
книги / Нефтяной углерод
..pdfРис. 49. Изменение молекулярной массы масел (кри вая 1), смол (кривая 2) и асфальтенов (криоая 3) при термодеструкции.
разованием химических связей в ассо- |
§ |
|
циатах, формируется |
нефтяной угле- |
| |
род, нерастворимый ни в чем. |
^ |
|
Многочисленные |
исследователь- |
^ |
ские данные о формировании углеро- ^ |
|
||
да нефтяного и каменноугольного про- | |
|
||
исхождения находятся |
в согласии с § |
|
|
изложенными выше |
представлениями |
|
|
о термодеструкции |
углеводородного |
|
|
СЫРЬЯ> |
|
О |
30 60 90 129 150110 |
Впервые продукт |
|
межмолекуляр- |
Длительность, мин |
ного взаимодействия, |
обладающий |
|
специфическими свойствами, обнаружили при коксовании камен ноугольной смолы Брукс и Тейлор; они назвали его мезофазой [144]. Эти исследователи, а затем Федосеев [129] и Гимаев [30] показали, что в результате термообработки каменноугольных и нефтяных пеков при температурах выше некоторой кри тической в однофазной массе появляются анизотропные мик росферы мезофазы размером 0,1—20 мкм. Сферическая форма вызвана действием сил поверхностного натяжения. Эти микросфе ры обладают способностью к изменению своих размеров.
Пеки могут находиться в изотропной и анизотропной фазах, которые характеризуются разными физико-химическими свойства
ми. Обычно плотность анизотропной |
фазы (мезофазы) — 1350— |
1400 кг/м3 — всегда выше плотности |
изотропной фазы— 1250— |
1320 кг/м8. Различие в свойствах анизотропной и изотропной фаз обусловливает их неодинаковую способность к расслоению и в дальнейшем к формированию из анизотропной фазы нефтяного уг лерода. Чем легче проходят процессы зарождения, роста, сращи вания и видоизменения микросфер, -тем выше волокнистость и гра- •фитируемость получаемых углеродов.
Этапы коксования пеков и нефтяных остатков в лабораторном кубе с периодической загрузкой сырья показаны на рис. 49. В за висимости от изменения молекулярной массы выделенных из сырья асфальтенов, смол и масел различают три этапа коксования. На первом этапе протекают преимущественно реакции распада угле водородов коксуемого сырья с образованием главным образом жидких дистиллятных фракций, Газообразование при этом незначи тельно. В газе постепенно возрастает количество водорода, метана и непредельных углеводородов. К концу этого этапа содержание непредельных углеводородов в газе достигает" максимума; молеку лярная масса масел, смол и асфальтенов постепенно снижается.
При нагревании нефтяных остатков скорости реакции распада и конденса ции должны изменяться неодинаково. Для образования коротко- и дол гоживу-
щих радикалов энергия разрыва связей должна быть в большинстве случаев намного больше или равна энергии активации. Энергия активации при деструк ции меньше, чем энергия разрыва связей, вследствие образования промежуточ ных продуктов (газы, бензин, промежуточные фракции). В этих продуктах но вые связи начинают образовываться одновременно с разрывом старых. Энергия активации крекинга равна разности между энергией разрыва связен молекул исходного сырья и энергией, затрачиваемой на образование новых связей в промежуточных продуктах. Таким образом, энергия активации крекинга есть функция глубины крекинга; при его протекании лучше осуществляется первый этап (распад), требующий меньшей энергии активации, чем полный крекинг молекул исходного вещества.
Опыт работы промышленных установок также подтверждает, что по мере углубления крекинга энергия активации распада воз растает.
По данным различных исследователей, средняя энергия актива ции термического разложения нефтяных остатков составляет 231 .кДж/моль. При увеличении молекулярной массы индивидуаль ных ароматических углеводородов энергия активации их распада уменьшается до определенного предела [124]. Та же закономер ность наблюдалась в работе [187] при термическом крекинге лиг роина и различных газойлей нефтяных фракций. Энергия актива ции при термическом крекинге лигроина и газойлей составляла со ответственно 273—294 и 231 кДж/моль.
С отмеченной закономерностью согласуются данные [64], в со ответствии с которыми энергия активации коксования в ряду: мас-
ла-*смолы-*-асфальтены |
снижается в следующем |
порядке: |
2 1 0 000-*-135£40->-108360 кДж/моль. Снижение энергии |
активации |
распада с повышением молекулярной массы, низкое ее значение в начальной стадии и высокое к концу процесса показывает, что в первую очередь при термическом крекинге углеводородов отщеп ляются атомные группировки со слабыми связями.
С повышением температур^ крекинга скорость образования короткоживущих радикалов растет быстрее, чем скорость образова ния долгоживущих радикалов; для образования которых требуется меньше энергии активации, ^ результате с повышением темпера-^ туры скорость реакции распада сырья крекинга должна быть выше скорости реакции конденсации. Экспериментально подтверж дено, что энергия активации распада (231 кДж/моль) выше, чем энергия активации реакции конденсации (197 кДж/моль) [70].
Между реакциями распада компонентов сырья и уплотнения проходит некоторое время; поэтому, регулируя процесс, можно по лучить значительное количество жидких и газообразных продуктов без существенного карбоидообразования (например, при термиче ском крекинге). Этим приемом в промышленных условиях пользу ются для легкого крекинга тяжелых нефтяных остатков с целью снижения их вязкости.
На втором этапе термодеструкции, как и следовало ожидать, интенсивно протекают процессы конденсации высокомолекулярных углеводородов, вызывающие увеличение молекулярной массы со ставляющих нефтяного остатка. В газе количество водорода и ме-
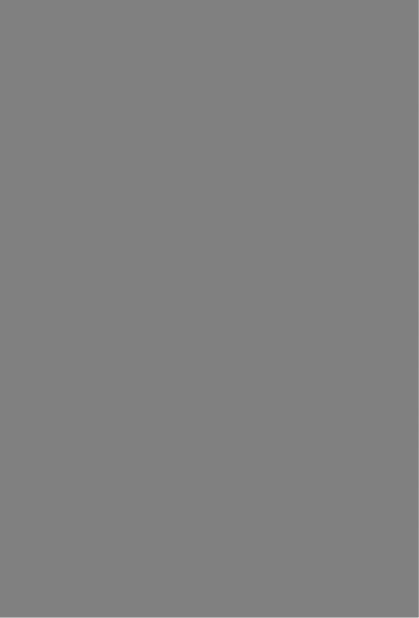
Рис. 51. Изотермы образования мезофазы в процессе коксования при Р=0,1- МПа дистиллят* иого крекинг-остатка (а) и гудрона (б).
Температура коксования, вС. а: / — 450; 2 — 460; 3 — 480; б: / — 440; 2 — 460; 3 — 460;
460 и Я= 1,0 МПа.
предела) и длительности термодеструкции доля мезофазы растет
истремится к единице.
Вслучае пространственной конфигурации молекул (гудрон) доля мезофазы при тех же условиях меньше; она несколько по вышается с увеличением давления (до 0,5 МПа) в системе. Для тех же видов остатков на рис. 52 показано изменение групповых компонентов в процессе коксования. Из рисунка видно, что значе ния пороговой концентрации асфальтенов, после достижения кото рой начинается интенсивное карбоидообразование, для остатков различного происхождения неодинаковы. При более высоких тем пературах пороговая концентрация асфальтенов достигается в слу чае меньшей длительности нагрева остатков в системе.
Подвижность ассоциатов в процессе термодеструкции в значит тельной мере зависит от свойств дисперсионной среды. Для форми рования из микросфер крупных сфер мезофазы необходимо сокра тить влияние диффузионных факторов, обеспечить подвод к микро сферам полициклических ароматических структур и создать одно временно возможность слияния-этих микросфер в более крупные.
Исследования вязко-пластических свойств коксующейся массы
впроцессе термодеструкции показали, что дистиллятные крекингостаТки остаются пластичными более длительное время, чем кре кинг остатки остаточного происхождения. Длительный интервал пластичности, высокая пороговая концентрация асфальтенов в про цессе термодеструкциипозволили рекомендовать высокоароматизованныё дистиллятные крекинг-остатки и смолы пиролиза для получения пёков с различными температурами размягчения, обла дающих специфическими физико-химическими свойствами.
Для разного использования в промышленности требуются пеки со строго определенным групповым углеводородным составом и физико-химическими свойствами. Как показано выше (см. с. 81), необходимо получать пеки с широкими пределами температуры размягчения по КИС (50—250 °С). Если жесткие требования к
групповому углеводородному составу пеков не предъявляются, то
.пеки с одинаковой температурой размягчения можно получить при различном соотношении в остатках содержания карбенов, карбондов, асфальтенов, смол и масел.
При работе на одном и том же виде сырья соотношение груп повых компонентов регулируют изменением диффузионных факто ров (вязкости), режима (температуры, давления, длительности) и добавкой инициаторов или ингибиторов цепной реакции. На осно вании этого предложены варианты получения пеков с различным составом и температурами размягчения:
получение пека с низкой температурой размягчения при жест ком режиме (450—500 °С и повышенном давлении) — скоростной метод Таушева [ 1 2 1 ];
производство связующих веществ при 420 °С и давлении, близ^ ком к атмосферному,— медленный способ по Л. В. Долматову;
способ И. 3. Ахмерова для получения пека с высокой темпера турой размягчения при низких температурах (340—380 °С) и под вакуумом [ 1 0 ].
При немассовом производстве пеков можно рекомендовать спо соб раздельного получения (с применением растворителей) группо вых компонентов с последующим их компаундированием. Возмож ны также комбинации первых трех способов с целью регулирова-
90 |
450°С |
|
> л п |
|
W C |
|
||
|
|
|
|
|
|
|||
Г |
|
|
|
70 |
|
|
/ |
f |
|
/ |
3 |
50 |
|
||||
& 50 |
|
|
|
|
|
|
||
н 30/ |
|
|
2 |
30 |
f |
|
|
|
10 |
|
|
|
|
|
|
|
|
|
90 |
7 |
10 |
f |
xjr |
\ |
-^i |
|
1f 30 60 |
120 150180 |
1 |
20 |
W 60 |
00 100 no |
Рис. 52. Изменение концентрации асфальтенов (кривая 1), карбенов (кривая 2) и карбондов (кривая 3) в остатке коксования дистиллятного крекинг-остатка (а) н гудрона (б).
|
Условия опыта |
Темпера |
Состав пека |
|
|||
|
|
|
|
|
|
|
|
|
|
|
длитель |
тура раз |
|
|
|
Способ |
темпера- |
давление, |
мягчения |
карбены+ |
асфальте |
масла |
|
|
ч р - |
МПа |
ность, |
по КИС, |
карбонды |
ны |
|
|
|
ч |
°С |
|
|
|
|
Таушеза |
450 |
0,2 |
I |
75 |
28 |
50 |
22 |
Долматова |
420 |
0,2 |
5 |
80 |
30 |
45 |
25,0 |
Ахмерова |
380 |
0,0001— |
2 |
170 |
15 |
80 |
5,0 |
|
|
—0,0003 |
|
|
|
|
|
лия состава получаемых пеков. Ахмеровым £10] показана возмож ность повышения температуры размягчения пека при добавлении в качестве инициатора дикумйла. Качество пеков, полученных раз личными способами при работе на одном и том же виде сырья (дистиллятный крекинг-остаток), приведено в табл. 16.
Наиболее жесткие требования к составу предъявляются при получении пека для формования. Для получения пека с высокой температурой размягчения необходима высокая концентрация асфальтенов (не менее 80%) и низкое со держание парафино-нафтеновых углеводородов и карбоидов. Наличие последних затрудняет процесс формования и проведение последующих стадий облагоражи вания углеродного волокна.
Таким образом, второй этап термодеструкции (см. рис. 49) яв ляется ответственным, с точки зрения формирования мезофазы и получения пеков с различными температурами размягчения.
Как видно из рис. 49, третий этап характеризуется кажущимся снижением молекулярной массы составляющих остатка. На самом деле на этом этапе происходят дальнейшие процессы уплотнения и конденсации, заканчивающиеся образованием продуктов глубокого уплотнения всего остатка коксового пирога. При отборе проб и их анализе определяют молекулярные массы легких продуктов, кото рые не подверглись конденсации, что и обусловливает понижение молекулярных масс компонентов на третьем этапе. Об интенсив-' ном протекании на этом этапе процессов уплотнения свидетельству ют* снижение выделения дистиллята и бурное образование газа.
"Кинетическая модель деструкции, учитывающая растворяю щую силу среды и возможность образования двухфазной системы при коксовании нефтяных остатков, предложена в работе [18]. Ис ходные остатки мангышлакской и котур-тепинской нефти, выки пающие выше 500 °С, подвергались термодеструкции в реакторе ин тегрального типа периодического действия при 452, 462 и 472 °С. По обычной методике в изотермических условиях по времени от бирали пробы, в которых определяли содержание групповых ком понентов. На основании полученных данных на рис. 53 представ лены кинетические кривые деструкции гудронов указанных остат ков при 472 °С, а на рис. 54 в качестве примера приведены кривые изменения концентраций полициклических ароматических углево дородов, асфальтенов и карбоидов в жидких продуктах разложе
Рис. 53. Кинетика деструкции гудронов мангышлакской (а) и котур-тепинской (б) нефтей при 472 °С:
Xi —масла; *2—полициклические углеводороды; жз—смолы; ж« — асфальтены; JTS —карбои- Ды; ж«— летучие в условиях опыта вещества.
Сплошные линии — экспериментальные данные; пунктирные — расчеты
ния тех же остатков при 452-°С (схожие кривые деструкции остат ков при 462 и 472 °С приведены в работе [18]).
При разработке |
кинетической модели термодеструкции остатков приняты |
в [18] представления |
об образовании надмолекулярных структур в жидких про |
дуктах деструкции и об изменении по мере непрерывного превращения группо вых компонентов устойчивости и механической прочности системы.
Кинетическая модель имеет следующий вид:
Г8
. |
П |
ж |
Гг |
ж |
Гз |
ж |
4 |
» |
(о |
|
ч = > |
А 2 |
4 - ь А 3 |
у -Л |
A t |
5==* |
А ъ |
||
|
Г В |
|
Г ю |
|
ПХ |
|
'12 |
|
|
1Г* |
|
|
\* |
|
|г’ |
|
|
|
|
I____________ |
|
|
* |
' |
|
|
I |
|
|
Рис. 54. Изменение концентрации полициклических углеводородов х2, асфальтенов х4 и карбоидов xs в жидких продуктах разложения гудронов.
Сплошные линии — экспериментальные, пунктирные — расчетные мангышлакской (а) и ко- тур-тепинской (б) нефтей при 452 ®С.
В изотермическом реакторе изменение концентраций компонентов для схе мы (1) опишется системой уравнений:
( 2 )
5
где *в = 1 — £ ]х * ;
|
|
W i — Tj —г э — К А Х |
ХяЛ2; |
|||
|
|
W 2= г2— г0= К гА \ —Хю-^з» |
||||
W* = |
'з - |
гп = К,Л§ - |
К 1ХА ^ |
Wb = г* = КьАг ; |
||
|
W a — г6 = |
М з |
> |
^ 7 = |
Г1 = ^7^4» |
|
|
|
IFg = г8= |
/е8Л2Л4; |
|||
» |
W |
. = х 4 |
(л4 - л ' |ас) 2 |
|
||
----------1- 2— , |
если Л4 > Л * |
|||||
|
|
2 |
л£+Х.И» |
|
||
|
|
1=1 |
|
|
|
|
|
|
№4 = |
г4 = |
0, если Л4 <Л™ С |
Здесь i4i — масла; Лг— полициклические ароматические углеводороды; А з— смолы; Л* — асфальтены; Аь — карбоиды; Лв — летучие; Go — навеска исходного образца. Объем жидкой фазы V равен:
где d Ji — плотность t-ro компонента; х,-— массовая доля t-ro компонента;
г, — скорость превращения компонента по направлению /; K f— коцстанта скоро
сти по Аррениусу; а — коэффициент, характеризующий растворяющие свойства полициклических ароматических углеводородов; К\г — коэффициент, характери зующий стабилизирующие свойства смол; а0, аи аг, в — эмпирические константы;
Лов — концентрация парафиновых углеводородов. Л »ас — концентрация асфаль-
тенов в момент насыщения; ИР/— изменение концентрации компонента по на правлению /.
Поиск констант для кинетической модели (2) проводили с помощью мини мизации функции:
где п — число замеров в одном опыте; т — число опытов.
На основании дифференциальных уравнений, описывающих данную схему, были подсчитаны константы скорости каждой ста дии. Результаты расчетов подтвердили, что полициклические аро матические углеводороды могут подвергаться деструктивным пре вращениям по двум ветвям (см. с. 109), что свидетельствует о двухканальной схеме превращения высокомолекулярных углеводо родов при термодеструктивных превращениях. Одновременно было подтверждено влияние на процессы коксообразования растворяю щей силы среды, которая влияет на расслоение нефтяной системы на фазы. Так, наличие в остатках котур-тепинских нефтей повышенного содержания ароматических углеводородов приводит к дезагрегации асфальтенов, увеличению их дисперсности и соот ветственно устойчивости (высокий порог осаждения). .
Карбоидообразования в этих остатках (см. рис. 54, а) не про
исходит до тех пор, пока кривая концентрации асфальтенов (Схл) не пересечет кривую концентрации полициклических арома
тических углеводородов (С*2), т. е. это происходит тогда, когда
€*а>Сх3 .
В высокопарафинистых остатках мангышлакских нефтей (см. рис. 54, б) концентрация асфальтенов (С*4) всегда больше кон
центрации полициклических ароматических углеводородов (C*f );
поэтому уже на ранних стадиях термодеструкции в результате пе рехода асфальтенов во вторую фазу образуется микрогетерогенная система, после чего они начинают интенсивно превращаться в карбоиды. Полученные результаты хорошо согласуются с промыш ленными данными, показывающими более быстрое закоксовывание змеевиков промышленных печей при работе на остатках мангыш лакских нефтей.
Механизм коксования, установленный в лабораторных услови ях, дополняют данными, полученными в промышленных необогреваемых камерах высотой 25 м и диаметром 5 м. После подключе ния в систему подготовленной камеры с верха ее через определен ные интервалы времени отбирают пробы для анализа и фиксируют режимные параметры. Исследуют также образцы коксов, отобран ных из различных зон реактора. По-видимому, гидродинамические условия коксообразования оказывают влияние на внутри- и меж молекулярные взаимодействия и на структуру (в том числе и по-
ровую) различных слоев кокса, которая, в свою очередь, может предопределить интенсивность процессов деструкции, уплотнения и структурирования при последующей термообработке этих об разцов.
Описанный метод позволяет не только изучать механизм и ки нетику деструкции нефтяных остатков, но и -выяснить закономер ности влияния на процесс коксования сопутствующих явлений (например, вспучивания остатков), осложняющих и в ряде случа ев сокращающих длительность работы установок, а также устано вить неоднородность кокса, получаемого в камере. Методика очень проста и убедительна, поэтому она успешно применяется на нефте перерабатывающих заводах для исследовательских целей.
В работе [76] показана нестабильность свойств дистиллятов, отбираемых сверху камеры (реактора) при использовании прямо гонного сырья и крекинг-остатка. Аналогичные изменения кривых температуры верха реактора и физико-химических констант дис тиллята указывают на одни и те же причины этих изменений, ко торые связаны с фазовыми переходами в реакторе в процессе кок сования. В первый период коксования до пороговой концентрации асфальтены накапливаются в остатке, затем они выпадают во вто рую фазу. Момент выпадения асфальтенов и начало образования коксового массива четко прослеживаются на кривых изменения выходов и качества дистиллята. Чем меньше агрегативная устой чивость системы (чем больше асфальтенов и парафинов), тем ско рее достигается пороговая концентрация асфальтенов и выпаде ние их во вторую фазу. Затем наступает при постоянной подачесырья в реактор период непрерывного выделения асфальтенов, кон центрация которых превышает порог осаждения. Результаты ана лиза кокса по высоте реактора показали его неодинаковое качест во. Большее время, затрачиваемое на удаление кокса из средней части камеры, согласуется с высокой механической его прочностью в этой зоне. При удалении кокса из нижней и верхней зоны фор мируется мелочь (фракции ниже 25 мм), что снижает качество, электродного кокса. Это видно из данных табл. 17, полученных на различных установках замедленного коксования при работе на различном сырье.
На основании полученных результатов и литературных мате риалов, механизм замедленного коксования в необогреваемых ка мерах при непрерывной подаче сырья в реактор можно представить
вследующем виде.
Вначальный момент при загрузке реактора горячим сырьем стенки камеры разогреваются. Происходит усиленное выделение паров и на дне реактора накапливается жидкая масса — тяжелая часть загрузки. При незначительном уровне жидкости в реакторе
дистиллят, проходящий через верх реактора, представляет собой в основном малоизмененные фракции исходного сырья. В этом: случае процесс испарения преобладает над процессом разложения, что и приводит к высоким значениям плотности и вязкости дис-