
книги / Экономика отраслей машиностроения
..pdfЦехом называется основное производственное подразделение предприятия, выполняющее возложенную на него определенную часть производственного процесса (основного или вспомогательного). Цехи являются самостоятельными подразделениями и осуществляют свою деятельность на началах внутрипроизводственного хозяйственного расчета. Цехи обычно состоят из участков, количество которых зависит от объемов выпуска продукции, сложности выполняемой работы, состава оборудования, численностирабочих (идругих факторов).
Состав цехов завода, порядок и формы их кооперирования по выполнению производственного процесса называют производ-
ственной структурой предприятия. Соответственно, состав участ-
ков цеха, порядок и формы их кооперирования называют произ-
водственной структурой цеха.
Производственная структура предприятия определяется следующими важнейшими факторами: особенностями конструкции выпускаемых изделий; объемом выпуска продукции и трудоемкостью ее изготовления; уровнем специализации и производственным профилем предприятия; способами изготовления продукции, т.е. составом и сложностью применяемых технологических процессов. Схема взаимосвязей и взаимовлияния факторов, определяющих производственную структуру предприятия, приведена на рис. 2.
Производственный профиль предприятия непосредственно влияет на специализацию цехов: чем однороднее продукция, изготавливаемая предприятием, тем шире возможности более узкой специализации цехов и, следовательно, применения кооперирования не только внутри предприятия, но и вне его.
Объем выпуска продукции и трудоемкость ее изготовления влияют на размеры цехов, их количество и специализацию. Чем больше объем выпуска продукции, тем крупнее могут быть цехи предприятия, тем отчетливее они специализированы. На крупных машиностроительных заводах нередко можно встретить несколько литейных, механических, механосборочных и других цехов, автономное существование которых экономически оправдывается большими объемами выпуска продукции. Напротив, малый объем выпуска изделий позволяет за счет кооперирования с другими предприятиями обходиться без некоторых цехов.
11
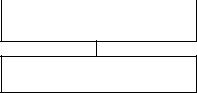
Например, при малом потреблении отливок нет необходимости в организации самостоятельного литейного цеха, продукция которого будет более дорогой, чем на специализированном предприятии. Небольшие размеры производства (наряду с некоторыми другими особенностями) позволяют в ряде случаев полностью отказаться от выделения самостоятельных цехов и перейти на бесцеховую производственную структуру, когда предприятие делится непосредственно на мастерские или производственныеучастки.
|
|
Особенности |
|
|
|
Объем выпуска |
|
Уровень и форма |
|
|||||||||||
|
|
конструкции |
|
|
|
|
изделий |
|
специализации |
|
||||||||||
|
|
|
|
|
|
|
|
|
|
|
|
|
|
|
|
|
|
|
|
|
|
|
|
|
|
|
|
|
|
|
|
|
|
|
|
|
|
|
|||
|
|
|
|
|
|
|
|
|
|
|
|
|
|
|
|
|
|
|
||
|
|
количество |
|
устойчивость |
|
|
объем |
|
структура |
|||||||||||
|
|
номенклатурных |
|
|
|
основных |
|
основных |
||||||||||||
|
|
|
номенклатуры |
|
|
|
||||||||||||||
|
|
позиций |
|
|
|
фондов |
|
фондов |
||||||||||||
|
|
|
|
|
|
|
|
|
|
|
|
|||||||||
|
|
|
|
|
|
|
|
|
|
|
|
|
|
|
|
|
|
|
|
|
|
|
|
|
|
|
|
|
|
|
|
|
|
|
|
|
|
|
|
|
|
|
|
|
|
|
|
|
|
|
|
|
|
|
|
|
|
|
|
|
|
|
технологический процесс изготовления продукции
производственная структура предприятия
Рис. 2. Схема взаимосвязи факторов, определяющих производственную структуру
Применяемая технология является одним из важнейших факторов, определяющих производственную структуру предприятия. Так, наличие большого числа деталей, изготавливаемых из поковок, требует организации самостоятельного кузнечного цеха; большая потребность в оригинальных крепежных деталях специальной конструкции предопределяетнеобходимостьвыделения автоматного цеха ит.д.
Таким образом, при выборе и проектировании производственной структуры машиностроительного предприятия должно быть установлено деление предприятия на соответствующие структурные подразделения, определены формы их специализации и кооперирования.
12
Вполне понятно, что производственная структура предприятия не может быть неизменной. Технический прогресс, развитие специализации и кооперирования предприятий могут потребовать пересмотра производственной структуры, создания новых цехов, перепланировки площадей, изменения производственной мощности и др. Структура предприятия должна обеспечивать наиболее правильное сочетание во времени и пространстве всех звеньев производственного процесса.
На основании вышеизложенного далее рассматривается сущность основополагающих технологий, используемых в основных цехах машиностроительных предприятий.
2. ТЕХНОЛОГИИ МАШИНОСТРОИТЕЛЬНОГО ПРОИЗВОДСТВА
2.1. Литейное производство
Литейным производством называют процесс получения литых заготовок, называемых отливками, путем заливки расплавленного металла в рабочую полость литейной формы. При охлаждении залитый металл затвердевает и сохраняет конфигурацию той полости, в которую он был залит. Конечную продукцию называют отливкой.
Литье является наиболее простым и дешевым промышленным способом получения заготовок, в том числе имеющих сложную геометрическую форму. Литьем получают разнообразные конструкции, отлитые массой от нескольких граммов до ~ 300 тонн, длиной от нескольких сантиметров до 20 метров. Продукция литейного производства распределяется между основными отраслями укрупненно следующим образом: машиностроение – 60 %, строительство – 20 %, металлургии 15 %, остальное – 5 %.
Технология получения отливок складывается из следующих основных операций:
изготовление литейной формы;
расплавление металла и заливка его в рабочую полость литейной формы;
кристаллизация металла в литейной форме и охлаждение от-
ливки;
13
выбивка отливки из формы; если форма разовая, то ее разрушают, если металлическая – ее раскрывают;
обрубка прибылей и литниковой системы и при необходимости очистка поверхностей отливки;
термическая обработка и, как правило, направление на механическую обработку для снятия припуска и получения точных размеров и необходимой шероховатости поверхности.
Металлы и сплавы, используемые для производства отливок, должны иметь хорошие литейные свойства: обладать жидкотекучестью, небольшой литейной усадкой и невысокой температурой плавления. Наибольшее распространение среди литейных сплавов получили серый и ковкий чугуны, углеродистая и легированная стали, силумин (сплав алюминия), бронзы и латуни (сплавы меди).
Литейные формы. Литейные формы предназначены для заливки в них металла и образования отливки. Устройство литейной формы схематически представлено на рис. 3, в качестве примера взята песчано-глинистая форма.
Основными элементами литейной формы являются рабочая полость и литниковая система. В рабочей полости 7 формируется тело отливки. Конфигурация рабочей полости соответствует конфигурации изготавливаемой детали, а ее размеры соответствуют размерам детали плюс припуски на литейную усадку и последующую механическую обработку. Внутри отливки и на ее поверхности в соответствии с чертежом детали могут быть различные отверстия и полости, для образования которых в литейную форму при ее сборке устанавливают соответствующие элементы, называемые стержнями 9. Стержни бывают металлические или керамические, и их удаляют при выбивке отливки из формы.
Литниковая система служит для подвода расплавленного металла в рабочую полость и питания отливки в процессе кристаллизации металла. Она состоит (см. рис. 3) из литниковой чаши (воронки) 2, стояка 3, дросселя 4, регулирующего скорость заливки и предотвращающего подсос воздуха в стояк, шлакоуловителя 5, служащего для задержки неметаллических включений, питателя 6, подающего расплавленный металл в рабочую полость непосредственно либо, как
14
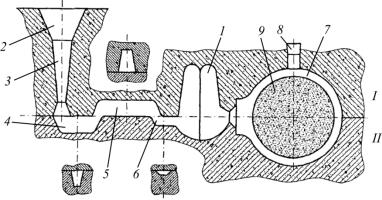
показано на рисунке, через боковую прибыль 1 и выпор 8. Прибыль– это массивный прилив, затвердевающий в последнюю очередь. Он питает отливку при охлаждении и кристаллизации металла и предотвращает образование в ней усадочных раковин. Прибыли могут быть бокового или верхнего расположения. Выпоры – это вертикальные каналы, устанавливаемые на самых высоких местах отливки и служащие для выхода газов, образующихся при заливке в форму жидкого металла.
Рис. 3. Принципиальная схема литейной формы: 1 – прибыль; 2 – литниковая чаша; 3 – стояк; 4 – дроссель; 5 – шлакоуловитель; 6 – питатель; 7 – рабочая полость; 8 – выпор; 9 – стержень;
I – верхняя опока; II – нижняя опока
Материалы литейных форм: песчано-глинистые смеси, песчаносмоляные смеси, металлы – чугуны, стали, алюминиевые и медные сплавы, керамика, графит и др.
Существуют и используются следующие способы заполнения литейных форм расплавом: под действием гравитационных сил, под действием высокого (до 700 МПа) избыточного давления, под действием низкого (0,1 МПа) избыточного давления, под действием центробежных сил и др.
Многообразие литейных форм и способов их заполнения расплавом предопределяет множество способов литья, среди которых
15
наиболее распространены следующие способы: в песчано-глинистые формы, в оболочковые формы, в кокиль, по выплавляемым моделям, центробежное литье, непрерывное литье и др.
Литье в разовые песчаные формы
В песчаных формах производят ~ 80 % всего объема выпуска отливок. Способ позволяет получать отливки самой разнообразной конфигурации и размеров, из различных литейных сплавов, в условиях как единичного, так и массового производства. Способ является универсальным.
Отливка получается в результате заполнения расплавленным металлом полости литейной формы (см. рис. 3), изготовленной из кварцевого песка, глины и специальных добавок. Глина является связующим и при оптимальном содержании воды (4–5 %) придает формовочной смеси необходимую прочность и пластичность. Песок увеличивает пористость и, следовательно, газопроницаемость формовочной смеси. Кроме того, в формовочную смесь вводят противопригарные добавки (каменноугольную пыль, графит), защитные присадочные материалы (борную кислоту, серный цвет) и другие ингредиенты. Для изготовления стержней используют стержневые смеси, состоящие из кварцевого песка и самотвердеющих неорганических (жидкое стекло с добавкой 10 % раствора NaOH) или органических (фенолформальдегидная или карбамидофурановая смолы) связующих.
После затвердевания и охлаждения металла форма разрушается для извлечения отливки. Способ позволяет получать отливки плотной структуры без газовой пористости и раковин, без трещин и остаточных напряжений. Однако отливки имеют невысокую точность 14–17 квалитет и шероховатость поверхности отливок Rz = 320…80 и, следовательно, большие припуски на механическую обработку. К недостаткам этого способа следует отнести не всегда удовлетворительные условия труда. Обрабатываемые материалы: чугуны, углеродистые и легированные стали, алюминиевые и медные сплавы. Структурная схема этого метода литья представлена на рис. 4.
На этой схеме среди прочих операций показана операция выбивки.
16
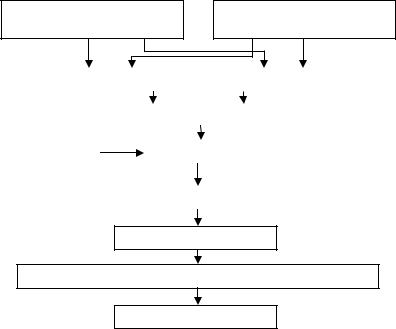
Выбивка – процесс удаления затвердевшей и охлажденной до нужной температуры отливки из литейной формы. Форма при этом разрушается.
Приготовление формовой и стержневой смеси
Изготовление моделей, стержневых ящиков
|
|
Изготовление полуформ |
|
|
Изготовление стержней |
|||
|
|
|
|
|
|
|
|
|
|
|
|
|
|
|
|
||
|
|
|
|
Сборка формы |
|
|
||
|
|
|
|
|
|
|
|
|
|
|
|
|
|
|
|
|
|
|
Приготовление |
|
|
|
|
|
|
|
|
|
Заливка расплава |
|
|
||||
|
|
расплава |
|
|
||||
|
|
|
|
|
|
|
|
|
|
|
|
|
|
|
|
|
|
|
|
|
|
|
||||
|
|
|
|
|||||
|
|
Затвердение сплава, охлаждение отливок в форме |
|
|||||
|
|
|
|
|
|
|
|
|
Выбивка отливок из формы
Отделение литников, прибылей, очистка поверхности
Контроль качества отливок
Рис. 4. Схема технологического процесса литья в разовые формы
Литье в кокиль
Кокиль (от французского coquille) – металлическая форма из чугуна, стали или алюминиевых сплавов. Кокиль используют многократно (несколько тысяч раз). В качестве примера на рис. 5 показана схема кокиля с несколькими разъемами по горизонтали и вертикали для получениясложнойпространственнойотливки изалюминиевого сплава.
В кокилях получают точные отливки (12–14 квалитет) с чистой поверхностью (Rz = 40…10 мкм) массой до 200 кг. Повышенная скорость охлаждения способствует получению плотных отливок с мелкозернистой структурой, что повышает прочность и пластичность материала отливок.
17
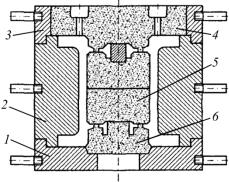
Рис. 5. Схема кокиля с несколькими разъемами по горизонтали и вертикали: 1 – нижняя часть формы; 2 – разъемные половины формы; 3 – верхняя часть
формы; 4, 5, 6 – стержни
Сущность процесса состоит в том, что расплав заливают в многократно используемую форму, металлические части которой составляют ее основу и формируют конфигурацию и свойства отливки. Отдельные элементы кокиля, главным образом стержни, формирующие сложные внутренние полости отливки, могут быть изготовлены из песка на том или ином связующем и предназначаться только для разового использования.
К особенностям технологического процесса следует отнести нанесение на рабочую поверхность кокиля огнеупорного покрытия толщиной 0,3–0,8 мм, уменьшающего скорость нагрева кокиля. Покрытие снижает разность температур по толщине кокиля, уменьшает температурные напряжения в нем и повышает его стойкость. В качестве огнеупорных материалов применяют пылевидный кварц, окислы и карбиды металлов, графит, асбест.
После нанесения покрытия кокиль нагревают до рабочей температуры 150–350 °С. Затем в кокиль устанавливают песчаные, керамические или металлические стержни. Половины кокиля соединяют и скрепляют, после чего заливают расплав в кокиль. После охлаждения отливки до заданной температуры кокиль раскрывают и удаляют отливку. Из отливки выбивают песчаный стержень, обрезают литники, прибыли. Затем цикл повторяется.
18
Скорость отвода теплоты от расплава и отливки можно регулировать, изменяя температуру нагрева кокиля перед заливкой.
Этот способ в сравнении с литьем в песчаные формы имеет ряд преимуществ:
–повышение производительности труда в результате исключения трудоемких операций смесеприготовления, формовки, очистки;
–более высокую точность размеров и малую шероховатость поверхности отливок;
–повышение механических свойств, плотности, образование мелкозернистой структуры;
–улучшение условий труда.
Недостатки способа:
–высокая стоимость кокиля, сложность и трудоемкость его изготовления;
–высокая интенсивность охлаждения расплава ограничивает возможность получения тонкостенных протяженных отливок;
–отсутствие у стенок кокилей газопроницаемости;
–неподатливый кокиль приводит к появлению в отливках напряжений, а иногда и трещин при изготовлении отливок со сложными очертаниями и переходами.
Литье в оболочковые формы
Сущность процесса сводится к тому, что расплав заливают в тонкостенную толщиной 6–10 мм форму, изготовленную из песча- но-смоляной формовочной смеси с термопластичными и термореактивными связующими смолами. В сравнении с литьем в песчаноглинистые формы способ имеет повышенную точность литейной формы и позволяет в два раза снизить припуск на механическую обработку. Получаемые отливки имеют толщину стенки до 3–15 мм, а массу 0,25–8,16 кг. Этим способом обрабатываются: чугуны, углеродистые и легированные стали, алюминиевые, медные, магниевые, цинковые сплавы. Особенности способа обусловлены свойствами связующего, в качестве которого обычно используется смесь фенолформальдегидной смолы с 8 % уротропина. В исходном состоянии смола термопластична, а в присутствии уротропина она становится термореактивной, полимеризуется и затвердевает необратимо.
19
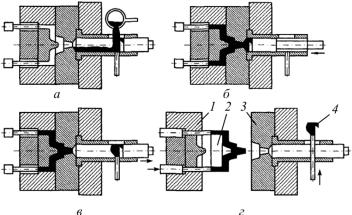
Литье под давлением
Суть процесса заключается в том, что литейная форма заполняется расплавом под действием внешних сил, значительно превосходящих силы гравитации (5–350 МПа), а затвердевание отливки протекает под избыточным давлением (рис. 6).
Рис. 6. Схема получения заготовок литьем под давлением:
а– заливка металла в камеру прессования; б – запрессовка металла;
в– открытие пресса-формы; г – удаление отливки; 1,3 – элементы пресса-формы; 2 – деталь; 4 – пресс-остаток
Обрабатываемые материалы – алюминиевые, цинковые, медные сплавы. Расплав заполняет пресс-форму за доли секунды (0,01–0,6 с) при скорости до 120 м/с. При этом он сильно фонтанирует, ударяется о стенки формы и в течение 0,003–0,004 с закупоривает вентиляционные каналы. В момент окончания заполнения полости формы расплав мгновенно останавливается. Вследствие гидравлического удара поверхностный слой ~0,2 мм отливок получается плотным, без газовой пористости, пузырьки газа остаются во внутренних сечениях отливки. Пресс-форма для этого способа является весьма сложным и точным инструментом. Формообразующие детали изготавливают из специальных сталей, легированных вольфрамом, хромом, никелем.
Изготавливают отливки массой от нескольких граммов до 50 кг, обычно тонкостенные (до 0,8 мм), сложной конфигурации. Отливки имеют высокую точность размеров (8–12 квалитет), малую шерохо-
20