
книги / Экономика отраслей машиностроения
..pdf
Qосн.мат = 152 · 1,2 = 182,4 кг.
Таблица1 5
Расчет чистого веса станка
Подузел |
Конструкци- |
Чугун, |
Сталь специального |
Вес узла, |
|
онная сталь, кг |
кг |
назначения, кг |
кг |
||
|
|||||
Приводной механизм |
48 |
– |
– |
48 |
|
Механизм управления |
12 |
– |
8 |
20 |
|
Механизм создания |
23 |
– |
– |
23 |
|
давления |
|||||
|
|
|
|
||
Корпус |
61 |
– |
– |
61 |
|
Итого |
144 |
|
8 |
152 |
Таблица 1 6
Расчет стоимости материалов
|
|
Вес |
Цена |
Стои- |
Вес |
Цена |
Стои- |
|
|||
|
Чистый |
мость |
отхо- |
мость |
Кисп |
||||||
Материал |
вес, кг |
метал- |
металла |
метал- |
отхо- |
дов, |
отходов, |
||||
|
|
ла, кг |
руб/кг |
ла, руб. |
дов, кг |
руб/кг |
руб. |
|
|||
|
|
|
|
|
|
|
|||||
Сталь |
|
|
|
|
|
|
|
|
|
|
|
конст- |
|
|
|
|
|
|
|
|
|
|
|
144 |
172,8 |
22,6 |
3905,28 |
28,8 |
|
4 |
|
115,2 |
|
1,2 |
|
рукцион- |
|
|
|
||||||||
|
|
|
|
|
|
|
|
|
|
|
|
ная |
|
|
|
|
|
|
|
|
|
|
|
Чугун |
|
0 |
|
0 |
0 |
|
|
|
0 |
|
|
Сталь |
|
|
|
|
|
|
|
|
|
|
|
специаль- |
|
|
|
|
|
|
|
|
|
|
|
8 |
9,6 |
38,4 |
368,64 |
1,6 |
|
8 |
|
12,8 |
|
|
|
ногона- |
|
|
|
|
|||||||
|
|
|
|
|
|
|
|
|
|
|
|
значения |
|
|
|
|
|
|
|
|
|
|
|
Итого |
|
|
|
4273,92 |
|
|
|
|
128,00 |
|
|
Общая сумма затрат на основные материалы определяется по формуле
i
Зосн.мат QЦмK QобщЦо ,
1
где Q – расход (вес) данного вида материала; i – число наименований различных материалов и групп изготавливаемых деталей; Цм – цена одного килограмма данного вида материала; Kтз – коэффициент,
101
учитывающий транспортно-заготовительные расходы, Kтз = 1,08; Qо – вес отходов; Цo – цена отходов,
Зосн.мат = 4273,92 · 1,08 –128 = 4487,83 руб.
Общие затраты наматериалы определяются следующимобразом:
Зобщ = Зосн.мат + Зк.осн.мат Kтз,
где Зк.осн.мат – стоимость покупных комплектующих изделий; Расчет затрат на покупные комплектующие:
Зк.осн.мат = 34839 · 1,01 = 35187,39 руб.,
Зoбщ = Зосн.мат + Зк.осн.мат = 4487,83 + 35187,39 = 39675,22 руб.
Таблица 1 7 Расчет затрат на покупные комплектующие
№ |
Наименование |
|
Количество |
Планово- |
Сумма |
и тип комплектующих |
|
комплектующих |
заготовительная |
затрат, |
|
п/п |
|
||||
|
изделий |
|
изделий, шт. |
цена, руб/шт. |
руб. |
1 |
2 |
|
3 |
4 |
5 |
|
|
|
Блок привода |
|
|
1 |
Бoлт M10–6g×45 |
|
4 |
18 |
72 |
2 |
Винт A.M3–6g×8 |
|
20 |
6 |
120 |
3 |
Винт A.M4–6g×11 |
|
4 |
7 |
28 |
4 |
Винт M6–6g×6 |
|
3 |
10 |
30 |
5 |
Винт M6–6g×12 |
|
2 |
10 |
20 |
6 |
Bинт M6–6g×18 |
|
3 |
10 |
30 |
7 |
Винт A.M5–6g×14 |
|
2 |
8 |
16 |
8 |
Винт A.M6–6g×16 |
|
9 |
10 |
90 |
9 |
Винт M6–6g×14 |
|
2 |
10 |
20 |
10 |
Bинт M6–6g×16 |
|
8 |
10 |
80 |
11 |
Винт M6–6g×20 |
|
7 |
10 |
70 |
12 |
Винт M8–6g×20 |
|
6 |
12 |
72 |
13 |
Bинт M10–6g×60 |
|
4 |
18 |
72 |
14 |
Гайка М24–6Н |
|
1 |
25 |
25 |
15 |
Гайка МЗЗ–6Н |
|
1 |
32 |
32 |
16 |
Кольцо А55 |
|
1 |
20 |
20 |
17 |
Кольцо А68 |
|
2 |
22 |
44 |
18 |
Кольцо А110 |
|
2 |
25 |
5 |
19 |
Подшипник 46108 |
|
1 |
30 |
30 |
102
|
|
|
Продолжение |
табл. 1 7 |
||
|
|
|
|
|
|
|
1 |
2 |
3 |
|
4 |
|
5 |
20 |
Подшипник 46916 |
1 |
|
35 |
|
35 |
21 |
Подшипник 80106 |
1 |
|
40 |
|
40 |
22 |
Подшипник 80108 |
2 |
|
40 |
|
40 |
23 |
Подшипник 80916 |
1 |
|
45 |
|
45 |
24 |
Ремень зубчатый |
2 |
|
650 |
|
1300 |
СБ 4–71–16 |
|
|
|
|
|
|
|
|
|
|
|
|
|
25 |
Силовой блок |
1 |
|
20000 |
|
20000 |
FM STEPDRIVE |
|
|
|
|
|
|
|
|
|
|
|
|
|
26 |
Частотный преобразо- |
1 |
|
8000 |
|
8000 |
ватель L100 004NFE |
|
|
|
|
|
|
|
|
|
|
|
|
|
27 |
Шайба 5 65Г |
2 |
|
8 |
|
16 |
28 |
Шайба 6 65Г |
2 |
|
10 |
|
20 |
29 |
Шайба 6 |
3 |
|
5 |
|
15 |
30 |
Шпонка 6×6×13 |
1 |
|
12 |
|
12 |
31 |
Шпонка 6×6×16 |
2 |
|
12 |
|
24 |
32 |
Штифт 2,8×26 |
1 |
|
15 |
|
15 |
33 |
Электродвигатель |
1 |
|
1500 |
|
1500 |
АИР56В4 |
|
|
|
|
|
|
|
|
|
|
|
|
|
34 |
Электродвигатель |
1 |
|
3600 |
|
3600 |
шаговый 86BYG350C |
|
|
|
|
|
|
|
|
|
|
|
|
|
|
Нажимное устройство |
|
|
|||
35 |
Винт A.M3–6g×8 |
2 |
|
6 |
|
12 |
36 |
Bинт A.M3–6g×Ю |
3 |
|
6 |
|
18 |
37 |
Bинт A.M5–6g×Ю |
2 |
|
8 |
|
16 |
38 |
Винт A.M5–6g×14 |
8 |
|
8 |
|
64 |
39 |
Винт A.M8–6g×100 |
1 |
|
12 |
|
12 |
40 |
Винт A.M5–6g×14 |
1 |
|
8 |
|
8 |
41 |
Винт M6–6g×8 |
2 |
|
10 |
|
20 |
42 |
Bинт M6–6g×12 |
4 |
|
10 |
|
40 |
43 |
Винт M8–6g×20 |
1 |
|
12 |
|
12 |
44 |
Гайка М8–6Н |
3 |
|
15 |
|
45 |
45 |
Гайка Ml 6–6H |
3 |
|
15 |
|
45 |
46 |
Гайка М24–6Н |
1 |
|
25 |
|
25 |
47 |
Кольцо А47 |
1 |
|
17 |
|
17 |
48 |
Подшипник 101 |
2 |
|
25 |
|
50 |
49 |
Подшипник 204 |
1 |
|
30 |
|
30 |
50 |
Подшипник 205 |
1 |
|
32 |
|
32 |
51 |
Пружина 335 |
1 |
|
16 |
|
16 |
52 |
Шайба 5 |
1 |
|
8 |
|
8 |
53 |
Шайба 8 |
3 |
|
10 |
|
30 |
103
|
|
|
Окончание |
табл. 1 7 |
||
|
|
|
|
|
|
|
1 |
2 |
3 |
|
4 |
|
5 |
54 |
Штифт 5×8 |
1 |
|
10 |
|
10 |
55 |
Штифт 6×16 |
1 |
|
12 |
|
12 |
56 |
Штифт 2,8×26 |
1 |
|
18 |
|
18 |
57 |
Штифт 10×25 |
1 |
|
16 |
|
16 |
Итого |
34839 |
|
|
|
|
|
Определение трудоемкости по данным производственнотехнической характеристики станка
Для определения трудоемкости изготовления узлов и деталей станка необходимы следующие данные: чистый вес станка и количество деталей в изделии (в том числе оригинальных и унифицированных), количество деталей, изготовленных излитья, литыхдеталей и др.
Общая трудоемкость определяется по формуле
Тобщ = Тлит + Тмех. + Тсб.сл. + Тпр,
где Тлит, Тмех, Тсб.сл, Тпр – трудоемкость изготовления соответственно литейных работ, механической обработки, слесарно-сборочных и
прочих работ.
Рассчитаем общую трудоемкость изготовления станка на основании его веса по формуле
Тобщ = Qобщ · tуд,
где Qобщ – общий вес спроектированного станка, кг; tуд – удельная трудоемкость станка–прототипа (чел.-ч/кг).
Qобщ = 152 кг;
tуд = 0,8 чел.-ч/кг;
Тобщ = 152·0,8 = 121,6 чел.-ч.
В процентном отношении от общей трудоемкости трудоемкость по видам работ может быть распределена в следующих отношениях:
Трудоемкость по видам работ |
Тобщ, чел.-ч |
Значение, чел.-ч |
|
Тлит = Тобщ·0,2 |
|
24,32 |
|
Тмех.обр = Тобщ·0,45 |
121,6 |
54,72 |
|
Тсл.сб = Тобщ·0,25 |
30,4 |
||
|
|||
Тпр = Тобщ·0,1 |
|
12,16 |
104
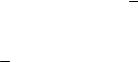
Исходя из трудоемкости отдельных тарифных ставок, рассчитаем тарифный ных рабочих.
видов работ Tj и средних фонд оплаты труда основ-
m
Зтар Tj Сч j ,
1
где m – виды работ (заготовительные, механообрабатывающие, сборочные, прочие); Сч j – часовая тарифная ставка.
Зтар = 24,32 · 55 + 54,72 · 83 + 30,4 · 65 + 12,16 · 65 = 8645,76 руб. Здоп = 0,15 · Зо = 1296,86 руб.
Зо = (Зтар + Здоп) · 0,3 = 2982,8 руб.,
где Зо – основная заработная плата рабочих; Здоп – дополнительная заработнаяплата; Зсоц– начислениявсоциальныефонды(страховойвзнос).
Принимаем разряды для рабочих по видам выполняемых работ в соответствии с табл. 18.
Таблица 1 8 Тарифные разряды для рабочих, выполняющих разные операции
Вид работ |
Разряд |
Тарифный коэф. |
Тариф за 1 ч |
|
|
|
в руб. |
Заготовительные работы |
3 |
2,97 |
55 |
Механообрабатывающие |
5 |
3,76 |
83 |
Сборочные работы |
4 |
3,34 |
65 |
Прочие работы |
4 |
3,34 |
65 |
Расходы на подготовку и освоение производства Зосв включают в себя затраты на проектирование нового изделия, разработку технологических процессов его изготовления, проектирование и изготовление оснастки, перепланировку и перестановку оборудования и т.д.:
Зосв = Зпр + Зп.п + Зхоз.осв,
где Зп.п – постоянные расходы служб подготовки (75 % к зарплате проектировщиков); Зхоз.осв – общехозяйственные расходы (50 %
105
к заработной плате проектировщиков); Зпр – затраты на проектирование новой конструкции.
Поскольку наши расчеты приблизительные, Зпр мы определяем по методу, основанному на объеме работ в натуральных единицах (чертежах) и нормативной трудоемкости выполненияединицыработ:
З т Л T З З ,
пр i i доп соц
1
где m – виды проектно-конструкторских работ при разработке проекта чертежей на оборудование; Лi – количество листов проектноконструкторской документации по каждому виду работ в комплекте чертежей (в пересчете на лист формата А1); Тi – нормированная трудоемкость разработки одного приведенного чертежа по i-му виду работ, чел.-ч/лист; γ – средняя стоимость человеко-часа проектноконструкторских работ на базовом предприятии.
1) Деталировочные чертежи
Лi = 10;
Ti = 5 чел.-ч; γ = 96 руб.;
3оклад = Лi · Ti · γ = 4800 руб.; Здоп = 0,15 · Зо = 720 руб.; Зсоц = (Зо + Здоп)·0,3 = 1656 руб.
2) Узловые чертежи
Лi = 3;
Тi = 11 чел.-ч; γ = 96 руб.;
3оклад = Лi · Ti · γ = 3168 руб.; Здоп = 0,15 · Зo = 475,2 руб.;
Зсоц = (Зо + Здоп)·0,3 = 1093,0 руб.
3) Общие виды
Лi = 1;
Ti = 16 чел.-ч; γ = 96 руб.;
106

3oклад = Лi · Ti · γ = 1536 руб.; Здоп = 0,15 · 3оклад = 230,4 руб.; Зсоц = (Зо + Здоп)·0,3 = 530 руб.;
Зпр = 4800 + 720 + 1556 + 3168 + 475,2 + 1093 + 1536 +230,4 + + 530 = 14 108 ,6 руб.;
Зосв = 14 108 ,6 +14 108 ,6 · 0,75 + 14 108 ,6 · 0,5 = 31 744,35 руб.
Постоянные затраты на производство станка рассчитываются от основной заработной платы основных производственных рабочих по соответствующим процентам предприятия-аналога:
а) затраты по статье РСЭО:
ЗРСЭО KРСЭО Зо 2239,25 руб., 100
KРСЭО = 25,9 %;
б) общецеховые расходы:
Зцех Kцех Зо 20749,82 руб., 100
Kцех 240 %;
в) общехозяйственные расходы:
Зхоз Kхоз Зо 21614, 4 руб., 100
Kхоз 250 %;
г) внепроизводственные расходы:
Звн Kвн Зо 172,9152 руб., 100
Kвн 2 %.
Уровень рентабельности изделия в себестоимости за вычетом прямых затрат примем равным 47 %.
Прибыль, включаемая в оптовую цену проектируемой конструкции, вычисляется по формуле
107
П P Cизг ,
100
П 47 150931,98 70938,03 руб. 100
Структура себестоимости и формирования цены на станок представлена в табл. 19.
Таблица 1 9 Расчет стоимости и цены проектируемой конструкции
№ |
Статьи расходов |
Условное |
Сумма, |
|
п/п |
обозначение |
руб. |
||
|
||||
1 |
Основные материалы (за вычетом |
Зосн.мат |
4487,83 |
|
|
возвратных отходов) |
|||
|
|
|
||
2 |
Покупные полуфабрикаты |
Зк.осн.мат |
35187,39 |
|
Итого |
материальных затрат |
|
39675,22 |
|
3 |
Основная зарплата основных |
Зо |
|
|
|
производственных рабочих |
8645,76 |
||
|
|
|||
4 |
Дополнительная зарплата основных произ- |
Здоп |
|
|
|
водственных рабочих |
1296,86 |
||
|
|
|||
5 |
Начисления в социальные фонды (страховые |
Зсоц |
|
|
|
взносы) |
3179,0 |
||
|
|
|||
6 |
Расходы на подготовку и освоение |
|
|
|
|
производства, включая затраты |
Зосв |
|
|
|
на проектирование |
|
31744,35 |
|
7 |
Расходы на содержание и эксплуатацию обо- |
ЗРСЭО |
|
|
|
рудования |
2239,25 |
||
|
|
|||
8 |
Цеховые расходы |
Зцех |
20749,82 |
|
9 |
Общехозяйственные расходы |
Зхоз |
21614,4 |
|
10 |
Общепроизводственные расходы |
Зпроизв |
21614,4 |
|
Итого |
производственная себестоимость |
|
150759,06 |
|
11 |
Внепроизводственные расходы |
Звн |
172,92 |
|
12 |
Полная себестоимость |
Сизг |
150931,98 |
|
13 |
Прибыль |
П |
70938,03 |
|
14 |
Цена без НДС |
|
221870,0 |
|
15 |
НДС |
18 % |
39936,6 |
|
16 |
Оптово-отпускная цена конструкции |
Цо |
261806,6 |
108
Расчет технологической себестоимости детали при эксплуатации спроектированного оборудования
В настоящее время для тонкой доводки ответственных деталей иногда используется ручной труд высококвалифицированных и довольно редких специалистов-доводчиков. Этот метод не только морально устарел, но и отличается низкой производительностью. Кроме того, выполнять данный вид работ способны лишь опытные рабочие шестого разряда, и оплата таких рабочих соответственная. С внедрением проектируемого плоскодоводочного станка значительно повышается производительность, необходимость в специалистах высоких разрядов отпадает.
Для определения экономического эффекта от внедрения спроектированного оборудования необходимо знать себестоимость продукции (работ), производимой с его применением. Рассмотрим сначала вариант применения проектируемого плоскодоводочного станка.
1. Расчеткапитальных вложений втехнологическоеоборудование
Годовая программавыпуска детали «пята» составляет 14 000 штук. Рассчитаем потребное количество станков по формуле
n |
|
Vпродtшт |
, |
расч |
|
ФэKв.н 60 |
|
где Vпрод – годовой выпуск продукции; tшт – норма штучного времени обработки детали, tшт = 8 мин; Фэ – эффективный годовой фонд времени работы одного станка, Фэ = 1940 ч, так как предприятие работает в одну смену; Kв.н – коэффициент выполнения норм, Kв.н = 1.
nрасч |
14000 8 |
0,96. |
|
1940 1 60 |
|||
|
|
Примем количество станков, потребных для обработки данной детали (пята), равным 1.
Рассчитаем коэффициент загрузки оборудования по формуле
Kз 0,961 0,96.
109
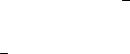
Капитальные вложения в технологическое оборудование рассчитываются по формуле
К1 = Б · nпр,
Б = Ц · Kтз · Kф · Kм,
где Б – первоначальная балансовая стоимость станка; Ц – оптовая цена станка по прейскуранту, Ц = 261806,6 руб.; Kтз – коэффициент, учитывающий транспортные расходы, Kтз = 1,04; Kф – коэффициент, учитывающий затраты на фундамент; Kм – коэффициент, учитывающий затраты на монтаж и освоение станка, Kм = 1,05.
Поскольку речь идет о станке настольного исполнения, то Kф не учитывается.
Б= 261806,6 · 1,04 · 1,05 = 285892,8 руб. К1 = 285892,8 · 1 = 285892,8 руб.
2.Расчет капитальных вложений в приспособление
Данный расчет осуществляется на основании принятого количества станков, по формуле
К2 = Спр · nпр,
где Спр – первоначальная стоимость приспособления, Спр = 1500× ×1,04 = 1560 руб.
К2 = Зпр · nпр = 1560 · 1 = 1560 руб.
Общая величина капиталовложений (К) определяется суммированием стоимости оборудования и приспособлений:
К = К1 + К2 = 285892 ,8 + 1560 = 287452,8 руб.
Расчет технологической себестоимости обработки детали
Технологическая себестоимость доводочной операции может быть представлена в следующем виде:
С Зуд.пер Vпрод Зпост; C Зпер Зпост,
где С – себестоимость годового объема обработки деталей, руб/год; Зуд.пер – переменные (пропорциональные) затраты, руб/шт.; Зпер –
110