
книги / Принципы технологии основного органического и нефтехимического синтеза.-1
.pdfветственно движущей силы процесса Ас в реакторах смешения, по сравнению с реакторами вытеснения, тем больше, чем выше конверсия реагентов и порядок реакции. Следовательно, при прочих равных условиях для проведения процесса и достижения заданной конверсии в реакторах смешения требуется большая продолжительность процесса.
Кроме того, важное значение имеют энергетические затраты при осуществ лении соответствующего процесса, которые для реакторов полного смешения могут быть в несколько раз выше, чем для реакторов полного вытеснения. Вме сте с тем реактор полного смешения, в котором во всех точках наблюдаются по стоянные концентрации и температуры, легче автоматизировать, чем реактор полного вытеснения. Более того, при наличии в реакторах режимов, близких к полному вытеснению, трудно подводить и отводить тепло, а при наличии интен сивного перемешивания условия передачи тепла улучшаются. Поэтому не слу чайно в аппаратах со взвешенным слоем катализатора, которые приближаются к реакторам полного смешения, отвод тепла при экзотермических реакциях осу ществляется проще, чем в трубчатых аппаратах. Однако в аппаратах с псевдо ожиженным слоем катализатора наблюдается его сильное истирание и унос в виде пыли.
Как было указано ранее, создание технологий для безотходных производств в значительной степени зависит от правильной организации подсистемы реак ционного процесса. При этом основная задача заключается в достижении не только максимальной конверсии сырья, но и селективности процесса. Достиже ние необходимых конверсии и селективности процесса зависит не только от ор ганизации процесса (теплообмена, переноса массы, гидродинамики и т.д.), но и главным образом от выбора каталитической системы. Типы каталитических систем были рассмотрены ранее. Теперь рассмотрим характеристики катализа торов, которые необходимо учитывать при их выборе.
К основным характеристикам катализаторов можно отнести следующие:
S специфичность, выражающуюся втом, что определенный тип катализато ров применяют для осуществления конкретных процессов (гидрирование, де гидрирование, окисление и др.);
■S избирательность, или селективность, т.е. способность ускорять реакцию (реакции), по которой получается целевой продукт;
S активность, которая определяется количеством целевого продукта, полу чаемого с единицы массы или объема катализатора в единицу времени.
Наиболее важной характеристикой катализаторов является их активность, которая зависит от:
S температуры (или интервала температур). Для каждого катализатора су ществует оптимальный температурный режим, при котором достигается его максимальная активность. При более низких температурах активность катали затора будет мала, а при более высоких — усиливается протекание побочных ре акций и происходит дезактивация катализатора. Чем активнее катализатор, тем ниже его оптимальный температурный режим;
S давления, определяющего концентрацию реагирующих веществ в реакци онном объеме (при жидкофазном катализе) или на поверхности катализатора (при гетерогенном катанизе);
S размера частиц катализатора, определяющих поверхность контакта между реагентами и катализатором. Уменьшение размера частиц катализатора снижает
2515 |
81 |
его диффузионное и тепловое сопротивление и, следовательно, увеличивает ак тивность;
S содержания примесей в сырье, которые могут вызывать частичную или полную дезактивацию (отравление) катализатора;
S способа приготовления катализатора, его активации, носителей и др. Наиболее эффективно катализаторы применяются для химических процес
сов, протекающих в кинетической области.
Так как значительное число промышленных процессов основного органиче ского и нефтехимического синтеза протекает в гетерофазных системах, особен но часто в системах газ—жидкость или жидкость—жидкость, то для протекания химических реакций необходимо обеспечить межфазный перенос вещества. При этом в зависимости от относительных скоростей массопередачи и химиче ской реакции процесс может протекать в различных областях: кинетической, когда химическая реакция идет много медленнее процесса массопереноса; диф фузионной, в которой самым медленным является процесс переноса вещества; переходной области, характеризующейся сравнимыми скоростями химической реакции и массопереноса.
Следует также учитывать, что реакция может протекать как в одной, так и в нескольких фазах. Поэтому возникает задача выявления определяющей или ли митирующей стадии процесса. В зависимости от скорости реакции и массопере носа можно выделить четыре основных случая протекания процессов.
Первый случай характеризуется медленной реакцией. Скорость процесса ли митируется скоростью химических превращений, так как концентрации в фазах быстро выравниваются за счет диффузии. Следовательно, процесс протекает во внутренней кинетической области. Для увеличения скорости процесса необходи мо увеличивать как объем фазы, так и температуру. В этом случае особенно ве лика роль катализатора.
Второй случай характеризуется быстрой реакцией. Скорость процесса лими тируется скоростью диффузии реагентов из одной фазы в другую (например, газа в жидкость) и вовнутрь катализатора. Следовательно, процесс протекает во внутренней диффузионной области. Для ускорения процесса необходимо увели чить диспергирование за счет более интенсивной турбулизации (перемешива ния) системы.
Третий случай определяется очень быстрой реакцией, протекающей на по верхности раздела фаз при осуществлении, например, процесса газ—жидкость. Следовательно, процесс лимитируется самой химической реакцией, протекаю щей на внешней поверхности зерна катализатора, что возможно, если ее ско рость значительно превосходит скорость внутренней диффузии, но значительно меньше скорости внешней диффузии. В этом случае процесс протекает во внеш ней кинетической области.
Четвертый случай характеризуется плохим перемешиванием в дисперсной фазе. Следовательно, скорость процесса определяется скоростью диффузии реагентов из потока к внешней поверхности зерна катализатора или, наоборот, скоростью диффузии продуктов от катализатора в поток. Подобный гетероген но-каталитический процесс протекает главным образом во внешней диффузион ной области. Для увеличения общей скорости процесса необходимо увеличивать поверхность раздела фаз.
Для гетерогенных процессов наиболее характерно протекание вдиффузион ной области. Однако применение современных интенсивных приемов турбули-
82
зации потоков и развития поверхности соприкосновения фаз позволяет пере вести процесс из диффузионной области в кинетическую. Кроме того, при по вышении температуры гетерогенный процесс может перейти из кинетической области во внешнедиффузионную.
Таким образом, для достижения необходимых результатов любого химиче ского процесса требуется располагать технологическими способами ведения этого процесса. Для этого нужно: правильно выбирать вариант осуществления процесса (последовательный или параллельный, периодический, непрерывный или полунепрерывный); управлять рабочими концентрациями; управлять тем пературными режимами; создавать развитую поверхность контакта гетероген ных фаз; поддерживать активность катализатора.
Организация периодических, полупериодических, сменно-циклических и непрерывных процессов была рассмотрена ранее.
Что касается управления рабочими концентрациями, то на практике для этой цели используют следующие способы: рециркуляция непревращенных реагентов; рециркуляция одного из реагентов (или самого продукта реакции); многоточечный подвод исходных веществ в один реактор или вразные реакторы каскада; секционирование реакционного объема аппарата.
Рециркуляция непрореагировавших исходных веществ позволяет не только изменять концентрации реагентов в реакторе, но и более полно использовать сырье. Рециркуляция одного из реагентов (обычно менее реакционноспособно го) дает возможность достигнуть большей конверсии и селективности химичес кого процесса. В ряде случаев за счет такой рециркуляции удается регулировать (иногда тормозить) некоторые высокоэкзотермические процессы.
Подвод же реагентов вразные точки реактора или вразные аппараты каскада способствует не только регулированию скорости химического процесса, а сле довательно, и скорости выделения тепла при протекании реакций, но и повы шению селективности процесса. Как правило, в разные точки подается наибо лее реакционноспособный компонент. Секционирование приводит к увеличе нию средней движущей силы процесса за счет снижения продольного переме шивания и поэтому находит наибольшее применение в аппаратах смешения. Секционирование сможетбыть выполнено в одном аппарате путем расчленения его на отдельные составные части, последовательно или параллельно соединен ные между собой, либо путем разделения одного реакторного устройства на ряд самостоятельных реакторов, соединенных последовательно, т.е. на каскад реак торов меньшего объема.
Движение реагентов в секционированном аппарате может быть построено как по принципу прямотока, так и по принципу полного или ступенчатого про тивотока, который чаше всего применяют в гетерогенных системах, например газ — твердое тело.
Как уже отмечалось, в зависимости от способа подвода или отвода тепла в ре акционном устройстве тепловой режим может быть изотермическим, адиабати ческим или политермическим.
Управление температурным режимом осуществляют двумя способами: не прерывным и ступенчатым. Для непрерывного отвода или подвода тепла реак тор должен иметь поверхность теплообмена, расположенную в зоне реакции. С целью ступенчатого теплообмена поверхность теплообмена размещается вне зоны реакции, т.е. выносится в отдельную часть реактора или вообще выносится из него. При этом тепло может отводиться как при подаче теплоносителя в теп
6* |
S3 |
лообменное устройство, так и за счет испарения части сырья, продуктов реак ции (в случае жидкофазного процесса), а также за счет подачи захоложенного сырья. Подвод тепла может осуществляться при подаче теплоносителя в тепло обменное устройство или в реакционное устройство. Следовательно, в качестве теплоносителей могут быть использованы сырье и продукты реакции, традици онные теплоносители, катализаторный раствор и др. В некоторых случаях тре буется сочетать непрерывный теплообмен со ступенчатым отводом или подво дом тепла.
Методы управления температурными режимами процессов необходимо рас сматривать во взаимосвязи с управлением рабочими концентрациями. Действи тельно, количество выделяемого или поглощаемого тепла в значительной степе ни зависит от скорости реакции, которая в свою очередь определяется концен трацией реагентов. Следовательно, регулировать рабочие температуры можно, изменяя концентрации реагентов. Вместе с тем температурный режим в значи тельной степени определяет концентрации реагентов в реакторе.
Для гетерогенных процессов большое значение имеет создание развитой по верхности контакта фаз. Причем в таких процессах скорость подвода и отвода как реагентов и продуктов реакций, так и тепла определяется размером поверх ности взаимодействующих фаз. Увеличить эту поверхность можно следующими методами: эмульгированием (в случае несмешивающихся жидкостей), распыле нием систем газ—жидкость, барботажем, созданием пленки, созданием движу щегося, кипящего или суспендированного слоя, а также измельчением твердых частиц для процессов с твердой фазой.
Для каталитических процессов самое большое значение имеет поддержание активности катализатора. Она может поддерживаться на должном уровне час тичной сменой отработанного катализатора, регенерацией катализатора в са мом реакторе или вне его, циркуляцией катализатора с его регенерацией и дру гими способами.
3.3.КЛАССИФИКАЦИЯ РЕАКТОРНЫХ УСТРОЙСТВ
Вреакторных устройствах при проведении собственно химического превра щения протекают различные физические процессы (гидродинамические, теп ловые, диффузионные и др.), с помощью которых создаются необходимые усло вия.
Для осуществления физических процессов в реакторных устройствах ис пользуются различные конструктивные элементы (мешалки, контактные уст ройства, теплообменники и др.). Так как сочетаний этих элементов и реакцион ных процессов может быть много, то и количество реакторных устройств также значительно.
Для реакторов существуют общие принципы, на основе которых можно най ти связь между конструкцией реакторного устройства и основными закономер ностями химического процесса, в них протекающего.
Как процессы, протекающие в реакторных устройствах, так и сами реактор ные устройства можно классифицировать по следующим признакам: режиму работы (периодические или непрерывные), гидродинамическим и тепловым ре жимам, а также физическим свойствам реагентов и продуктов реакций.
Выбор того или иного типа реакторного устройства обусловливается требуе мой селективностью химических превращений исходных веществ, а также про
84
изводительностью по целевому продукту (продуктам). Реакторное устройство должно также удовлетворять целому ряду требований, позволяющих эффектив но проводить химические процессы. К таким требованиям относятся:
•возможность размещения в реакторе необходимого количества катализа тора максимальной активности;
•создание требуемой поверхности контакта взаимодействующих реагентов
икатализатора, а также отдельных фаз;
•обеспечение необходимого гидродинамического режима движения реа гентов и фаз;
•обеспечение необходимого теплообмена при подводе или отводе тепла;
•наличие необходимого реакционного объема;
•поддержание необходимого режима процесса и др.
Реакторные устройства должны обеспечивать оптимальную скорость реак ций. Кроме того, выбор конструктивного типа реактора зависит от условий про ведения процессов и свойств участвующих в них веществ.
К важнейшим факторам, определяющим устройство реакторного аппарата, можно отнести:
• режим работы (периодический, непрерывный или полунепрерывный);
• температуру и давление, при которых протекают процессы;
• физические и химические свойства исходных веществ и продуктов реак ций;
• агрегатное состояние исходных веществ и продуктов реакций;
• теплоту реакций и процесса в целом, а также скорость подвода (отвода) те
пла; |
|
• способы |
интенсивного перемешивания реагентов; |
• способы |
подвода реагентов и отвода продуктов реакций; |
• способ регенерации катализатора или его замены.
Все реакторы, применяемые в отрасли основного органического и нефтехи мического синтеза, могут быть отнесены ктому или иному типу взависимости от:
• состояния реагентов (газ, жидкость, твердое тело, газ—жидкость, жид кость-жидкость, газ—твердое тело, жидкость—твердое тело);
• состояния катализатора: твердый (в стационарном состоянии, в псевдо
ожиженном состоянии, в диспергированном |
состоянии), |
жидкий; |
• расположения поверхности теплообмена |
(внешнее, |
внутреннее); |
• способа отвода тепла (через поверхность теплообмена, за счет испарения реагентов или продуктов реакций, за счет подачи холодных реагентов);
•способа диспергирования газа, жидкости и твердых частиц (реагентов и ка тализатора);
•способа развития поверхности контакта фаз.
Рассмотренные факторы в значительной степени определяют конструкции вспомогательных устройств (перемешивающие устройства, теплообменные уст ройства и т.д.).
По конструкции реакторные устройства могут быть разделены на: Преакторы типа реакционной камеры;
2)реакторы типа колонны;
3)реакторы типа теплообменника;
4)реакторы типа печи.
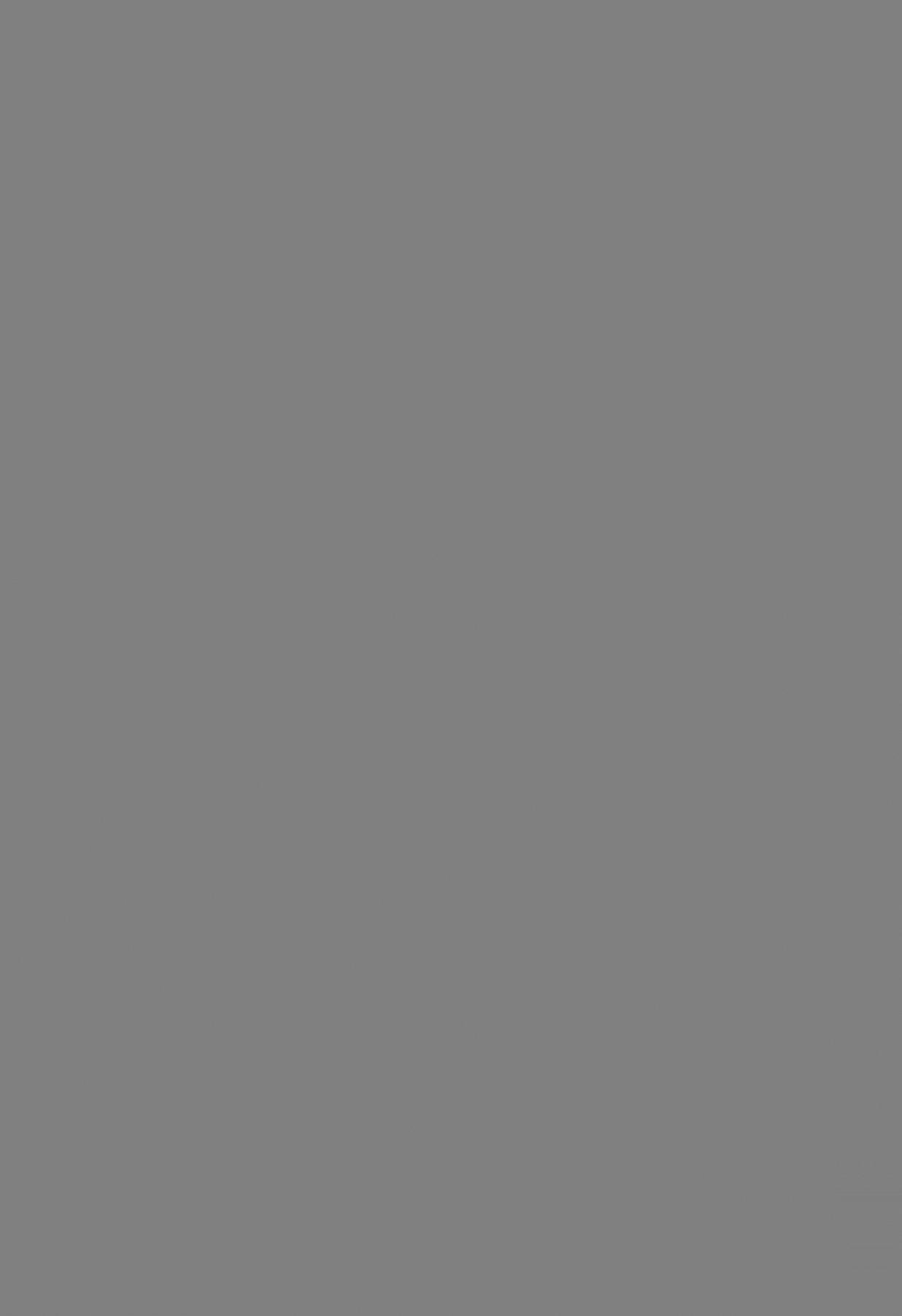
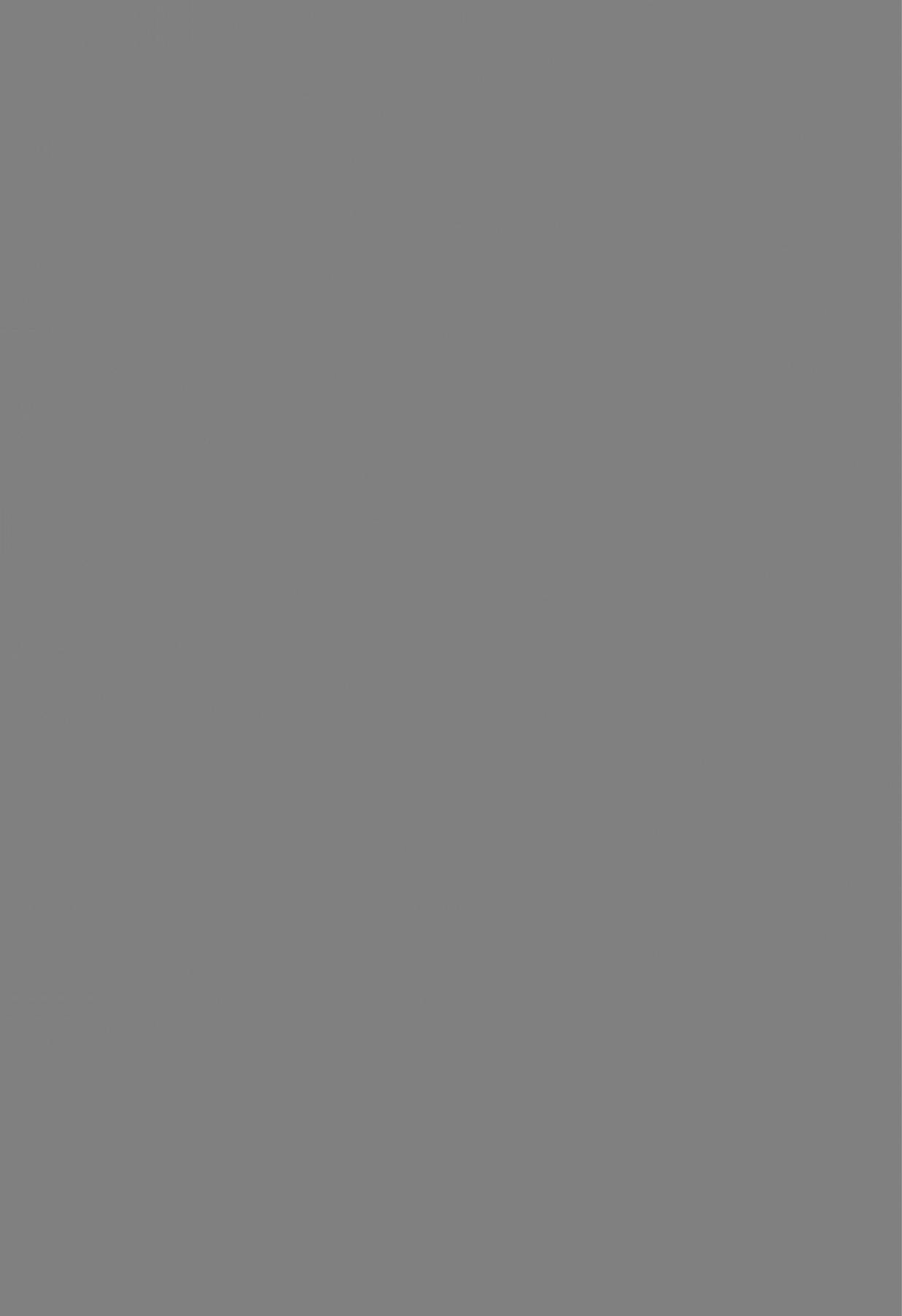
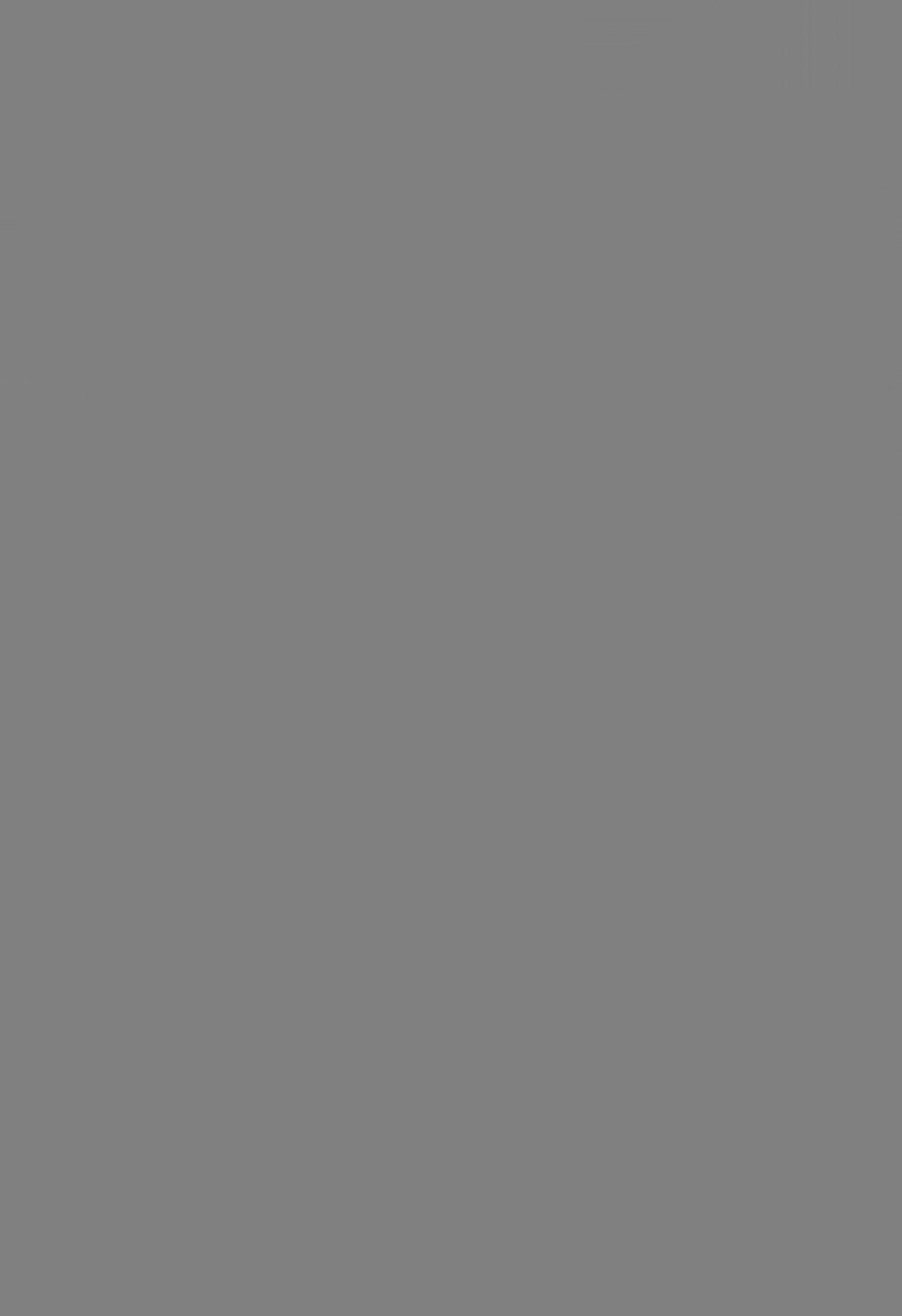
Т а б л и ц а 3.2. Классификация реакторов по конструктивным элементам
Тип реак |
Конструкци |
Гидродинами |
Агрегат |
Форма теплообмена и на |
Пример химиче |
||||
тора |
онная схема |
ческий режим |
ное со |
личие |
поверхности |
тепло |
ского процесса |
||
|
реактора |
|
|
стояние |
|
обмена |
|
|
|
|
|
|
|
|
без по |
с на |
с внут |
|
|
|
|
|
|
|
верхно |
ружной |
ренней |
|
|
|
|
|
|
|
сти те |
поверх |
поверх |
|
|
|
|
|
|
|
плооб |
ностью |
ностью |
|
|
|
|
|
|
|
мена |
|
|
|
|
Трубча |
Рис. 3.11, |
а |
Полное вы |
Г |
— |
+ |
— |
Синтез |
ви |
тый |
|
|
теснение |
|
|
|
|
нилацетата |
|
|
Рис. 3.11, |
б |
То же |
Ж |
— |
+ |
— |
Алкилирова |
|
|
|
|
|
|
|
|
|
ние бензола |
|
|
Рис. 3.11, |
в |
» |
Ж -Ж |
|
+ |
1 1 |
Получение |
|
|
|
|
|
|
|
|
|
диметилдиокса- |
|
|
|
|
|
|
|
|
|
на |
|
Колон Рис. 3.12, |
а |
Полное вы |
Г -Ж |
— |
ный |
|
теснение |
|
|
Рис. 3.12, |
б |
То же |
Г -Ж |
+ |
— |
+ |
Окисление уг |
|
|
леводородов |
—— Нейтрализа
ция НС1
Рис. 3.12, в |
Полное вы г - ж |
+ |
Окисление |
|
|
теснение (газ), |
|
твердых пара |
|
|
полное |
сме |
|
финов |
|
шение |
(жид |
|
|
|
|
кость) |
|
|
|
|
|
|
Рис. 3.12, |
г |
Полное |
вы |
г - ж |
+ |
|
— |
Окисление |
|
|
теснение |
|
|
|
|
• |
ацетальдегида |
|
|
|
|
|
|
|
||
Рис. 3.12, |
д |
Полное |
вы Г - Г - Т |
|
|
+ |
Синтез акри |
|
|
|
теснение (газ), |
|
|
|
|
лонитрила |
|
|
|
полное |
сме |
|
|
|
|
|
|
|
шение (твер |
|
|
|
|
|
|
|
|
дая фаза) |
|
|
|
|
|
|
Рис. 3.12, |
е |
То же |
|
г - т |
+ |
■■■ |
|
Хлорирова |
|
|
|
|
|
|
|
|
ние углеводоро |
|
|
|
|
|
|
|
|
дов |
Рис. 3.12, |
ж |
» |
|
г - т |
— |
+ |
— |
Получение |
|
|
|
|
|
|
|
|
оксида этилена |
Рис. 3.12, |
з |
Полное |
вы |
Г - Г - Т |
|
+ |
|
Фторирова |
|
|
теснение |
|
|
|
|
|
ние углеводоро |
|
|
|
|
|
|
|
|
дов |
Шахт |
Рис. 3.13, |
а |
То же |
г - т |
ный |
|
|
|
|
Реакци |
Рис. 3.13, |
б |
Полное |
ж |
онные ка |
|
|
смешение |
|
меры с пе |
|
|
|
|
ремешива |
|
|
|
|
нием |
|
|
|
|
+ |
— |
— |
Дегидрирова |
|
|
|
ние этилбензола |
||
+ |
+ |
+ |
Гомогенный |
|
|
|
пиролиз |
жиров |
|
|
|
и |
масел, |
хлор |
|
|
бензола; |
полу |
|
|
|
чение |
винил |
|
|
|
хлорида |
из ди |
х л о р э т а н а
Окончание табл. 3.2
Тип реак |
Конструкци |
Гидродинами |
Агрегат |
Форма теплообмена и на |
Пример химиче |
||
тора |
онная схема |
ческий режим |
ное со |
личие* поверхности |
тепло |
скою процесса |
|
|
реактора |
|
стояние |
|
обмена |
|
|
|
|
|
|
без по |
с на |
с внут |
|
|
|
|
|
верхно |
ружной |
ренней |
|
|
|
|
|
сти те |
поверх |
поверх |
|
|
|
|
|
плооб |
ностью |
ностью |
|
|
|
|
|
мена |
|
|
|
Реакци |
Рис. 3.13, |
б |
Полное |
онные ка |
|
|
смешение |
меры с пе |
|
|
То же |
ремешива |
|
|
|
|
|
|
|
нием |
|
|
|
Печи |
Рис. 3.13, |
в |
Полное вы |
|
|
|
теснение |
Г - Ж |
+ |
+ |
+ |
Хлорирова |
|
|
|
|
ние этилена |
Ж - Ж |
+ |
+ |
+ |
Сульфирова |
|
|
|
|
ние бензола |
Г - Г |
— |
+ |
+ |
Пиролиз |
Т а б л и ц а 3.3. Классификация реакторов по фазовым состояниям реагентов и катализатора
Класс |
Фазовое |
Фазовое |
Вид катализатора |
Конструктивны й |
Пример |
химического |
процесса |
|||||
|
состояние |
состояние |
|
|
тип |
реактора |
|
|
|
|
||
|
реагентов |
катализа |
|
|
|
|
|
|
|
|
|
|
|
или среды |
тора |
|
|
|
|
|
|
|
|
|
|
1 |
Г' |
Т |
|
Труба |
или |
Контактный |
Синтез |
синильной |
кислоты, |
|||
|
|
|
|
сетка |
|
|
|
|
окислительное дегидрирование |
|||
|
|
|
|
|
|
|
|
|
спиртов |
|
|
|
|
Г |
Т |
|
Фильтрую |
Трубчатый |
Гидрирование ароматических |
||||||
|
|
|
|
щий или непод |
|
|
|
углеводородов |
и насыщенных |
|||
|
|
|
|
вижный |
слой |
|
|
|
альдегидов |
|
|
|
|
Г |
т |
|
Взвешенный |
Реакционная |
Хлорирование углеводородов |
||||||
|
|
|
|
слой |
|
камера |
|
|
|
|
|
|
|
Г |
т |
|
Движущийся |
То же |
|
Каталитический крекинг |
|||||
2 |
ж |
т |
|
Неподвиж |
Трубчатый |
Гидрирование |
|
|||||
|
|
|
|
ный слой |
|
|
|
|
|
|
|
|
|
ж |
т |
|
Взвешенный |
Реакционная |
Получение олефинов |
||||||
|
|
|
|
слой |
|
камера |
|
|
|
|
|
|
|
ж |
т |
|
Взвесь в жид |
Колонный |
Карбонилирование |
метанола |
|||||
|
|
|
|
кости |
|
|
|
|
в уксусную кислоту при высо |
|||
|
|
|
|
|
|
|
|
|
ком давлении |
|
|
|
|
ж |
т |
|
Равномерно |
Аппарат с ме |
Алкилирование бензола жид |
||||||
|
|
|
|
распределен |
шалкой |
|
кими олефинами |
|
||||
|
|
|
|
ные в жидкости |
|
|
|
|
|
|
|
|
|
|
|
|
частицы |
|
|
|
|
|
|
|
|
3 |
г - ж |
ж |
|
Взвесь в жид |
Колонный с |
Хлорирование бензола |
||||||
(4) |
|
(или |
Т) |
кости |
|
насадкой |
|
|
|
|
|
|
|
г - ж |
Ж |
|
Взвесь в жид |
Барботажная |
Окисление |
ацетальдегида в |
|||||
|
|
(или |
Т) |
кости |
|
колонна (барбо |
уксусную |
кислоту, гидратация |
||||
|
|
|
|
|
|
таж |
газа |
через |
ацетилена |
|
|
|
|
|
|
|
|
|
жидкость |
или |
|
|
|
|
|
|
|
|
|
|
|
взвесь твердого |
|
|
|
|
||
|
|
|
|
|
|
вещества) |
|
|
|
|
|
90