материалоемкость, эффективность техники, т. е. совершенство техники определяется возможностями материалов, используемых при изготовлении этой техники, выдерживать высокие рабочие температуры в тече ние заданного срока эксплуатации.
- На рис. 2.14 в качестве примера показан уровень установившихся температур летательного аппарата, вызываемый аэродинамическим нагревом при полете на раз
личных высотах [71]. Можно привести |
много других примеров, когда интенсифика |
|||||
ция режима эксплуатации приводит к повышению рабочих температур. |
|
|||||
Т а б л и ц а 2.4. Температурные области применения металлических |
||||||
|
сплавов |
|
|
|
||
|
Сплав |
|
Температурная область применения |
|||
Алюминиевый |
|
|
Комнатная |
...530 |
К |
|
Магниевый |
|
|
470 К ... 700 К |
К |
|
|
Низколегированная сталь |
|
Комнатная |
...920 |
|
||
Дисперсионнотвердеющая нержавеющая |
Комнатная |
...810 |
К |
|
||
сталь |
|
|
530 К ... 870 К |
|
|
|
Титановый |
|
|
|
|
||
Жаропрочный на основе Ni и Со |
|
810 К ... 1420 К |
К (как жаростой |
|||
Нержавеющая |
сталь |
|
Комнатная |
...1470 |
||
Молибденовый |
(при условии защиты |
от |
кий материал) |
|
|
|
1140 К ... |
1640 К |
|
|
|||
окисления) |
|
|
|
|
|
|
В табл. 2.4 по данным работы [71] приведены температурные области |
примене |
|||||
ния металлических сплавов. Следует отметить условность температурных |
областей, |
приведении •• в этой таблице, так как температура использования зависит от усло вий нагруженности той или иной детали. Конкретные значения характеристик со противления деформированию и разрушению при высоких температурах некоторых металлических сплавов в области их использования приведены в табл. 2.5 [153].
Более высокие рабочие температуры по сравнению со сплавами на основе желе за, алюминия, титана, никеля и кобальта можно получить на сплавах таких туго плавких металлов, как вольфрам, молиб ден, тантал, ниобий.
Достижимые пределы прочности для этих сплавов показаны на рис. 2.15 [72].
Рис. 2.14. Установившиеся температуры обшивки, вызванные аэродинамическим нагревом (величины получены расчетом)
Рис. 2.15. Максимально достижимые значения предела прочности для «наилучших» сплавов на основе вольфрама (/), молибдена (2), тантала (3) и ниобия (4)
Материал
Алюминиевый
сплав АК4-1
ВД-17
'Титановый
сплав ВТ-9
Основной химический состав, |
Термическая обработка |
|
% |
||
|
Си 1,9—2,5; |
Mg 1,4— 1,8; |
Закалка |
при 788 К в воду. |
Ni 0,3—0,8; Ti 0,015; Al — |
Старение при 458 К 8— 12 ч |
||
основа |
|
|
|
Си 2,6—3,2; |
Mg 2—2,4; |
Закалка при 788 К в воду. |
|
Мп0,45—0,7; Fe 0,3; А1— |
Старение |
при 443 К 16 ч |
|
основа |
|
|
|
А1 16,5; |
Mo 3,5; Si 0,25; |
Закалка при 1173 К в воду. |
Zn2,0; |
Ti — основа |
Старение при 773...873 К |
|
|
1—6 ч |
ВТЗ-1 |
AI |
5,5; |
Mo 2,0; Cr 2,0; |
Закалка при 1423 К в воду. |
|
Fe |
1,0; |
Ti — основа |
Старение при 823 К 3 ... 10 ч |
Темпера тура, К
293
423
473
523
573
293
473
513
523
573
293
673
723
773
823
873
293
673
723
773
823
973
Конструкцион |
С 0,2; |
Мп 0,4; |
Сг 2,8; |
Нормализация |
при |
1423 К. |
293 |
||||
ная сталь |
Ni 0,45; |
W 0,4; |
Fe — ос- |
Закалка |
при 1323 К в масло |
723 |
|||||
ЭИ415 |
нова |
|
|
|
|
|
|
|
|
773 |
|
|
|
|
|
|
|
|
|
|
|
823 |
|
|
|
|
|
|
|
|
|
|
|
873 |
|
Коррозионно- |
С < 0 ,1 2 ; Мп 1—2; |
Сг 18; |
Закалка |
при |
1323 К вводу |
293 |
|||||
стойкая (нер- |
Ni 10; Ti 0,8; Fe — основа |
|
|
|
|
|
813 |
||||
жавеющая сталь) |
|
|
|
|
|
|
|
|
|
973 |
|
12Х18Н9Т |
|
|
|
|
|
|
|
|
|
1073 |
|
Жаропрочная |
|
|
|
|
|
|
|
|
|
|
|
сталь |
|
|
|
|
|
|
|
|
|
293 |
|
37Х12Н8Т8МФБ |
С 0,35; |
Мп 8,5; |
Сг |
12,5; |
Закалка |
при |
|
1423 К 1,5 ч |
|||
|
723 |
||||||||||
(ЭИ481) |
Ni 8,0; |
Mo 1,3; Fe — осно- |
в во д у . Старение при 943 К |
||||||||
873 |
|||||||||||
|
ва |
|
|
|
16 ч и при |
1063 К |
16 ч. |
||||
|
|
|
|
923 |
|||||||
|
|
|
|
|
Охлаждение |
на воздухе |
|||||
|
|
|
|
|
973 |
||||||
|
|
|
|
|
|
|
|
|
|
||
ХН35ВТ |
СО, 1; M nl,5;C r 15; Ni 35; |
Закалка |
при |
1453 К в воду. |
293 |
||||||
(ЭИ612) |
Fe — основа |
|
|
Старение |
при |
1053 |
К 8— |
903 |
|||
|
|
|
|
|
10 ч и |
при |
|
1003 К 25 ч. |
923 |
||
|
|
|
|
|
Охлаждение |
на воздухе |
973 |
||||
|
|
|
|
|
|
которых сплавов при высоких температурах
°0,2 |
Ô |
<*100 tfliOO °0,2/100 |
|
|
Область прнменання |
МПа |
% |
МПа |
450 |
380 |
18 |
26 |
_ |
. |
— |
Лопатки |
осевых компрессоров, |
|||||||||
400 |
360 |
12,5 |
26,5 |
290 |
— « |
280 |
крыльчатки, |
диски, |
кольца |
и |
|||||||
340 |
300 |
11 |
23 |
170 |
_ |
160 |
другие |
кованые |
детали, |
рабо- |
|||||||
240 |
190 |
6 |
30 |
100 |
- |
80 |
тающие |
при |
|
температурах |
до |
||||||
170 |
140 |
8 |
34,5 |
40 |
— |
30 |
523 К |
|
|
|
|
|
|
|
|
|
|
500 |
330 |
13 |
21 |
|
|
|
|
|
|
|
|
|
|
|
|
|
|
380 |
— |
16 |
33 |
190 |
— |
160 |
|
|
|
|
|
|
|
|
|
|
|
— |
— |
— |
— |
130 |
__ |
90 |
|
|
|
|
|
|
|
|
|
|
|
240 |
— |
16 |
66 |
100 |
L |
75 |
|
|
|
|
|
|
|
|
|
|
|
180 |
— |
21 |
75 |
55 |
— |
32 |
|
|
|
|
|
|
|
|
|
|
|
1150 |
1030 |
5 |
— |
_ |
|
— |
Диски, |
лопатки, |
корпуса |
ком- |
|||||||
850 |
720 |
7 |
— |
— |
|
— |
прессоров, крепежные |
детали, |
|||||||||
— |
— |
— |
— |
_. |
. |
— |
работающие |
при |
температура* |
||||||||
800 |
660 |
7 |
— |
650 |
_ |
280 |
до 723,,.773 |
К |
|
|
|
|
|
||||
780 |
620 |
8 |
— |
450 |
-- |
120 |
|
|
|
|
|
|
|
|
|
|
|
720 |
550 |
9 |
— |
230 |
|
|
|
|
|
|
|
|
|
|
|
|
|
1000 |
950 |
12 |
25 |
- |
550 |
— |
Диски, |
лопатки |
компрессоров, |
||||||||
760 |
630 |
8 |
— |
650 |
300 |
работающие |
при |
температурах |
|||||||||
*-- |
— |
— |
— |
650 |
500 |
160 |
до 623...673 К |
|
|
|
|
|
|
||||
700 |
560 |
10 |
— |
360 |
270 |
60 |
|
|
|
|
|
|
|
|
|
|
|
—— |
— |
— |
— |
|
|
|
|
|
|
|
|
|
|
|
|
|
|
530 |
18 |
— |
— |
— |
— |
|
|
|
|
|
|
|
|
|
|
|
|
850 |
740 |
13,4 |
68,5 |
5ÏÔ |
500 |
— |
Поковки |
турбинных |
|
роторов, |
|||||||
650 |
590 |
13,1 |
60 |
— |
дисков, крепежные детали, ра- |
||||||||||||
640 |
600 |
15 |
59 |
490 |
420 |
— |
ботающие при температурах до |
||||||||||
570 |
544 |
15,5 |
65 |
350 |
320 |
— |
473...823 К |
|
|
|
|
|
|
|
|||
440 |
423 |
10,5 |
49 |
250 |
170 |
|
|
|
|
|
|
|
|
|
|
|
|
620 |
280 |
41 |
63 |
|
250 |
|
Детали коммуникаций |
горячих |
|||||||||
400 |
180 |
25 |
61 |
|
|
паров, |
коллекторы, |
патрубки, |
|||||||||
280 |
160 |
26 |
59 |
_ |
130 |
|
реактивные |
сопла |
и |
другие |
|||||||
180 |
100 |
35 |
69 |
— |
50 |
|
сварные детали, работающие |
во |
|||||||||
|
|
|
|
|
|
|
влажных средах и при повы |
||||||||||
|
|
|
|
|
|
|
шенных температурах |
|
|
|
|||||||
940 |
600 |
16 |
86 |
- |
___ |
|
Диски турбин, |
силовые кольца |
|||||||||
720 |
500 |
13 |
3t |
|
____ |
|
н крепежные |
детали |
газовых |
||||||||
600 |
450 |
|
|
|
|
|
|
|
|
|
|
|
|
|
|
|
|
12 |
|
___ |
— |
|
турбин, |
работающие |
|
при |
тем |
||||||||
560 |
430 |
12 |
— |
|
__ . |
|
пературах |
до |
873 К |
|
|
|
|
||||
•-- |
380 |
13 |
— |
— |
— |
|
|
|
|
|
|
|
|
|
|
|
|
830 |
500 |
24 |
40 |
800 |
230 |
|
Диски цельнокованых |
и |
свар |
||||||||
670 |
440 |
21 |
24 |
|
ных |
роторов. Лопатки, крепеж |
|||||||||||
570 |
420 |
15 |
24 |
300 |
|
|
ные |
детали, |
|
работающие |
при |
||||||
480 |
410 |
10 |
15 |
— |
— |
|
температурах до 923 К |
|
|
Материал
ЭИ257 (с титаном)
XH77TIOP
(ЭН437Б)
ХН80ТБЮ
(ЭИ607)
Никелевый
сплав
ЖС6К.П
Удимет 700
Основной химический состав. |
Термическая обработка |
Темпера, |
% |
|
тура, к |
С 0,10; |
Si 0,8; |
Мп0,7; |
|
Сг 14; Ni |
14; W 2,3; Mo 0,5; |
||
Ti 0,5; Fe — основа |
|
||
С < 0 ,0 7 ; |
Сг 20; |
|
Ti 2,7; |
Al 0 ,6 -1 ,0 ; Fe 1,0; |
N i— |
||
основа |
|
|
|
С < 0 ,0 8 ; Сг 15—17;
Nb 1,0— 1,5; |
Ti 1,8—2,3; |
А! 0» 15; Fe 3,0; |
Ni — осно- |
ва |
|
СО, 15; Сг 15; Со 18; Ti 3,5; Al 4,0; Mo 5,0; Fe 1,0; Ni — основа
Нормализация |
при |
1373 К |
293 |
|||||
|
|
|
|
|
|
|
|
873 |
|
|
|
|
|
|
|
|
898 |
|
|
|
|
|
|
|
|
923 |
Закалка |
при |
1353 К |
8 ч на |
293 |
||||
воздухе. |
Старение |
|
при |
|
||||
1023 К 16 ч. Охлаждение на |
823 |
|||||||
воздухе |
|
|
|
|
|
|
873 |
|
|
|
|
|
|
|
|
|
|
|
|
|
|
|
|
|
|
973 |
|
|
|
|
|
|
|
|
1023 |
|
|
|
|
|
|
|
|
1073 |
Закалка |
при |
1373 К |
5 |
ч в |
293 |
|||
воду. Тройное |
ступенчатое |
923 |
||||||
старение |
|
|
|
|
|
|
973 |
|
|
|
|
|
|
|
|
|
|
Закалка |
при |
1493 К 4 ч на |
273 |
|||||
воздухе. Отжиг |
при |
1223 К |
1073 |
|||||
2 ч. Охлаждение на возду- |
||||||||
ке |
|
|
|
|
|
|
|
1173 |
|
|
|
|
|
|
|
|
|
|
|
|
|
|
|
|
|
1223 |
|
|
|
|
|
|
|
|
1173 |
|
|
|
|
|
|
|
|
1323 |
Закалка |
при |
1463 К |
2 ч на |
293 |
||||
воздухе. |
Закалка |
1353 |
К |
1088 |
||||
4 ч |
на |
воздухе. |
Старение |
1143 |
||||
при |
1113 К 24 |
ч. |
Охлаж |
1253 |
||||
дение на воздухе. Старение |
|
|||||||
1033 |
К |
16 ч. |
|
Охлаждение |
|
|||
на воздухе |
|
|
|
|
|
|
Уаспалой |
С 0,07; Сг 19; Со 14; Ti 3,0; |
|
Al 1,3; Mo 4,3; 1,0; Ni — |
|
основа |
Закалка |
при |
1353 К 4 |
ч на |
293 |
воздухе. |
Старение |
при |
923 |
|
1113 К |
24 ч. |
Охлаждение |
1003 |
|
на воздухе. |
Старение |
при |
1088 |
|
1033 К 16 ч. Охлаждение на |
1143 |
|||
воздухе |
|
|
|
|
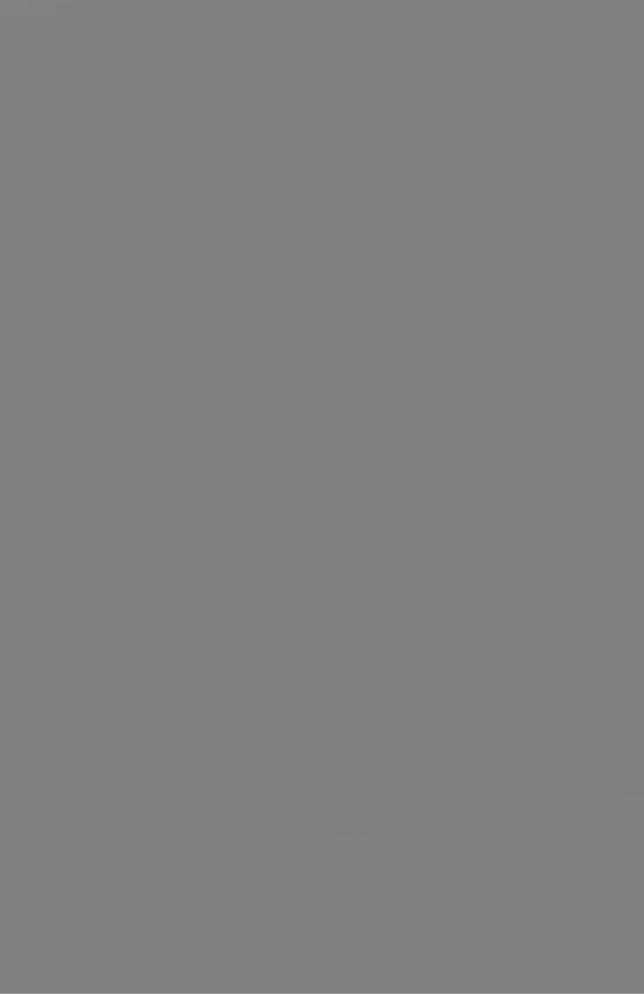
Материал
ЖСбК
MAR 246
Сплав туго плавких метал лов на основе мо
либдена ВМ-2
на основе ни обия ВН-4
на основе воль фрама
Основной химический состав,
%
С 0,16; Сг 9,5; Ti 2,5; Al 5; Со 4,5; W 5,0; Ni — осно ва
С 0,15; Сг 9; Ti 1,5; Al 5,5; Со 10; Mo 2,5; Та 1,5; Ni — основа
Ti 0,8— 1,3; Zr 0,36;
Nb 0,25 -0,5; G 1 -1 ,8 ; Mo — основа
Mo 8,5—10,5; Zr 1—2;
C0,25—0,4; La 0,01—0,45)
Nb — основа
Th02 2,0; W — основа
Термическая обработка |
Темпера- |
|||
|
|
|
|
тУра,-К |
Закалка при 1493 К 4 чна |
293 |
|||
воздухе |
|
|
|
1073 |
|
|
|
|
|
|
|
|
|
1173 |
|
|
|
|
1203 |
Закалка при |
1453 К |
2—4 ч |
1033 |
|
на воздухе |
|
|
1088 |
|
|
|
|
|
1144 |
|
|
|
|
1255 |
|
|
|
|
1311 |
Отжиг |
для |
снятия |
напря |
293 |
жений |
при |
1173— 1223 К. |
1073 |
|
Рекристаллизационный от |
1213 |
|||
жиг при 1473...2273 К |
1073 |
|||
|
|
|
|
1273 |
1073
1273
293
1323
1373
1423
1473
293
1743
1923
2135
2463
Использование подобных материалов в технике встречает большие сложности в связи с необходимостью их защиты от окисления при высоких температурах.
Недостатком многих этих сплавов является высокая температура хрупкости и существенная ее зависимость от наличия примесей (азота, кислорода, серы). Весьма высокие температуры плавления (или диссоциации) имеют тугоплавкие соединения — карбиды, бориды, нитриды, оксиды и т. п.
По данным работы [1], число тугоплавких соединений, температура плавления которых превышает 2773 К, составляет около 80. Эти соединения помимо высокой температуры плавления обладают целым рядом других ценных физико-химических свойств. Недостатком их является почти полное отсутствие пластичности, вплоть до весьма высоких температур. Отсутствие пластичности приводит к целому комплек су свойств, препятствующих использованию тугоплавких соединений в, качестве кон струкционных материалов, эксплуатирующихся в условиях высокщ^температур. Это низкие характеристики прочности при растяжении по сравнению с характерис-