
книги / Монтаж шахтных стационарных установок
..pdfЪ\ должны быть равны между собой в сечении АА и соответст
вующим размерам в сечении ББ.
Расстояния U и h от мест замера до приспособлений для на тяжки струн должны быть равны между собой, при этом необ ходимо учитывать провес струны. В зависимости от диаметра струны принимается следующая величина натяжного груза:
при диаметре струны 0,35 мм . |
9,45кг |
0,40 |
12,34 |
0,45 |
15,02 |
0,50 |
19,29 |
Во избежание сложных расчетов величина провеса струны принимается по табл. 26, рассчитанной для условий натяжения струн, соответствующими им грузами.
Длина струны, м
|
|
|
|
|
|
Т а б л и ц а |
26 |
|
|
Провес струны, в сотых долях миллиметра |
|
|
|
||||
|
Расстояние от |
стойки (/, |
или |
см. рис. 92). м |
|
|
||
1 |
1 .6 1 2 12.5 | 3 з,б | |
4 4.5 |
5 |
1 5.5 |
6 |
6.5 |
7 7.5 |
8 |
4 |
6,5 |
9 |
10 |
24 |
|
|
|
|
|
|
|
|
|
|
|
5 |
12,5 |
18 |
22 |
40 |
|
|
|
|
|
|
|
|
|
|
|
6 |
18 |
26 |
30 |
39 |
55 |
|
|
|
|
|
|
|
|
|
|
7 |
22 |
31 |
39 |
46 |
52 |
70 |
|
|
|
|
|
|
|
|
|
8 |
25 |
36 |
45 |
54 |
62 |
68 |
86 |
|
|
|
|
|
|
|
|
9 |
28 |
40 |
50 |
60 |
70 |
77 |
83 |
100 |
|
|
|
|
|
|
|
10 |
31 |
42 |
54 |
65 |
77 |
86 |
93 |
98 |
н е |
|
|
|
|
|
|
11 |
33 |
46 |
59 |
71 |
83 |
94 |
ЮЗ |
109 |
114 |
132 |
|
|
|
|
|
12 |
35,5 |
50 |
64 |
76 |
90 |
102 |
112 |
120 |
127 |
129 |
146 |
|
|
|
|
13 |
38 |
54 |
69 |
82 |
96 |
109 |
119 |
129 |
136 |
142 |
145 |
161 |
|
|
|
14 |
41 |
58 |
74 |
90 |
105 |
117 |
128 |
137 |
145 |
152 |
157 |
160 |
176 |
|
|
15 |
44 |
63 |
80 |
95 |
ПО |
124 |
135 |
144 |
153 |
160 |
165 |
170 |
174 |
190 |
|
16 |
49 |
67 |
86 |
100 |
115 |
130 |
140 |
150 |
159 |
167 |
174 |
180 |
186 |
189 |
|
|
Проверка угла вала производится микрометрическим штих- |
||||||||||||||
масом путем |
замера |
расстояния b |
(рис. 93, |
а) |
от галтели |
кри |
вошипа до струны, натянутой по оси параллелей. Замеры рас стояния b производятся при двух противоположных положениях колена вала (Ь и Ь\). Разность в замерах при проверке угла вала не должна превышать 0,15 мм на 1 м диаметра кривошипа.
Перед укладкой в подшипники коленчатый вал очищается от противокоррозийной краски и смазки; если имеются кольце вые неглубокие риски и забоины на шейках, то они шлифуются мелким наждачным полотном с маслом.
Установка вкладышей подшипника в корпус и подгонка их по шейкам вала производится согласно указаниям, приведенным в § 12.
Шейки вала проверяются индикатором (рис. 93, б) ца бие ние, которое не должно превышать 0 , 0 5 мм для коренных и 0,08 мм для концевых шеек.
Горизонтальность вала проверяется установкой на его шей ках уровня. При этом по каждой шейке окончательной считается среднеарифметическая величина из 4 замеров. Положение вала считается правильным, если общая линия его имеет уклон от концов к середине. Разность в замерах уклонов коренных шеек вала у обеих рам не должна превышать 0,5—1,0 ^деления по
уровню с ценой деления 0, 1!7оо.
Горизонтальность кривошипных шеек проверяется уровнем при каждом повороте вала на 90° Непараллельность оси криво шипной шейки к оси коренной шейки вала допускается в пре делах 0,02 мм на 100 мм длины шейки.
После насадки ротора на вал проверяется размер с — рас хождение щек каждого колена и зазоры а около галтелей вала, окончательно подгоняются вкладыши концевых подшипников. Замер расхождения щек производится микрометрическим штихмасом в 4 диаметрально противоположных точках на расстоя нии 20—30 мм от края щек.
Разность замеров расхождения щек не должна превышать 0,00018# (где Я — ход поршня в мм).
Зазоры по галтелям фиксирующего подшипника с обоих его торцов не должны в сумме превышать 0,00Ш (где D — диаметр шейки вала в мм). Остальные зазоры должны быть в пределах допусков, указанных в сборочных чертежах.
Внутренние полости цилиндров тщательно очищаются от сле дов коррозии, промываются керосином и насухо протираются.
На фундамент устанавливаются опорные плиты, а на них цилиндры. При этом проверяется по краске прилегание лап ци линдров к опорным плитам. Между лапами и плитами допус кается зазор не более 0,05 мм на участке длиной в 0,1 перимет ра. Зазор проверяется щупом.
Установленный на опорную плиту цилиндр соединяется с ра мой болтами. Затяжка болтов производится равномерно. Сво бодный конец цилиндра при установке подпирается домкратом, который одновременно служит для регулирования цилиндра в период укладки опорной плиты.
Правильность установки цилиндров проверяется по струне по совпадению оси /—/ рамы 1 с осью II—II цилиндра 2 (рис. 94). При этом должно быть учтено провисание струны. Обнаруженный в процессе установки цилиндра перекос b по струне более 0,5 мм на 1 м расстояния L должен устраняться опиловкой привалочной плоскости (место М плоскости цилинд ра, соприкасающейся с рамой). Величина спиливания при пере косе определяется по свинцовому оттиску 3 при совпадении осей рамы и цилиндра.
После окончания выверки рам, цилиндров и коленчатого ва ла, фундаментные болты затягиваются до отказа и производится подливка рам цементным раствором. Одновременно цементным раствором заливаются опорные плиты цилиндров.
Рис. 93. Выверка вала компрессора.
л — проверка угла вала, б — провеока биения шеек вала, t вал, 2 — индикатор
Рис. 94. Проверка установки цилиндра:
/ — рама, 2 — цилиндр, 3 — свинцовый оттиск
1 2
Рис. 95. Выверка крейцкопфа:
1 — башмак, 2 — направляющая рама, 3 — шток, 4 — корпус
Перед установкой крейцкопфа его детали промываются керо сином, а смазочные отверстия продуваются.
Если башмаки 1 (рис. 95) крейцкопфа подлиты баббитом, то проверяется качество заливки. Баббит должен плотно приле гать к башмаку и при обстукивании издавать звук без дребез жащих и глухих тонов.
При установке крейцкопфа необходимо обеспечить совпаде ние его оси с осью направляющей рамы 2. Выверка осей произ водится по штоку 3 и регулируется прокладками между нижним башмаком и корпусом 4 крейцкопфа. Зазор а между верхним башмаком крейцкопфа и параллелью рамы регулируется при помощи прокладок между верхним башмаком и корпусом крейц копфа. Окончательная доводка зазора между верхним башма ком и параллелью достигается шабровкой поверхности башмака. Величина верхнего зазора должна быть не более 0,00Ш (где D — диаметр крейцкопфа в мм). Зазор проверяется щупом в нескольких местах по длине и ширине башмака при крайних положениях крейцкопфа.
При установке крейцкопфа проверяется наличие масляных клиньев с и смазочных канавок на рабочих поверхностях баш маков крейцкопфа.
Перед заводкой поршня в цилиндр проверяется его крепле ние на штоке, прилегание посадочных мест, а также отсутствие люфта в резьбе штока. Шток не должен иметь забоин или ри сок, особенно продольных рисок на участке, работающем в саль нике. При наличии мелких рисок последние выводятся бархат ным напильником и шлифуются мелким наждачным по лотном.
До заводки на поршень устанавливаются кольца, для этого каждое поршневое кольцо сжимается мягкой проволокой, кото рая разрезается при заходке половины кольца в цилиндр. Вме сто проволоки для сжатия поршневых колец применяются спе циальные зажимы. Торцовый зазор поршневых колец при плот ном их сжатии должен быть в пределах 0,4—1 мм, а при встав ленном поршне в цилиндр — 0,005D (где D — диаметр цилиндра в мм). Зазор между торцами поршневых колец и стенками ка навки в сумме не должен быть более 1 мм.
Заводка поршня 1 в цилиндр 2 (рис. 96) должна осущест вляться с большой предосторожностью, чтобы избежать повреж дения поршня. При заводке под поршень укладывается из шпал постель 3, а поршень поддерживается талью 4, при этом стро повка производится канатными стропами 5 за шток 6 и хомут 7. Как только шток зайдет в гнездо 8 сальника, поддерживающий его строп снимается, а поршень остается подвешенным на стро пе за хомут. Подача поршня вдоль оси цилиндра осуществляется домкратом 9 через деревянную подушку 10.
Кроме описанного способа, заводку поршня можно произво дить приспособлениями, показанными на рис. 66.
Ю И. В. Браун |
145 |
После заводки поршня и соединения его с крейцкопфом со бирается сальник.
При сборке сальника проверяется натяжка торцовых зазо ров уплотнительных колец, обжимающих шток. Зазор должен
Сечение поАЯ
т т т
Рис. 9ü. Заводка поршня со штоком в цилиндр:
/ — поршень, |
2 — цилиндр, 3 — постель, |
4 — ручная таль. |
|
5 — стропы, |
6 — шток, |
7 — хомут, 8 — гнездо сальника, |
|
9 — домкрат, |
10 — деревянная |
подушка |
быть в пределах 0.005D (где D — диаметр штока, мм). Кольца сальника пришабриваются по штоку, а их торцы — по плите и между собой. Для проверки каналов смазки и совпадения на правляющих штифтов по гнездам, производится контрольная сборка сальника. После чего производится сборка сальника на штоке и соединение штока с крейцкопфом.
Выверка правильности установки поршня заключается в про верке зазора между поршневыми кольцами и зеркалом цилинд ра. Этот зазор должен быть не более 0,05 мм на 7з окружности цилиндра. Площадь прилегания несущей поверхности поршня к зеркалу цилиндра должна составлять не менее 50—60% рабо чей площади поршня.
Крышки цилиндров устанавливаются после сборки и выверки кривошипно-шатунного узла.
После окончательной установки поршня (который должен быть предварительно смазан) вторично проверяется его соеди нение с крейцкопфом и положение последнего на нижней па раллели. Горизонтальное положение штока проверяется индика тором при передвижении его на величину хода.
При проверке положения штока индикаторы устанавли-’ ваются в вертикальной плоскости, после чего проворачивают ко ленчатый вал на полный ход поршня. Если при этом стрелка индикатора не изменяет своего положения, то шток горизон тален.
Монтаж шатунов сводится к правильной их установке отно сительно цилиндра и кривошипа. При установке шатунов их продольные оси должны лежать в параллельных плоскостях, в которых проходят и оси цилиндров. Оси головок шатунов долж ны быть параллельны оси коленчатого вала и перпендикулярны осям цилиндров, а расстояния между осями головок обоих ша тунов равны.
Кривошипные и крейцкопфные вкладыши шатунов подго няются соответственно к шейке коленчатого вала и пальцу крейцкопфа. Площадь прилегания вкладышей проверяется по краске и должна быть равна не менее 60—70% рабочей пло щади. Зазор между вкладышами мотылевого подшипника и шейкой должен быть в пределах 0,0003—0,0005D (где D — диа метр шейки, мм)у а между вкладышем крейцкопфа и пальцем — 0,03—0,05 мм. Зазор по галтелям шатунного подшипника с обоих его торцов в сумме должен быть в пределах 15—20 мму а по галтелям крейцкопфного подшипника (размеры б и в см. рис. 95) — 0,5—0,7 мм.
При сборке кривошипно-шатунного узла весьма важно пра вильно установить зазор между поршнем и крышками цилинд ра. Эта проверка производится в два приема. Первоначально поршень со штоком, соединенным только с крейцкопфом, пере двигается до упора в переднюю и заднюю крышки цилиндра и на параллелях отмечается крайние положения крейцкопфа. Затем крейцкопф соединяется с шатуном, кривошип ставится в мертвое положение и на параллелях отмечается положение крейцкопфа. Расстояния между метками в первом и втором случаях составят зазоры между поршнем и крышками цилиндра (мертвое пространство).
Величина зазора между поршнем и крышками цилиндра уста навливается в строгом соответствии со сборочными чертежами. Зазор между передней крышкой и поршнем регулируется изме нением толщины дистанционной шайбы в крейцкопфе, а зазор между поршнем и задней крышкой — изменением толщины уплотнительной прокладки между цилиндром и задней крышкой.
Пластины клапанов поступают притертыми по седлам и при
монтаже производится лишь проверка керосином их плотности. Корпус клапана должен свободно входить в гнезда. Собран ный клапан проверяется на легкость хода пластин по направ ляющим ребрам и отсутствие перекашивания и заедания пла стин. После контрольной сборки клапаны снимаются, смазы ваются и до обкатки хранятся в кладовой.
Подготовка фундаментов и укладка подкладок под электро двигатель производится аналогично разобранным выше опе рациям при установке рам. На подкладки устанавливаются опорные* плиты двигателя, которые выверяются по осям комп рессора.
Двухцилиндровые горизонтальные компрессоры в качестве привода имеют синхронные электродвигатели.
Электродвигатель имеет разъемный ротор. Плоскость разъ ема ротора параллельна оси двигателя. Каждая половина ро тора имеет половину маховика.
Монтаж этих электродвигателей существенно отличается от установки электродвигателей других шахтных машин и меха низмов.
Сборка электродвигателя производится в следующем по рядке.
Коленчатый вал вынимается из подшипников и укладывается в стороне на деревянных подкладках. Статор устанавливается на опорные плиты и сдвигается в сторону, противоположную маховику. В статор на паранитовые подкладки укладывается одна половина ротора. После этого в подшипники укладывается коленчатый вал, вставляется вторая половина ротора, которая шпильками соединяется-с первой половиной ротора. Соединен ный ротор передвигается по валу до места установки (согласно сборочному чертежу) и закрепляется при помощи шпонок и шпи лек. Затем передвигается статор на место и устанавливаете,! таким образом, чтобы зазоры между статором и ротором соот ветствовали сборочному чертежу.
Остальные узлы и детали компрессорной установки (проме жуточный холодильник, смазочная система, система охлажде ния, арматура и трубопровод в пределах здания компрессорной) монтируются одновременно со сборкой и выверкой крмпрессоров. Монтаж перечисленных узлов и деталей не представляет особой сложности, однако следует заметить, что при установке арматуры и трубопроводов необходимо обеспечить плотность соединения, соответствие диаметров труб и арматуры и соблю дение уклонов труб. Всасывающий и нагнетательный трубопро воды должны присоединяться к фланцам компрессора без осо бой натяжки.
Собранная масляная система (маслопроводы) протравли вается аналогично масляной системе подъемных машин.
До установки воздухосборника проверяется его фундамент, укладываются подкладки и выверяется их горизонтальность.
Воздухосборник, как правило, устанавливается за пределами здания при помощи крана на автомобильном или гусеничном ходу. Строповка воздухосборника производится так, чтобы он в поднятом состоянии находился в вертикальном положении. После установки воздухосборник закрепляется на фундаменте болтами и соединяется трубопроводом с коммуникациями ком прессорной установки и воздушной сетью шахты.
После окончания монтажа компрессор обкатывают, проду вают и опробуют под нагрузкой.
Перед обкаткой система смазки заполняется маслом и про качивается до тех пор, пока масло не будет выходить из масло провода совершенно чистым. Чистота масла проверяется по фильтровальной сетке. При прокачке масла маслопровод отсое диняется от точек смазки и слив из маслопровода направляется в картер.
Перед каждым пуском компрессора масло прокачивается ручным насосом через коренные подшипники и крейцкопф, а лубрикатором — в цилиндры и сальник; проверяется длинным щупом зазор между ротором и статором, при помощи специаль ного механизма проворачивается ротор на один оборот.
Перед обкаткой включаются в работу системы смазки и охлаждения, проверяется направление вращения двигателя. При правильном направлении вращения электродвигатель включают на 5 мин. После этого компрессор останавливается и прове ряется температура трущихся частей, которая не должна быть выше 25—30° (при такой температуре детали на ощупь кажутся холодными). Причинами повышения температуры трущихся деталей могут явиться плохая смазка и шабровка вкладышей, различные перекосы и недостаточные радиальные зазоры в под шипниках. После устранения причин, вызвавших повышенный нагрев, компрессор вновь пускается на 20 минут. При этом нагрев трущихся деталей не должен превышать 40—45° При нормальном нагреве опробование продолжается — компрессор запускается на 6 час. непрерывной работы.
Обкатка компрессора производится со снятыми клапанами. Если после часа непрерывной работы температура трущихся деталей не превышает 60°, то приступают к продувке компрес сора.
Перед продувкой каждый клапан разбирается, прочищается и смазывается.
Продувка компрессора производится в следующем порядке: 1) устанавливаются всасывающие клапаны первой ступени и продувается нагнетательная полость в цилиндре этой ступени; 2) устанавливаются нагнетательные клапаны первой ступени, продувается всасывающая полость второй ступени и холодиль-
ник; 3) устанавливаются всасывающие клапаны второй ступени
и продувается нагнетательная полость цилиндров этой ступени.
4) устанавливаются нагнетательные клапаны второй ступе ни и продувается трубопровод этой ступени и воздухосборника.
Каждая продувка продолжается в течение 15—20 мйн. После продувки компрессорная станция опробуется. При
опробовании компрессор в течение 10—15 мин. должен рабо тать в атмосферу, а затем вентиль на нагнетательном трубопро воде закрывается и давление поднимается до 2 ати. Поддержи вая давление в нагнетательном трубопроводе второй ступени на уровне 2 ати в течение 20 мин. производится проверка: дав ления масла в трубопроводе; работы клапанов и кривошипношатунного механизма (отсутствие стуков, ненормального нагре ва); герметичности фланцевых соединений; работы сальников, подачи смазки и охлаждающей воды. Затем задвижка на нагне тательном трубопроводе постепенно прикрывается и подни мается давление до 5 ати, и в течение 1 часа производится та же проверка. После этого давление доводится до 7—8 ати и проверяется работа компрессора при этом давлении в течение 2 час. Температура воздуха при выходе из холодильника не дол жна превышать +40°, а сжатого +150°. После остановки комп рессора температура трущихся деталей не должна превышать + 60°.
При отсутствии дефектов компрессор испытывается под на грузкой 24 часа.
После опробования компрессора производится его ревизия, при которой вскрываются и просматриваются все подшипники, всасывающие и нагнетательные клапаны, вскрываются крышки и осматриваются цилиндры. По окончании ревизии масло в си стеме смазки заменяется и составляется акт о сдаче компрес сорной установки в эксплуатацию.
§ 24. Монтаж насосных станций главного водоотлива
Па каждой шахте в околоствольном дворе в специальной ка мере монтируется насосная станция, состоящая из трех и более центробежных насосов типа КСМ или АЯП (рис. 97).
До начала монтажа насосов необходимо убедиться в готов ности горнопроходческих и строительных работ и принять под монтаж фундаменты, а также подготовить необходимые подъ емные средства и инструмент. В качестве подъемных средств используются предусмотренные в каждой насосной станции крап-балка или тренога с талью.
На монтаж насосных станций главного водоотлива состав ляется проект производства работ, в котором, кроме монтажа оборудования, приводится организация работ по спуску насо сов в шахту.
Насос производительностью до 70 м?/час в комплекте с элек тродвигателем собирается на общей раме и опробуется на по верхности шахты.
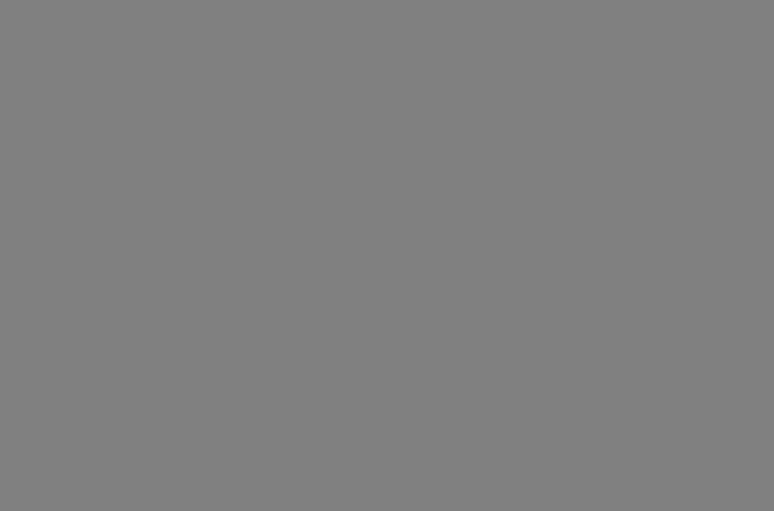