
книги / Производство, облагораживание и применение нефтяного кокса
..pdfв пробирку смесь нагревают в печи со скоростью 4,5—5°С/мин дотемпературы, при которой резко понижается уровень воды в мано метрической трубке вследствие взрывообразного выделения газов. Эта температура и принимается за температуру самовоспламене ния кокса.
Автор совместно с И. Б. Минишевым изучал этим методом са мовоспламенение нефтяных коксов ФИПЗ, НУ НПЗ, КНПЗ (см. рис. 6, стр. 37). Сырые нефтяные коксы имеют температуру само воспламенения 330—350 °С; эта температура снижается при про каливании (минимальная температура достигается после прокали вания кокса до 800—900 °С). Наиболее резко температура само воспламенения снижается у порошкообразного кокса (на 60 °С), в то время как для коксов с установок замедленного коксования она становится ниже всего на 40—50 °С. Это согласуется с измене нием других параметров коксов при прокаливании (удельная по верхность, равновесная влажность и др.). По мере дальнейшего со вершенствования структуры кокса доступ окислителя в поры кок сов затрудняется, что ведет к повышению температуры самовос пламенения в интервале температур прокаливания. Как и следова ло ожидать, удаление сернистых соединений, влияя на удельную поверхность коксов, изменяет и склонность их к окислению.
Вполне понятно, что чем меньше содержится летучих в коксе, тем выше их температура самовоспламенения.
Из мелочи кокса ФНПЗ, содержащего 11% летучих, прокали ванием при 460 °С были изготовлены образцы с содержанием лету чих веществ 4,5; 2-,7 и 1,3%; для этих образцов получены следую щие температуры самовоспламенения:
Выход летучих |
Температура само! |
веществ |
°С |
1,3 |
400 |
2,7 |
387 |
4,5 |
375 |
11 (исходный) |
360 |
Установлено также, что при постепенном повышении в коксе сернистых соединений до 2,0% и зольных до 3,0% температура са мовоспламенения понижается примерно на 25—30 °С. Дальнейшее увеличение этих соединений в коксе мало сказывается на резуль татах опыта. Результаты экспериментов на полупромышленной установке с многоступенчато-противоточным аппаратом подтвер дили значения температур самовоспламенения нефтяных коксов с установок замедленного коксования, определенных в лаборатор ных условиях. Температуру самовоспламенения их при содержа нии летучих 7—8% следует принимать равной 340—360 °С.
Теплоемкость
Теплоемкость нефтяных коксов, так же как и других нефтепродук тов, зависит от их химического состава. Известно, что теплоем кость парафиновых углеводородов выше, чем ароматических. Так,
после депарафинизации теплоемкость масел понижается с 0,53 до 0,48 ккал/(кг-°С). Следовательно, теплоемкость нефтепродуктов можно рассчитать по химическому составу. Теплоемкость нефте продуктов >с увеличением .плотности (ароматичности) снижается Так, с повышением относительной плотности с 0,7 до 1,0 теплоем кость с нефтепродукта понижается соответственно с 0.50 до 0,420 ккал/(кг-°С) [195].Зависимость теплоемкости нефтяного кок са от состава углеродистого вещества в общем случае может быть выражена формулой, сходной с формулой Шлепфера и Деб руннера [65].
Поскольку для сухого кокса содержание воды (W) равно нулю,' в конечном счете формула для определения теплоемкости малосер нистого сухого кокса
ВW
с ~ ~ 100 *С в |
с ° ' 100 |
запишется в следующем виде:
В |
100 —В |
(15) |
с = 100 ’ СВ + СВ ‘ |
ю о |
где с — теплоемкость кокса, ккал/(кг*°С) ; В — содержание углеро дистого вещества в коксе, %; св, cv — соответственно теплоемкости углеродистого вещества и водорода, ккал/(кг-°С).
Из формулы (15) вытекает, что чем выше Н:С, тем должна быть больше теплоемкость кокса, так как cv больше св в несколько раз. В литературе сведений о теплоемкости нефтяных коксов, за исключением единичных данных, приведенных в работе [65], почти нет. Более полно представлены данные по удельной теплоемкости углей и получаемых из них коксов. Для различных углей приво дятся [8] значения удельной теплоемкости в пределах 0,25— 0,38 ккал/(кг*°С). По мере нагрева структура углей становится однородной и после прокаливания до 1100°С значения теплоемко стей различных коксов, полученных из этих углей, сближаются (0,21—0,22 ккал/(кг-°С)). При достижении температуры графита-
ции теплоемкости |
всех углеродистых |
веществ снижаются до |
0,165 ккал/(кг-°С). |
Сходные данные по |
теплоемкости нефтяного |
кокса после прокаливания при 1700 °С, сопровождающегося непре рывным снижением соотношения Н:С, — 0,22 ккал/(кг-°С), приво дятся в работе [65]. Подставляя значение ср для прокаленного кокса в формулу (15) и принимая для кокса замедленного
коксования выход |
водорода |
около 3,5% и ср водорода |
3,4 ккал/(кг-°С) [70], |
находим |
удельную теплоемкость сырого |
нефтяного кокса равной 0,34 ккал/(кг-°С). Близкое значение удель ной теплоемкости — 0,40 ккал/(кг-°С) для сырого нефтяного кокса приводит В. К. Замолуев [65]. При нагреве углеродистых мате риалов, в том числе нефтяных коксов, теплоемкость изменяется по сложной зависимости. С одной стороны, в результате снижения значения Н:С она уменьшается и стремится к своему предельному значению 0,165 ккал/(кг-°С), с другой стороны — высокие темпе-
ратуры способствуют повышению теплоемкости коксов. Это хорошо1 иллюстрируется данными по теплоемкости угля (С =82,76; Н= 5,7,6; N = 2,80; S == 0,8; 0 2= 9,01 % ), приведенными на рис. 46. Видно, что истинная теплоемкость повышается монотонно с 0,32 до 0,430 ккал/(г-°С), в то время как кажущаяся теплоемкость ме няется по сложной зависимости. Указанным обстоятельством обыч но пользуются при расчете теплового эффекта деструкции углеро дистых материалов. Эндотермический эффект (Qi) деструкции угля ярко выражен до 675 °С и составляет — 49,55 кал/г, а при
Температурите
Рис. 46. Тепловые эффекты пиролиза га зового угля. (Ш. Полысасвская 2, пл. Полысасвскнй) при скорости нагревания 10 *С, мин:
/ — истинная теплоемк |
2 — кажущаяся |
|
теплоемкость. |
|
|
дальнейшем нагревании |
до 900 °С выявляется экзотермический |
|
эффект (Q2), 'величина |
которого весьма ощутима и равна |
|
44,32 кал/г. Суммарный |
тепловой эффект Q3 в целом невелик — |
|
5.23 кал/г. |
|
|
На практике чаще пользуются средней теплоемкостью — вели чиной условной и постоянной для заданного интервала температур. При этом, определяя расход тепла, можно получить тот же резуль тат, что и при использовании переменной теплоемкости, зависящей от температуры. Пользуясь методом количественной термографии,. И. Д. Волошин [37] определил некоторые теплофизические пара метры коксов замедленного коксования и порошкообразного кокса. Так, он установил, что эффективные теплоемкости коксов замед ленного коксования и полученных в кипящем слое, различаются.
В табл. 23 приведены средние удельные теплоемкости кокса за медленного коксования, графита и угля.
По разнице между общими затратами тепла (?общ—2(Сэф/Л*0 и расходом тепла на нагрев кокса QK=2(cA£t) и на удаление лету чих <3л= (&GiCPiti) определен тепловой эффект деструкции кокса
замедленного коксования. Эндотермический эффект в интервале температур от 400 до 700 °С составляет — 10 кал/г, а экзотерми-
1ва
Т а б л и ц а 23. Средние теплоемкости (в ккал/кг °С) нефтяного кокса, трафита и угля
Температурный |
Нефтяной |
|
Гра |
Температурный |
Нефтяной |
|
Гра |
кокс |
Уголь |
кокс |
Угрль |
||||
интервал. |
замедленного |
фит |
интервал. |
замедленного |
фит |
||
°С |
коксования |
|
|
|
коксования |
|
|
2 0 - 2 0 0 |
0,289 |
0,220 |
0,226 |
20-700 |
0,375 |
0,322 |
0,330 |
20-300 |
0,310 |
0,250 |
0,255 |
20-800 |
0,384 |
0,334 |
0,342 |
20—400 |
0,329 |
0,276 |
0,280 |
20—900 |
0,390 |
0,346 |
0,353 |
20-500 |
0,348 |
0,294 |
0,300 |
20— 1000 |
0,394 |
0,355 |
0,362 |
20—600 |
0,363 |
0,311 |
0,317 |
|
|
|
|
•ческий эффект деструкции при дальнейшем нагревании до 1000 °С возрастает до 14,5 кал/г. Суммарный тепловой эффект положи телен и (Зз=4,5 кал/г. Энтальпию кокса с достаточной для практи ческих целей точностью при температурах свыше 1000°С можно определять по графику, изображенному на рис. 47.
Для получения данных по теплоемкости нефтяных коксов, раз личающихся способом получения и качеством сырья, необходимы дополнительные исследования. Важно также установить суммар ный тепловой эффект реакций деструкции нефтяных коксов в более широком диапазоне температур (от 0 до 1600 °С).
Теплопроводность
Теплопроводность связана непосредственно с теплоемкостью; для тяжелых нефтепродуктов она возрастает с повышением их тепло емкости и плотности и выражается следующей зависимостью [195]
|
^ = |
0 , 325^ - 0,02 |
( 16) |
|
где |
Сро — теплоемкость при |
постоянном давлении |
и температуре |
|
|
30 °С, ккал/('КГ-0С) ; d — плотность при |
температуре t , |
||
|
кг/л. |
|
|
|
Теплопроводность нефтяных продуктов по мере их утяжеления |
||||
возрастает. Так, для нефти |
(р4 |
=0,890) она равна |
0,113, для ма |
|
зута |
(Q4° =0,898) — 0,123 и для |
крекинг-остатка |
(с4 = 1,054) — |
0,134 ккал/(м-ч-°С). С повышением температуры нагрева тепло проводность нефтепродуктов, как следует из формулы (16), сни
жается, например, дизельного топлива с 0,101 |
при 20 °С до |
0,093 |
||||
при 100°С [195]. |
|
|
(плотности) |
кокса, как и следовало |
||
Увеличение ароматичности |
||||||
ожидать, также |
приводит |
к |
повышению |
его |
теплопроводности. |
|
Теплопроводность |
сырого |
нефтяного кокса |
в порошке |
0,14— |
0,16 ккал/(м*ч-°С). Однако при повышении температуры нагрева кокса, в отличие от жидких нефтепродуктов, теплопроводность его не уменьшается, а увеличивается.
По данным [65], теплопроводность порошкообразного кокса при 1700°С составляет 0,215 ккал/(м-ч-°С), при 1800—1900 °С
(начало графитации) достигает 0,26—0,27 ккал/(м*ч*°С) и остает ся на этом уровне до конца графитации. В работе [8] отмечается увеличение теплопроводности углеродистых веществ с повышением температуры пропорционально увеличению разности четвертых степеней абсолютных температур теплоносителя и нагреваемого тела.
На теплопроводность кокса влияют влажность, пористость, раз мер частиц, зольность. В связи с разными теплопроводностями углеродистого вещества кокса (0,1—0,15 ккал/(м*ч*°С), воды (0,506 ккал/(м*ч*°С), воздуха (0,02 ккал/(м-ч-°С) и золы общую теплопроводность кокса находят в зависимости от соотношения в -нем этих компонентов. При добавлении к сухому коксу до 30% воды теплопроводность его увеличивается в 2—2,5 раза. Чем выше пористость углеродистого вещества, тем меньше его теплопровод ность. По данным [9], при увеличении насыпной массы угля с 0,600 до 0,950 г/см3 теплопроводность его возрастает на 29%.
Практический интерес представляет зависимость теплопровод ности кокса от его гранулометрического состава. Очевидно, при дайной объемной массе теплопроводность крупных кусков будет выше, чем мелких, из-за возникновения дополнительных тепловых сопротивлений в мелких кусках. Опытами, проведенными при 400°С, установлено, что теплопроводность кокса размером частиц менее 0,75 мм равна 0,14 ккал/(м*ч-°С), а фракций 2—6 мм — 0,20 ккал/(м-ч*°С). В интервале 0—1000°С средняя теплопровод ность мелких углеродистых частиц 0,11—0,23, а крупных 0,18— 0,44 ккал/(м-ч-°С). Наиболее сильно возрастает теплопроводность нефтяных коксов при нагреве до температур выше 700 °С, что объясняется повышением роли теплопередачи излучением и появ лением в межкусковом пространстве углеводородных газов, со держащих значительное количество водорода. Результаты иссле дований при 900—1200 °С в движущемся слое кокса [165] показа ли, что кажущаяся теплопроводность для частиц нефтяною кокса размерами 6—7 мм при 900—1000 °С равна 1,6 ккал/(м-ч-°С).
Близкие значения теплопроводности сухой шихты приводятся в работе [134]. По данным этой работы, для фракции сухого кок са 0—10 мм при температурах от 100 до 800 °С теплопроводность повышается с 0,5 до 1,3 ккал/(м-ч-°С).
Коэффициент температуропроводности
Коэффициент температуропроводности а связан с плотностью d% теплопроводностью К и теплоемкостью ср следующей известной за висимостью:
_ J , ____Я_
а ~ cpd ~ с'
где Ср — удельная весовая теплоемкость, ккал/(кг-°С) ; с' —удель ная объемная теплоемкость, ккал/(м3-°С).
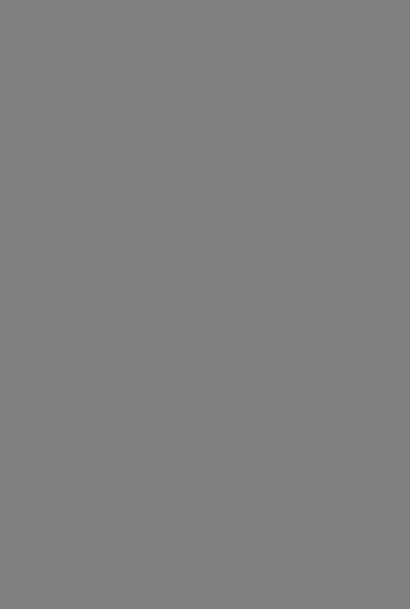
где Rx — расстояние между термопарами, измеряющими темпера туру на оси образца и на расстоянии от нее 0,707 радиуса образ ца, м; Ат— время запаздывания температуры на оси образца по отношению к температуре, измеряемой на расстоянии Rx, ч (полу чается из диаграммной ленты опыта); е — поправка на перемен ность скорости нагрева образца; Ô— поправка на зависимость фи зических параметров от температуры.
Полученное значение а относится к средней по сечению темпе ратуре, при которой по диаграмме вычислена Ат (рис. 49). Как
Рис. 49. Зависимость эффективного коэффициента температуропроводности нефтяного кокса от температуры при диаметре частиц (в мм):
У— 0.1—1.0; 2 — 1.0-2,0; 3 — 2,0-3,0; 4 — 3.0-5.0.
видно, ширина полосы разброса опытных точек с ростом диаметра частиц кокса и с повышением температуры увеличивается. Темпе ратуропроводность кокса значительно ниже, чем металлов (тем пературопроводность алюминия 0,52 м2/ч; железа 0,022 м2/ч; стали
углеродистой 0,0202 м2/ч; чугуна 0,0278 м2/ч), и |
приближается |
|
к температуропроводности |
таких материалов, |
как асбест |
(0,000324 м2/ч), влажная земля |
(0,000693 м2/ч). |
|
С повышением температуры прокаливания температуропровод ность изменяется по сложной зависимости; при этом повышается теплопроводность, теплоемкость н плотность кокса. В целом, как следует из рис. 49, с повышением температуры температуропровод ность нефтяных коксов возрастает.
Коэффициент линейного термического расширения (а) различ ных коксов определяет их поведение при прокаливании и графита-
ции и выражается следующей зависимостью:
АI л - l0bt
где Д/ — удлинение образца при увеличении температуры на At; io — первоначальная длина -образца.
Углеродистые материалы, как всякие твердые тела, при нагре вании расширяются, но в отличие от большей их части могут пре терпевать и усадку, особенно интенсивную на начальной стадии прокалки. Известно, что коэффициент линейного термического рас ширения у металлов (никель, вольфрам, палладий, серебро, хром) сохраняет постоянное значение до высоких температур, в то время, как у углеродистых веществ при высоких температурах он сущест венно изменяется.
Зависимость коэффициента линейного термического расшире ния графитированных материалов от температуры для участка на грева выше 600 °С может быть выражена следующим путем:
аг = авоо + 7■10-10 (Т — 600)
Коэффициент линейного термического расширения у углероди стых материалов даже при высоких температурах в 6—30 раз ни же, чем у металлов. В то же время коксы растрескиваются при резком изменении температуры в процессе прокаливания и графи та ции тем в большей степени, чем выше а. Отсюда следует, что при изменении скорости нагрева углеродистых материалов необхо димо учитывать их коэффициент линейного термического расши рения. Допустимая скорость (Удоп) нагрева углеграфитовых мате риалов качественно может быть оценена формулой [120], пред ложенной для определения Удоп нагрева керамических изделий:
v |
__ |
G ДОП (1 -----И ) а |
ИД°п - |
A OLE S 2 |
где Кдоп — скорость нагрева, °С/ч; Gaon— предел прочности угле графитового бруска при изгибе, кгс/см2; А — коэффициент формы тела; т] — коэффициент Пуассона( поперечного сжатия); а — коэф фициент температуропроводности, м2/ч; а — коэффициент линейно го термического расширения, 1/°С; Е — модуль упругости при изги бе, кгс/м2; 5 — толщина (высота) изделия, см.
Из этой формулы можно заключить, что в процессах прокали вания анодов и графитацни электродных изделий брака по трещи нам будет тем больше, чем больше сечение (высота), коэффициент линейного термического расширения и чем ниже коэффициент температуропроводности изделия. Поэтому перед нефтепереработ чиками стоит задача получения таких компонентов электродных масс, которые бы при обжиге и графитации давали изделия, обла дающие низкими значениями а и высокими значениями а.
По данным электродных заводов, средний коэффициент линей ного термического расширения графитированных образцов в ип-
тервале температур 100—2000 °С различается |
для разных нефтя |
|||
ных коксов весьма существенно: |
|
|
||
Образцы графитнроваиных изделий, изготовленных |
1 |
•106 |
||
из нефтяного кокса |
|
|||
Новобакинского НПЗ |
\ |
Замедленное коксо- |
5,05 |
|
Надворнянского НПЗ |
I |
ванне |
4,35 |
|
Бакинского НПЗ |
J |
Коксование в кубах |
3,60 |
|
Грозненского НПЗ |
3,90 |
По-видимому, на показатель а влияет не только качество сырья, но и способ коксования. Влияние качества сырья на а гото вых электродных изделий изучалось P. Н. Гимаевым, 3. И. Сюняе-
вым, Г. Ф. Давыдовым, О. Н. Тиняковым |
|
|
|
|
^ |
|||||||||
и А. В, Цинько. Нефтяные остатки пря |
|
|
|
|
|
|||||||||
могонного |
и вторичного |
происхождения |
|
|
|
|
|
|||||||
были разделены |
на смолисто-масляную |
|
|
|
|
|
||||||||
и асфальтовую |
часть |
на |
лабораторной |
|
|
|
|
|
||||||
установке добей >в БашНИИ НП. Из них |
|
|
|
|
|
|||||||||
на пилотной |
установке, |
моделирующей |
|
|
|
|
|
|||||||
промышленные установки |
замедленного |
|
|
|
|
|
||||||||
коксования, были получены образцы кок |
|
|
|
|
|
|||||||||
са. В Государственном научно-исследова |
|
|
|
|
|
|||||||||
тельском институте электродной промыш |
|
|
|
|
|
|||||||||
ленности |
из |
этих образцов |
кокса были |
|
|
|
|
|
||||||
изготовлены |
графитированные |
электро |
|
|
|
|
|
|||||||
ды. У полученных электродов определя |
|
|
|
|
|
|||||||||
ли а в диапазоне температур |
100—900 °С. |
|
|
|
|
|
||||||||
Из рис. 50 видно, что качество сырья, его |
|
|
|
|
|
|||||||||
состав и температура прокаливания ока |
|
|
|
|
|
|||||||||
зывают |
на |
коэффициент |
термического |
|
|
т |
600 еоо |
|||||||
расширения |
электродов |
весьма |
заметное |
|
|
|||||||||
влияние. На основании результатов этих |
|
Температура, °С |
|
|||||||||||
Рис. 50. Влияние вида сырья и |
||||||||||||||
опытов |
рекомендуется |
для |
получения |
температуры |
прокаливания |
на |
||||||||
нефтяных |
пеков |
и изготовления из |
них |
коэффициент |
термического |
рас |
||||||||
ширения |
электродов. |
|
|
|||||||||||
электродов |
с низкими |
значениями а |
ис |
Сырье: |
1 — крекинг-остаток |
НУ |
||||||||
пользовать нефтяные остатки, не содер |
ИПЗ: 2 — дсасфальтизат гудрона |
|||||||||||||
НУ НПЗ: 3 — дсасфальтизат гуд |
||||||||||||||
жащие асфальтены (газойли термическо |
рона ФНПЗ; |
4 — деасфальтизат |
||||||||||||
го и каталитического крекинга, остатки, |
крекинг-остатка НУ |
ИПЗ. |
|
|||||||||||
полученные при производстве печной са |
|
|
|
|
|
|||||||||
жи, деасфальтизаты и др.) |
и предварительно термически обрабо |
танные, например, на установках термического крекинга. Подбо ром сырья представляется возможным снизить а графитированных изделий из нефтяных коксов примерно в 2 раза.
По данным [198], коэффициент линейного термического расши рения неграфитированных материалов примерно в 2 раза выше, чем графитированных. При .изготовлении электродных масс важно ие только подобрать сырье, но и использовать такие связующие вещества на нефтяной основе, которые при обжиге образовывали
бы кокс, близкий или идентичный по своим свойствам наполните лю. Кроме того, работникам электродной промышленности необхо димо для каждого вида изделия устанавливать допустимые скоро сти нагрева, учитывающие коэффициенты термического расшире ния его компонентов.
Теплофизические характеристики нефтяных коксов были в даль нейшем использованы при проектировании опытных и опытно-про мышленных установок облагораживания. Удовлетворительное сов падение расчетных тепловых балансов с фактически полученными на опытных установках показывает их надежность и целесообраз ность использования.
Механические свойства
Сырые нефтяные коксы состоят из кристаллитов, между кото рыми существуют сложные перекрещивающиеся валентные связи. Эти связи стабилизируют структуру в трехмерной плоскости и при дают всей системе определенную прочность.
Поскольку нефтяные коксы имеют неоднородную микро- и мак роструктуру (доли участков волокнистого и точечного строения не одинаковы), механические свойства их существенно различаются.
Механические свойства характеризуют работоспособность неф тяных коксов и изготовленных из них изделий. В результате воз действия внешних сил на твердое тело изменяются его размеры и форма, в зависимости от характера и величины приложенных сил, вызывая вначале деформацию, а затем разрушение. Нефтяные коксы различного происхождения, особенно изделия из них, в свя зи со специфичностью структуры разрушаются по определенным, характерным для данного углеродистого вещества участкам, обла дающим наименьшим сопротивлением разрыву. В связи с этим важным свойством углеродистого вещества, как и любого твердо го тела, является величина сопротивления разрушению.
До наступления разрушения углеродистых веществ наблюдает ся более или менее широкая область упругих и необратимых пла стических деформаций. При упругой деформации после снятия внешних сил тело принимает прежнюю форму, в то время как при пластической деформации его размеры и далее свойства изме няются.
Для оценки поведения коксов при гидрорезке, хранении, транс портировании, дроблении и использовании в промышленности важ но знать такие его свойства, как механическая прочность, коэф фициент упругого расширения, коэффициенты релаксации и проч ности частиц и их изменения в процессе термообработки.
Механическая прочность кускового кокса определяется чаще всего методом раздавливания или толчения. Испытанию на раз давливание обычно подвеграют образцы — кубики размерами 40X40X40 см. Поверхность кубиков должна быть отполированной и без трещин. Предварительно определяют размеры образца мик