
книги / Теория механизмов и механика систем машин
..pdf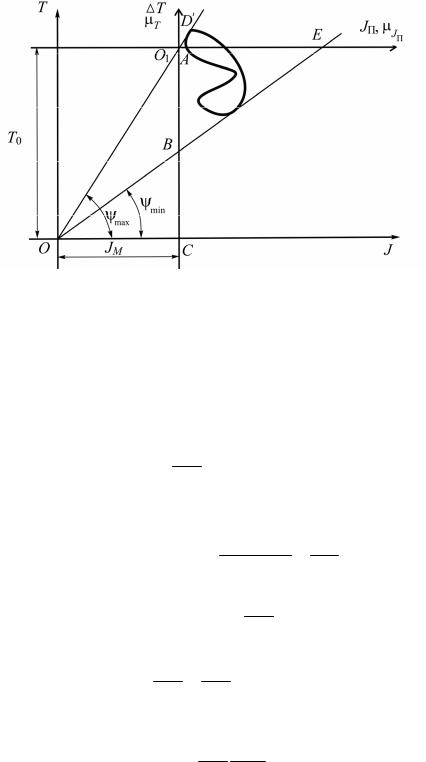
Определив начало координат полной диаграммы энергомасс Т = f (JП), можно найти момент инерции маховика JП и начальную кинетическую энергию Т0 так, как показано на рис. 5.4. Отрезок ОС в масштабе J П пред-
ставляет собой искомый момент инерции маховика: JМ = µJП (ОС).
Рис. 5.4. Определение истинного закона движения ведущего звена
Погрешность расчета этим методом возникает при проведении касательных, так как углы ψmax и ψmin, особенно при малых δ, очень близки друг к другу, что затрудняет точное проведение касательных и определение положения начала координат точки О. Касательные в этом случае в пределах чертежа обычно не пересекаются. Тогда момент инерции маховика
tg max OCAC , tg min OCBC .
Взяв разность тангенсов, получим
tg max tg min AC BC AB ,
OC OC
tg max tg min JП 2ср ,
Т
АВ JП 2срδ
ОС Т
или
ОС JП А2В ,
JП ср
101

JM AB2 T .
ср
Иногда (при больших значениях углов ψmax и ψmin) касательные в пределах чертежа не пересекают ось ординат Т, но пересекают ось абсцисс в точках D и Е. Тогда, измерив отрезки О1D и О1Е, отрезок АВ можно вычис-
лить следующим образом. На рис. 5.4 О1А = О1Dtg ψmax, O1B = O1EDtgψmin,
откуда AB = O1B – O1A = O1Etgψmin – О1Dtgψmax.
5.7. Определение основных размеров маховика
После определения момента инерции маховика JМ переходят к выбору его основных размеров. Обычно маховик рассматривается как массивное кольцо среднего диаметра D, в котором сосредоточено примерно 0,9 массы маховика. При этом условии момент инерции маховика
JM GD4g2 ,
где G – вес маховика; D – средний диаметр обода маховика; g – ускорение силы тяжести.
Произведение GD2 называется маховым моментом и является основным параметром, характеризующим маховик.
Поскольку в выражение махового момента входят две неизвестные величины G и D, то одну из них задают, а другую находят. Обычно задают из конструктивных соображений диаметр маховика, а находят его вес.
Из соотношения GD2 = 4gJМ видно, что чем больше диаметр маховика, тем меньше его вес. Но злоупотреблять увеличением размеров для уменьшения веса маховика не рекомендуется, так как с увеличением диаметра возрастает окружная скорость, а следовательно, создается напряжение на ободе и может произойти его разрыв. Необходимо при выборе диаметра проверять окружную скорость на ободе, вычисляя ее по следующей формуле:
V |
max |
D |
|
1 |
D . |
||
окр |
2 |
cp |
2 |
|
2 |
||
|
|
|
|
|
При этом можно руководствоваться следующими цифрами: Vокр ≤ 30 м/с для чугунных маховиков; Vокр ≥ 50 м/с для стальных маховиков. Выбрав диаметр маховика, определяют его теоретический вес:
102
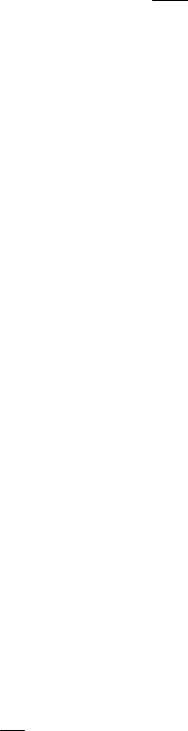
G 4DJM2 .
Обычно действительный вес обода
GД = 0,9G.
5.8. Конструкции маховиков
Основное назначение маховика заключается в ограничении колебаний угловой скорости главного вала в пределах, заданных коэффициентом δ. Маховик является аккумулятором кинетической энергии машины. Если при работе механизма с маховиком Т > 0, то угловая скорость главного вала возрастает и маховик накапливает кинетическую энергию. В противном случае при недостатке Т угловая скорость главного вала снижается и маховик отдает часть энергии машине, являясь дополнительным источником движущих сил.
За счет значительной накопленной энергии во время ускоренного движения маховик применяется для преодоления повышенных нагрузок без увеличения мощности двигателя. В машинах ударного действия: молотах, прокатных станах, прессах, в автомобилях – он содействует выводу рабочих органов из «мертвых» положений.
Наибольшее распространение в технике получили маховики двух типов: со спицами и дисковой конструкции.
Маховик со спицами
Конструкции этих маховиков приведены на рис. 5.5. Материал для маховиков выбирают в зависимости от окружной скорости V на наружном диаметре D.
При V ≤ 25 м/c применяются литые маховики из чугуна СЧ12-28; при
V ≤ 25–30 м/с – из чугуна СЧ15-32; V ≤ 30–35 м/с – из чугуна СЧ18-36 и
СЧ21-40 (плотность ρ = 6800–7400 кг/м3); при V ≤ 45 м/с – маховики литые стальные из СТ3–СТ5 (ρ = 7500–7900 кг/м3). Сечение спиц эллиптическое с
отношением осей bcn 0,4 0,5. Спицы выполняются коническими. Разме-
acn
ры bcn и can уменьшаются от ступицы к ободу на 20 %. При наружном диаметре D < 300 мм маховики изготавливают дисковой конструкции без спиц. Значения размеров и массовых характеристик маховиков в соответствии с рис. 5.5 представлены в табл. 5.1.
103
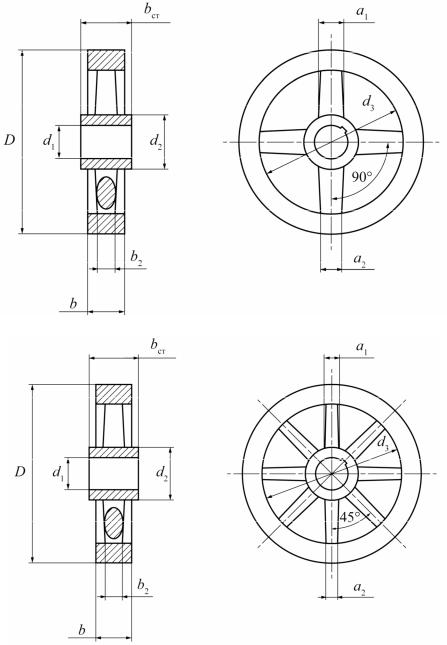
а
б
Рис. 5.5. Конструкции маховиков с четырьмя (à), восемью (á) спицами
|
|
|
|
Таблица 5 . 1 |
|
Основные параметры маховика со спицами |
|||
|
|
|
|
|
D, мм |
|
Число спиц, n |
|
Основные размеры, мм |
300–800 |
|
4 (рис. 5.5, а) |
d1 |
= 0,2D; d2 = 0,3D; d3 = 0,08D; |
|
|
|
b = 0,125D; b1 = 0,44b; b2 = 0,352b |
|
800–1600 |
|
6 |
a1 = 1,1b; a2 = 0,88b; bст = 1,05b |
|
|
|
|
d1 |
= 0,2D; d2 = 0,32D; d3 = 0,08D; |
≥1600 |
|
8 (рис. 5.5, б) |
b = 0,125D; b1 = 0,44b; b2 = 0,352b; |
|
|
|
|
a1 |
= 0,88b; a2 = 0,704b; bст = 1,05b |
104
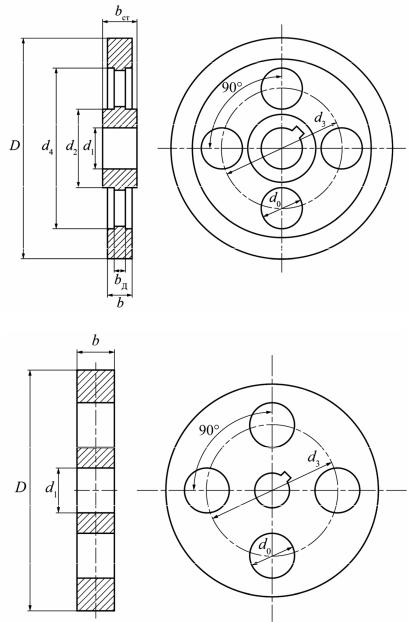
Дисковый маховик
Маховики данного типа показаны на рис. 5.6. При наружном диаметре D < 300 мм независимо от величины окружной скорости следует применять маховики дисковой конструкции. При окружных скоростях V ≤ 45 м/с рекомендации по материалу те же, что и в случае маховика со спицами. При окружных скоростях V > 45 м/с для маховиков следует применять стали марок 45, 40Н, 34ХНТМ, 35ХМ и т.д., а также алюминиевый сплав АК4.
а
б
Рис. 5.6. Конструкции маховиков: à — с отверстиями в диске; á — литой; â — облегченного типа
105
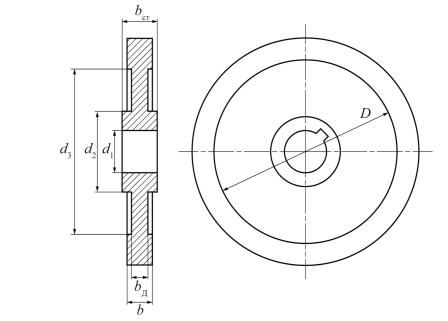
в
Рис. 5.6. Окончание
При одном и том же моменте инерции маховики из алюминиевых сплавов получаются в среднем на 35 % легче по сравнению с конструкциями, изготовленными из стали. Рекомендовано при окружных скоростях V > 100 м/с применять маховики без отверстий в диске, чтобы избежать дополнительного шума при работе. Маховик со сплошным диском получается на 5–8 % тяжелее маховика с отверстиями. Значения основных параметров дисковых маховиков приведены в табл. 5.2.
|
|
|
|
Таблица 5 . 2 |
|
Значения основных параметров дисковых маховиков |
|||
|
|
|
|
|
№ |
Число |
|
|
Основные размеры, мм |
рисунка |
отверстий, n |
|
|
|
5.6, а |
4 |
d0 |
= 0,25D; d1 |
= 0,15D; d2 = 0,25D; d3 = 0,525D; |
d4 |
|
1 |
||
|
|
= 0,8D; b = 0,125D; bД 3 b ; bст = 1,05b |
||
5.6, б |
4 |
d1 |
= 0,15D; d2 |
= 0,6D; d0 = 0,3D; b = 0,125D |
5.6, в |
0 |
d1 |
= 0,15D; d2 |
= 0,25D; d0 = 0,8D; b = 0,125D |
106
6. СИНТЕЗ КУЛАЧКОВЫХ МЕХАНИЗМОВ
6.1. Виды кулачковых механизмов
При конструировании машин приходится подбирать тип или серию механизмов, включаемых в состав машины, исходя из тех процессов, которые должны быть воспроизведены в машине во время ее работы. В тех случаях, когда перемещение, а следовательно, скорость и ускорение ведомого звена должны изменяться по заданному закону, и особенно в тех случаях, когда ведомое звено должно временно останавливаться при непрерывном движении ведущего звена, наиболее рационально применение кулачковых механизмов.
Очертание элементов кинематической пары на кулачке называется профилем кулачка. Выбирая тот или иной закон изменения радиуса векторной кривой кулачка, можно получить самые разнообразные движения ведомого звена. Простота воспроизведения заданного закона движения ведомого звена послужила причиной широкого распространения кулачковых механизмов.
Их достоинством является простота конструкции, надежность, компактность, относительно высокий КПД, возможность движения ведомого звена по любому заданному закону с паузами, что особо ценно для автоматических устройств.
Недостатками кулачковых механизмов являются:
а) сравнительно большой износ соприкасающихся поверхностей высшей кинематической пары из-за больших удельных давлений и высоких относительных скоростей;
б) ограниченность применения при повышенных скоростях ввиду возникновения динамических нагрузок;
в) трудности при изготовлении кулачков сложного профиля. Кулачковые механизмы разделяются на плоские и пространственные
(рис. 6.1).
У плоских кулачковых механизмов все точки движутся в одной или параллельных плоскостях. Эти механизмы различают по виду движения ведомого звена, а также по элементам высшей кинематической пары.
Движение ведомого звена или ведущего звена кулачкового механизма может быть поступательным или вращательным.
Схемы кулачковых механизмов с вращающимися кулачками и поступательно движущимся кулачком показаны на рис. 6.2, а, в, д.
107
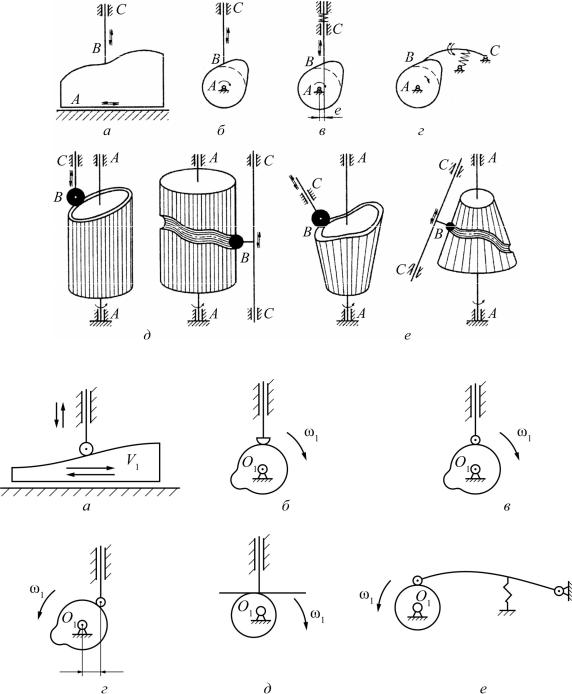
Рис. 6.1. Кулачковые механизмы: à, á, â, ã — плоские; ä, å — пространственные
Рис. 6.2. Кулачковый механизм
На рис. 6.2, б изображен кулачковый механизм с грибовидным толкателем, а на рис 6.2, в – кулачковый механизм с толкателем, оканчивающимся роликом, что резко уменьшает трение при работе механизма. Ось движения толкателя проходит здесь через центр вращения кулачка, такой механизм называется центральным.
На рис. 6.2, г показан кулачковый механизм со смещением, т.е. ось толкателя смещена относительно центра вращения кулачка. Иногда конец толкателя оканчивается плоскостью (рис. 6.2, д). Если ведомое звено долж-
108
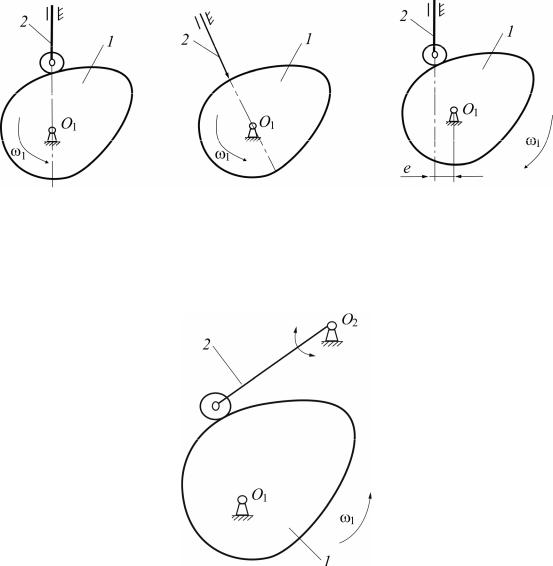
но совершать качательное движение, то возможно построение кулачковых механизмов, где толкатель заменен рычагом или коромыслом (рис. 6.2, е). Постоянное соприкосновение элементов высшей кинематической пары может обеспечиваться устройством пазовых кулачков с двусторонней связью. Эту задачу также можно решить, если поставить пружину на толкатель, такой способ называется силовым замыканием (см. рис. 6.2, е).
Кулачковый механизм с поступательно движущимся толкателем представлен на рис. 6.3.
а |
б |
в |
Ðèñ. 6.3. |
Кулачковый механизм с поступательно |
движущимся толкателем: |
à — с центральным толкателем (ось толкателя проходит через ось вращения кулачка); á — с центральным заостренным толкателем (ось толкателя проходит
через ось вращения кулачка); â — с внеосным толкателем
Рис. 6.4. Кулачковый механизм с возвратно-вращающимся толкателем
Кулачковый механизм с возвратно-вращающимся толкателем показан на рис. 6.4, где звено 2 (толкатель) совершает возвратно-вращающееся движение с центром вращения в точке О2.
109
Рабочий процесс кулачкового механизма
Большинство механизмов используется в машинах и устройствах, имеющих цикловой характер работы. За цикл осуществляется определенная совокупность работ и процессов, в результате которых все параметры состояния системы повторяются, т.е. к концу цикла система приходит в точно такое же состояние, в котором она находилась в начале цикла.
Различают разные виды циклов. Период времени, через который положения и направления скоростей точек всех звеньев механизма или системы механизмов повторяются, называют кинематическим циклом.
Период повторяющегося изменения мощности действующих сил и моментов сил называют энергетическим циклом.
Период повторяющейся совокупности операций технологической машины, в течение которого заканчивается изготовление детали или изделия, называют рабочим циклом.
Изображение согласованности перемещений исполнительных звеньев механизма и состояния элементов управления в зависимости от времени называют графиком цикличности, или циклограммой. Используются также изображения, поясняющие взаимодействие и связи между отдельными механизмами и элементами управления. К ним относятся схемы процесса работы, мнемонические, структурные и функциональные схемы, диаграммы и циклограммы.
На основе этого анализа определяют время отдельных интервалов движения (рабочих и нерабочих перемещений, выстоев и т.п.), оценивают возможности совмещения технологических и транспортных операций, сокращения времени некоторых операций, совмещения операций друг с другом или разбивки операций на менее продолжительные переходы с целью уплотнить циклограмму, т.е. уменьшить время рабочего цикла и повысить производительность технологических машин.
В пределах каждого цикла различают такты или фазы, которые позволяют выделять основное состояние механизма или машины. Например, можно выделить такты движения и такты покоя исполнительных звеньев, такты впуска, сжатия, расширения рабочей смеси и выпуска отработанных газов в четырехтактном карбюраторном двигателем внутреннего сгорания (ДВС), такт продувки и сжатия и такт рабочего хода и выпуска в двухтактном дизеле. В течение такта движения состояние ни одного из исполнительных механизмов и устройств не изменяется, т.е. состояние движения звеньев либо сохраняется, либо отсутствует.
110