
книги / Экономика отраслей машиностроения
..pdf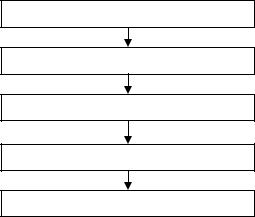
Применительно к отдельному входящему элементу конструкции сборочной единицы основные операции сборки разделяются на этапы установки и соединения.
Этап установки включает в себя перемещение элемента конструкции и базирование, обеспечивающее с заданной точностью требуемое положение устанавливаемого элемента относительно других элементов конструкции сборочной единицы.
Этап соединения включает операции, связанные с образованием контуров соединений, заданных в конструкторской документации.
В формализованном виде технологический процесс установки и соединения детали в сборочнойединице представлен на схемерис. 14.
Подготовка детали к сборке
Перемещение детали к месту установки
Базирование детали по месту установки
Выполнение соединений с другими деталями
Контроль качества сборки
Рис. 14. Схема технологического процесса установки и соединения детали в сборочной единице
Конкретное содержание операций соединения зависит от вида соединений, применяемых средств технологического оснащения, уровня механизации и автоматизации, организации производства и т.п.
Классификация видов соединений
Виды соединений классифицируются по целостности и подвижности составных частей, форме соединяемых поверхностей и методам образования соединений (рис. 15).
31
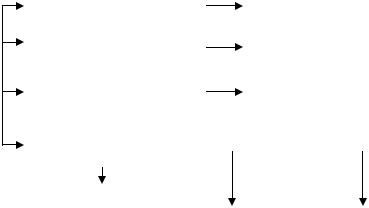
Целостность соединения |
|
|
|
Разъемные, неразъемные |
|
|||||
|
|
|
|
|
|
|
|
|
|
|
|
|
|
|
|
|
|
|
|
|
|
Подвижность составных частей |
|
|
|
|
|
|
|
|||
|
|
Подвижные, неподвижные |
|
|||||||
|
|
|
|
|
|
|
|
|
|
|
|
|
|
|
|
|
|
|
|
|
|
|
|
|
|
|
|
|
|
|
|
|
|
Форма поверхностей |
|
|
|
Плоские, цилиндрические, кони- |
|
||||
|
|
|
|
|
|
ческие, сферические, винтовые, |
|
|||
|
|
|
|
|
|
|||||
|
|
|
|
|
|
профильные, комбинированные |
|
|||
Методы образования |
|
|
|
|
||||||
|
|
|
|
|
|
|
|
|
||
|
соединений |
|
|
|
|
|
|
|
|
|
|
|
|
|
|
|
|
|
|
|
|
|
|
|
|
|
|
|
|
|
|
|
|
|
|
|
|
|
|
|
|
|
|
|
резьбовое |
|
|
|
|
|
|
|
|
|
|
|
|
|
|
|
|
|
|
|
|
|
клиновое |
|
|
|
шарнирное |
|
контактное |
|
||
|
|
|
|
|
|
|
|
|
|
|
|
шпоночное |
|
|
|
прессовое |
|
термоусаженное |
|
||
|
|
|
|
|
|
|
|
|
||
|
шлицевое |
|
|
фальцованное |
|
гвоздевое |
|
|||
|
|
|
|
|
|
|
|
|||
|
штифтовое |
|
развальцованное |
|
замковое |
|
||||
|
|
|
|
|
|
|
|
|
|
|
|
шплинтовое |
|
|
|
сварное |
|
пружинное |
|
||
|
|
|
|
|
|
|
|
|
|
|
|
фланцевое |
|
|
|
паяное |
|
сшивное |
|
||
|
|
|
|
|
|
|
|
|
|
|
|
клеевое |
|
|
|
клепанное |
|
комбинированное |
|
||
|
|
|
|
|
|
|
|
|
|
|
Рис. 15. Классификация соединений
Методы образования соединений отличаются наличием или отсутствием специальных соединительных элементов конструкции. При отсутствии таких элементов соединение осуществляется по сопрягаемым поверхностям. К таким соединениям относятся шлицевые, прессовые, термоусаженные и т.п.
В сварных, паяных и клеенных соединениях соединительным элементом является сварной, паяный или клеевой шов. Для выполнения таких соединений предварительно необходимы операции обработки кромок, механической и химической очистки соединяемых поверхностей в зоне соединительного шва.
32
Классификация видов сборки
Виды сборки классифицируются по объекту сборки, стадии и организации производства сборочных работ, последовательности сборки, точности сборки, механизации и автоматизации работ, подвижности объекта сборки в процессе выполнения сборочных работ.
Объектом сборки является сборочная единица – составная часть изделия или изделие в целом.
Общая сборка – сборка, объектом которой является изделие в целом. Она является заключительным этапом сборочного процесса, обеспечивающим заданное качество изделий. После окончательного (приемочного) контроля изделие обычно окрашивают. Изделие разбирают, если его размеры и масса не позволяют транспортировать его на место эксплуатации.
Сборочные единицы относятся к различным иерархическим уровням членения изделия – к агрегатам (секциям, отсекам) или узлам. Сборочная единица n-го порядка (уровня) собирается на п-м этапе процесса сборки.
Стадия сборки характеризует процесс сборки по степени его законченности.
Организация производства характеризуется сборкой изделий или его составных частей в различных условиях выполнения технологического процесса сборки.
Последовательность сборки характеризуется очередностью (порядком) выполнения этапов и операций сборки, а также возможностью их выполнения строго поочередно или одновременно (параллельно).
2.6. Технологические процессы сварки
Сварка – технологический процесс получения неразъемных соединений из металлов, сплавов и других однородных или разнородных материалов в результате образования атомно-молекулярных связей между частицами соединяемых заготовок.
Основной задачей сварки является получение прочного неразъемного соединения свариваемых заготовок с заданными физикомеханическими свойствами. Не все металлы и их сплавы и не в лю-
33
бых комбинациях могут надежно свариваться обычными методами сварки с применением традиционной технологии, т.е. не могут образовывать после сварки соединения с требуемыми механическими и физическими свойствами. Поэтому существует понятие – свариваемость металлов и их сплавов.
Свариваемостью металла называют совокупность его физических и технологических свойств, определяющих его способность обеспечить с помощью того или иного обычного методасварки ипринятого технологического процесса надежноевэксплуатации соединение.
Сварное соединение считают высокопрочным и равнопрочным, если его физико-механические свойства близки к таким свойствам основного (свариваемого) металла и в нем отсутствуют дефекты – трещины, поры, шлаковые включения, раковины и пр.
Процесс сварки является одним из наиболее совершенных, экономически выгодных, высокопроизводительных и в значительной степени механизированных технологических процессов. Поэтому сварку широко применяют практически во всех отраслях машиностроения. Сварка позволяет надежно соединять между собой детали, элементы узлов машин, заготовки практически любых толщин и конфигурации. Поэтому сварные изделия или отдельные их узлы могут иметь очень сложную форму в сочетании с незначительной массой при относительно простой и нетрудоемкой технологии изготовления.
Существует несколько десятков способов сварки и их разновидностей. Все они значительно отличаются один от другого по технике выполнения, однако по характеру протекания процессов формирования соединения и в зависимости от агрегатного состояния металла в месте во время сварки все существующие способы сварки принято объединять в две группы: сварка плавлением, сварка с примене-
нием давления.
На рис. 16 представлена классификация основных способов сварки и их разновидностей, имеющих в настоящее время промышленное значение.
При сварке плавлением происходит совместное расплавление кромок свариваемых заготовок, а в случае необходимости – также присадочного металла для дополнительного заполнения зазора между
34
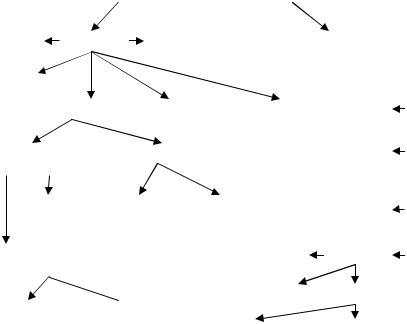
|
|
|
|
|
|
|
|
|
|
|
|
|
|
|
СВАРКА МЕТАЛЛОВ |
|
|
|
|
|
|
|
|
|
|||||||||||
|
|
|
|
|
|
|
|
|
|
|
|
|
|
|
|
|
|
|
|
|
|
|
|
|
|
|
|
|
|
|
|
|
|
|
|
|
|
|
|
|
|
|
|
|
|
|
|
|
|
|
|
|
|
|
|
|
|
|
|
|
|
|
|
|
|
|
|
|
|||
Плазменная |
|
|
Плавлением |
|
Газовая |
|
|
|
|
|
|
С применением давления |
|
|
|||||||||||||||||||||
|
|
|
|
|
|
|
|
|
|
|
|||||||||||||||||||||||||
|
|
|
|
|
|
|
|
|
|
|
|
|
|
|
|
|
|
|
|
|
|
|
|
|
|
|
|
|
|
|
|
|
|
|
|
|
|
|
|
|
|
|
|
|
|
|
|
|
|
|
|
|
|
|
|
|
|
|
|
|
|
|
|
|
|
|
|
|
|
||
Лазерная |
|
|
|
|
|
|
|
|
|
|
|
|
|
|
|
|
|
|
|
|
|
|
|
|
|
|
|
|
|
|
|||||
|
|
|
|
|
|
|
|
|
|
|
|
|
|
|
|
|
|
|
|
|
|
|
|
|
|
|
|||||||||
|
|
|
|
|
|
|
|
|
|
|
|
|
|
|
|
|
|
|
|
|
|
|
|
|
|
||||||||||
|
|
|
Электродуговая |
|
Электронно- |
|
|
|
|
|
Электрошлаковая |
|
|
Трением |
|
||||||||||||||||||||
|
|
|
|
|
|
|
|
|
|
|
|
|
|
|
лучевая |
|
|
|
|
|
|
|
|
|
|
|
|
|
|
|
|
|
|||
|
|
|
|
|
|
|
|
|
|
|
|
|
|
|
|
|
|
|
|
|
|
|
|
|
|
|
|
|
|
||||||
|
|
|
|
|
|
|
|
|
|
|
|
|
|
|
|
|
|
|
|
|
|||||||||||||||
|
Металлическим |
|
|
Угольным электродом |
|
|
|
|
|
|
|
Ультразвуковая |
|
||||||||||||||||||||||
|
электродом |
|
|
|
|
|
|
|
|
|
|
|
|
|
|
|
|
|
|
|
|
|
|
|
|
|
|
|
|||||||
|
|
|
|
|
|
|
|
|
|
|
|
|
|
|
|
|
|
|
|
|
|
|
|
|
|
|
|
||||||||
|
|
|
|
|
|
|
|
|
|
|
|
|
|
|
|
|
|||||||||||||||||||
|
|
|
Под слоем |
|
|
|
Прямого |
|
Косвенного |
|
|
|
Диффузионная |
|
|||||||||||||||||||||
|
|
|
флюса |
|
|
|
действия |
|
действия |
|
|
|
|
в вакууме |
|
||||||||||||||||||||
|
|
|
|
|
|
|
|
|
|
|
|
|
|
|
|
|
|
|
|
|
|
|
|
|
|
|
|
|
|
||||||
|
В среде защитных газов |
|
|
|
|
|
|
|
|
|
|
|
|
Шовная |
|
|
Контактная |
|
|||||||||||||||||
|
|
|
|
|
|
|
|
|
|
|
|
|
|
|
|
||||||||||||||||||||
|
|
|
|
|
|
|
|
|
|
|
|
|
|
|
|
|
|
|
|
|
|
|
|
||||||||||||
|
|
|
|
|
|
|
|
|
|
|
|
|
|
|
|
|
|
|
|
|
|
|
|
|
|
|
|
|
|
|
|
|
|
|
|
|
|
|
|
|
|
|
|
|
|
|
|
|
|
|
|
|
|
|
|
|
|
|
|
|
|
|
|
|
|||||||
|
|
|
|
|
|
|
|
|
|
|
|
|
|
|
|
|
|
|
|
|
|
|
|
|
|
Точечная |
|
Стыковая |
|
||||||
|
Плавящимся |
|
|
Неплавящимся |
|
|
|
|
|
|
|
|
|
|
|
|
|
|
|
|
|
|
|
|
|||||||||||
|
электродом |
|
|
|
|
электродом |
|
|
|
|
|
|
|
|
|
|
|
|
|
|
|
|
|
|
|
|
|||||||||
|
|
|
|
|
|
|
|
|
|
|
Без оплавления |
|
|
Оплавлением |
|||||||||||||||||||||
|
|
|
|
|
|
|
|
|
|
|
|
|
|
|
|
|
|
|
|
|
|
|
|
||||||||||||
|
|
|
|
|
|
|
|
|
|
|
|
|
|
|
|
|
|
|
|
|
|
|
|
|
|
|
|
|
|
|
|
|
|
|
|
Рис. 16. Классификация основных способов сварки
ними. В результате образуется сварочная ванна металла, после затвердевания которой формируется сварочный шов. При сварке с применением давления заготовки соединяются в результате совместного воздействия нагрева и давления. Выбор того или иного способа сварки и режима сварки зависит в первую очередь от свойств свариваемого материала, от толщины, геометрической формы и габаритов свариваемых заготовок, назначения изделия.
Сварка плавлением
Электрическая дуговая сварка. Сущность процесса электри-
ческой дуговой сварки состоит в том, что расплавление кромок заготовок происходит за счет тепла сварочной дуги, возбуждаемой между электродом и кромками заготовок. Максимальная температура дуги наблюдается в осевой ее части и составляет 4500–6000 °С.
35
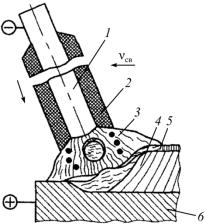
В качестве исходных заготовок при дуговой сварке используют продукцию стального и цветного проката, объемной и листовой штамповки, поковки, отливки и др.
Ручная дуговая сварка. Ручную дуговую сварку широко применяют во всех областях техники. Однако этот способ малопроизводителен, и качество сварки зависит от квалификации сварщика.
Заготовку или полуфабрикат располагают на металлическом столе или стальной плите, обеспечивая при этом с помощью механических прижимов надежный электрический контакт между ними и фиксирование заданного положения свариваемых кромок. Электрод 1 (рис. 17) закрепляют в специальном электродержателе.
Рис. 17. Принципиальная схема сварки
К заготовкам 6 и электроду 1 подводится переменный или постоянный ток напряжением не ниже 60 В, и затем сварщик возбуждает между ними сварочную дугу (при нормальном горении которой устанавливается рабочее напряжение 16–20 В). За счет тепла дуги кромки заготовок и металл торца электрода взаимно расплавляются, образуется сварочная ванночка 4. При этом также расплавляются на торце электрода и обмазка 2, образуя над ванной 4 некоторый объем нейтрального газа 3 и шлака 5, которые повышают стабильность горения дуги и защищают кипящий металл ванны от вредного воздействия атмосферного воздуха.
36
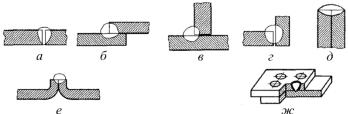
Сварщик вручную перемещает электрод вдоль шва, сообщая концу электрода с горящей дугой поперечные колебательные или вращательные движения для обеспечения равномерного расплавления обеих кромок заготовок и перемешивания металла сварочной ванны. По мере перемещения дуги металл сварочной ванны затвердевает, образуя сварной шов, соединяющий заготовки.
Вслучае сварки ответственных изделий с толщиной стенок более 4–6 мм часто накладывают швы один на другой путем повторного прохода, что обеспечивает более полный провар кромок на всю их толщину.
При сварке прерывистым швом или для прихватки заготовок
вотдельных точках сварщик перемещает электрод, периодически возбуждая дугу в необходимых точках.
Взависимости от вида сварных соединений, взаимного расположения свариваемых элементов существуют различные типы свар-
ных соединений (рис. 18): встык (а), внахлестку (б), тавровые (в), угловые (г), кромочные (д), с отбортовкой кромок (е), точечные
(ж). Наиболее прочными и экономичными являются стыковые соединения. Угловые и бортовые соединения выполняют главным образом связующую роль, так как практически не способны воспринимать заметные силовые нагрузки.
Рис. 18. Виды сварных соединений
Взависимости от положения продольной и поперечной оси шва
впространстве различают сварку в нижнем, вертикальном, горизонтальном и потолочном положениях.
Области применения ограничены горизонтальными швами. Автоматическую сварку под флюсом применяют в серийном и мас-
37
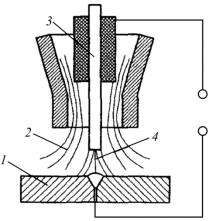
совом производствах для выполнения непрерывных прямолинейных и кольцевых швов большой протяженности на металле толщи-
ной 2–100 мм.
Дуговая сварка в защитных газах. Принципиальная схема процесса сварки показана на рис. 19.
Рис. 19. Сварка в защитном газе:
1 – свариваемые детали; 2 – защитный газ; 3 – электрод; 4 – дуга
В зону действия сварочной дуги 4 непрерывно подается с помощью специальной сварочной горелки защитный газ 2, надежно защищающий металл сварочной ванны и охлаждающий металл шва. Защитные газы, как правило, обладают хорошей ионизирующей способностью, поэтому обеспечивают стабильное горение дуги при любой величине тока. В качестве защитных газов наибольшее распространение получили инертные газы: аргон или гелий, а также активный газ – углекислый газ.
Более подробно остановимся на варианте аргонодуговой сварки. Этим способом можно сваривать неплавящимся вольфрамовым электродом без присадки и с присадкой и плавящимся электродом вручную (рис. 20, а), полуавтоматическим (рис. 20, б, в) и автоматическим методами.
38
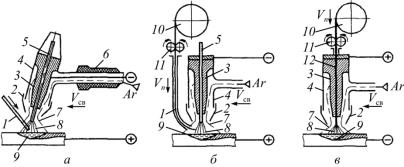
Рис. 20. Разновидности сварки в среде защитных газов: а – ручная; б – полуавтоматическая с неплавящимся электродом; в – полуавтоматическая с плавящимся электродом: 1 – присадочный пруток или проволока, 2 – сопло; 3 – токоподводящий мундштук; 4 – корпус горелки; 5 – неплавящийся вольфрамовый электрод; 6 – рукоять горелки; 7 – атмосфера защитного газа; 8 – сварочная дуга; 9 – ванна расплавленного металла; 10 – кассета с проволокой; 11 – механизм подачи; 12 – плавящийся
металлический электрод (сварочная проволока)
Процесс сварки в варианте ручной сварки (см. рис. 20, а) происходит следующим образом. Кромки заготовок плотно прижимаются к стальной или медной подкладке, при этом фиксируется расположение свариваемых кромок. К заготовкам и вольфрамовому электроду 5 подводится сварочный ток напряжением холостого хода не ниже 60 В. Затем сварщик включает автоматическую подачу аргона 7 в зону сварки и спустя 5–7 с возбуждает с помощью горелки 4 стабильную дугу 8 (которая затем действует устойчиво при напряжении 10–12 В) и одновременно обеспечивает, если требуется, подачу присадочной проволоки в зону дуги. Под действием дуги 8 кромки заготовок и присадочная проволока расплавляются, образуется сварочная ванна 9, которую защищает поступающий из сопла 2 горелки аргон 7. При этом сварщик вручную перемещает горелку вместе с действующей дугой и подачей присадочной проволоки и аргона вдоль свариваемых кромок. По мере перемещения дуги жидкий металл ванны затвердевает, образуя сварной шов. В случае выполнения прерывистого шва или прихватки заготовок в отдельных точках
39
сварщик перемещает горелку непрерывно, а дугу возбуждает и включает подачу аргона и присадочной или электродной проволоки периодически.
В качестве присадочного материала и плавящегося электрода применяют в большинстве случаев проволоку d = 0,5…3 мм, по химическому составу близкую к составу свариваемого материала. Аргонодуговая сварка неплавящимся электродом является одним из лучших способов сварки тонколистовых заготовок (от 0,1 до 2 мм) изделий из многих алюминиевых и магниевых сплавов, нержавеющих и жаропрочных сталей. Также успешно сваривают изделия из тугоплавких и химически активных металлов и сплавов – ниобия, тантала, молибдена, циркония и др.
40