
книги / Теоретические основы процессов получения и переработки полимерных материалов
..pdf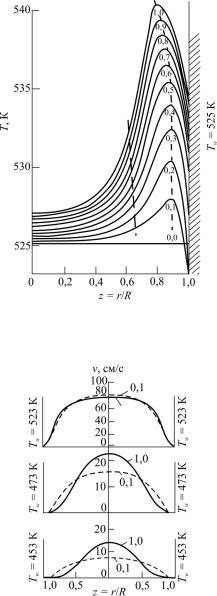
Рис. 5.1. Распределение температур по сечению трубы при течении расплава полиэтилена; цифры у кривых – относительное расстояние от входа в канал (l = x/L).
Рис. 5.2. Распределение скоростей потока расплава полиэтилена по сечению трубы; цифры у кривых – относительное расстояние от входа в канал (l = x/L)
51
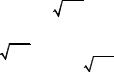
В последнем случае нагрев полимерного материала осуществляется как за счет теплопроводности, так и за счет тепла, выделяющегося вследствие химических реакций трехмерной полимеризации.
Ниже приведены примеры решения задачи теплопроводности
для тел различной геометрии в виде определения распределения температуры с указанием начальных и граничных условий:
полуограниченное твердое тело
|
|
|
|
|
|
|
|
|
|
|
|
|
T − T |
|
|
|
|
|
|
|
|
x |
|
|
|
|
|
|
|
|
|
|
|
|
|
|
|
|
|
|
|||||
|
|
|
|
|
|
|
|
|
|
|
|
|
|
|
|
1 |
|
= erf |
|
|
|
|
|
|
|
|
; |
|
|
|
|
|
|
|
|
|
|
|
|
|
|||||
|
|
|
|
|
|
|
|
|
|
|
|
|
T0 − T1 |
|
|
|
|
|
|
|
|
|
|
|
|
|
|
|
|
|
|
|
|
||||||||||||
|
|
|
|
|
|
|
|
|
|
|
|
|
|
|
|
|
|
|
|
|
4at |
|
|
|
|
|
|
|
|
|
|
|
|
|
|
||||||||||
|
|
|
|
|
|
|
T (x, 0) = T0 ; T |
(0, t) |
= T1 |
|
T (∞, t) = T0 ; |
|
|
|
|
|
|||||||||||||||||||||||||||||
|
|
|
|
|
|
|
T − T0 |
= |
q |
|
|
4at[1 − erf |
|
|
|
x |
|
|
|
|
|
|
|
|
|
|
|||||||||||||||||||
|
|
|
|
|
|
|
0 |
|
|
|
|
|
|
|
]; |
|
|
|
|
|
|
|
|
||||||||||||||||||||||
|
|
|
|
|
|
|
k |
|
|
|
|
|
|
|
|
|
|
|
|
|
|
||||||||||||||||||||||||
|
|
|
|
|
|
|
|
|
|
|
|
|
|
|
|
|
|
|
|
|
|
|
|
|
|
|
|
|
|
4at |
|
|
|
|
|
|
|
|
|||||||
|
|
|
|
|
T (x, 0) = T |
; T (∞, t) = T |
; − k |
∂T |
|
|
= q |
; |
|
|
|
|
|||||||||||||||||||||||||||||
|
|
|
|
|
|
|
|
|
|
|
|
0 |
|
|
|
|
|
|
|
|
|
0 |
|
|
|
|
|
∂x |
|
|
0 |
|
|
|
|
|
|||||||||
|
|
|
|
|
|
|
|
|
|
|
|
|
|
|
|
|
|
|
|
|
|
|
|
|
|
|
|
|
|
|
|
|
x=0 |
|
|
|
|
|
|||||||
|
плоская пластина |
|
|
|
|
|
|
|
|
|
|
|
|
|
|
|
|
|
|
|
|
|
|
|
|
|
|
|
|
|
|
|
|
|
|
||||||||||
|
T1 − T |
|
∞ |
|
(−1)n |
|
|
|
|
|
|
|
|
1 |
|
2 |
|
|
|
|
2 |
|
|
|
|
1 |
|
x |
|
||||||||||||||||
|
|
|
|
= 2∑ |
|
|
|
|
|
|
|
|
exp |
− n + |
|
|
|
π |
|
(at / b |
|
cos n + |
|
π |
|
; |
|||||||||||||||||||
|
T |
− T |
|
|
1 |
|
|
|
|
2 |
|
|
2 |
b |
|||||||||||||||||||||||||||||||
|
|
= |
|
|
π |
|
|
|
|
|
|
|
|
|
|
|
|
|
|
|
|
|
|
||||||||||||||||||||||
1 |
|
0 |
|
n |
0 |
n + |
2 |
|
|
|
|
|
|
|
|
|
|
|
|
|
|
|
|
|
|
||||||||||||||||||||
|
|
|
|
|
|
|
|
|
|
|
|
|
|
|
|
|
|
|
|
|
|
|
|
|
|
|
|
|
|
|
|
|
|
|
|
|
|
|
|
|
|
|
|
||
|
|
|
|
|
|
|
|
|
|
T (x, 0) = T0 ; T (±b, t) = T1; |
|
|
|
|
|
|
|
|
|||||||||||||||||||||||||||
|
|
|
|
|
|
|
hb |
|
|
|
|
|
x |
|
|
|
|
|
|
|
|
|
|
|
|
|
|
|
|
|
|
|
|
|
|
|
|||||||||
T − T |
|
∞ |
|
|
2 |
|
k |
cosβn |
|
|
|
|
|
|
|
|
|
|
|
|
|
|
|
|
|
|
|
|
|
|
|
|
|
||||||||||||
|
|
|
|
b |
|
|
|
|
|
|
|
|
|
2 |
|
|
|
|
|
2 |
|
|
|
|
|
|
|
||||||||||||||||||
1 |
|
|
|
|
|
|
|
|
|
|
|
|
|
|
|
|
|
|
|
|
|
|
|
|
|
|
|
|
|
|
|
|
|
|
|
|
|
|
|||||||
|
|
|
= ∑ |
|
|
|
|
|
|
|
|
|
|
|
|
|
|
|
|
|
|
|
|
|
exp(−βn at / b |
|
); βn tgβn |
= hb / k; |
|||||||||||||||||
T1 − T0 |
β2 + hb |
|
|
hb |
|
2 |
cosβ |
|
|
|
|
||||||||||||||||||||||||||||||||||
|
n=1 |
+ |
|
n |
|
|
|
|
|
|
|
|
|
|
|
|
|
|
|
|
|
|
|
|
|
|
|||||||||||||||||||
|
|
|
|
|
|
|
n |
k |
|
|
|
k |
|
|
|
|
|
|
|
|
|
|
|
|
|
|
|
|
|
|
|
|
|
|
|
|
|
|
|
||||||
|
|
|
|
|
|
|
|
|
|
|
|
|
|
|
|
|
|
|
|
|
|
|
|
|
|
|
|
|
|
|
|
|
|
|
|
|
|
|
|||||||
|
|
|
|
|
|
|
|
∂T |
|
|
|
|
|
|
|
|
|
|
|
|
|
|
|
|
|
|
|
|
|
∂T |
|
|
|
|
|
|
|
|
|
|
|||||
|
|
|
|
|
|
|
|
|
|
|
|
|
|
|
h |
|
|
|
|
|
|
|
|
|
|
|
|
|
|
|
|
h |
|
|
|
|
|
||||||||
|
T (x, 0) = T0 ; − |
∂x |
x=−b = |
|
|
[T1 − T |
(−b)]; |
− |
∂x |
|
x=b = |
|
[T (b) − T1 ], |
||||||||||||||||||||||||||||||||
|
k |
|
k |
||||||||||||||||||||||||||||||||||||||||||
|
|
|
|
52

цилиндр
|
|
T1 −T |
|
|
|
2 |
|
|
∞ |
|
J0 (rcn ) |
|
|
|
|
|
|
|
|
|
|
|
|
|
|
|
|
|
|
|
|
|
|
|
|
|
|
|
|
|
|
|||||||||
|
|
= |
|
|
∑ |
|
|
|
|
|
exp(−acn2t); J0 (Rcn ) = 0; |
|
||||||||||||||||||||||||||||||||||||||
|
|
|
|
|
|
|
|
|
|
|
|
|
|
|
|
|
||||||||||||||||||||||||||||||||||
|
|
T −T |
|
R n=1 |
|
c J |
|
(Rc ) |
|
|
|
|
|
|
|
|
|
|
|
|
|
|
|
|
|
|
|
|
|
|
|
|
|
|
|
|||||||||||||||
1 |
0 |
|
|
|
|
|
|
|
|
|
|
|
n 1 |
|
|
n |
|
|
|
|
|
|
|
|
|
|
|
|
|
|
|
|
|
|
h |
|
|
|
|
|
|
|
|
|
|
|||||
|
|
T1 −T |
|
|
|
2 |
|
|
∞ |
|
|
|
|
|
|
|
|
|
|
|
|
|
|
|
|
|
|
|
|
|
|
|
|
|
J0 (rβn ) |
|
|
|
|
|
||||||||||
|
|
|
|
|
|
|
|
|
|
|
2 |
|
|
|
|
|
|
|
|
|
|
|
|
|
|
|
|
k |
|
|
|
|
|
|||||||||||||||||
|
|
|
|
|
= |
|
|
|
|
∑exp(−aβnt) |
|
|
|
|
|
|
|
|
|
|
|
|
|
|
|
|
|
|
|
|
|
|
|
; |
|
|||||||||||||||
|
|
T0 −T1 |
|
|
|
|
|
h |
|
|
2 |
|
|
|
|
|
|
|
|
|
|
|||||||||||||||||||||||||||||
|
|
|
|
R n=1 |
|
|
|
|
|
|
|
|
|
|
|
|
|
|
|
|
2 |
J0 (Rβn ) |
|
|||||||||||||||||||||||||||
|
|
|
|
|
|
|
|
|
|
|
|
|
|
|
|
|
|
|
|
|
|
|
|
|
|
|
|
|
|
|
|
+βn |
|
|
||||||||||||||||
|
|
|
|
|
|
|
|
|
|
|
|
|
|
|
|
|
|
|
|
|
|
|
|
|
|
|
|
k |
|
|
|
|
|
|
|
|
|
|
|
|
|
|
||||||||
|
|
|
|
|
|
|
|
|
|
|
|
|
|
|
|
|
|
|
|
h |
|
|
|
|
|
|
|
|
|
|
|
|
|
|
|
|
|
|
|
|
|
|
|
|
|
|
|
|||
|
|
|
|
|
|
|
β |
n |
J |
|
(Rβ |
n |
) + |
|
|
J |
|
|
(Rβ |
n |
) |
= 0; |
|
|
|
|
|
|
|
|
|
|||||||||||||||||||
|
|
|
|
|
|
|
0 |
k |
|
|
0 |
|
|
|
|
|
|
|
|
|
||||||||||||||||||||||||||||||
|
|
|
|
|
|
|
|
|
|
|
|
|
|
|
|
|
|
|
|
|
|
|
|
|
|
|
|
|
|
|
|
|
|
|
|
|
|
|
|
|||||||||||
|
|
|
T (r, 0) =T ; |
|
− k |
∂T |
|
r |
= |
R |
= h[T (R) −T ], |
|
||||||||||||||||||||||||||||||||||||||
|
|
|
|
|
|
|||||||||||||||||||||||||||||||||||||||||||||
|
|
|
|
|
|
|
|
|
|
|
|
|
|
0 |
|
|
|
|
|
|
|
∂r |
|
|
|
|
|
|
|
|
|
|
|
|
|
1 |
|
|
|
|||||||||||
сфера |
|
|
|
|
|
|
|
|
|
|
|
|
|
|
|
|
|
|
|
|
|
|
|
|
|
|
|
|
|
|
|
|
|
|
|
|
|
|
|
|
||||||||||
|
|
|
|
|
|
|
|
|
|
|
|
|
|
|
|
|
|
|
|
|
|
|
|
|
|
|
|
|
|
|
|
|
|
|
|
|
|
|
|
|
|
|
|
|
|
|
|
|||
|
T −T |
|
|
2R |
|
|
∞ |
|
(−1)n |
|
|
|
nπR |
|
|
|
|
|
|
|
|
|
|
|
|
|
|
|
|
|
|
|
|
|||||||||||||||||
|
1 |
|
= |
|
|
|
|
|
|
|
∑ |
|
|
|
|
sin |
|
|
|
|
|
|
|
|
|
|
exp(−an2 |
π2t / R2 ); |
|
|
|
|||||||||||||||||||
T1 −T0 |
|
πR |
2 |
|
|
n |
|
|
|
|
|
|
R |
|
|
|
|
|
|
|||||||||||||||||||||||||||||||
|
|
|
|
|
|
n=1 |
|
|
|
|
|
|
|
|
|
|
|
|
|
|
|
|
|
|
|
|
|
|
|
|
|
|
|
|
|
|
|
|
|
|||||||||||
|
|
|
|
|
|
|
|
T (r, 0) =T0 ; T (R, t) =T1; |
|
|
|
|
2 |
|
|
|
||||||||||||||||||||||||||||||||||
|
|
|
|
|
2 |
h |
|
|
|
|
|
|
|
|
|
|
|
|
|
|
|
|
|
|
|
|
|
|
R |
2βn2 |
|
|
h |
|
|
|
|
|||||||||||||
|
T −T1 |
|
|
k |
|
|
|
∞ |
|
|
|
|
|
|
|
|
|
|
|
|
|
|
|
|
|
|
|
|
|
|
|
|
+ R |
k |
−1 |
|
|
|
|
|||||||||||
|
= |
|
|
|
∑exp(−aβn2 ) |
|
|
|
|
|
|
|
|
|
|
|
|
|
|
|
|
|
|
|
|
|
|
|
|
|
× |
|||||||||||||||||||
|
T0 −T1 |
|
|
|
|
|
|
|
|
|
|
2 |
|
|
|
|
|
h |
|
h |
|
|
|
|||||||||||||||||||||||||||
|
|
|
r |
|
|
n=1 |
|
|
|
|
|
|
|
|
|
|
|
|
|
2 |
|
|
2 |
+ R |
|
− |
|
|
||||||||||||||||||||||
|
|
|
|
|
|
|
|
|
|
|
|
|
|
|
|
|
|
|
|
|
|
|
|
βn |
|
R |
|
|
βn |
|
|
R |
k |
1 |
|
|||||||||||||||
|
|
|
|
|
|
|
|
|
|
|
|
|
|
|
|
|
|
|
|
|
|
|
|
|
|
|
|
|
|
|
|
|
|
|
|
|
k |
|
|
|
|
|
||||||||
|
|
×sin(Rβn )sin(rβn ); Rβnctg(Rβn ) + R |
h |
−1 = 0; |
|
|||||||||||||||||||||||||||||||||||||||||||||
|
|
k |
|
|||||||||||||||||||||||||||||||||||||||||||||||
|
|
|
|
|
|
|
|
|
|
|
|
|
|
|
|
|
|
|
∂T |
|
|
|
|
|
|
|
|
|
|
|
|
|
|
|
|
|
|
|
||||||||||||
|
|
|
|
|
|
|
|
|
|
|
|
|
|
|
|
|
|
|
|
r=R = h[T |
(R) −T1 ]. |
|
|
|
||||||||||||||||||||||||||
|
|
|
|
|
|
|
|
|
|
|
|
|
|
|
|
|
|
|
|
|
|
|||||||||||||||||||||||||||||
|
|
|
T (r, 0) =T0 ; − k |
∂r |
|
|
|
|
||||||||||||||||||||||||||||||||||||||||||
|
|
|
|
|
|
|
|
|
|
|
|
|
|
|
|
|
|
|
|
|
|
|
|
|
|
|
|
|
|
|
|
|
|
|
|
|
|
|
|
|
||||||||||
Здесь erf (z) – хорошо известная функция ошибок, определяемая |
||||||||||||||||||||||||||||||||||||||||||||||||||
как |
|
|
|
|
|
|
|
|
|
|
|
|
|
|
|
|
|
|
|
|
|
|
|
|
|
|
|
|
|
|
|
|
|
|
|
|
|
|
|
|
|
|
|
|
|
|
|
|
||
|
|
|
|
|
|
|
|
|
|
|
erf (z) = |
|
2 |
|
|
∫z exp(−s2 )ds. |
|
|
|
|
|
|
|
|
||||||||||||||||||||||||||
|
|
|
|
|
|
|
|
|
|
|
|
π |
|
|
|
|
|
|
|
|
||||||||||||||||||||||||||||||
|
|
|
|
|
|
|
|
|
|
|
|
|
|
|
|
|
|
|
|
0 |
|
|
|
|
|
|
|
|
|
|
|
|
|
|
|
|
|
|
|
|
|
|
|
|
|
|||||
|
|
|
|
|
|
|
|
|
|
|
|
|
|
|
|
|
|
|
|
|
|
|
|
|
|
|
|
|
|
|
|
|
|
|
|
|
|
|
|
|
|
|
|
|
|
|
|
|
Также обозначены: k – коэффициент теплопроводности; β – отношение плотностей твердой фазы и расплава; X – толщина, размер грани или диаметр; x/b – относительная глубина прогрева; r/R – относительный радиус.
53
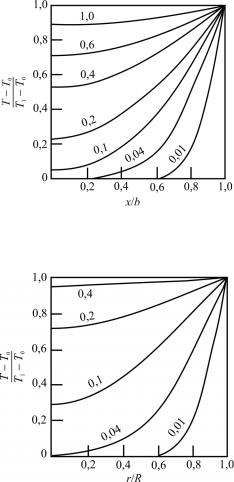
На рис. 5.3–5.6 показаны температурные профили при нестационарном режиме теплопроводности в полимерных телах простой геометрии. Во всех случаях: T0 – начальная температура при t = t0; T1 – температура, докоторойпрогреваетсявнешняяповерхностьполимера.
Значение a для исследованного полимера равно 1·10–7м2/с.
Рис. 5.3. Температурные профили при нестационарном режиме теплопроводности в полуограниченных плоских пластинах: T (x, 0) = T0 ;
T (±b, t) = T1; числаукривых– значениепараметраat/b2
Рис. 5.4. Температурные профили при нестационарном режиме теплопроводности в неограниченном цилиндре: T (r, 0) = T0 ;
T (R, t) = T1; числа у кривых – значение параметра at/R2
54
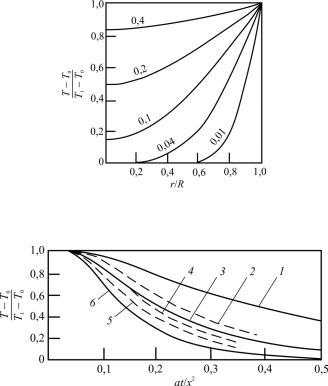
Прогрев полимера вплоть до его плавления, в том числе и в составе наполненного материала, приводит к изменению вязкости. Температурная зависимость динамического коэффициента вязкости аморфных полимеров определяется с помощью уравнения Вильямса – Ланделя – Ферри:
|
η |
|
|
|
−17,44(T −Tg ) |
|
log aT = log |
T |
|
= |
|
. |
|
|
51,6 − (T − T ) |
|||||
|
η |
|
|
|
|
|
|
|
g |
|
g |
|
По мере прогрева, начиная с Tg, полимер становится высокоэластичным материалом, а затем при Tm переходит в вязкотекучее (жидкое) состояние.
Рис. 5.5. Температурные профили при нестационарном режиме теплопроводности в сфере: T (r, 0) = T0 ;
T (R, t) = T1; числа у кривых – значения параметра at/R2
Рис. 5.6. Температура в центре полимерных тел различной формы в сравниваемое время: 1 – неограниченная пластина; 2 – квадратный стержень; 3 – неограниченный цилиндр; 4 – куб; 5 – цилиндр с L = D; 6 – сфера
55
При температуре плавления в кристаллической фазе частичнокристаллических полимеров осуществляется переход первого рода. Плавление кристаллической фазы происходит в интервале температур 10–30 оС, величина которого зависит от характера распределения размеров кристаллитов, степени их совершенства и скорости нагрева.
Обычно за Tm принимают значение температуры, соответствующее окончанию процесса плавления. Эта температура зависит от структуры полимера; при плавлении блок-сополимеров наблюдаются две температуры плавления, характерные для каждого из гомополимеров.
Температурная зависимость частично-кристаллических полимеров выше Tm подчиняется закону Аррениуса. Полиамиды, например, превращаются в низковязкие жидкости даже при температуре на несколько градусов выше Tm.
56
Лекция VI
Взаимосвязь реологических свойств и молекулярных характеристик полимерных материалов
В принципе, реологические свойства полимерных композиционных материалов, включая наполненные, зависят от реологических свойств полимерной основы или полимерного связующего, содержащего пластификатор. Реологические свойства полимеров зависят от их молекулярной массы, молекулярно-массового распределения и степени разветвленности молекул. Имеет значение и химическое строение (степень полярности) молекулярной цепи полимера.
Наиболее известная молекулярная теория вязкоупругого пове-
дения полимеров была разработана Ф. Бики. Основываясь на статистической теории сопротивления полимерного клубка, он принял в качестве допущений следующие ограничения: молекула полимера разделена на ряд «субцепей», каждая из которых ведет себя подобно «малой массе», прикрепленной к линейной пружине (упругому элементу). Затем он нашел формальное решение задачи для случая смещения каждой «субцепи» относительно своего равновесного положения. Ф. Бики исходил из представления о действии силы сдвига (F) на мономерные звенья при вращении полимерного клубка относительно центра масс:
F = 3kT ax
Na2 ,
где k – константа Больцмана; T – абсолютная температура определения; ax – величина смещения мономерного звена в направлении приложения силы сдвига; a – валентная связь между мономерными звеньями; N – числомономерных звеньеввгауссовойполимернойцепи.
Для механического сдвига Бики рассчитал диссипацию энергии при перемещении каждого элемента, умножая силу на скорость движения всех N сегментов относительно растворителя. Далее, суммируя диссипацию энергии для всей молекулы, Бики получил следующее выражение для относительного динамического коэффициента вязкости пластифицированного полимера:
57

η−η |
sw |
|
|
6 N |
|
|
γ |
2λ2 |
|
|
|
|
|
γ |
2λ2 |
|
|
|
||||
|
=1 |
− |
|
|
∑ |
|
|
|
|
1 |
|
|
2 − |
|
|
|
|
1 |
|
, |
(6.1) |
|
η0 −ηsw |
π |
2 |
n |
2 |
(n |
4 |
+ γ |
2 |
2 |
n |
4 |
+ γ |
2 |
2 |
||||||||
|
|
|
n=1 |
|
|
|
λ1 ) |
|
|
λ1 |
|
|
где η0 – вязкость полимера при скорости сдвига, стремящейся к 0; ηsw – вязкость пластификатора; γ – градиент скорости сдвига; λ1 – релаксационная константа Бики, которая выражается формулой
λ = |
12(η0 −ηsw )Mm |
, |
(6.2) |
|
|||
1 |
π2cRT |
|
где с – концентрация полимера в растворе с пластификатором. Параметр λ1 следует рассматривать как характерное время ре-
лаксации полимерной цепи. Видно также, что теория Бики учитывает зависимость динамического коэффициента вязкости от градиента скорости сдвига.
Вслучае полимерных материалов в «блоке», т.е. находящихся
врасплаве, рекомендуется использовать выражения (6.1) и (6.2), ис-
ключив значение вязкости пластификатора ηsw и заменив концентрацию полимера в растворе с на его плотность ρ. Тогда для полимерных расплавов получим соответствующие уравнения:
η |
|
6 |
N |
|
|
γ |
2λ2 |
|
|
|
||
|
=1− |
|
|
∑ |
|
|
|
|
1 |
|
|
2 |
η0 |
π |
2 |
n |
2 |
(n |
4 |
+ γ |
2 |
2 |
|||
|
|
n=1 |
|
|
|
λ1 ) |
где
λ1 = 12η0 Mm . π2ρRT
− |
|
|
γ |
2λ2 |
|
|
|
|
|
|
|
1 |
|
, |
|
n |
4 |
+ γ |
2 |
2 |
|||
|
|
|
λ1 |
|
(6.3)
(6.4)
Для большинства полимерных растворов и расплавов при очень низких скоростях сдвига динамический коэффициент вязкости не зависит от последней. С повышением скорости сдвига вязкость начинает уменьшаться от максимального значения η0 , соответствующего скорости сдвига, стремящейся к нулю. Фокс и Флори первыми
58
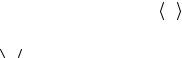
показали, что наибольшая ньютоновская вязкость η0 концентрированных растворов и расплавов линейных полимеров пропорциональна молекулярной массе, ниже некоторого критического значения Mmc ( η = KMm ), тогда как при молекулярной массе, превышающей критическую, вязкость очень быстро растет и становится пропорциональной Mm3,4 ( η = KMm3,4 ).
На рис. 6.1 представлены зависимости динамического коэффициента вязкости от молекулярной массы в логарифмических координатах для расплавов различных линейных полимеров. Параметр Xm, пропорциональный Mm, вычисляется по формуле
X |
m |
= s |
2 |
Zϕ |
pol |
/ M |
m |
v, |
|
|
0 |
|
|
|
где s0
– среднеквадратичный радиус инерции невозмущенного мо-
лекулярного клубка; Z – число атомов в основной цепи макромолекулы; v – удельный объем полимера; ϕpol – объемная доля полимера
в растворе.
Полагают, что критическая молекулярная масса – это величина, ниже которой переплетения молекул или их зацепления недостаточны для возникновения большого сопротивления течению. При этом действие растворителя или пластификатора эквивалентно уменьшению значения Mm.
Из формул (6.1) и (6.3) видно, что относительные динамические коэффициенты вязкости (η−ηsw ) /(η0 −ηsw ) и η/ η0 являются функ-
цией только параметра γλ1 . Для конкретного полимерного связующего (при фиксированных значениях с или ρ, а также Mm) величина λ1 зависит лишь от абсолютной температуры определения. При из-
вестных значениях массовой концентрации полимера в растворе (с), молекулярной массы полимера (Mm) и абсолютной температуры определения (Т) для установления аналитического вида зависимости η (γ) достаточно измерить η0.
59

Рис. 6.1. Логарифмическая зависимость вязкости от молекулярной массы для расплавов полимеров: 1 – полидиметилсилоксан, 2 – полиизобутилен, 3 – полибутадиен, 4 – политетраметил-n-фенил-силоксан, 5 – полиметилметакрилат, 6 – поливинилацетат, 7 – полистирол
60