
книги / Монтаж шахтных стационарных установок
..pdfэтих деталей и узлов совпадали с осями вращения. Смещение центра тяжести с оси вращения создает неуравновешенность, которая сопровождается вибрацией.
Уменьшение неуравновешенности до допускаемого предела достигается статической и динамической балансировкой. Дина мическая балансировка вращающихся узлов в практике мон тажных работ на угольных шахтах применяется редко.
Статическая балансировка может быть произведена на стан ках с призмами (рис. 67).
Станок с призмами состоит из четырех стоек 1 с установоч ными 2 и подъемными 3 винтами, двух швеллеров 4, закреп ленных на стойках, и двух призм 5,
Рис. |
67. |
Станок для стратической балансировки деталей: |
|
/ — стойки, |
2 — установочные винты, 3 — подъемные винты, 4 — швел |
||
|
|
леры, |
5 — призмы |
Призмы |
изготовляются из |
стали с последующей закалкой |
и должны иметь длину не менее 1,5—2 длины окружности шей ки вала. Ширина а призмы в зависимости от веса балансируе мого узла принимается:
при весе узла до 1 т . |
-3—5 мм |
1 - 3 |
5 - 6 |
3 -5 |
6-8 |
6 — 8 |
50 |
Призмы устанавливаются по уровню с точностью до 0,02 мм на 1 м их длины.
Узел, подлежащий балансировке, например вал с шестерней, устанавливается так, чтобы ось вала была перпендикулярна призмам.
Различают балансировку предварительную и окончательную. При предварительной балансировке окружность детали (шестер ни) делится на шесть-восемь равных частей. Установив каждые два противоположных деления в горизонтальном положении добиваются неподвижного состояния детали на призмах за счет дополнительных грузов (замазка, воск, пластинки намагничен ной стали).
При окончательной балансировке к каждой из указанных
точек пересечения линии диаметра с внешней окружностью под вешиваются грузы до тех пор, пока деталь не выйдет из со стояния равновесия (покоя). Вес грузов записывается в таб лицу, по данным которой строится кривая. При тщательной балансировке кривая должна иметь вид синусоиды, у которой нижняя точка соответствует наиболее тяжелому месту детали. Для балансировки детали следует в диаметрально противопо ложном направлении наиболее тяжелого места добавить урав новешивающий груз.
Вес уравновешивающего груза определяется по формуле
|
Qy = |
A m tx — |
|
|
2 |
где |
и A mia— соответственно максимальный и минималь |
|
ный груз. |
|
Полученный уравновешивающий груз Qy не должен превы шать величины контрольного груза QK, определяемого по фор муле
где G — вес балансируемой детали;
п — номинальная скорость вращения детали; R — радиус балансируемой детали.
После балансировки грузы снимаются и по их весу подби раются металлические пластинки, которые прикрепляются в те места, откуда были сняты грузы. Уравновешивание также про изводится высверливанием отверстий в балансируемой детали в месте, противоположном месту подвешенного груза. Вес вы сверленного из детали металла должен быть равен весу урав новешивающего груза.
§ 19. Соединение конвейерных лент методом вулканизации
Наиболее надежное неразъемное соединение конвейерных лент достигается методом горячей вулканизации.
Соединение горячей вулканизацией промежуточных стыков конвейерных лент производится в свободном положении ленты, а последний замыкающий стык соединяется с натяжкой. Вулка низация промежуточных стыков ленты производится обычно на полу помещения возле приводной головки конвейера. Замыкаю щий стык вулканизируется на рабочей стороне роликоопор, то есть сверху конвейера. На период вулканизации под стык ленты, на ролики, укладывается стальной лист длиной 1,5—2,0 м.
Перед вулканизацией концы ленты должны быть соответст-
юз
вующим образом подготовлены (рис. 68, а ). Каждый конец лен ты размечается на ступени, составляющие с направлением дви жения ленты острый угол а. Этот угол называется у г л о м з а к р о я с т у п е н е й и зависит от отношения толщины ленты Ô
к диаметру приводного барабана D6. |
Ь |
1 |
Если отношение — > — , |
||
|
Лб |
80 |
Рис, 68. Соединения конвейерных лент способом вулкани зации:
|
о — схема разделки |
стыка, |
б — соединение |
стыков. |
/ — эа>киМные |
|
|
брусья, |
2 —- стяжной |
болт, 3 — стяжная гайка |
|||
то |
ступени размечаются |
под |
углом |
а = 30°, |
если отношение |
|
— < — — под углом а = 45 |
|
|
|
|||
£)б |
80 |
|
|
|
|
|
Ширина b каждой ступени и общее число ступеней опреде ляются расчетом.
После разметки стыка делается надрез резины до первой тканевой прокладки. При этом необходимо следить, чтобы был надрезан только слой резины, а не тканевая прокладка. Затем узкими полосками шириной по 30—40 мму с помощью клещей, снимается резиновая прокладка. Для дблегчения отслаивания узких полосок производится надрез прокладок вдоль ленты че^ рез каждые 30—50 мм. Поверхность каждой ступени тщательна обрабатывается металлической щеткой, наждачной бумагой к высококачественным (авиационным) бензином.
Ступенчатый стык второго конца конвейерной ленты разде лывается аналогично, но только с обратной (нижней) стороны
ленты.
На подготовленные к вулканизации поверхности каждой из ступеней наносятся щетинной щеткой 3—4 слоя резинового клея. После просушки резинового клея концы ленты зажимаются двумя брусьями / (рис. 68,6) и стягиваются болтами 2 при по мощи гайки 3; после этого ступени одного конца ленты накла дываются на соответствующие ступени другого конца ленты. Для лучшего соединения место склейки прокатывается валиком.
|
|
|
Т а б л и ц а 23 Г< |
Количество прокладок |
Продолжительность вулканизации, мин. |
||
|
|
||
конвейерной |
ленты |
лента без обкладок |
лента с обкладками |
|
|
||
3 |
|
12-15 |
15-18 |
4 |
|
20 |
21-23 |
5 |
|
25 |
30 |
6 |
|
30 |
35 |
8 |
|
35 |
40 |
10 |
|
40 |
45 |
12 |
|
45 |
48 |
затем стык ленты помещается в вулканизационный аппарат, со стоящий из двух обогреваемых плит, скрепленных прижимными балками. Стык ленты нагревается до температуры 140—145° Продолжительность вулканизации стыков приведена в табл. 23-
Г л а в а III
МОНТАЖ Ш АХТНОГО СТАЦИОНАРНОГО ОБОРУДОВАНИЯ
Современная шахта оснащается сложным стационарным обо рудованием; монтаж его должен производиться только по про ектам производства работ, в которых в конкретных условиях обосновывается выбор метода монтажа. Порядок разработки проекта и его объем подробно изложен в § 1, а в настоящей главе рассматриваются лишь наиболее распространенные мето ды и технология сборки основного шахтного стационарного обо рудования.
При этом предполагается, что до начала монтажа обору дование должно быть тщательно осмотрено, очищено от грязи, детали и узлы промыты. Монтаж установки может быть начат только при полной укомплектованности самого оборудования и наличии необходимых монтажных средств и материалов.
§ 20. Монтаж подъемных машин
Подъемная машина на шахте или руднике является самым основным и наиболее сложным стационарным оборудованием. Подъемная машина (рис. 69) обеспечивает подъем из подзем ных выработок полезного ископаемого и породы, спуск в шахту и подъем на поверхность людей, вспомогательных материалов и оборудования.
До начала монтажа подъемной машины разрабатывается проект производства работ. Монтаж выполняется в строгом со ответствии с графиком, являющимся составной частью проекта производства работ.
Мех'аническая часть подъемной машины поступает с завода на шахту в разобранном виде и состоит из коренной части, ре дуктора, тормозных приводов, управления, указателя глубины с ограничителем скорости, воздушной и смазочной систем, ог раждения и деталей пружинных муфт.
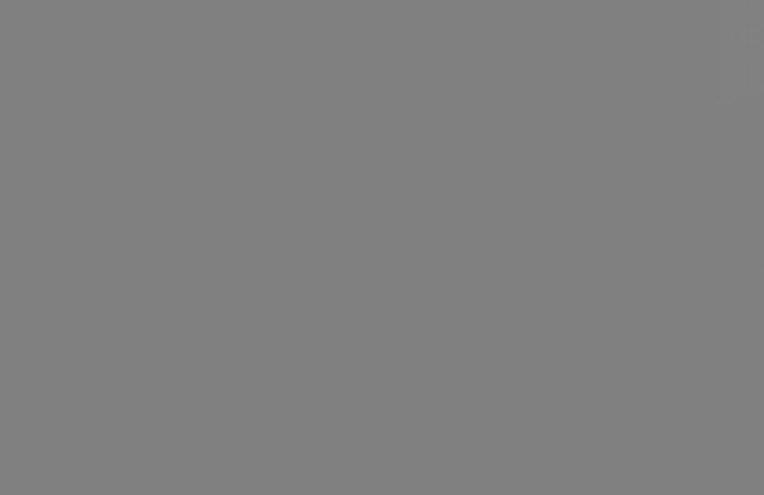
Коренная часть содержит постаменты с подшипниками, ко ренной вал со ступицами и механизмом перестановки бараба нов и барабаны.
Прибывшее на строительную площадку оборудование дол жно быть размещено в местах, специально предназначенных для этих целей проектом производства работ.
До начала монтажа шахтной подъемной машины на пло щадке выполняются все подготовительные работы. Проверяется комплектность узлов и деталей подъемной машины, устанавли ваются й оснащаются подъемно-транспортные средства и при нимается под монтаж строительная часть (здание и фундамент)
Фундамент перед монтажом должен быть очищен от строитель ного мусора и грязи и хорошо промыт водой. На фундаменте должны быть нанесены главные оси машины по осям подъема
икоренного вала. Перед началом монтажа заготовляется и до ставляется в здание подъемной машины инструмент и всевоз можные вспомогательные средства (подмости, настилы, шпалы
ит. д.). Примерный перечень основного оборудования, приспо соблений и материалов, необходимых для монтажа подъемной машины, приведен в табл. 24.
Т а б л и ц а 24
|
|
|
Наименование монтажных |
Единица |
Количе |
||
|
|
|
|
средств |
иа.\ ере- |
ство |
|
|
|
|
|
|
|
ния |
|
Лебедка электрическая (0 = 5 т) . |
ШТ. |
3 |
|||||
Трактор ........................ |
|
|
1 -2 |
||||
Таль ручная (Q = 1 |
т) . |
|
|
1 |
|||
Салазки металлические (0 = 30—60 т) |
|
1 |
|||||
Металлический лист размером 3 X 1 . 5 м |
|
2 |
|||||
Мачта из стальных труб 0 |
400 мм, высотой 9 м |
|
2 |
||||
Блок 3-роликовый |
(0 = 20 т) |
|
6 |
||||
» |
2-роликовый |
(0 = 10 т) . |
|
5 |
|||
„ |
однороликовый (0 = |
5 ш) |
|
8 |
|||
Съемник универсальный (0 |
1000 м) |
компл. |
1 |
||||
Приспособление для проточки футеровки барабанов |
1 |
||||||
Канат стальной |
0 |
21,5 мм |
|
м |
520 |
||
Канат стальной |
0 |
24 мм . |
|
щ |
280 |
||
Верстак передвижной на одни тиски |
Ш Т . |
1 |
|||||
Электросварочный аппарат |
|
» |
2 |
||||
Переносное горно |
|
|
п |
1 |
|||
Точило наждачное |
|
|
п |
1 |
|||
Бурильный |
молоток |
|
л |
1 |
|||
Огбойный |
молоток ........................... |
1 |
|||||
Вертикально-сверлильный станок по металлу 0 25 мм |
» |
1 |
|||||
Дисковая пила по дереву . |
|
* |
1 |
||||
Пневматический молоток для рубки стали |
п |
1 |
|||||
Суппорт для проточки ободьев |
9 |
2 |
|||||
Бензорез |
|
|
|
|
компл. |
2 |
Одной из трудоемких и ответственных работ при монтаже шахтных подъемных машин является доставка и установка тя-
108
желовесных узлов и деталей. Эти монтажные операции должны •быть тщательно разработаны в проекте производства работ, а имеющиеся подъемно-транспортные средства и их оснастка проверены соответствующими расчетами.
Доставку основных тяжеловесных узлов машины — коренного вала, полубарабанов и редуктора — от мест складирования к зданию подъемной машины лучше всего производить на санях
Рис. 70. Затаскивание тяжеловесных |
узлов подъемной |
машины типа |
2Х 6X2,4: |
|
|
1 — коренной вал, 2 — электрические лебедки, |
3 — настил из рельс, |
4 — деревянный |
настил, 5 — поддерживающие ролики, 6 — полубарабан
трактором. Затаскивание в здание и перемещение внутри его рекомендуется выполнять при помощи электрических лебедок грузоподъемностью 5 т. При этом для затаскивания узлов подъ емной машины типа 2 х 6X2,4 необходимо иметь в здании два монтажных проема А и Б (рис. 70), а для машин типа 2Х4Х Xl,8 и 2 x 5 x 2 ,3 достаточно одного проема.
Второй проем £, перпендикулярный оси подъема, исключает разворот внутри здания коренного вала машины.
Для затаскивания тяжеловесных узлов подъемной машины типа 2X6X2,4, например коренного вала 1, устанавливаются электрические лебедки 2 грузоподъемностью 5 ткаждая, выкла дываются шпальные клетки, на которые опирается настил 3 из швеллера или рельсов. Во избежание прогиба настила в котло-
ване фундамента из деревянных брусьев устанавливаются опор ные рамы.
Перемещение коренного вала машины в поперечном направ лении производится по настилу 4 из деревянных брусьев. Для предохранения тяговых канатов от истирания о стенки здания устанавливаются поддерживающие ролики 5 (однороликовые балки). Вал перемещается до совпадения осей шеек вала с ося ми коренных подшипников. Через проем А также по настилу при помощи лебедок затаскиваются полубарабаны 6.
Монтаж подъемной машины начинается с установки поста ментов с подшипниками на фундамент, который предварительно очищается от масляных пятен и грязи. Для лучшего схватыва ния с подливаемым цементным раствором на бетоне фундамента делаются насечки.
До монтажа постаментов должны быть заложены анкерные плиты и размечены на фундаменте места для установки метал лических подкладок. Анкерные плиты опускаются в подвальное помещение фундамента и устанавливаются в специально преду смотренные ниши, после чего заводятся анкерные болты поста ментов. Подкладки устанавливаются по обе стороны анкерных болтов и в промежутках между ними на расстоянии 600—700 мм. Одна из подкладок ставится по оси подшипника.
На подкладки устанавливаются постаменты с подшипниками и закрепляются легкой затяжкой гаек анкерных болтов, после чего при помощи уровня и монтажных осевых струн, с которых отпускаются отвесы, производится выверка правильности уста новки постаментов.
Отклонение от горизонтальности для постаментов допу скается не более 0,15 % о (т. е. 0,15 мм на 1 м длины). Регули ровка горизонтальности производится за счет изменения тол щины подкладок. Постаменты проверяются на параллельность между собой и по высотным отметкам. Высотные отметки про веряются нивелиром. На выставленные по проекту постаменты устанавливаются подшипники. При этом проверяется прилега ние опорных поверхностей подшипников и отклонение их от оси коренного вала. Прилегание подшипника к постаменту про веряется щупом, пластинка которого толщиной 0,2 мм не долж на проходить между прилегающими поверхностями. Качествен ное прилегание достигается шабровкой. Отклонение оси под шипника от осевой линии коренного вала не должно превышать 0,05%о, а отклонение от горизонтали 0,1%0. Выверка подшип ников производится при ослабленных болтах.
Перед укладкой коренного вала в подшипники его шейки тщательно очищаются от краски и смазки и проверяется уста новка съемных деталей. Иногда в зависимости от принятого способа монтажа перед укладкой коренного вала в подшипники в котлован фундамента опускаются полубарабаны.
Способ укладки коренного вала в подшипники зависит от
но
принятых для монтажа подъемных средств. При монтаже подъ емной машины при помощи мачт коренной вал стропится к подъ емным крюкам мачт, поднимается с саней на 200 мм и опус кается в подшипники. Иногда коренной вал устанавливается в подшипники при помощи гидравлических домкратов.
Во всех случаях опускание вала в подшипники должно про изводиться с большой предосторожностью, чтобы не повредить вкладыши.
Уложенный в подшипники вал проверяется на горизонталь ность по высотным отметкам и заданным осям. Проверка рас положения' вала производится через каждый поворот вокруг своей оси на 60° Схема выверки коренного вала подъемной ма шины при помощи нивелира показана на рис. 71. Горизонталь ность вала может быть проверена уровнем, укладываемым на шейки валов или рейсмусом.
При правильном расположении вала 1 (см. рис. 71) по отно шению к его продольной оси, проекция отвесов 2 на торец вала должна совпадать с его центром. Проверка производится при помощи нивелира 3, который устанавливается так, чтобы от весы проектировались одной линией. Высотные отметки прове ряются нивелированием положения вала по отношению к вы сотному реперу, для чего на репер и на вал устанавливаются масштабные рейки 4 с делением 1 мм.
При отклонении положения вала от проектного регулировка производится за счет смещения подшипников при помощи бо ковых клиньев или установки под постаменты подкладок. При этом вал приподнимается гидравлическими домкратами или мачтами. Небольшие перемещения подшипников и, если необ ходимо, постаментов производятся при ослабленных анкерных болтах.
Проверка правильного положения вала по отношению к оси подъема производится путем опускания отвеса на вал из точ ки А пересечения монтажных струн — осей вала и подъема. Равенство расстояний от отвеса до внутренних ступиц барабана показывает правильность положения вала по отношению к оси подъема.
После проверки правильности установки вала и затягивания анкерных болтов постаментов проверяется вращение ступиц пе реставного барабана, устанавливаются верхние вкладыши и крышки подшипников. Зазор между шейкой вала и верхними вкладышами подшипников должен соответствовать допускам, указанным в сборочных чертежах.
Барабаны подъемной машины являются ответственными уз лами, поэтому к монтажу их необходимо отнестись с особым вниманием. Барабаны крупных подъемных машин поступают на шахту разобранными на две части (в виде полубарабанов). Барабаны могут быть собраны с предварительным опусканием их половин в котлован фундамента до установки коренного вала