
книги / Экономика отраслей машиностроения
..pdf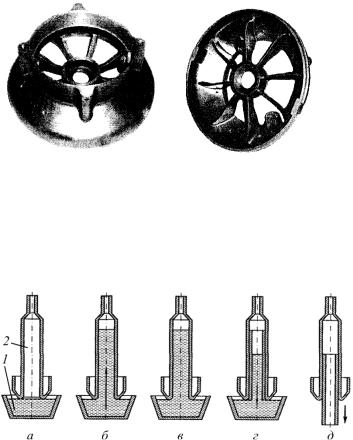
ватость поверхности Rz = 20…10 мкм и даже Ra = 1,25…0,63 мкм. На рис. 7 приведен пример корпусной тонкостенной детали из алюминиевого сплава, полученной с помощью данного метода.
Рис. 7. Внешний вид типичной детали, полученной литьем под давлением
Литье вакуумным всасыванием
Суть процесса: под действием разряжения, создаваемого в полости формы, расплав заполняет форму и затвердевает, образуя отливку (рис. 8).
Рис. 8. Принципиальная схема вакуумного всасывания: a – погружение формы в расплав; б – всасывание расплава в форму; в – выдержка металла в форме; г – слив незатвердевшего металла; д – удаление отливки из формы
Вакуумирование полости при заливке позволяет получать тонкостенные отливки с толщиной стенки 1–1,5 мм, повысить механические свойства отливки. Наиболее часто способ используют для
21
литья заготовок втулок, вкладышей подшипников скольжения из дефицитных и дорогостоящих сплавов.
Сущность технологического процесса вакуумным всасыванием заключается в следующем. Форма-кристаллизатор 2, охлаждаемая водой, погружается на невольную глубину в тигель 1 с жидким металлом. Всасывание происходит благодаря тому, что в кристаллизаторе вакуумом-насосом через вакуум-баллон (на рисунке они не показаны) создается разрежение. Наибольшая высота отливки, которую можно изготовить этим способом, зависит от плотности жидкого сплава и составляет около 1200–1400 мм для медных сплавов
иоколо 4000 мм для алюминиевых сплавов. Вакуумным всасыванием можно также изготавливать втулки или трубы. Для этого после определенного времени, необходимого для затвердевания на стенке кристаллизатора сплава до определенной толщины, снимают разряжение и выливают не успевший затвердеть сплав в тигель. Затем поднимают кристаллизатор с затвердевшей в виде втулки частью сплава. Качество внешней поверхности такой отливки хорошее, внутренняя же поверхность отливки имеет развитую волнистость,
иее удаление возможно только механической обработкой. Для получения сплошной заготовки требуется более продолжительная выдержка. Форма может заполняться расплавом с требуемой скоростью, плавно, без разбрызгивания, сплошным фронтом. Расплав, заполнивший форму, затвердевает в условиях вакуума; газы, содержащиеся в расплаве, могут из него выделяться, благодаря чему создаются условия для получения отливок без газовых раковин и пористости.
Под действием давления воздуха на зеркало расплава, последний постоянно питает усаживающуюся отливку, в результате чего отливка может быть получена плотной, без усадочных дефектов.
Центробежное литье
Расплавленный металл в процессе заполнения литейной формы и формирования отливки находится под действием центробежных сил, которые возникают в результате вращения формы (рис. 9).
22
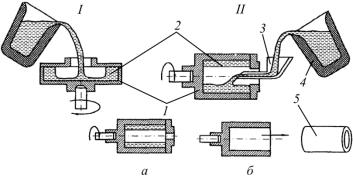
Рис. 9. Схемы центробежного литья на машинах с вертикальной (I) и горизонтальной (II) осью вращения: а – вращение формы
до затвердевания отливки; б – остановка формы и удаление отливки; 1 – форма; 2 – сплав; 3 – желоб; 4 – разливочные ковши; 5 – отливки
Обрабатываемые материалы – чугуны, медные сплавы, стали, титановые сплавы. Способ пригоден для получения пустотелых отливок; втулок, колец и т.д. Центробежное литье применяют для заливки роторов электродвигателей, двухслойных и многослойных изделий.
Особенности технологического процесса заключаются в том, что во вращающуюся форму через специальный желоб заливают металл. Под действием центробежной силы, во много раз превышающей силу тяжести, расплав заполняет полость литейной формы и затвердевает. После затвердевания и частичного остывания отливки вращение формы прекращают, горячую отливку извлекают и в дальнейшем ее охлаждают на воздухе или в охладительной камере.
Центробежные силы улучшают заполнение форм жидким металлом и ускоряют выделение и перемещение газовых пузырьков и неметаллических включений. Менее плотные, чем расплав, включения выносятся на внутреннюю поверхность отливки, а более плотные скапливаются у наружной поверхности. Повышенное давление способствует устранению в отливках пористости. По мере удаления от оси вращения центробежная сила возрастает, соответственно повышается плотность отливки. Из-за повышенного давления расплава тормозится усадка и уменьшается зазор между от-
23
ливкой и формой. Конвективное перемешивание металла в период кристаллизации и быстрое охлаждение способствуют измельчению структуры отливки.
Наиболее рационально использовать этот метод для получения труб, втулок, гильз, колец и т.п.
2.2. Технологии получения заготовок из порошковых, композиционных и других неметаллических материалов
Получение заготовок из порошковых материалов
Технология порошковой металлургии позволяет получать изделия из одного металла, например железа (такие изделия называют однокомпонентными), а также из смеси порошков металлов или металлов с неметаллами (многокомпонентные изделия), причем в самых различных сочетаниях. По этой технологии можно получить псевдосплавы из металлов, которые не образуют растворов, не смешиваются в жидком состоянии (железо–свинец, вольфрам–медь и др.), а также из металлов с неметаллами (медь–графит, алюминий– оксид алюминия, карбид вольфрама–кобальт), из некоторых оксидов металлов (Fe2О3 и МnО, Ре2О3 и NiO).
Схема получения заготовок из порошков включает следующие основные процессы: получение порошков, подготовка исходных компонентов (термообработка, нанесение покрытий, смешивание порошков для обеспечения оптимальной плотности засыпки), получение из порошка консолидированного тела – формование применением давления и получение плотных полуфабрикатов (спекание), отделка.
Применение различных значений удельной нагрузки при формовании определяет получение компактных прессовок различной плотности либо пористых деталей. Такая схема определяет практически безотходную технологию производства и возможность получения деталей с самыми разнообразными свойствами. Эти детали могут быть весьма мягкими и чрезвычайно твердыми, фрикционными и антифрикционными, магнитомягкими и магнитотвердыми, с высокой электрической проводимостью и высоким электрическим сопротивлением, жаростойкими и хладостойкими. Для многих деталей порошковая металлургия является единственным спо-
24
собом их получения. Например, порошковая металлургия незаменима при производстве компактных изделий из вольфрама, молибдена, ниобия, деталей для устройств вычислительной техники
ирадиоэлектроники (ферриты), для изготовления металлокерамических твердых сплавов, производстве металлических фильтров
имногого другого. (Порошковую металлургию называют также металлокерамикой, что объясняется схожестью одной из основных операций: спекания – в порошковой металлургии и обжига при производстве керамики.)
Внедрение порошковой металлургии дает большой экономический эффект. Отходы металла при традиционных способах обработки (на угар, в прибыли и литниковую систему, в обрезки, окалину, стружку) составляют в среднем более 50 %, а нередко достигают 80 %; при порошковой металлургии отходы практически отсутствуют.
2.3. Технологические процессы обработки заготовок пластическим деформированием
Уровень использования обработки давлением в технологических процессах машиностроения в любой стране в известной мере определяет уровень машиностроения в этой стране в целом.
Лишь в том случае, если 50 % проката проходят при обработке операции, связанные с пластическим деформированием, можно считать, что отходы металла при этом минимальны, а производительность достаточно высока.
Процессы обработки давлением характеризуются минимальным расходом металла, высокой производительностью. Большим преимуществом является также повышение качества металла при его пластическом деформировании, поскольку волокна металла не перерезаются, а только изгибаются, металл упрочняется, залечиваются его дефекты. Поэтому ответственные детали, такие как колеса и оси железнодорожных вагонов, детали турбин самолетов и т.д., обязательно подвергаются обработке пластическим деформированием.
Современная тенденция развития машиностроения в части применения новых материалов – пластмасс, металлопорошков, компо-
25
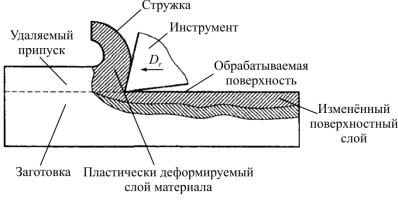
зитных материалов, керамики приводит к еще большему расширению сферы применения обработки давлением, ибо все эти материалы обрабатываются пластически.
Следует отметить еще одну тенденцию – совмещение разных методов. Одним из компонентов всякой комбинации технологических процессов часто являются операции пластической обработки.
2.4. Технология механической обработки резанием с использованием твердотельных инструментов
Механическая обработка или обработка деталей резанием –
это технологический процесс изготовления деталей заданной формы, размеров, точности и качества поверхностного слоя путем удаления припуска с заготовки в виде стружки.
Процессы резания среди других процессов размерной обработки являются наиболее эффективными по производительности, удельной энергоемкости и качеству обработки. Пока что ни один из известных процессов удаления материала не может конкурировать с резанием по этим параметрам. На долю резания приходится около 90 % общей трудоемкости размерной обработки.
В ближайшие десятилетия резание будет оставаться главным технологическим методом размерной обработки в машиностроении, хотя доля его будет сокращаться.
Рис. 10. Схема резания
26
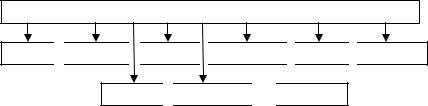
В данной главе рассматриваются только традиционные методы резания, для которых управляемое удаление слоя материала заготовки осуществляется твердым, имеющим неизменные формы и размеры физическим телом (инструментом). Удаление припуска с заготовки в процессе резания осуществляется путем внедрения с определенным усилием режущего инструмента в обрабатываемый материал и их относительного перемещения (рис. 10). Предполагается, что твердость инструмента существенно выше твердости заготовки.
Методы механической обработки заготовок
Основные методы механической обработки заготовок твердым телом представлены на рис. 11.
Методы обработки заготовок резанием
Точение Сверление
Строгание
Фрезерование
Пиление
Шлифование
Долбление Протягивание
Прошивание
Рис. 11. Методы механической обработки твердым телом
Формообразование поверхности заготовки можно представить в виде схемы обработки.
Схема обработки – условное изображение процесса резания
сизображением заготовки, ее установки и закрепления на станке
суказанием положения режущего инструмента относительно заготовки и движении резания.
Вкачестве примера на рис. 12 приведены токарная (а) и фрезерная (б) технологические схемы обработки.
Процессы резания условно можно разделить по виду применяемого инструмента на две группы:
–обработка резанием лезвийным инструментом:
–обработка абразивным инструментом.
К лезвийному инструменту относят: резцы, фрезы, сверла, зен-
керы, развертки, протяжки, пилы, долбяки, метчики и т.д. Из-
27
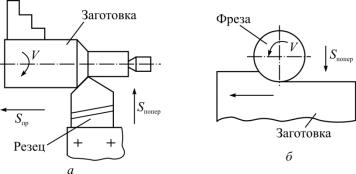
готавливают лезвийный инструмент из инструментальных и быстрорежущих сталей, металлокерамических и твердых сплавов, керамики, сверхтвердых материалов – алмаза, эльбора и др.
Рис. 12. Технологические схемы обработки точением (а) и фрезерованием (б)
К твердотельному абразивному инструменту относят: шлифовальные круги, бруски. В качестве «режущей» основы используются зерна карбида кремния зеленого и черного, электрокорунда, карбида бора, окиси хрома, алмазов, эльбора, гексанита и др. В качестве связующего используются органические вещества, например бакелитовые, керамика и металлы.
Схемы обработки заготовок на станках токарной группы
Технологический метод формообразования поверхностей точением характеризуется вращательным движением заготовки V и поступательным движением инструмента – резца Sпр (рис. 12, а). Движение подачи осуществляется параллельно оси вращения заготовки (продольное движение подачи – Sпр), перпендикулярно оси вращения заготовки (поперечное движение подачи – Sпопер), под углом к оси вращения заготовки (наклонное движение подачи).
На токарных станках обрабатывают, как правило, детали типа тел вращения, к которым относятся гладкие и ступенчатые валы, тонкостенные оболочки, втулки, детали со сложным наружным профилем, тарельчатые (дисковые) детали и др. (рис. 13).
28
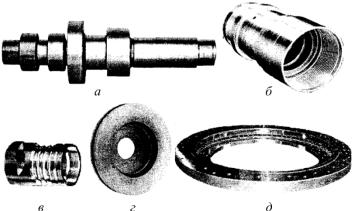
Рис. 13. Типовые детали цилиндрической формы:
а– ступенчатые валы; б – тонкостенные оболочки; в – втулка
снаружным фасонным профилем; г – тарельчатая деталь;
д– крупногабаритная кольцевая деталь
Токарная обработка имеет несколько разновидностей: точение, растачивание, подрезание, разрезание.
Точение – это обработка наружных поверхностей заготовок. Растачивание – обработка внутренних поверхностей. Подрезание – обработка плоских (торцевых) поверхностей. Разрезание – разделение заготовки на части.
Схемы основных видов обработки поверхностей, рассмотренных далее, считаются типовыми, так как их можно реализовать на универсальныхтокарныхстанках, полуавтоматах, автоматахистанкахсЧПУ.
2.5. Технологии сборочных работ
Для любых отраслей машиностроения, при всех мыслимых отличиях потребительских свойств изделий между собой и при определенных различиях в структуре их технологических процессов изготовления, общим всегда является необходимостьсборочных процессов.
Сборка является заключительным этапом в производстве машин и представляет собой большой комплекс слесарных, сборочных, поверочных и окрасочных работ.
29
Технологическим процессом сборки называют установку в требуемое положение и соединение готовых деталей, узлов, агрегатов в определенной последовательности, в результате чего получают готовое изделие, машину или механизм, полностью отвечающие заданным требованиям в соответствии с их служебным назначением.
Исходные предметы груда: элементы конструкции сборочной единицы (детали, узлы, агрегаты, болты, шайбы, гайки, винты, заклепки и т.п.).
Конечный предмет труда: сборочная единица, включающая все входящие элементы конструкций, соединенные в соответствии с чертежом.
Особенности технологического процесса сборки
Сборные изделия отличаются большим разнообразием служебного назначения, обеспечиваемого использованием различных физических эффектов и явлений – механических, гидравлических, аэродинамических, электромагнитных, электрических, оптических, электронных и т.п.
Это и определяет разнообразие конструктивно-технологических свойств сборочных единиц и входящих в них элементов конструкции, влияющих на содержание технологического процесса сборки.
Сложность структуры – состава и взаимосвязи элементов конструкций сборного изделия – определяет иерархический характер технологического процесса сборки, отображаемый в виде схемы сборки изделия.
Основными структурными компонентами технологического процесса сборки изделия являются этапы и сборочные операции.
Этап – есть законченная часть технологического процесса сборки изделия или его составной части, выделяемая в соответствии со схемой сборки.
Сборочная операция, как и в других технологических процессах машиностроительного производства, является основным структурным элементом технологического процесса, соответствующим определенному изменению свойств предмета труда с использованием конкретного физического, химического или иного эффекта и определенных средств технологического оснащения.
30