
книги / Теоретические основы процессов получения и переработки полимерных материалов
..pdf
Рис. 9.5. Зависимость функции F(n,β) от k = 1/β при течении полимерных расплавов в кольцевом зазоре; числа у кривых– значения индекса n реологическогозаконаОсвальдадеВиля
Для значений 0,4 ≤ Ri / R0 ≤1,0 , которые характерны для относи-
тельно узких кольцевых зазоров, функция F оказывается независимой от индекса течения. Это аналогично случаю течения между параллельными пластинами:
Q = |
πR3 |
|
R ∆P |
β−1 |
2+s |
1+β |
. |
(9.19) |
|
0 |
|
0 |
|
|
|
|
|||
|
|
|
|
2β |
|||||
|
s + 2 2mL |
β |
|
|
|
Кабельные головки (рис. 9.6) предназначены для наложения изоляции на основе полимера на металлическую проволоку.
Головка состоит из матрицы (корпуса) 1, внутри которой концентрически укреплен полый дорн 2. Металлическая жила (медь, алюминий, латунь) 3 проходит через отверстие в дорне и попадает в кольцевую полость А, от экструдера по кольцевому каналу В нагнетается полимерный расплав, образующий на проводе изоляционный слой 4 толщиной h.
101
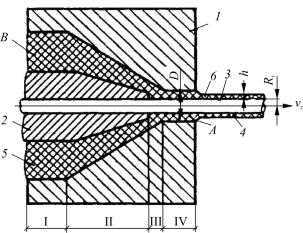
Рис. 9.6. Схема типичной кабельной головки
Определяя диаметр матрицы, следует иметь в виду, что проходящий через головку провод уносит с собой некоторое количество расплава полимера Qd за счет возникновения дополнительного вынужденного потока. Кроме того, основное количество расплава Qp выдавливается из головки избыточным гидростатическим давлением самого экструдера: Q = Qp +Qd .
Если задана толщина полимерного покрытия [(D–H)/2], диаметр (D = 2Ri) и линейная скорость протягивания провода вдоль оси (vz), то суммарный объемный расход расплава определится выражением
Q = 2πvz (Ri + H / 2)H. |
(9.20) |
Степень вытяжки. Средняя скорость (vmid) вытекающей из кабельной головки кольцевой струи, как правило, отличается от скорости протягивания провода. Если пренебречь высокоэластичным восстановлением, то средняя скорость истечения полимерного расплава определится выражением
vmid = Qρ/[π(D − H )Hρs ]. |
(9.21) |
102 |
|
При учете высокоэластичного восстановления скорость полимерной струи еще больше уменьшится:
vel |
= Qρ/[π(D − H |
el |
)H |
el |
ρ |
], |
(9.22) |
mid |
el |
|
s |
|
|
где Del и Hel – наружный диаметр полимерного покрытия (равный диаметру кабеля) и внутренний диаметр изоляции (равный диаметру провода) после эластичного восстановления полимерного покрытия провода.
Степень вытяжки λ определится как отношение скорости протягивания к скорости полимерной струи:
λ = v |
z |
/ vel |
= |
(Del − Hel )Hel |
, |
(9.23) |
|
||||||
|
mid |
|
2(Ri + h)h |
|
||
|
|
|
|
|
где h – толщина полимерного покрытия кабеля.
Давление экструзии кабеля. Если известен объемный расход полимерного расплава Q, то можно определить давление, развивающееся на выходе из кабельной головки экструдера. При расчете необходимо иметь в виду, что: на участках I и II (см. рис. 9.6) имеет место течение расплава в кольцевом цилиндрическом и кольцевом коническом каналах (Qd = 0); на участках III и IV – одновременно расход под давлением и расход вынужденного течения.
Потери давления (∆Р) на участках I и II (L) определяются по формулам:
|
Q = kr(∆P/η)n, |
|
(9.24) |
|
kr = |
π(R − R )n+2 |
(R + R ) |
, |
|
0 i |
0 |
i |
||
(n + 2)2n+1[L + m(R − R )]n |
||||
|
|
0 |
i |
|
где kr – коэффициент сопротивления для течения полимерной жидкости, m – поправка на гидравлические потери при входе расплава в головку.
Для участков III и IV необходимо вначале определить объемный расход вынужденного потока полимера по формуле
103

R0 |
|
|
πVz (R02 |
|
|
|
|
|
|
|
Q = 2π∫ rvz (r)dr = |
− Ri2 )g(n,β), |
(9.25) |
||||||||
Ri |
|
|
2 |
|
|
|
|
|
|
|
|
|
|
|
|
|
|
|
|
|
|
где функция g(n,β) определяется выражением |
|
|
|
|||||||
g(n,β) = |
2(n −1) |
|
1 |
+ |
4 |
|
|
1 |
, |
|
n −3 1−βn−1 |
n −3 β2 −1 |
|
||||||||
|
|
|
|
а величина β есть отношение радиусов R0/Ri.
Затем можно рассчитать искомый перепад давления и на этих участках головки экструдера, формующей кабельный провод на основе полимерного диэлектрика, например поливинилхлорида:
∆P = n Q / kr η, |
(9.26) |
где η – динамический коэффициент вязкости полимерного расплава. Полный перепад давлений в кабельной головке определится
в результате суммирования потерь давления на участках I–IV. Вальцевание – периодический (или условно непрерывный) про-
цесс, применяемый для пластикации (или завершения пластификации) каучука, нитрата целлюлозы в производстве баллиститного пороха, распределения наполнителя или пигмента (красителя) в различных полимерных материалах.
Основной процесс на вальцах – смешение компонентов в зазоре между вращающимися навстречу друг другу валками за счет сдвиговых усилий.
На рис. 9.7 схематично показан типичный вальцевальный аппарат, особенности которого следующие.
По назначению вальцы делятся на смесительные и листовальные. Соответствующие аппараты применяются для пластификации каучуков и смешения полимеров с различными твердыми и жидкими ингредиентами, а также для получения листов резиновой смеси. Кроме того, на вальцах можно измельчать вулканизат (резину) при его регенерировании, подогревать резиновую смесь перед ее подачей к каландру или шприц-машине, дробить регенерируемую резину, тонко измельчать твердые сыпучие компоненты.
104
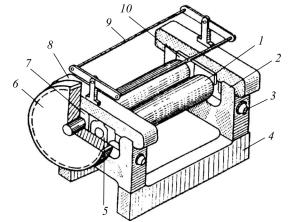
Рис. 9.7. Схема вальцов: 1 – валок; 2 – станина; 3 – винт, регулирующий зазор; 4 – основание; 5 – корпус переднего подшипника; 6 – большая шестерня привода валков; 7 – корпус заднего подшипника; 8 – поперечины; 9 – тяга механизма аварийногоостанова; 10 – ограничительнаястрелка
Подлежащие смешению компоненты (полимер, пластификатор, наполнитель) загружаются в зазор, в котором за счет интенсивной деформации сдвига, сопровождающейся интенсивным разогревом, происходит смешение. Валки 1 обычно изготавливают из кокильного чугуна. Рабочая поверхность отбеливается на глубину 15–18 мм; при этом твердость по Бринеллю должна составлять 3,0–4,5 кН/мм. Наружная поверхность валков шлифуется до класса чистоты 7 − 9. На поверхности валков дробильных вальцов под углом 7–11о осуществляется рифление на глубину 4,5–6,0 мм и ширину 4,5–11,0 мм; края валков оставляют гладкими. Валки рафинировочных (очистительных) вальцов имеют бочкообразную форму, обеспечивающую выдавливание твердых включений вдоль образующей на край валка. Для необходимого теплообмена валки имеют каналы, расположенные непосредственно у поверхности валка, в которых с большой скоростью циркулирует жидкость с соответствующей температурой. Взависимости от назначения частота вращения валков может быть одинаковой или различной. В последнем случае частота вращения заднего валка U2 выше, чем переднего U1. ОтношениеU1/U2 называетсяфрикцией(трением).
105
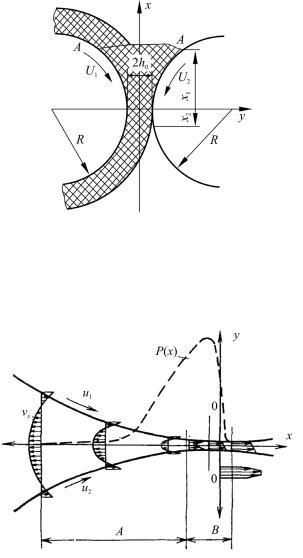
На рис. 9.8 показана технологическая схема вальцевания.
Рис. 9.8. Схема процесса вальцевания
Качественное описание физики процесса вальцевания демонстрируется на рис. 9.9, на котором показаны эпюры скоростей течения и давления, формируемые в вальцуемом полимерном композиционном материале.
Рис. 9.9. Распределение скоростей и давления в вальцуемом полимерном материале
106

Гидродинамическая теория вальцевания полимерного мате-
риала. Основные положения теории изотермического вальцевания полимерных композиций, реологические свойства которых подчиняются степенному закону Освальда де Виля, приведены ниже.
Основные уравнения движения материала в вальцах (см. рис. 9.8) выводятся при следующих допущениях: 1) течение двумерное; 2) среда несжимаема; 3) течение ламинарное, установившееся; 4) инерционные имассовые силы по сравнению с вязкими пренебрежимо малы; 5) составляющие скорости vx пропорциональны U; составляющие скорости vx пропорциональны Uh/L, где L и h – характерные длины вдоль осей x и y,
причем L >> h; 6) ∂vx / ∂x ≈U / L; 7) ∂vx / ∂y ≈U / h; 8) ∂vy / ∂x ≈Uh / L2 ; 9) вальцуемый материал является псевдопластичным (по Освальду де Вилю), а его эффективный динамический коэффициент вязкости описываетсявыражением, учитывающимтолькоаномалиювязкости:
1 |
(1−1/ n) / 2 |
|
||
ηa = µ0 |
|
I2 |
, |
|
2 |
||||
|
|
|
где µ0 – значение эффективной вязкости при условии – 12 I2 =1.
Исходная система дифференциальных уравнений имеет вид:
– уравнения сохранения количества движения в напряжениях (давлениях):
∂∂Px = ∂∂pxxx + ∂∂pyxy ;
(9.27)
∂∂Py = ∂∂pyyy + ∂∂pxyx ;
107
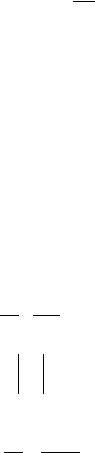
– составляющие тензора напряжений (давлений):
pxx = −p + 2µ0 I2(1/ n−1) / 2 ∂∂vxx ;
pyy = −p + 2µ0 I2(1/ n−1) / 2 ∂∂vyy ;
(9.28)
pxy = pyx |
= µ0 I2(1/ n−1) / 2 |
|
∂v |
x + |
∂vy |
; |
|
|
||||||||||
|
|
|
|
|
|
|
|
|||||||||||
|
|
|
|
|
|
|||||||||||||
|
|
|
|
|
|
|
|
|
∂y |
∂x |
|
|
|
|
||||
I2 |
|
∂vx 2 |
|
|
∂vy 2 |
|
|
∂vx |
|
∂vy |
|
|
||||||
= |
|
|
+ |
|
|
+ |
|
|
+ |
|
|
|
|
|
; |
|||
∂x |
|
|
∂y |
∂x |
|
|
||||||||||||
|
|
|
|
|
∂y |
|
|
|
|
|
|
|
|
– уравнение неразрывности потока:
∂v |
x + |
∂vy |
= 0. |
(9.29) |
|
∂y |
|||
∂x |
|
|
Используя допущения и учитывая оценки в теории пограничного слоя, эту систему уравнений можно упростить до соотношений:
P = P(x);
dP
dx
pxy = µ0
= dpdyxy ;
∂vx 1/ n−1 ∂vx .
∂y ∂y
Интегрируя уравнение (9.30), представим его в виде
pxy = dP h y ± y0 . dx h
(9.30)
(9.31)
Полученное решение показывает, что в рамках оговоренных приближений распределение напряжений сдвига в зазоре линейно. Константа y0 по своему физическому смыслу – это координата сечения, вкотором напряжения сдвига равны нулю. Из условия симметрии сле-
108

дует, что при отсутствии фрикции (U1/U2) y0 = 0. Поэтому все уравнения симметричного вальцевания существенно упрощаются. Вслучае несимметричного вальцевания сечение нулевых напряжений сдвига смещаетсявсторону валка, вращающегосясбольшейокружнойскоростью.
Каландрование – процесс непрерывного продавливания (прокатка) полимерного материала через зазор между вращающимися навстречу друг другу обогреваемыми полыми цилиндрами, при котором образуется бесконечный тонкий лист или пленка. В отличие от вальцевания при каландровании полимерный расплав проходит через каждый зазор только один раз. Каландрование широко применяется в резиновой промышленности и индустрии переработки пластмасс для изготовления тонких пленок и листов, а также для наложения полимерного слоя на ткань (рис. 9.10).
Анализ процесса каландрования методом МКЭ (методом ко-
нечных элементов) был осуществлен Влачопулосом. Область течения полимерного материала в зазоре валков разбивалась на треугольные элементы (рис. 9.11), а численное интегрирование системы исходных дифференциальных уравнений проводилось методом «взвешенных невязок» (разновидность метода Галеркина). Полимерный расплав рассматривался как жидкость с постоянной (эффективной) вязкостью.
Рис. 9.10. Схема каландрового агрегата: 1 – смеситель закрытого типа: 2 – вальцы; 3 – детектор металла; 4 – Z-образный каландр; 5 – охлаждающие барабаны; 6 – толщиномер; 7 – устройство для обрезания кромок; 8 – закаточное устройство
Исходными дифференциальными выражениями являются уравнение сохранения количества движения
∂P / ∂x = ∂τxy / ∂y |
(9.32) |
109 |
|
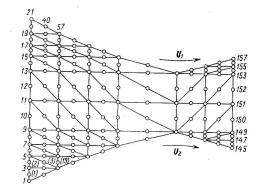
и уравнения неразрывности |
|
∂(hvx ) / ∂x = 0, |
(9.33) |
где h – половина зазора между валками. |
|
Рис. 9.11. Схема и система обозначения треугольных конечных элементов, используемых в анализе процесса каландрования
Цель решения– определение узловых значений скоростей и давлений. В качестве аппроксимирующих функций для поля скоростей использовалисьпараболическиефункции, адляполядавлений– линейные.
На рис. 9.12 показан результат анализа методом МКЭ каландрования полимерной композиции с n = 0,25 (течение по реологическому закону Освальда де Виля для полимерных систем).
При анализе неизотермического каландрования уравнение сохранения энергии составляют, предполагая, что теплофизические характеристики полимерного материала имеют постоянное значение.
Поэтому в рамках смазочной аппроксимации искомое дифференциальное уравнение принимает вид
ρC |
v |
∂T |
= K |
∂2T |
+ τ |
∂vx . |
(9.34) |
p |
|
x ∂x |
|
∂x2 |
|
yx ∂y |
|
Интегрирование этого уравнения осуществляется одновременно с интегрированием уравнений (9.32) и (9.33). Граничное условие – постоянство температуры полимерного материала на входе, которая принимается равной температуре поверхности валков. Решение
110