
книги / Механическая усталость в статистическом аспекте
..pdf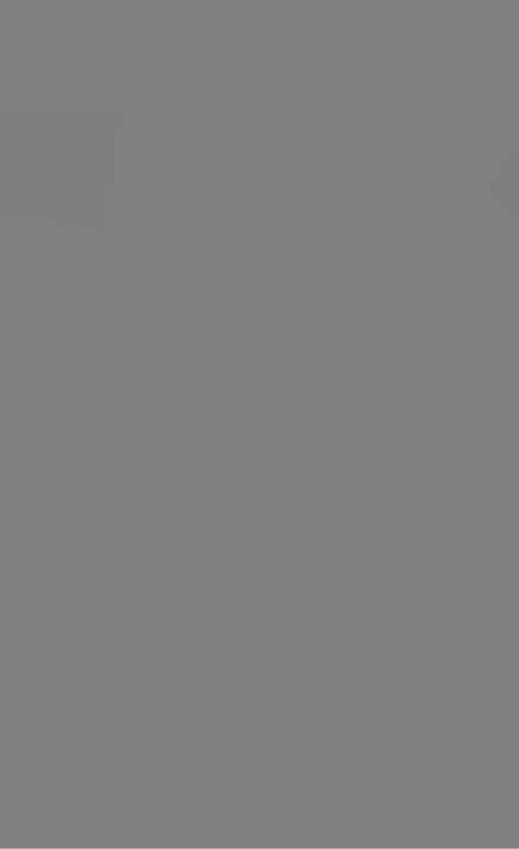
Ряс. 9. Семейство кривых равной вероятности усталостного повреждения для гладких образцов
а — по началу образования усталостной трещины; б — по окончательному разру шению: 1 — Р = 97,5%; 2—90%; з — 70%; 4 — 50%; 5—30%; 5—20%; 7—10%; 8—2,5%
а — по началу образования усталостной трещины; 6 — по окончательному разрушению
1 — Р = 96%; 2 — 90%; з —70%; 4—50%; 5—30%; 5—20%; 7— 10%; 8— 3,5%
размеры усталостного повреждения. Для пластин прямоугольного сече ния (ширина 24 мм, высота 94 мм и длина 700 мм) критической (или опас ной) площадью усталостной трещины, при которой после однократной перегрузки происходило хрупкое разрушение, оказалась площадь Ру, равная 13—18 мм2. Глубина таких трещин, замеренная после разрушения, как это видно на рис. 8, примерно равнялась радиусу полуокружности, по которой развивалась трещина, и составляла 2,0—3,3 мм. В работах [17—18] для установления критической (опасной) глубины трещины испы тывались образцы прямоугольного сечения с различными сварными со единениями (толщина 18—24—30 мм, ширина 160—200 мм и длина 810—
Рис. 11. Функции распределения пределов выносливости стали 45 для различных баз испытаний по началу образования трещины (пунктирные линии) и окончательному разрушению (сплошные линии)
а — для гладких образцов; б — для надрезанных образцов
1100 мм). После того как на образцах появлялись усталостные трещины различной величины, испытания при переменных напряжениях прекра щались. Образец замораживали до температуры — 40—60° С и затем растягивали в разрывной машине. При пониженной прочности хрупко разрушались те образцы, у которых глубина трещины усталости была 3—4 мм или более. Поэтому за критерий усталостного разрушения было предложено принимать момент достижения трещиной глубины 1—3 мм. В работах [2—41 за критерий усталостного разрушения цилиндрических образцов в условиях комнатной температуры была принята усталостная трещина глубиной 0,02—0,04 мм.
В настоящей работе при назначении критерия усталостного разрушения по развивающейся трещине руководствовались тем, что появление трещины должно рассматриваться как предельное состояние независимо от длитель ности ее развития до окончательного разрушения образца. За критерий
была принята видимая развивающаяся трещина длиной ОД мм (с откло нением до 0,5 мм), полагая, что чем меньше по длине зафиксированная усталостная макротрещина, тем полнее характеризуется начальная стадия процесса ее развития. При этом учитывалось, что в начальной стадии трещина развивается очень медленно, как это видно на рис. 2.
По полученным диаграммам распределения долговечности в коорди натах Р = N для гладких и надрезанных образцов (см. рис. 4,5) постро ены в координатах а*— N семейства кривых усталости (рис. 9 и 10), со ответствующие равной вероятности образования трещины длиной 0,1 — 0,5 мм или равной вероятности окончательного разрушения — 2; 10; 20; 30; 50; 70; 90 и 95%. По графикам (рис. 9 и 10) и опытным данным были построены в координатах Р — а* или (Ир + 5) — сг* полные вероятностные диаграммы усталости (или функции распределения пределов выносливо сти) для различных баз испытаний.
Сводные графики функций распределения пределов выносливости по началу образования трещины и окончательному разрушению в коорди натах Р = или (ир + 5) — от* при различных базах испытаний пред ставлены на нормальной вероятностной бумаге для гладких образцов (рис. 11, а) и для образцов с надрезами (рис. И, б).
На диаграммах в координатах Р — а* точки, обозначенные одинарным контуром, через которые проведены усредненные линии распределения пределов выносливости по началу образования трещины и окончатель ному разрушению, получены интерполяцией по семейству кривых уста лости (см. рис. 9 и 10), соответствующих различным вероятностям об разования трещины или разрушения, до пересечения вертикальных ли ний, проходящих через ось абсцисс в точках 104; 103, 106; 107и 108циклов. Точки, изображенные на этих графиках с обведенной окружностью, по лучены непосредственно по поврежденным трещиной и л и разрушенным образцам: их ординаты соответствуют отношению (в процентах) числа К разрушенных образцов или образцов, у которых появилась трещина усталости (0,1—-0,5 лш) до принятой базы испытания, к общему числу об разцов в одной партии п.
Проведенные по этим точкам усредненные линии представляют собой функции распределения пределов выносливости по началу образования трещины и по окончательному разрушению, соответствующие базам испытаний 104; 105; 10е; 107 и 108 циклов.
На рис. 11,6 видно, что в пределах рассматриваемой вероятности раз рушения от Р = 1,0% до Р = 99,0% как для появления макротрещины, так и для окончательного разрушения надрезанных образцов с прямо угольным сечением при увеличении базы испытаний с 104 до 108 циклов интервал рассеяния значений пределов вы носливости уменьшается, а угол наклона л и н и й функций распределения разрушающих напряжений
к |
оси |
абсцисс, характеризующий |
среднее квадратичное отклонение |
5 |
(сг*), |
увеличивается. Для гладких |
образцов такая закономерность |
менее выражена.
Интервалы рассеяния пределов выносливости на различных базах ис пытаний в указанных выше пределах вероятности появления трещины или окончательного разрушения приведены в табл. 2.
Среднее квадратичное отклонение разрушающих напряжений опре деляли графически по диаграммам функций распределения разрушаю щих напряжений (см. рис. И) как разность между напряжением _при
сдвинутых квантилях Цр + 5 = 6 и м р + |
5 = 5, а среднее значение 0| — |
|
в точке, соответствующей квантили ир + |
5 = 5 (Р = 50%). Коэффици |
|
ент вариации предела выносливости определялся выражением |
V (ст*) = |
|
= Я (а*) /а*. Полученные характеристики рассеяния пределов |
выносли |
вости по началу образования трещины и разрушающим напряжениям при различных базах испытаний приведены в табл. 3.
Интервалы рассеяния пределов выносливости образцов из стали 45, полученные по началу образования трещины п окончательному разрушению, в пределах вероятности от _Р=1,0% до Р = 99% при различных базах испытании
Геомэтричесине харак теристики образцов
Гладкие:
Ь = 20 мм
к = |
3 |
м м |
г = |
42,5 мм |
|
а |
II |
О |
|
о* (по началу образо |
Размах |
о1 (по разрушению), |
Размах |
||
|
вания трещины), п Г /м м - |
кГ / м м 2 |
раессянняо |
|||
База |
|
|
рассеяния о* |
|
|
в интерва |
|
|
в интервале |
|
|
ле вероят |
|
N |
при |
при |
вероятности |
при |
при |
ности от |
ЦИКЛОВ |
от Р = 1% |
Р = 1,0% |
||||
|
Р = 1.0% |
Р = 99% |
до Р = 99%, |
Р = 1.0% |
Р = 99% |
до 7^=99%, |
|
|
|
к Г /м м * |
|
|
п Г /м м * |
104 |
41,4 |
42,5 |
1,1 |
42,3 |
43,4 |
1,1 |
10й |
35,7 |
37,2 |
1,5 |
36,2 |
37,8 |
1,6 |
106 |
30,6 |
32,6 |
2 ,0 |
31,0 |
33,2 |
2 ,2 |
107 |
23,4 |
30,6 |
2 ,2 |
23,9 |
31,4 |
2,5 |
Надрзанные: |
104 |
27,9 |
35,5 |
7,6 |
35,4 |
42,7 |
7,3 |
||
Ъ = |
20 |
м м |
|||||||
к = |
3 |
м м |
105 |
17,1 |
24,1 |
7,0 |
25,7 |
33,0 |
7,3 |
г = |
0,3 м м |
106 |
11,6 |
16,9 |
5,3 |
15,6 |
22,8 |
7,2 |
|
1 = |
2 |
м м |
Ю7 |
10,6 |
15,1 |
4,5 |
10,9 |
16,6 |
5,7 |
а0 = |
2.52 |
108 |
10,0 |
14,2 |
4,2 |
10,1 |
14,7 |
4,6 |
|
|
|
|
|
|
|
Т а б л н ц а |
||
Средние значения |
среднеквадратичные отклонения 8 а^ коэффициенты |
вариации |
|||||||
V разрушающих напряжении |
при различных базах испытаний* для образцов из |
||||||||
|
|
|
стали 45 |
(или пределов выносливости) |
|
|
|||
База N |
|
|
|
База N |
|
|
1 |
||
».'Г/.н.нг |
5а{,пГ/мм* |
О^, кГ/мм* |
30^.ХГ/Л1Л12 |
||||||
циклы |
|
ЦИКЛОВ |
|||||||
|
|
Г л а д к и е о б р а з ц ы |
Н а д р е з а н н ы е о б р а з ц ы |
1 |
|||||
|
|
0,0536 |
|||||||
104 |
|
42,0** |
0,2 |
0,0048 |
Ю4 |
31,7 |
1,7 |
||
|
42,8 |
0,25 |
0,0058 |
39,0 ** |
1,6 |
0,0410 |
|||
105 |
|
36,5 |
0,3 |
0,0082 |
105 |
20,6 |
1,5 |
0,0728 |
|
|
37,0 |
0,3 |
0,0081 |
2973 |
1,55 |
0,0529 |
|||
10е |
|
31,6 |
0,4 |
0,0127 |
10е |
14,3 |
1,1 |
0,0769 |
|
|
32,1 |
0,5 |
0,0156 |
19,2 |
1,5 |
0,0781 |
|||
|
|
|
|||||||
10? |
|
29,5 |
0,45 |
0,0153 |
107 |
12,8 |
1,0 |
0,0781 |
|
|
30,1 |
0,55 |
0,0183 |
13,7 |
1,25 |
0,0912 |
|||
|
|
|
|||||||
|
|
|
|
|
108 |
12,10** |
0,9 |
0,0744 |
|
|
|
|
|
|
12,35 |
1,0 |
0,0810 |
||
|
|
|
|
|
|
||||
*В |
числителе — по |
началу образовании трещины, в знаменателе — по |
окончательному раз |
||||||
рушению. |
|
|
|
|
|
|
|
||
** Точки получены экстраполяцией. |
|
|
|
|
Данные о снижении пределов усталости по началу образования трещи ны в сравнении с пределами усталости, полученными по окончательному разрушению при различных базах испытаний, приведены в табл. 4. Как видно из табл. 4 для надрезанных образцов, испытанных на базе 104циклов (в сравнении с базами 105— 108),не наблюдается закономерного снижения сопротивления усталости при сопоставлении пределов выносливости, полученных по началу образования трещины и по разрушению. Это мож но объяснить тем, что при высоких уровнях нагружения максимальные напряжения в вершине надреза намного превышают предел текучести материала, и происходит значительная пластическая деформация, вызы вающая наклеп и остаточные напряжения.
Т а б л п ц а 4
Снижение пределов выносливости (в %) по началу образования трещппы в сравнении с пределами выносливости, полученными по окончательному разрушению при различных базах испытания
База N |
Р = 1,0°/ |
Р = 50% |
Р = 90% |
База ЛГ |
Р = 1,0% |
Р = 50»/ |
Р = 99% |
циклов |
циклов |
||||||
|
Г л а д к и е о б р а з ц ы |
|
Н а д р е з а н н ы е о б р а з ц ы |
||||
10* |
2,1 |
1,9 |
2,1 |
10* |
21,2 |
18,7 |
16,9 |
10й |
1,4 |
1,4 |
1,6 |
105 |
33,5 |
29,7 |
27,0 |
10е |
1,3 |
1,6 |
1,8 |
10° |
25,6 |
25,5 |
25,9 |
107 |
1,7 |
2,0 |
2,5 |
107 |
2,3 |
6,6 |
9,0 |
|
|
|
|
108 |
1,0 |
2,0 |
3,4 |
Выводы
1. Развитие трещины усталости у надрезанных образцов при номи нальных напряжениях, близких к пределу выносливости, происходит с остановками, длящимися по нескольку десятков миллионов циклов.
2.Скорость распространения трещины усталости уменьшается при снижении величины номинального напряжения и увеличивается по ме ре роста длины трещины.
3.Увеличение абсолютных размеров и изменения асимметрии цикла мало влияют на рассеяние средней относительной длительности разруше ния гладких образцов прямоугольного сечения.
4.Среднее квадратичное отклонение (ско) долговечности по циклам для надрезанных образцов из стали 45 по началу образования трещины (при одном и том же среднем значении логарифма числа циклов) несколько превышает ско по окончательному разрушению. У гладких образцов из этой стали превышение значения ско по началу образования трещины в сравнении с ско по окончательному разрушению незначительно.
5.Наибольшее различие по пределам выносливости (до 33,5%) при сопоставлении результатов испытаний надрезанных образцов из стали 45 по началу образования трещины и окончательному разрушению наб людали при базах испытаний 104, 105 и 10е циклов. По мере увеличения
базы испытаний это различие уменьшалось и при базах 107 и 108 циклов не превышало 9,0—3,4% соответственно. У гладких образцов аналогич ное снижение незначительно.
ЛИТЕРАТУРА
1.С. В. С е р е н с е п . Усталость конструкционных чугунов в связи с прочностью литых коленчатых валов.— Научные труды нпстнтута машиноведения и сельско хозяйственной механики, т. 111. Кпев, Изд-во АН УССР, 1951.
2.Р. Д. В а г а п о в . К определению долговечности крупногабаритных деталей по результатам испытаний модельных образцов.— Изв. АН СССР, ОТН, 1959, № 1.
3. Р. Д. В а г а п о в , О. И. Ш п ш о р и п а , Л. А. Х р и п н и а. Моделирование при испытаниях па усталость.— Сб. «Испытания деталей машин па прочность». Под ред. С. В. Серепсена. Машгиз, 1960.
4.Р. Д. В а г а п о в . Методика оценки усталостной прочности при разделении про цесса циклического нагружения па две стадии.— Заводская лаборатория, 1964,
№6.
5.С. В. С е р е п с е п, М. Э. Г а р ф, Л. А. К о з л о в . Машины для испытании на
усталость. Машгиз, 1957.
6. Э. Р. П а р к е р , Д. М. Ф о г р е д о . Зарождение и развитие трещин устало
сти.— Сб. «Усталость и выносливость металлов» под ред. Г. В. Ужика. ИЛ, 1963.
7.М. Я. Г а л ь п о р п н . О рассеяппп долговечности сталей до базы испытаний 108 циклов.— Заводская лаборатория, 1967, № 9.
8.Г. Н. В с е в о л о д о в . О развитии трещин усталости.— Сб. «Циклическая проч ность металлов». Изд-во АН СССР, 1962.
9.Г. Н. В с е в о л о д о в . О распространении усталостных трещин в образцах су достроительной стали.— Заводская лаборатория, 1959, № 6.
10.\У. ^ Н а г г 1 5. МеЪаШс РаИдие. Рег^ашоп Ргезз. N . У.— ОхГогй— Ьопйоп —
Рапз, 1961, р. 205—238.
11.В. П. К о г а е в. Методы статистической обработки результатов усталостных ис пытаний.— Заводская лаборатория, 1957, № 5.
12.А. X а л ь д. Математическая статистика с техническими приложениями. ИЛ, 1956.
13.М. Н. С т е п н о в . Об оценке вероятности разрушения при усталостных испыта ниях.— Сб. «Конструкционная прочность легких сплавов и сталей». Труды МАТИ.
14. |
Изд-во «Машиностроение», 1964, № 61. |
|
И. В. Д у н и н-Б а р к о в с к и й, Н. В. С м и р н о в . Теория вероятностей и |
||
15. |
математическая статистика в технике. |
Гостехтеоретпздат, 1955. |
Г. В. У ж и к . , М. Я. Г а л ь п е р и н . |
Об опасности мгновенного разрушения |
|
|
элементов конструкций при циклических |
перегрузках. Докл. АН СССР, 1960, |
|
131, № 5. |
|
16.М. Я. Г а л ь п е р и н . Определение склонности к хрупкому разрушению балок при изменении их размеров и наличии концентрации напряжений.— Заводская лаборатория, 1965, № 11.
17.В. И. Т р у ф я к о в . Вопросы методики испытаний сварных соединений на выно
сливость.— Автоматическая сварка, 1963, № 1 (118).
18. В. И. Т р у ф я к о в, |
10. А. С т е р е н б о г е н, П. П. М и х е е в, А. В. Б а- |
б а е в. Выносливость |
сварных соединении низколегированных сталей.— Авто |
матическая сварка, 1966, № 11 (164).
19.В. М. М а р к о ч е в, Б. А. Д р о з д о в с к и й. Методика и исследование кине тики разрушения листовых материалов при повторно-статическом нагруже нии.— Сб. «Прочность при малом числе циклов нагружения. Вопросы механиче ской усталости». Изд-во «Наука», 1969.
II.НАКОПЛЕНИЕ УСТАЛОСТНЫХ ПОВРЕЖДЕНИЙ ПРИ НЕСТАЦИОНАРНЫХ НАГРУЗКАХ
СОПРОТИВЛЕНИЕ УСТАЛОСТИ СПЛАВА ЭИ437Б ПРИ ПРОГРАММНОМ НАГРУЖЕНИИ И ПОВЫШЕННОЙ ТЕМПЕРАТУРЕ
В.П. КОГАЕВ, В. В. КИРИН
Сцелью исследования статистических закономерностей накопления усталостных повреждений при нестационарных нагрузках в условиях повышенных температур были проведены испытания образцов из сплава ЭИ437Б1 при стационарном и программном нагружении. Испытания про водили при изгибе в одной плоскости на электродинамической резонан сной установке с частотой 200 гц [1] (установка работает в автоколеба-
Рис. 1. Образец для пспытанпя на усталость
тельном режиме, регулирование и программирование амплитуды коле баний осуществляются электронной автоматической системой). Испытания прекращались в момент появления первой макроскопической трещи ны усталости, обнаруживаемой по снижению частоты собственных коле баний системы (длина трещины не более 1 мм).
Образцы нагревали в электрической печи сопротивления. Образец с захватами приведен на рис. 1. Условия испытания, материал образцов и установка были те же, что и в работе [1], где описаны результаты уста лостных испытаний образцов из сплава ЭИ437Б при температуре 800° С.
Ниже приводятся результаты испытаний этого сплава при температу
ре 700° С.
На рис. 2 представлены результаты испытаний для пяти уровней ста ционарных амплитуд напряжений, на каждом из которых испытывалось по 10 образцов (за исключением уровня а = 40,2 кГ/мм2, на котором бы ло испытано 3 образца). В табл. 1 приведены средние значения долговеч-
1 После закалки иа воздухе с 1080° и 16-часового старения при 700° сплав имел
предел прочности 89 кГ/лш2; при 700° и напряжении 40 кГ/мм2 время до разрушения было более 72 час.
ностей |
./V, N и стандартные отклонения |
и 8 ^ для каждого из уров |
||
ней амплитуд, |
подсчитанные по формулам |
|
|
|
8 * |
= ] / |
1 = ] / ^ |
2 (1ВЛГ*— 18ЛО*. |
(1) |
Как видно на рис. 2 и в табл. 1, при данных условиях испытания рас сеяние долговечности практически не зависит от уровня амплитуды нап ряжений, что наблюдалось также и в других исследованиях [1 , 2].
вУо
38 |
|
|
0 53,1 |
щ в |
I----- |
08,7 |
|
35 |
|
|
*{у |
|
|||
|
|
о |
|
—О----- |
|
||
50 |
|
|
|
|
|
|
|
|
|
о |
О |
о |
О |
оо,го * |
|
|
|
|
|||||
80 |
|
_010 |
с) |
||||
70 |
|
э |
|
о |
О |
|
|
00 |
|
СX |
о |
|
о |
о |
|
50 |
_с |
о |
|
0 |
с |
—с)— |
|
00 |
С |
о |
|
|
с1 |
||
а |
0 |
|
> |
э |
|
||
50 |
_а |
|
|
|
|||
20 |
Ф с |
|
о |
|
0 |
о |
|
|
о |
|
о |
6 |
о |
|
о |
70 |
о |
|
|
||||
|
|
|
|
|
|
||
о |
|
|
|
|
|
|
|
5 |
|
э |
У" |
|
|
|
|
о |
|
|
|
|
|||
2 |
|
|
|
|
|
|
|
7 |
|
|
703 |
|
|
|
|
70* |
|
|
|
70 3 |
707 |
/У |
|
Рис. |
2. Функции распределения долговечностей при стационарном режиме |
нагрузки |
(цифры у точек — а, кГ/лш2)
Для определения параметров полной вероятностной диаграммы уста лости при стационарных амплитудах напряжений результаты усталост ных испытаний были статистически обработаны методом линейного ре грессионного анализа с постоянной дисперсией [3, 4].
|
|
|
Т а б л и ц а 1 |
|
Средние значения а, ТУ, |
|
И 8 1ёХ |
|
|
кГ/мм* |
N |
|
8 N |
8 ^еN |
53,1 |
6,4-104 |
4,7427 |
3,36*10* |
0,2406 |
50,8 |
2, 5- 105 |
5,3557 |
1,18-Ю5 |
.0,2119 |
47,3 |
1,217.10° |
6,0474 |
5,17.10& |
0,1962 |
43,7 |
7,138.10° |
6,8182 |
2,83*10° |
0,1936 |
40,2 |
3,666-Ю7 |
7,5543 |
+ |
* |
|
|
|||
* Стандартные отклонения Зде |
и 8 ^ ^ |
не подсчиты |
|
|
с малым количеством образцов (3 шт.). |
|
|
Результаты обработки представлены в табл. 2 и в виде полной вероят ностной диаграммы усталости в координатах о — N (двойной логарифми ческий масштаб) на рис. 3, на котором приведены кривые усталости, со-