
книги / Нефтяной углерод
..pdfверхность и ее активность настолько возрастают, что процесс из мельчения становится обратимым. При дальнейшем увеличении степени дисперсности заметным становится агрегирование частиц н налипание их на мелющие тела и футеровку мельницы. Поэтому тонкий помол осуществляют либо с применением ПАВ, либо в жидкой среде (мокрый помол).
Механическая прочность, электрические, теплофизические свой ства, реакционная способность и другие показатели качества электродной продукции и вообще углеродонаполненных систем в значительной мере зависят от степени анизометрии структуры неф тяного углерода, формы частиц, степени дробления, соотношения фракций частиц, входящих в систему.
Удельная поверхность, физико-химическая природа — поверх ностная активность наполнителя и связующего — являются важ нейшими факторами, влияющими на прочность структуры напол ненных систем. Только при определенном соотношении Уд.ф/Уд.с наполненная система имеет максимальное число контактов напол нителя со связующим, обеспечивающее максимальную прочность структуры.
На прочность структуры наполненной системы оказывает влия ние форма частиц, которая, в свою очередь, зависит от молеку лярной структуры сырья коксования, от природы надмолекулярных структур и их упорядоченности, качества сырого и прокаленного коксов, типа размольного агрегата. При дроблении сырых коксов структура их мало влияет на форму образующихся частиц.
Как «мягкие» (легкодробящиеся), так и «твердые» (труднодробящиеся) сырые коксы, которые состоят из мелких кристалли тов, имеющих низкую степень упорядоченности, обладают различ ной степенью изотропности механических свойств, которая способ ствует получению при дроблении зерен неодинаковой изометричной формы. Различная склонность этих коксов к упорядочению в процессе прокаливания обусловливает получение пластинчатых (волокнистых) зерен при дроблении «мягких» коксов и зерен сфе роидальной (точечной) формы при измельчении «твердых» коксов. При наличии двух структур (волокнистой и точечной) частицы кокса разру шаются преимущественно по участкам волокни стой структуры. При прессовании электродной продукции плоские частицы кокса ориентируют ся (рис. 23) вдоль направления давления, что вы зывает увеличение анизотропии структуры в электродной массе и улучшает качество готовых электродов.
Поскольку прокаленные коксы, получаемые из сырья различной молекулярной структуры, су-
Рнс. 23. Расположение плоских частиц кокса при прессовании.
щественно различаются по степени прочности и упорядоченности кристаллитов, выбирают разные размольные агрегаты и подбирают соответствующие режимы их работы. Обычно прокаленный нефтя ной кокс дробят до получения частиц размером 8— 10 мм в вал ковых дробилках или на шаровых мельницах с периферийной вы грузкой. Фракции тонкого помола, от гранулометрического состава которых в значительной мере зависит качество электродной про дукции, на отечественных электродных заводах получают в труб чатых шаровых мельницах, работающих на слив, и с пневмоудале нием; одновременно происходит воздушная классификация по мола.
Фракции кокса, измельченного до необходимых размеров, хра нят в бункерах; оттуда они поступают на дозирование и смешение со связующим веществом (пеком). На отечественных алюминие вых заводах обычно применяют наполнитель следующего состава:
Размер, мм |
Содержание, % |
|
Размер, мм |
Содержание, % |
> 6 |
Не более 3 |
От |
1 до 0,15 |
По разности |
От б до 1 |
38±3 |
От |
0,15 до 0 |
40± 3 |
в том числе > 4 |
12±4 |
|
в том числе 0,075 |
30±3 |
В дальнейшем в электродных композициях намечается тенден ция к увеличению размеров частиц во фракциях крупного помола.
ДОЗИРОВАНИЕ КОМПОНЕНТОВ И ФОРМИРОВАНИЕ УГЛЕРОДОНАПОЛНЕННОЙ СИСТЕМЫ
УНС для получения электродных масс
В зависимости от вида изготавливаемой продукции из соответст вующего бункера (по дозировочному регламенту) отвешивают с помощью дозировочных устройств (автоматические весы, электровесовая тележка и др.) необходимое количество фракций крупного и тонкого помола. Наилучшие результаты получаются при автома
тическом дозировании. Отвешенные фракции коксовых порошков подают в машину для смешивания с расплавленным связующим до получения однородной тестообразной массы, обладающей соответ ствующими структурно-пластическими свойствами. Связующим чаще всего служит среднетемпературный каменноугольный пек. Его расплавляют до такого состояния, чтобы он имел минимальную вязкость и обволакивал зерна наполнителя тонким слоем, запол няя наружные поры в теле частичек (формируется адсорбционный слой). Ориентировочно за температуру смешения принимают удво енную температуру размягчения применяемого пека. Это объяс няется неодинаковым структурно-реологическим состоянием пеков при их температуре размягчения и удвоенной температуре размяг чения. Так, вязкость среднетемпературного магнитогорского пека (температура размягчения 65 °С) существенно снижается в интер вале 65—110°С, и он представляет собой пластично-текучее тело, обладающее высокой адгезией к углероду (по Бингаму — Шведо
ву). В интервале 130—140 °С и выше вязкость изменяется менее резко. Лучше всего пек рекомендуется использовать в качестве связующего при температуре, при которой он переходит из ассо циированного состояния в близкое к состоянию ньютоновской жидкости.
Очень важно определить оптимальный расход связующего, не обходимый для получения электродной массы достаточной механи ческой прочности. Наилучшие результаты достигаются в процессе спекания электродной массы при небольшом недостатке связующе го. Это обеспечивает хороший контакт между частицами, но кана лы между ними, необходимые для выхода летучих веществ из внутренних слоев массы в газовую фазу, сохраняются. При чрез мерном недостатке связующего связи между частицами ослабляют ся, они плохо спекаются, и механическая прочность изделия умень шается. Такие же результаты получаются при избытке связующего в электродной массе. Бурно выделяющиеся летучие вещества на рушают скелет заготовки — они вспучивают его и искривляют.
В общем случае расход пека (П) для достижения нормальных пластических свойств анодной массы (показатель пластичности /Сд=60—82%) слагается из двух составляющих:
|
|
П = Ппор -Ь Пад |
|
где Ппор — расход |
пека |
на заполнение пор в зернах |
и межзернового простран |
ства; Пад — расход |
пека |
на создание жидкого слоя |
на поверхности зерна, при |
дающего массе нормальные пластические свойства. |
|
При изготовлении анодной массы из малосернистого прокален ного нефтяного кокса расход среднетемпературного пека на запол нение пор Ппор не превышает 3—5%. Это согласуется с мнением, изложенным в работе '[174], в соответствии с которым вязкая жид кость типа пека существенно не проникает во внутренние поры прокаленного нефтяного кокса. Таким образом, основая масса свя зующего затрачивается на создание тонкого слоя пека вокруг зерен наполнителя (Пад). Обычно расход связующего для изготов ления анодной массы из шихты прокаленного малосернистого неф тяного кокса составляет 30—32% композиции. При прессовании заготовок количество связующего снижается на 5— 10%.
Электродную шихту смешивают со связующим в смесителях пе риодического и непрерывного действия, стараясь достичь адсорб ционного равновесия. На отечественных заводах чаще всего приме няют смесители периодического действия полезной емкостью 2000 л с двумя Z-образными лопастями и нижней выгрузкой. Смесители обогревают мятым паром (0,6 МПа). Поэтому температура в них не превышает 150°С. Затем электродную массу выгружают в фор мы, и после того как она остынет ее либо направляют в электро лизные цехи, либо прессуют.
Углеродистую анодную массу (для самообжигающихся анодов) выпускают (в зависимости от содержания золы и серы) нулевого и первого сорта (МРТУ 48-13-24—66):
|
|
|
|
|
Нулевой |
Первый |
|
|
|
|
|
сорт |
сорт |
|
|
|
|
|
АМ-0 |
АМ-1 |
Содержание, |
%» не более |
|
|
|||
золы |
|
|
, |
0 , 5 |
1 ,0 |
|
с е р ы ..................................... |
анодной |
массы |
0 ,9 |
1 ,4 |
||
Пластичность |
|
|
||||
для электролизеров, |
%: |
|
|
|||
с |
верхним |
токоподводом |
66 — 68 |
60— 86 |
||
с |
боковым |
токоподводом |
6 0 — 82 |
54— 88 |
Несколько иная технология применяется при изготовлении уг леродонаполненных систем, используемых для брикетирования. В качестве наполнителя можно применять [27] нефтяной кокс, раздробленный до частиц размером менее 6 мм, а в качестве свя зующего— дополнительно термообработанные нефтяные остатки, имеющие температуру размягчения по КиШ 70—90 °С и коксуе мость по Конрадсону около 38—40%. Наибольшая прочность бри кетов достигается при содержании в углеродонаполненной системе связующего 12%.
Углеродонаполненные системы из нефтяных коксов и связующего можно изготовлять на типовом оборудовании углебрикетных фабрик. Кокс смешивают с пеком в горизонтальных шнековых смесителях. Необходимое давление прессо вания 20—25 МПа. Коксобрнкеты (размером 60x50x35 мм и массой около80 г) охлаждают на конвейерной ленте и затем направляют на хранение и перера ботку.
ОСОБЕННОСТИ ФОРМИРОВАНИЯ УГЛЕРОДОНАПОЛНЕННОЙ СИСТЕМЫ — РЕЗИНОВОЙ СМЕСИ
Важная особенность формирования резиновых смесей — многокомпонеитность си стемы, в связи с чем необходимо повышенное внимание к качеству смешиваемых ингредиентов (вулканизующих агентов, ускорителей, пластификаторов, пассиваторов, наполнителя и др.) и их дозирование. Наилучшие условия для смешения компонентов резиновой смеси достигаются при диспергировании наполнителей до коллоидального состояния на агрегатах для измельчения и введения ПАВ. Тем пература смешения зависит от свойств каучуков; для основных видов натураль ных и синтетических каучуков она составляет 90—100°С. Для каучуков, менее склонных к преждевременной вулканизации (например, бутилкаучуков), она мо жет быть намного выше.
Поскольку диспергирование с помощью ПАВ происходит в течение дли тельного времени, рекомендуется вылежка резиновых смесей в течение 4—6 ч.
ВУЛКАНИЗАЦИЯ РЕЗИНОВЫХ СМЕСЕЙ И ИЗДЕЛИЙ ИЗ НИХ |
||
Резиновые смеси и изделия из |
них могут |
из пластического состояния перейти |
в состояние эластичной резины |
в процессе |
вулканизации, осуществляемой обыч |
но при 140— 170 °С в присутствии вулканизирующего комплекса |
(серы, ускорите |
лей, активаторов и др.). В процессе вулканизации физические |
связи переходят |
в химические.
Подбором каучуков соответствующего качества и состава и других компо нентов, а также режима вулканизации достигается регулирование эластичных прочностных, тепло-, масло-, морозостойких, газостойких и других свойств гото вых изделий.
Подробно о смешении и вулканизации резиновых изделий изложено в спе циальных работах [57, 101].
РЕГУЛИРОВАНИЕ ПРОЧНОСТИ УГЛЕРОДОНАПОЛНЕННЫХ СИСТЕМ ПУТЕМ ПРЕВРАЩЕНИЯ ФИЗИЧЕСКИХ СВЯЗЕЙ В ХИМИЧЕСКИЕ
Спекание электродных заготовок, самообжигающихся анодов, за готовок для производства обожженных анодов во многом анало гично процессу замедленного коксования тяжелых нефтяных остат ков в необогреваемых камерах. Спекание, так же как и коксование, происходит по радикальному механизму, но с иными кинетически ми закономерностями. В результате сложных физико-химических изменений компонентов связующего, происходящих при высоко температурном нагреве, между зернами наполнителя образуются химические связи, приводящие к упрочнению структуры заготовок. При интенсивном обжиге летучие, выделяющиеся в виде паров и газов, искажают структурный скелет заготовок и ослабляют их механическую прочность. Постепенный нагрев заготовок в особо ответственных моментах (500—800 °С) способствует выделению ле тучих в виде низкомолекулярных газов и большему выходу кокса, образующегося при спекании связующего, что в конечном счете приводит к меньшему искажению структурного скелета заготовок.
Продукт, полученный после обжига, состоит из кокса-наполни теля и кокса, образовавшегося при коксовании связующего. По скольку температура прокаливания (1100—1300°С) и обессерива ния (1450°С) нефтяных коксов обычно другая, чем при обжиге заготовок, возникают различия в физико-химических свойствах (механическая прочность, реакционная способность, пористость, электропроводность и др.) кокса-наполнителя и кокса, образовав шегося из связующего. Наиболее однородной и, следовательно, лучшей по качеству электродная продукция будет при использо вании наполнителя и связующего, близких по степени анизометрии структуры частиц и при максимальном приближении условий про каливания наполнителя и обжига «зеленых» заготовок (наполни тель, смешанный с пеком в необходимом количестве). В принципе такие условия могут быть достигнуты при следующих комбинаци ях компонентов «зеленых» заготовок: нефтяной кокс-{-нефтяной пек; пековый кокс+каменноугольный пек; нефтяной кокс+камен ноугольный пек; пековый кокс + нефтяной пек. Для выбора типа пеков и коксов, позволяющих получать «зеленые» заготовки и далее из них электродные изделия (заготовки) с требуемыми качествами, необходимы дополнительные исследования.
«Зеленые» заготовки (800—1000°С) обжигают в отапливаемых газом многокамерных (до 32 шт) кольцевых печах сводового и от крытого типа и в однокамерных печах. Реже для этой цели исполь зуют туннельные и электрические печи. После обжига «зеленые» заготовки превращаются в единый монолит (электродные .заготов ки) высокой прочности. Электродные заготовки графитируют в спе циальных печах при 2300—3000 °С в течение 2—4 суток. Полный цикл графитирования с охлаждением длится до 20 суток.
Технология обжига самоспекающихся или самообжигающихся
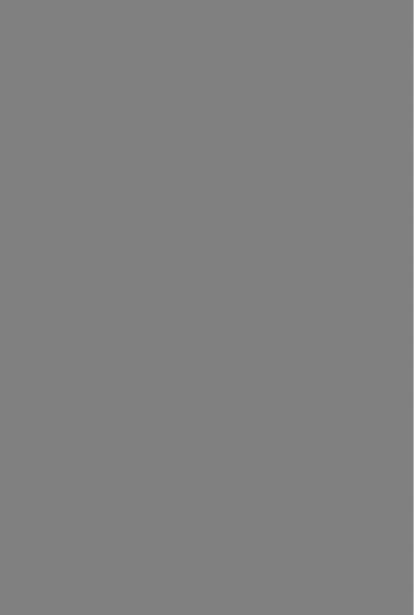
Рис. 25. Изменение |
структурной прочности |
^ |
иефтекоксобрикетов и металлургических коксов |
||
в нагретом состоянии: |
|
^ |
/ — брикеты из нефтяного кокса; 2 — кокс Ор* |
Ц |
|
ско-Халиловского МК; |
3 — кокс Губакннского |
с |
КХЗ. |
|
^ |
скорости |
нагрева 2—2,5°С/мии |
| |
||
брикеты |
полностью |
сохраняют |
|
|
свою форму и трещины в них не |
^ |
|||
образуются. |
С повышением раз- |
|||
мера брикетов в процессах спе- |
И |
|||
кания и прокаливания между по |
|
|||
верхностью |
и центром изделия |
Температура опыта.°с |
||
возрастает |
|
разница |
температур; |
|
она тем больше, чем выше скорость нагрева, что видно из следую щих данных:
|
|
Размеры образцов |
|
|
|
55X45X35 |
69X55X35 |
Скорость нагрева, °С/мин |
2,5 |
|
|
I образец |
|
||
11 |
образец |
5,0 |
|
III |
образец . |
10,0 |
|
Разница температур между по |
|
||
верхностью н центром |
наде |
|
|
лия, |
°С |
47 |
68 |
I образец |
|||
II |
образец |
90 |
112 |
III |
образец |
280 |
320 |
Образованию трещин при больших скоростях нагрева в значи тельной мере способствует распирающее действие паров и газов внутри брикетов. На рис. 25 показано изменение структурной прочности брикетов из нефтяного кокса и металлургических кок сов в нагретой состоянии.
При конечной температуре нагрева (900— 1000 °С) прочность брикетов из нефтяного кокса составляет 12,5— 15,0 МПа, т. е. при мерно такая же, как и у каменноугольных коксов; поэтому в ряде* случаев они могут стать заменителями коксов каменноугольного* происхождения.
Прочность брикетов зависит от среды и температуры, при ко торой их испытывают. При температурах выше 700°С, когда ак тивные газы интенсивно реагируют с углеродом, прочность коксов обычно ниже, чем в атмосфере инертных газов (азота, газопаро вых продуктов прокаливания).
ЗАЩИТНЫЕ ПОКРЫТИЯ ГРАФИТИРОВАННЫХ ЭЛЕКТРОДОВ
По заключению потребителей электродной продукции [72], из неф тяных коксов анизотропной структуры получают электроды высо кого качества. Электропроводность и термостойкость графитиро-
ванных электродов, изготовленных из такого кокса, выше, чем у
электродов, изготовленных на основе обычных нефтяных коксов, что позволяет повысить плотность тока в них в 2 раза. Благодаря главным образом улучшению термостойкости электродов расход их при выплавке стали снижается на 15—20%.
Больший расход углерода, чем расход его в результате низкой «термостойкости, наблюдается при контакте углерода в эксплуата ционных условиях при весьма высоких температурах с активными газами. Для предотвращения контакта электродов с активными га зами и снижения расхода углерода издавна были разработаны защитные покрытия на основе карбидообразующих элементов и их соединений, тугоплавких веществ и других материалов. Недо статком таких покрытий являлась малая адгезия с графитом при высоких температурах, что вызывало их отслаивание.
Впервые болгарские специалисты на основе алюминия и леги рующих элементов разработали весьма устойчивое защитное по крытие, предотвращающее в значительной мере угар электродов £25], которое можно применять при температурах выше 1750°С. В результате обработки электрической дугой последовательно на несенных на электрод слоев расплавленного и порошкообразного -алюминия и легирующих элементов достигается высокая адгезия покрытия толщиной 0,5—0,8 мм. Гомогенизированный слой элект родного покрытия содержит около 75% алюминия. При темпера турах выше 600 °С покрытие находится в расплавленном состоя нии, но не стекает с поверхности, обеспечивая хорошую сцепляемость с поверхностью графитированного электрода и газофобность его поверхности.
По данным Вылчева и др. i[25], защитное покрытие придает графитовым электродам повышенную электропроводность и спо собствует снижению расхода углерода. У электродов с увеличени ем диаметра с 200 до 450 мм электропроводность повышается вдвое, с дальнейшим увеличением их сечения она несколько сни жается. Основными источниками потерь углерода электродов яв ляются: боковое окисление (50%), торцевое окисление (35%), •расход огарков и поломка электродов (15%). У электродов, защи щенных покрытием, скорость бокового окисления в печном прост ранстве в течение 10—20 ч существенно замедляется, в результате чего расход графитированных электродов уменьшается на 25— «‘35%. В настоящее время защищенные электроды применяют во 1МНОГИХ развитых странах, в том числе и в СССР. Экономический
эффект от использования 1 т электродов с защитным покрытием доставляет 90 рублей.
ИСПОЛЬЗОВАНИЕ УГЛЕРОДОНАПОЛНЕННЫХ СИСТЕМ (УНС| И НЕФТЯНЫХ УГЛЕРОДОВ
Твердые углеродонаполненные системы в зависимости от их фи зико-химических и эксплуатационных свойств широко применяют в народном хозяйстве для различных целей. Твердые высокопроч ные УНС, нефтяные коксы и брикеты из них используют для сле дующих целей:
малосернистые нефтяные коксы — в качестве восстановителя к проводника электрического тока, а также для производства кон струкционных материалов;
высокосернистые нефтяные коксы и брикеты из них — как вос становитель и сульфидирующий агент (ВОС) в металлургии и хи мической технологии;
сажи (технический углерод) — в качестве наполнителей высо коэластичных УНС, применяемых в производстве покрышек, рези но-технических изделий и др., а также в качестве наполнителей; жидких УНС.
ИСПОЛЬЗОВАНИЕ ТВЕРДЫХ И ВЫСОКОПРОЧНЫХ УНС И НЕФТЯНЫХ КОКСОВ В КАЧЕСТВЕ ВОССТАНОВИТЕЛЕЙ, А ТАКЖЕ ПРОВОДНИКОВ ЭЛЕКТРИЧЕСКОГО ТОКА
Твердые и высокопрочные УНС после обжига или после обжига, графитации и соответствующей обработки (механическая обра ботка, нанесение защитного покрытия и др.) используют в элект ротермических производствах в качестве электродной продукции (электродов). Электродную продукцию применяют для подвода, тока в рабочую зону электролизеров и электропечей, предназна ченных для выплавки алюминия, магния, высококачественных ста лей и других металлов, а также ферросплавов и карбидов. В зави симости от эксплуатационных характеристик и условий примене ния различают, два вида электродов.
1. Угольные (обожженые и самообжнгающиеся) аноды, применяемые в ме таллургической, химической и электротехнической промышленности, получаемые из рядовых сортов нефтяного кокса и других углеродистых материалов камен ноугольного происхождения. Заготовки угольных анодов обжигают при 900— 1400 °С.
2. Графитированные электроды, используемые в электротермических процес сах, главным образом для производства стали. Заготовки графитированных электродов изготовляют нз лучших сортов нефтяных коксов; их обжиг осущест вляют при температурах до 2800—3200 °С. Графитированные электроды являют ся более качественными, чем угольные; они обладают высокой чистотой, повы шенной стойкостью к действию химических реагентов, имеют низкое удельное электросопротивление. Однако графитированные электроды в 2—3 раза дороже, чем угольные.
Для* проведения электротермических процессов графитированные электроды как наиболее термостойкие применяют при жестких (при температурах выше 1700°С), а угольные аноды — при мягких условиях (около 1000 °С). В принципе графитированные электро ды можно применять взамен некоторых видов угольных анодов в случае осуществления электротермических процессов при мягких условиях, но это экономически не выгодно.
При вводе в эксплуатацию крупнотоннажных электродуговых сталеплавильных печей, оборудованных мощными трансформато рами, используют крупногабаритные графитированные электроды (диаметром 555 мм и более) с повышенными эксплуатационными характеристиками, выдерживающие высокие токовые нагрузки — до 30—32 А/см2, в отличие от обычных графитированных электро дов, выдерживающих 12— 15 А/см2. В настоящее время электрод ная промышленность выпускает более 30 видов графитированных электродов и около 20 видов угольных анодов.
В процессе эксплуатации графитированные электроды и аноды подвергаются действию высоких температур, контактируют с раз личными химическими соединениями и испытывают механические воздействия. В результате они окисляются, сублимируются, рас творяются, выкрашиваются, обрываются и т. д.. Расход электродов является важной составляющей в себестоимости выплавляемой стали, алюминия и продукции других видов, поэтому на структуре расходования электродов следует остановиться поподробнее.
При выплавке стали в электродуговых печах отечественных за водов графитированных электродов расходуется 7— 10 кг/т стали. Учитывая такой большой расход и высокую стоимость электродов (150—300 руб/т) , представляет интерес выяснить факторы, влияю щие на структуру их расходования.
Сублимация и растворение графитированных электродов лока лизованы в зоне дуги, и поэтому их трудно контролировать. Элект роды выкрашиваются при их неправильном транспортировании, а также при резком изменении температурных условий и механиче ских воздействиях. Наибольшую долю в расходе электродов со ставляют потери при их окислении. По данным многочисленных исследований, доля угара электродов от окисления составляет около 75% от суммы потерь. Следовательно, изучению этого явле ния должно быть уделено особое внимание. Окисление вызывается химическим взаимодействием графита с кислородом, которое на чинается примерно с 400 °С. При высоких температурах углерод может взаимодействовать с двуокисью углерода и водяным паром:
С 4- 0 2 = |
СОо + 395 018 кДж |
(7) |
С 4 -С 02 = |
2СО — 173 124 кДж |
(8) |
С - f Н20 = СО -Ь Н2 — 133 224 кДж |
(9) |
Существенное влияние на реакционную способность электродов оказывает природа сырья, применяемого для ее изготовления. В работах {7, 8] показана возможность регулирования реакцион