
книги / Нефтяной углерод
..pdf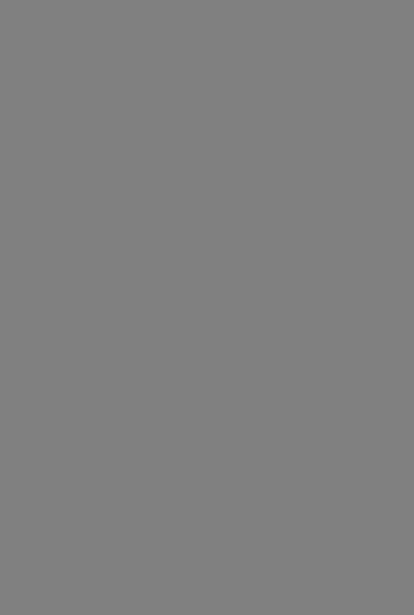
высокой степени дисперсности. Такое направление в сочетании с повышением температуры процесса является весьма перспектив ным.
Утяжеление сырья сопровождается повышением содержания в получаемой саже сернистых соединений и других гетероэлементов. В присутствии некоторых гетероэлементов (например, щелочных металлов) свойства саж, как было ранее показано, также ухуд шаются (снижается их структурность). Как известно, металлоор ганические соединения*в наибольшей степени сконцентрированы в асфальтенах; для выяснения влияния повышения их доли в сырье
на свойства саж |
требуется проведение |
научно-исследовательских |
и опытных работ. |
термодеструктивные |
процессы обычно служат |
Жидкофазные |
для производства пеков и нефтяного кокса. Чаще всего эти про цессы используют для получения нефтяного кокса.
Производство нефтяного кокса из года в год растет в сред нем в СССР на 9%, а в США на 2,0%. В качестве сырья кок сования в СССР и за рубежом используют нефтяные остатки, вы ход которых на нефть составляет 30—50%. Определяющим пока зателем качества сырья, влияющим на выход кокса, следует счи тать коксуемость, которая для сырья, применяемого в СССР, со ставляет 10—20% масс., а для сырья США 18—25%.
Исходным сырьем для получения нефтяных остатков являются малосернистые (мангышлакские, ширванские, котур-тепинские и др.), сернистые (западносибирские, ромашкииские) и высокосер нистые (типа арланской, чекмагушской) нефти. Указанные нефти различаются содержанием не только серы, но и асфальто-смоли стых веществ, парафиновых и других углеводородов и их соотно шением, а также кислотностью и зольностью. Эти различия созда ют неодинаковые условия структурирования остатков в процессе их получения и дальнейшем воздействии на такие остатки пара метров процесса. Происхождение нефтяных остатков (прямогон ный, крекинг-остаток и дистиллятный крекинг-остаток) и содер жание гетероэлементов (серы, металлоорганических соединений) существенно влияют на ход и технологическое оформление про цесса производства пеков и кокса. Наиболее эффективные резуль-, тэты при производстве пеков и кокса игольчатой структуры полу чают из остатков дистиллятного происхождения.
Обычно для получения электродного кокса (S ^ 1,0%) исполь зуют малосернистые нефтяные остатки дистиллятного и остаточ ного происхождения коксуемостью 6—12%. Использование остат ков с низкой коксуемостью вызывает диспропорцию между за грузками реакторного блока типовых установок коксования и рек тификационной их части [112]. Это не позволяет эксплуатировать установки с одинаковой эффективностью при переработке остат ков с различной исходной коксуемостью. Установки с необогреваемыми камерами наиболее эффективны для коксования остат ков коксуемостью 12—20%.
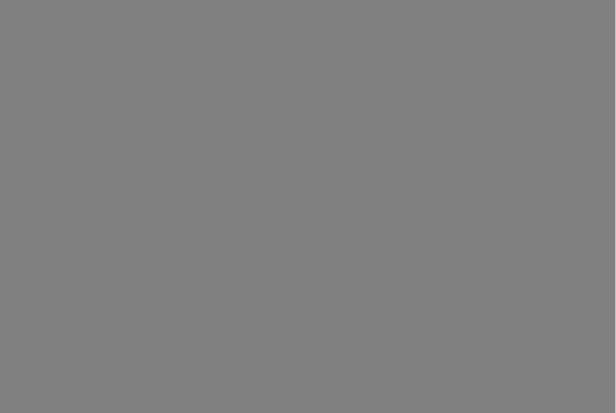
При углублении процесса переработки нефти коксуемость ос татков возрастает до 30% и более, что особенно существенно по вышает эффективность процесса коксования. Такое высокое зна чение коксуемости малосериистых остатков может быть достигну то термоконденсацией их при повышенном давлении [36]. Исход ные сернистые и высокосернистые нефтяные остатки характеризу ются значительной коксуемостью, поэтому предварительная под готовка сырья -перед коксованием требуется не всегда.
Общим для всех видов жидкого сырья для производства неф тяного углерода является большое содержание в нем углеводо родов, склонных к образованию ассоциатов, *что может быть оценено отношением Н : С, приведенным-в табл. 19. Там же при водятся другие физико-химические свойства нефтяных остатков.
ПРОМЫШЛЕННЫЕ СПОСОБЫ И ПЕРСПЕКТИВЫ РАЗВИТИЯ ПРОИЗВОДСТВА ТЯЖЕЛЫХ АРОМАТИЧЕСКИХ КОНЦЕНТРАТОВ И НЕФТЯНЫХ ОСТАТКОВ
Из всех нефтепродуктов наиболее склонны к образованию различ ных видов структур при высоких температурах ароматические концентраты (дистиллятный крекинг-остаток) и другие нефтяные остатки, поэтому их в основном и используют в качестве сырья для производства нефтяного углерода.
Ароматические концентраты. В различных нефтях содержится 20—30% аро матических углеводородов, главным образом в виде моноциклических и бициклических структур, которые в процессе переработки нефтей распределяются по фракциям. В результате различных деструктивных процессов образуется допол нительное количество ароматических углеводородов, одновременно возрастает степень их конденсированное™. В промышленных условиях обычно трудно вы делить в чистом виде ароматические углеводороды, поэтому их получают в виде ароматических концентратов: коксовые газойли и газойли каталитического кре кинга, экстракты масляного производства, смола пиролиза. В них ароматических углеводородов содержится 50—75%.
Коксовые газойли образуются в процессе коксования нефтяных остатков.
Они представляют собой широкую фракцию (200—500 °С), выход которой 40— 70%. Содержание в этой фракции ароматических углеводородов зависит от со става исходного сырья коксования и температурного режима процесса. При кок совании крекинг-остатков дистиллятного и остаточного происхождения сущест венно возрастает содержание ароматических углеводородов, что проявляется в резком увеличении плотности и в соответственном снижении характеризующего фактора газойлей. Предполагается, что в дальнейшем основным способом пере работки нефтяных остатков в кокс будет замедленное коксование, что позволит весьма существенно увеличить выработку газойлей на нефтеперерабатывающих заводах.
Коксовые газойли будут использоваться в качестве компонентов топлив пос ле их предварительного облагораживания (каталитический крекинг, гидроочист ка), компонентов профилактических смазок против прилипания и примерзания сыпучих материалов к поверхностям горнотранспортного оборудования, а также в качестве судового топлива. Высокое содержание в коксовых газойлях тяжелых ароматических углеводородов создает возможность использования их после тер мического крекинга в качестве сырья для производства нефтяного углерода.
Исследования последних лет [134] показали, что индекс корреляции коксо вых газойлей при коксовании дистиллятных крекинг-остатков в чистом виде или
I
о смеси с остаточными видами сырья 110—120; поэтому их можно направлять на производство саж без предварительной термодеструкции.
При термическом крекинге коксовых газойлей с другими концентратами ароматических углеводородов наряду с газом и бензином получают термогазонлевые фракции (газойль термического крекинга) п дистиллятный крекинг-оста
ток. Газойль |
термического крекинга |
используют в производстве печных саж, |
а дистиллятный крекинг-остаток — в |
производстве других видов нефтяного уг |
|
лерода (игольчатого нефтяного кокса, |
нефтяных пеков с различными температу |
|
рами размягчения). |
|
|
Газойли каталитического крекинга получают при каталитическом крекинге |
||
дистиллятных |
нефтяных фракций — вакуумных газойлей — прямой перегонки, |
кероенно-газойлевых фракций коксования в присутствии специальных алюмоси ликатных и цеолитсодержащих катализаторов.
Развитие процессов каталитического крекинга в присутствии высокоактив ных цеолитсодержащнх катализаторов позволит повысить степень ароматизации каталитических газойлей и, следовательно, создать более ценное сырье для по лучения газойля на установках термического крекинга, идущего для производ ства сажи.
В эксплуатации находятся установки каталитического крекинга с шарико вым катализатором в движущемся слое и микросферическим катализатором в кипящем слое. В связи с большими возможностями установок с кипящим слоем в СССР и за рубежом установки с шариковым катализатором больше не строят.
Ниже приводится типичный выход продуктов на установке с движущимся
слоем катализатора (в % масс.): |
|
|
||
Газ до |
С* |
.11,0 |
Легкий |
. 29 |
Бензин |
|
.28,0 |
Тяжелый |
27 |
Перевод установок на работу с цеолитсодержащими катализаторами типа АШНЦ-1 и АШНЦ-3 и повышение температуры на 150—200 °С способствует боль шей глубине превращения сырья, увеличению выхода бутан-бутиленовой фракции, а также выхода бензина за счет снижения выхода керосино-газойлевых фракций. Это приведет к резкому снижению ресурсов сырья для производства нефтяного углерода при одновременном улучшении качества газойлей каталитического кре кинга по содержанию ароматических углеводородов. По предварительным дан
ным, выход газойлей каталитического крекинга снизится более чем в 2 раза.
Экстракты масляного производства. Базовые масла, из которых в дальней
шем смешением (компаундированием) и добавлением присадок получают мотор ные, индустриальные, электроизоляционные и другие масла, производят на неф теперерабатывающих заводах по сложной технологии. Начальным процессом яв ляется прямая перегонка под вакуумом мазута — остатка после отгона светлых продуктов. При этом получают фракции 300—400, 350—420, 420—490 °С и остат ток (гудрон).
При обработке гудрона пропаном получают деасфальтизат и асфальт. Деасфальтизат очищают селективными растворителями от полициклических арома тических и нафтено-ароматических углеводородов, смол и других примесей. В результате очистки образуется экстракт (используемый для производства неф тяного углерода), выход которого зависит от качества сырья и глубины очистки.
Развитие гидрогенизационных процессов (гидрокрекинг и гидроизомеризация), которые в ряде случаев заменят очистку селективными растворителями, приведет к снижению выхода экстракта и, следовательно, уменьшению количест
ва сырья для производства нефтяного углерода.
Смолы пиролиза. Ценные нефтехимические продукты — этилен, пропилен, бу-
тилены извлекают из нефтезаводских газов и в основном в процессе термическо
го пиролиза. В |
результате термического воздействия (700—900 °С) на |
сырье |
(газы, бензины, |
керосино-газойлевые фракции, нефть, тяжелые остатки) в |
тече |
ние короткого времени и при низком давлении получают указанные непредельные углеводороды и одновременно продукты глубокой степени деструкции. Соотноше ние выхода продуктов пиролиза зависит от качества исходного сырья и техно логического режима процесса. С повышением молекулярной массы сырья и уве*
личеннем продолжительности процесса пиролиза возрастает выход жидких про дуктов, в том числе смол (сырья для получения нефтяного углерода), что видно из следующих данных:
|
Выход |
|
Выход |
Сырье пиролиза |
смолы, |
Сырье пиролиза |
СМОЛЫ, |
% масс. |
% масс. |
||
|
на сырье |
|
на сырье |
Этан |
2 - 3 |
Тяжелый бензин |
25—30 |
Пропан |
8 -1 0 |
Керосино-газойлевая |
3 0 -3 5 |
к-Бутан |
5 - 8 |
фракция |
|
Легкий бензин |
20—25 |
Мазут |
3 5 -4 0 |
Жидкие продукты пиролиза делят на бензиновую фракцию и фракцию, вы кипающую выше 200вС (-смолы). С повышением температуры и длительности процесса пиролиза увеличивается соотношение выходов смолы пиролиза: бензи новые фракции, одновременно в этих фракциях возрастает содержание арома тических углеводородов. Так, при повышении температуры пиролиза с 750 до 800 °С это соотношение в случае использования в качестве сырья бензинов из меняется в пределах 0,3—0,5, а в случае более тяжелых фракций — от 1,2 до 1,5.
Ужесточение режима приводит к глубоким изменениям в составе смол пиро лиза: в них уменьшается доля парафино-нафтеновых углеводородов, что обу словливает высокую плотность смол пиролиза. Проведенный Ивановой [49] с применением жидкостной адсорбционной хроматографии анализ тяжелых смол пиролиза (270—500 °С) показал, что в них содержится около 5% парафино-наф теновых и непредельных углеводородов и 20 и 73% соответственно моно- и полициклических ароматических углеводородов.
Вследствие низкого выхода при термическом пиролизе целевых продуктов, необходимости интенсификации и совершенствования процесса требуется внедре ние в промышленность каталитических процессов пиролиза. В присутствии ка тализаторов процесс можно проводить под повышенным давлением, увеличить выход этилена на 40—80%, но при этом выход омол снижается на 20—25%.
Жидкие продукты пиролиза, содержащие значительные количества аромати ческих углеводородов, используют в качестве компонентов товарных бензинов; кроме того, из них извлекают ароматические углеводороды (например, нафта лин). Иногда смолы пиролиза добавляют в котельные топлива. Однако более рационально использовать тяжелые смолы, выкипающие выше 200 °С и содер жащие в больших количествах би- и полициклические ароматические углеводо
роды, в качестве сырья |
для производства |
коксов игольчатой |
структуры, сажи |
и пеков с различными температурами размягчения. |
|
||
Нефтяные остатки. В |
промышленности |
наиболее широко |
распространены |
следующие методы подготовки сырья для получения массовых видов нефтяного углерода: 1) прямая перегонка нефти; 2)термическин крекинг дистиллятных и остаточных нефтепродуктов; 3) деасфальтизация нефтяных остатков.
В настоящее время чаще всего подготовка сырья для производства нефтяно го углерода (нефтяных коксов, пеков) осуществляется первыми двумя способами. Углубление переработки нефти достигается внедрением в схему нефтеперераба тывающих заводов деасфальтизации прямогонных нефтяных остатков (мазута) бензином (процесс добей). Применение этого процесса дает возможность полу чать деасфальтизаты с пониженными коксуемостью (в 1,8—2,0 раза) и темпера турой размягчения по сравнению с исходным сырьем [139], что позволяет ис пользовать деасфальтизат в качестве сырья для гидрогенизационных процессов. Асфальтит, получаемый в виде второго продукта процесса деасфальтизации, представляющий сильно структурированную жидкость, вместе с другими остат ками может в ряде случаев направляться на процесс коксования. Деасфальтизат после его термодеструкции может направляться на процесс коксования с целью получения специальных сортов нефтяного кокса.
Характеристика сырья и деасфальтизата, полученных при работе на ромашкинском н арланском гудронах, была приведена в табл. 19. В этой же таблице приведены физико-химические свойства и других видов нефтяных остаточных и дистиллятных продуктов, используемых на промышленных установках по по лучению нефтяного углерода.
ПРОМЫШЛЕННЫЕ СПОСОБЫ РЕГУЛИРОВАНИЯ СОДЕРЖАНИЯ КОНДЕНСИРОВАННЫХ АРОМАТИЧЕСКИХ УГЛЕВОДОРОДОВ В АРОМАТИЧЕСКИХ КОНЦЕНТРАТАХ
Регулирование качества углеводородного сырья, используемого для получения нефтяного углерода со строго определенными, но раз ными (в зависимости от направления их использования) свойст вами, основано на требованиях, предъявляемых к углеродистым, материалам в различных отраслях народного хозяйства. Это до стигается правильным подбором режима процесса термодеструк ции ароматических концентратов.
В наиболее типичном сырье для производства печной сажи — зеленом масле* содержится до 80—85% ароматических углево дородов, в том числе 75% приходится на долю тяжелых. Принято считать, что хорошим сырьем для производства сажи являются би- и полициклические ароматические углеводороды, концентра ция которых в исходной фракции должна быть не менее 75—80%. Ароматические концентраты (газойли коксования и каталитиче ского крекинга, масляные экстракты) не удовлетворяют этим тре бованиям. Так, по данным ВНИИ НП [109], каталитические га зойли содержат только 45—50% ароматических соединений, в том числе 20—25% тяжелых ароматических углеводородов, а в легких газойлях, полученных коксованием гудрона, соответственно 18 и 5%. Коксование остаточного крекинг-остатка позволяет увеличить общее содержание ароматических углеводородов в легких коксо вых газойлях до 50—60% при одновременном увеличении содер жания тяжелых ароматических соединений до 30%, но и эти ве личины значительно ниже требуемых норм. Кроме того, сырье для получения сажи ие обладает требуемым индексом корреляции.
В промышленности с целью повышения содержания тяжелых ароматических углеводородов в сырье (индекса корреляции) для производства печной сажи применяют три способа: 1) термический крекинг ароматических концентратов; 2) комбинированный про цесс термического крекинга с коксованием; 3) экстракцию газой лей деструктивных процессов с использованием селективных рас творителей (например, фенола или фурфурола).
Термический крекинг ароматических концентратов на реконст руированных установках двухпечного крекинга является основ ным видом подготовки сырья для производства печных саж, по лучившим развитие на ряде нефтеперерабатывающих заводов в- начале 70-х годов. При наличии на заводе коксовых установок к ароматическим концентратам добавляют коксовые газойли. В ре зультате термодеструктивных процессов доля парафино-нафтено вых и непредельных углеводородов в ароматических концентратах снижается.
* Зеленое масло представляет собой дистиллятную фракцию, выкипающую^ в пределах 200—350 °С, получаемую в процессе пиролиза крекинг-керосина.
Увеличение |
в сырье доли газойлей каталитического крекинга |
и коксования |
крекинг-остатков способствует получению сырья |
для сажи с большим содержанием полициклических ароматиче ских углеводородов, что весьма важно.
Длительный опыт работы установок двухпечного термического крекинга на смеси различных видов сырья показал возможность получения сажевого сырья (газойля термического крекинга) не более 28—32%. Специально поставленные во ВНИИ ИП иссле довательские работы показали, что в крекинг-остатке, отводимом с установки двухпечного термического крекинга, содержится зна чительное количество ароматизированных дистиллятов, вполне пригодных для использования в качестве сажевого сырья. Это объясняется тем, что в испарителе низкого давления, в котором производится подготовка сажевого сырья, при 350—400 °С и дав лении 0,1 МПа не удается извлечь все ценные компоненты. Поэто му некоторые авторы предложили дооборудовать одну из устано вок двухпечного крекинга вакуумной колонной; это позволило получить выход вакуумного газойля почти вдвое больший по срав нению с выходом газойля при атмосферной перегонке.
Материальный баланс установки при получении атмосферного и вакуумного термических газойлей приведен ниже (в % масс.):
|
При проиэиод- |
При производ |
|
стве атмосфер- |
стве вакуум |
|
ного газойля |
ного газойля |
Взято сырья |
100 |
100 |
Получено |
5,0 |
5,0 |
жирный газ |
||
рефлюкс |
1.3 |
1,3 |
бензин |
20,1 |
20,1 |
термический |
24,2 |
53,6 |
зойль . |
||
крекинг-остаток |
48,3 |
19,9 |
потери |
1,1 |
1,1 |
Большая цикличность ароматических соединений предопреде ляет повышенные плотность и вязкость вакуумного газойля по сравнению с атмосферным газойлем. Ниже приводится структур но-групповой состав вакуумного и атмосферного газойлей:
|
|
|
Атмосферный |
Вакуумный |
|
|
|
газойль |
газойль |
Общее число колец в сред |
3,01 |
|||
ней |
молекуле |
2,69 |
||
в том числе |
2,04 |
2,19 |
||
ароматических |
||||
нафтеновых |
0,65 |
0,82 |
||
Содержание углерода, % |
от |
|
||
общего содержания |
75,1 |
77,2 |
||
в |
кольцах . |
|||
|
в том числе |
59,8 |
59,2 |
|
|
в |
ароматических |
||
|
в |
нафтеновых |
15,3 |
18,0 |
в |
свободных и связан |
|
||
ных |
|
24,9 |
22,8 |
|
|
с кольцами цепях. |
Испытание вакуумного газойля, предназначенного для полу чения сажи ПМ-70, показало, что он полностью соответствует техническим условиям.
Комбинированный термический крекинг смеси сырья с коксо ванием образующегося при этом крекинг-остатка является одним из наиболее рациональных методов получения повышенного выхо да сажевого сырья, не требующего дополнительных затрат при наличии в схеме завода вышеуказанных установок. Достоинство метода — одновременное получение сырья для производства сажи, а также нефтяного кокса игольчатой структуры. При этом вари анте термический крекинг смеси дистиллятного сырья проводит ся при обычных условиях, а на коксование направляют дистиллят ный крекинг-остаток, где из него получают газ, бензиновые фрак ции, керосино-газойлевую фракцию (200—500 °С) и кокс.
Экстракция с применением селективных растворителей позво ляет готовить весьма высококачественное сырье для производст ва нефтяного углерода (сажи и пеки); индекс корреляции такого углерода составляет ПО—115. Экстракция фурфуролом на уста новке (пущена в эксплуатацию в 1973 г.) -подвергают смесь га зойлей термического и каталитического крекинга (фракция 270— 420 °С коксуемостью по Конрадсону не более 1,5%, Э=до 3,5%, И„=100). Выход экстракта на исходное сырье составляет 60%.
РЕГУЛИРОВАНИЕ КОЛИЧЕСТВА КОМПОНЕНТОВ С ОПРЕДЕЛЕННОЙ ПРОСТРАНСТВЕННОЙ СТРУКТУРОЙ МОЛЕКУЛ В СЫРЬЕ, ИСПОЛЬЗУЕМОМ ДЛЯ ПОЛУЧЕНИЯ УГЛЕРОДА РАЗЛИЧНОЙ СТЕПЕНИ АНИЗОТРОПИИ
Долгое время термодеструкция в промышленных условиях угле водородного сырья без учета его молекулярной структуры и склон ности к межмолекулярным взаимодействиям приводила к форми рованию коксов нерегулируемой структуры, разнородной по свой ствам массы (смесь коксов изотропной и анизотропной структуры в неизвестном соотношении). Изучению молекулярной структуры сырья опособствовали работы, проведенные Смндович [116]', Гимаевым [30] и автором [112].
Структуру нефтяных углеродов (степень анизотропии) можно регулировать путем составления сырьевых смесей с определен ным соотношением компонентов, имеющих структуры с простран ственным расположением фрагментов молекул и молекул, скон денсированных в двумерной плоскости.
Термодеструкция в жидкой фазе углеводородного сырья со строго регламентированной пространственной ориентацией фраг ментов сложных молекул приводит к формированию первичных ассоциатов и далее кристаллитов углерода с заданными размера ми и степенью упорядоченности. Это и определяет степень анизо тропии получаемых структур углерода и их дальнейшую склон ность к вторичным термодеструктивным процессам в твердой фа зе. Образование структуры наполнителя с высокой степенью ани
зотропии достигается в случае использования в качестве сырья ароматических концентратов типа сажевого сырья и продуктов еще большей степени коиденсированиости (дистиллятных кре кинг-остатков), состоящих из молекул, упорядоченных в двумер ной плоскости.
На основе научно-исследовательских и опытных данных пред ложен ряд вариантов получения нефтяных коксов преимуществен но анизотропной структуры. Одна из таких схем приведена ниже.
Аром атизоваиные |
Термический крекинг |
Сажевое сырье |
|
концентраты |
|||
|
|
Крекинг-остаток дистиллята
Игольчатый |
Сажевое сырье |
|
электродный кокс |
||
|
Вопытно-промышленном масштабе эта схема (без отдельного узла термоконденсации) испытана на одном из НПЗ при работе на малосернистых видах сырья (смесь газойлей коксования и ка талитического крекинга в отношении 1: 1 и смесь газойлей коксо вания, каталитического крекинга и вакуумного газойля в соотно шении 1,5:1,5:1). Судя по результатам термического крекинга га зойлей указанных качеств, лучшие показатели получаются при их термодеструкции в условиях повышенных давлений (на входе и выходе из змеевика соответственно 8,5—11,0 и 5,0—8,0 МПа).
Впромышленных условиях термический крекинг дистиллятных видов сырья (газойль коксования, каталитического крекинга и ва куумного газойля в соотношении 1,5:1,5:1) осуществлялся при давлении на входе в змеевик 2,2 МПа, на выходе— 1,2 МПа при
конечной температуре 502—505 °С. Материальный баланс термичес кого крекинга и коксования сырья приведен ниже:
Выход продуктов (в %) в процессе
Продукты |
термиче |
|
термического |
|
крекинга и |
||
|
ского |
|
коксования |
|
крекинга |
|
на исходное |
|
12 |
8,5 |
сырье |
Газ |
15,1 |
||
Бензин |
17 |
5 ,0 |
1 8 ,8 |
Керосино-газойлевая |
34 |
|
|
фракция |
6 0 ,5 |
5 6 ,5 |
|
Крекинг-остаток |
37 |
— |
— |
Кокс |
— |
2 6 ,0 |
9,6 |