
книги / Управление качеством. Основы теории и практики
.pdfмогут быть кружки качества, созданные по типу комплексных групп. Подтверждением реальности такого подхода к организации кружков качества явился опыт их создания и работы на заводе «Электросила» вСанкт-Петербурге в период с 1983 по 1989 гг. а это время было созда но 104 группы, в работе которых участвовало около 900 человек. Эти группы создавались и использовались в основном для решения слож ных технических проблем. Полученный опыт работы комплексных групп показал их достаточную эффективность. С их помощью удалось решить ряд проблем, которые раньше не решались длительное время из-за разобщенности специалистов разного профиля и недостаточного стимулирования. К сожалению, в 90-х годах эта работа прервалась изза сокращения персонала.
Работа таких комплексных групп по анализу причин возникно вения проблем и разработке мероприятий по их предупреждению и профилактике возможных отказов перекликается с известным методом анализа причин и последствий отказов (FMEA).
3.2.4Метод анализа причин
ипоследствий отказов
(Failure Mode Effect Analyses — FMEA)
Этот метод направлен на предупреждение возможных отказов уже на этапе разработки и технологической подготовки производства. Здесь также как и в описанных выше комплексных группах, работа проводится единой FMEA-командой, организованной из высокок валифицированных опытных специалистов разных подразделений, способных на основе имеющегося опыта предвидеть возможные дефекты и разработать предупредительные и профилактические меры, необходимые для их предотвращения в будущем. Для этого им предоставляются рабочее время и удобное место работы. Работа проводится методом «мозгового штурма». При этом рассматриваются вопросы, относящиеся к конструкции, технологии и производству продукции.
Существо этого метода состоит в проведении количественной оценки возможных дефектов и выявлении наиболее опасных из них для последующего рассмотрения и принятия мер предупреждения [26].
Каждый дефект можно характеризовать тремя показателями (критериями):
>значимостью, измеряемой тяжестью последствий дефекта;
>частотой (вероятностью) появления дефекта;
>частотой (вероятностью) обнаружения дефекта или его причины еще на заводе.
Каждый из этих критериев оценивается в диапазоне от 1 до 10. Причем для первых двух зависимость оценки прямая: чем больше значимость и вероятность появления дефекта, тем выше оценка. Для третьего критерия зависимость обратная: большая вероятность обнару жения дефекта снижает оценку. Обобщенная оценка получается путем перемножения трех оценок: чем выше оценка, тем хуже дефект. Перед оценкой заранее устанавливается критическая граница такой оценки.
После образования команды и организации ее работы она состав ляет перечень потенциально возможных дефектов и для каждого из них определяются наиболее тяжелые последствия и причины появ ления, для каждой из которых должна быть выставлена экспертная количественная оценка частоты появления. Далее рассматривается технология изготовления с точки зрения возможности обнаружения предполагаемого дефекта или его причины и выставляется оценка по критерию обнаружения. После этогодля каждогодефекта определяется обобщенная оценка как произведение трех оценок по вышеназванным критериям. Эту обобщенную оценку называют приоритетным числом риска — ПЧР, которое сравнивается с ранее установленной критичес кой границей — ПЧРгр. Если для рассматриваемого предполагаемого дефекта ПЧР получилось больше ПЧРгр, то разработка мер предуп реждения продолжается. Разработка предложений по улучшению конструкции и/или технологии изготовления изделий с целью сни жения вероятности появления возможных отказов — основная работа команды, которая заканчивается, когда для возможных отказов все оценки ПЧР будут не выше ПЧРгр.
Для внедрения метода FMEA в практику работ (если будет принято такое решение) работникам предприятия, которые будут в этом учас твовать, необходимо пройти специальное обучение. Этот метод был включен в состав документов системы качества QS 9000 для автомоби лестроителей США и отмечен в главе 7 при рассмотрении отраслевых стандартов по системам качества.
3.2.5. Система тотального обслуживания
оборудования (Total Productive Maintenance — TPM)
В заголовке использован краткий перевод термина ТРМ, хотя одним из его определений служит «обслуживание оборудования, позволяющее обеспечить его наивысшую эффективность на про тяжении всего жизненного цикла с участием всего персонала». Эта система, возникшая по некоторым данным в США, а по другим — в Японии в 60-х годах прошлого века, предназначена для повышения эффективности производственной системы путем постоянной работы по поддержанию оборудования в работоспособном состоянии при участии всего производственного персонала. Это позволяет свести к минимуму риск непредвиденного и экстренного обслуживания обо рудования с остановкой процесса производства и особенно важно для предприятий, у которых состояние оборудования является одним из основных факторов эффективной работы предприятия.
Внедрение ТРМ предполагает расширение обязанностей рабочих по текущему обслуживанию своих станков и активизацию работы обслуживающего персонала для поддержания стабильности харак теристик оборудования. При этом время обслуживания включается рабочему в его сменное задание или является неотъемлемой частью производственного процесса. Как видим, это не совсем то, что мы привыкли понимать, проводя силами работников службы главного механика плановые ремонты и техническое обслуживание оборудо вания. Проблема внедрения ТРМ заключается в том, чтобы придать тотальныйхарактер этойработеу привлечь конструкторов, технологов, механиков и производственников, создать команду, которая смогла бы постоянно, как в кружке качества, решать проблему поддержания иулуч шения характеристик оборудования. Конструктора и технологи могут при этом, исходя из специфики производства, модернизировать или разрабатывать новое технологическое оборудование, которое также позволит повысить эффективность производственной системы.
Такой характер работ по обслуживанию оборудования не исключает того, что традиционно делалось и делается на наших предприятиях. Контроль состояния оборудования может осуществляться, например, путем проведения регулярных плановых проверок оборудования на технологическую точность, а также при проведении периодических
и сп ы та н и й вы пускаем ой п р о д у кц и и с целью ко н т р о л я ста би л ьности те хн о л о ги че ско го процесса (см . далее ф у н к ц и ю контроль). П олезно будет, наверное, использовать та кж е о п ы т пров ед ени я о ц е н к и те х н и ческого уровня производства и аттестации рабочих мест, п о результатам ко то р о й п р и н и м а л и сь меры по их р а ц и о н а л и за ц и и и л и создавались новы е места, отвечаю щ ие пр о гр е сси в ны м те х н и ч е с ки м и о р га н и за ц и о н н ы м р еш ениям . Ч то касается вовлечения персонала в а кти в н у ю работу на пред при яти и, то это особо отм ечено в стандартах И С О серии 9000 по управлению качеством и предусм атривает р еш ени е э то й п р о блемы путем п о о щ р е н и я но вовведений, о р га н и за ц и е й эф ф е кти вн о й гр уп п о в о й работы, при зн ани ем д о с ти ж е н и й р а б о тн и ко в и и х дол ж ны м вознаграж дением , и д р у ги м и мерами.
П о у тв е р ж д е н и ю спец и ал и стов [8 ], вн едрение Т Р М в п р а к т и к у работ на зарубеж ны х пред при яти ях позвол и л о п о в ы с и ть отдачу п р о извод стве нн ой систем ы и качество вы п уска е м о й п р о д у к ц и и , сни зи ть уровень брака и реклам ац ий и связанн ы х с н и м и потерь, повы сить кул ьтуру прои звод ства и о б щ и й уровень организационной культуры предприятия к а к одн ого из подходов, используем ы х в науке управления (см . вы ш е).
3.2.6. Экономное (бережливое) производство
В настоящ ее |
время м н о ги е п рои звод ител и |
о б р а щ а ю т |
вн и м а ни е |
на о р га н и за ц и ю |
э к о н о м н о го (б ереж л ивого) п |
р о и зв о д с тв |
а , которое |
обеспечивается при м ен ени ем комплекса средств, методов и подходов к управлению, среди которы х:
> разработка п р о гр а м м ы н е п р е р ы вн о го с о в е р ш е н с тв о в а н и я де ятельности ( кайдзэн), что является кл ю ч е в о й к о н ц е п ц и е й , которая дополняется м е то д и ко й «шесть сигм », н а п р а вл е н н о й на д остиж ени е «нуля деф ектов»;
> внедрение систем ы 5S:
Separate — удаление н е н у ж н ы х предм етов с раб очего м еста;
Sort — со ртиров ка, располож ение всех н у ж н ы х пр едм етов для лег к о го и безопасного доступа;
Sweep — убор ка рабочего места;
Standardize —составление стандартны х правил для удаления не н уж ны х и располож ения н у ж н ы х предметов и у б о р ки раб очего м еста;
Sustain — поддержка, закрепление деятельности в области 5S путем систематического проведения аудитов по графику;
>применение средств визуального контроля, например, — графика работ, который позволяет наблюдать за текущим состоянием дел и любыми отклонениями;
>использование приемов защиты от ошибок путем применения контроля качества как составной части любой операции, и оснащения оборудования средствами встроенного контроля с целью исключения попадания дефектной продукции на следующий этап производства;
>внедрение сбалансированного ритмичного производства, ког да изделие не попадает на следующий этап, пока не будет завершен текущий этап и не проведен контроль качества, а ритм (не цикл!) производства диктуется темпом продаж, что избавляет от запасов незавершенного производства;
>применение тянущей системы производства (системы вытяги вания), при которой изготовление продукции осуществляется только после получения заказа и предусматривает поставки материалов, деталей и готовой продукции точно в срок, благодаря чему доставка продукции заказчику идет в основном напрямую мимо склада, что также позволяет избавиться от ненужных запасов;
>обеспечение быстрой переналадки оборудования для удовлет ворения индивидуальных запросов заказчиков при серийном про изводстве продукции, что должно быть заложено в возможностях оборудования и осуществляться путем четкой организации работ при наличии и рациональном размещении необходимого инструмента и принадлежностей;
>использование системы тотального обслуживания оборудова ния — метода ТРМ;
>организация работы компании как сфокусированного предпри ятия, чтобы оно было направлено на производство определенного типа продукции с минимальными затратами и ограниченными ре сурсами;
>распространение экономного производства за пределы цеха, бла годаря чему оно не ограничивается рамками цеха, а распространяется надругие подразделения, в том числе для решения административных задач при работе в офисах.
Как видно из перечисленных элементов, для внедрения системы экономного производства потребуется соответствующее обучение
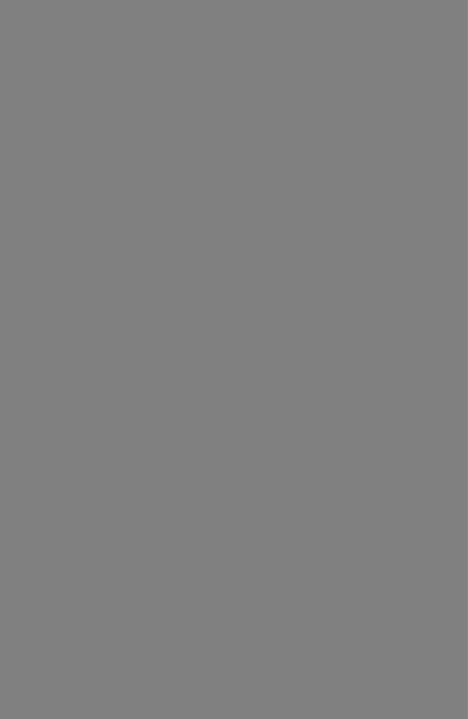
>Международная электротехническая комиссия (МЭК) —
в1906 году.
>Международная ассоциация национальных организаций по стандартизации (ИСА) — в 1926 году. Сейчас вместо ИСА, которая распалась во 2-ю мировую войну, действует Международная органи зация по стандартизации (ISO), основанная в 1947году (в российских стандартах почему-то обозначается как ИСО). Подробнее об ИСО сказано ниже при рассмотрении стандартов ИСО серии 9000.
ВРоссии начало стандартизации принято считать с указа Петра первого 1719 года в области кораблестроения «о судах нового маниру», чтобы делали суда по образцу. Современная же история стандар тизации в России началась с 1918 года—с принятия декрета Совета Народных Комиссаров о введении десятичной системы мер и весов. После этого, в 1922 году был создан комитет эталонов и стандар тов, а в 1925 году — Комитет по стандартизации при Совете Труда и Обороны, который положил начало истории Госстандарта России. В 1970 году этот комитет был преобразован в Государственный комитет стандартов Совета Министров СССР (Госстандарт СССР). В 1989 году Государственный комитет СССР по стандартам был преобразован в Государственный комитет СССР по управлению качеством продукции и стандартам. В 1991 г. Указом Президента Российской Федерации был образован Государственный комитет РСФСР по стандартизации, мет рологии и сертификации (Госстандарт России). В 2002 году был при нят Федеральный закон о техническом регулировании в Российской Федерации, в соответствии с которым в 2004 году на базе Госстандарта России была создана Федеральная служба, которая в том же году была преобразована в Федеральное агентство по техническому регулирова нию и метрологии (Ростехрегулирование).
В управлении качеством, кроме стандартов ИСО 9000, наглядны ми примерами использования стандартизации служит применение Нового и Глобального подходов в Европейском союзе и принципов Технического регулирования в Российской Федерации.
3.2.8. Н о в ы й и Глобальный п о д х о д ы
в Европейском Союзе
Развитие экономических связей и создание единого европейского рынка потребовало создать благоприятные условия для свободного
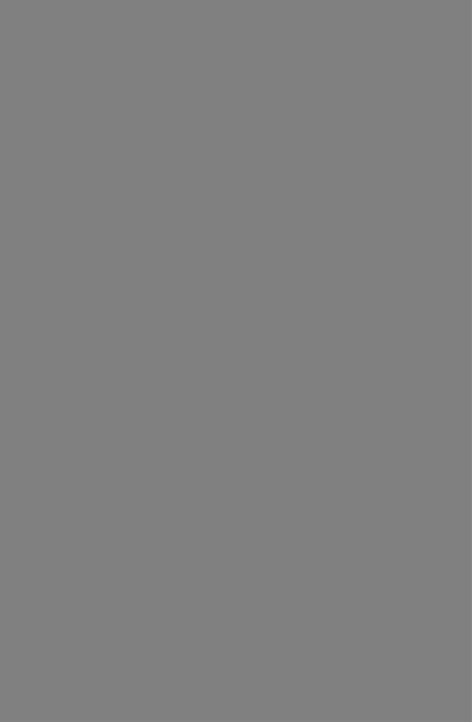
вгармонизированных с директивами стандартах, добровольных к применению. По оценкам специалистов европейские директивы рас пространяются на 25—30% всей выпускаемой в ЕС продукции.
Глобальный подход предусматривает процедуры оценки соответствия продукции установленным требованиям. В зависимости от требований директивы эти процедуры осуществляют изготовитель и орган по серти фикации или испытательная лаборатория, уполномоченные на проведе ние работ по конкретной директиве. Но сами лаборатории и органы по сертификации также должны соответствовать определенному уровню. Для введения единых критериев оценки компетентности лабораторий
иорганов по сертификации была создана Европейская организация по испытаниям и сертификации и разработана серия европейских стандар тов (Евро-Нормы) EN 45000. Эти стандарты стали единой нормативной базой для испытательных лабораторий и органов по аккредитации и сертификации, что обеспечило возможность взаимного признания сер тификатов, выданных лабораториями и сертификационными органами
вразных странах ЕС. Серия EN 45000 включает в себя стандарты:
EN 45001-89. Лаборатории испытательные. Общие критерии фун кционирования.
EN 45002-89. Органы по аккредитации лабораторий. Общие кри терии. EN 45003-89. Лаборатории испытательные. Общие критерии оценки.
EN 45011-89. Органы по сертификации продукции. Общие кри терии.
EN 45012-89. Органы по сертификации систем качества. Общие критерии.
EN 45013-89. Органы по аттестации персонала. Общие критерии. EN 45014-89. Заявления поставщика о соответствии. Общие кри
терии.
По результатам оценки соответствия продукции требованиям директивы, изготовителем принимается декларация о соответствии,
вкоторой приводится доказательная база соответствия продукции.
Взависимости от требований директивы доказательная база может ограничиваться возможностями изготовителя или должна предус матривать участие лаборатории и сертификационного органа. При положительном результате оценки соответствия продукции она мар кируется знаком СЕ.
Процедуры оценки соответствия продукции требованиям директи вы состоят из модулей, которые распространяются на проектирование, изготовление продукции, или на то и другое. При оценке соответствия продукции по директивам в ряде случаев (модулей) предусматривается оценка соответствия системы качества поставщика стандартам ИСО 9000, которая проводится специалистами по оценке продукции и за канчивается составлением протокола оценки системы качества, а не выдачей сертификатасоответствия. Тем не менее, это дает возможность заказчикам убедиться в наличии у поставщиков системы в работе по качеству (системы качества), которая обеспечивает стабильность ка чества продукции, отвечает современным требованиям и служит для заказчиков дополнительной гарантией качества. В этом случае для поставщиков создаются более благоприятные условия для заключения контрактов и реализации своей продукции на рынках сбыта.
Новый и Глобальный подходы оправдали себя на практике и пос лужили ориентиром для проведения реформы технического регули рования в Российской Федерации.
3.2.9. Техническое регулирование
вРоссийской Федерации
Всоответствии с реформированием технического регулирования, осуществляемым в России с 2003 года, введены новые правила уста новления требований к продукции и подтверждения соответствия этим требованиям, новый порядок аккредитации и Государственного надзора за соблюдением обязательных требований к продукции. Все это оказывает непосредственное влияние на управление качеством продукции и услуг.
До реформы технического регулирования требования к продукции в бывшем СССР устанавливались в государственных стандартах, на обложках которых вверху было напечатано: несоблюдение требований стандарта преследуется по закону. Это означало, что все требования стандартов были обязательны для исполнения и контролировались государством, независимо от того, влияют ли они на безопасность продукции, или устанавливают ориентиры потребительских свойств, не влияющих на безопасность.