
книги / Нефтяной углерод
..pdfлены в названиях марки сажи. В названиях некоторых саж имеются буквы В или Н, указывающие на структурность саж. Например, сажи ПМ-90В и ПМ-ЗОВ обладают высокими, а ПГМ-ЗОН— низкими показателями структурности. В саже, в зависимости от марки, регламентируется содержание зольных компо нентов (не более 0,05—0,48%), общей серы (не более 1,1%), содержание грита
(остатка после просеивания через сито с сеткой, например |
размерами 0,045 мк |
по ГОСТ 3584—73) — не более 0,08—0,10%. |
упакованном виде. |
Сажи марки ТГ-10 выпускают негранулпрованными в |
Все остальные марки гранулируют и перевозят или в специальных вагонах и автоцистернах, или, упаковывая в мешки, в крытых железнодорожных вагонах, контейнерах и автомашинах, избегая прямого контакта с водой. Поскольку тех нический углерод при 250—440 °С способен к самовозгоранию, необходимо строго соблюдать правила его хранения и транспортирования.
Грубодисперсные системы с небольшой удельной поверхностью можно получить в результате естественного образования (в про цессах коксования) или измельчения крупных частиц. Грубодис персная система, используемая для получения УНС, содержит ча стицы, различающиеся по размеру весьма существенно (от 1 0 мк
до 15—20 мм).
В зависимости от молекулярной структуры нефтяные углероды делят на анизотропные и изотропные; по степени сернистости — на малосернистые (до 1,0% S), среднесернистые (до 1,5% S), серни стые (до 4,0% S), высокосернистые (более 4,0% S); по грануло метрическому составу — на кусковой (фракции выше 25 мм), коксик или орешек (фракции от 6 — 8 до 25 мм) и мелочь (фракции ниже 8 мм); по степени зольности — на малозольные (до 0,5% А), среднезольные (0,5—0 ,8 % А) и зольные (более 8 % А) [1 1 2 ].
Нефтяные углероды могут существенно различаться по адсорб ционной и реакционной способности, по удельному электросопро тивлению (УЭС), структурности (в основном сажи), теплофизиче ским и другим свойствам, что должно быть учтено при использо вании их в различных отраслях народного хозяйства.
В качестве связующих веществ в УНС обычно используют жидкие продукты различной вязкости — каучуки, нефтяные и каменноугольные пеки и др.
Хорошая возможность регулирования пластичности и эластичности нату ральных и синтетических каучуков в процессе их получения и вулканизации делает их незаменимыми видами связующих веществ УНС специального назна чения. Химические и физические свойства различных каучуков (изопреновый, этилен-пропилен-диеновый, хлоропреновый, бутилкаучук, уретановый и др.) из ложены в специальных работах [101] и здесь Яе рассматриваются.
Нефтяные и каменноугольные пеки, являющиеся важной составляющей УНС, принято делить на: а) пропитывающие средства, обладающие высокой прони кающей способностью в поры наполнителя и коксуемостью и низкими темпера турами размягчения (50—70®С по КиС)*; б) связующие вещества, характери зующиеся высокой поверхностной активностью и соответственно адгезионной способностью, коксуемостью, со средними температурами размягчения (70— 120°С по КиС); в) пеки для формирования углеродных волокон с высокими
значениями коксуемости и температурами размягчения (170—200 °С по К,иС).
* Температура размягчения определяется по методу «кольцо и стержень».
Многообразие наполнителей*, различие в их структуре, дисперс ности, степени анизотропии, адсорбционной способности в сочета нии со связующими веществами позволяет получать наполненные системы с заданными эксплуатационными свойствами.
В соответствии с современными представлениями наполненная система на первом этапе получения состоит из трех компонентов: наполнителя, связующего и межфазного продукта (адсорбционно го слоя), образованного при взаимодействии компонентов УНС.
В равновесной идеализированной системе частицы наполнителя равномерно распределены в связующем; при этом свойства систе мы не изменяются. Реальные углеродонаполненные системы, ис пользуемые на практике, заметно отличаются от идеальных компо зиций. В реальных условиях достижение равновесного состояния адсорбционного слоя зависит от смачиваемости наполнителя, ко торая, в свою очередь, зависит от чистоты его поверхности, микро рельефа, величины поверхностной энергии. О достижении равно весного состояния адсорбционного слоя можно судить только после установления равновесного угла смачивания, продолжаю щегося весьма долго.
В углеродонаполненной системе существует два критических состояния связующего, обусловленные разными его свойствами и значительно влияющие на поведение системы.
1.Связующее вещество на поверхности наполнителя находится
вквазитвердом, стеклообразном состоянии. Количество связующе го, расположенного в этом состоянии на поверхности наполнителя,, называют критической концентрацией граничного слоя.
2.Связующее вещество на поверхности наполнителя находится
впластическом состоянии. Предельную концентрацию связующего,, выше которой система начинает течь, называют критической кон
центрацией пластического слоя.
Прочность наполненной системы возрастает за счет адгезион ных сил компонентов УНС до определенного критического значе ния (критическая концентрация пластического слоя).
Граничный и пластический слои обладают сопротивлением сдвиговому усилию и не являются текучими, они сохраняют при данную им форму. Толщина этих слоев не является постоянной даже для одного и того же углерода, на поверхности которого из связующего формируется межфазный продукт. При избытке свя зующего прочность системы снижается. По мере увеличения раст воряющей силы компонентов связующего (путем изменения груп пового состава связующего*, повышения температуры и других факторов) толщина адсорбционного слоя уменьшается, что при водит при изготовлении УНС к меньшему расходу свзующего.
* Здесь и далее под наполнителем понимаются все компоненты, которые вводят в систему для улучшения физико-химических и эксплуатационных свойств УНС.
Наличие в наполнителе пор также может изменить долю свя зующего, адсорбирующегося на его поверхности и повлиять на фи зико-химические свойства углеродонаполненных систем.
Критическую концентрацию пластического слоя можно рассчи тать и определить экспериментально [103]. По Сагалаеву и Симо нову-Емельянову [104], условие, при котором достигается крити ческая концентрация пластического слоя для наполнителя с волок нистой структурой, определяется толщиной пластического слоя б
|
|
|
6 > 0 ,0 7 d + 0,52а |
|
||
где |
d — диаметр |
волокна; а — минимальное расстояние |
между волокнами. |
|||
|
|
|
Л (1-Я .1ф „) |
|
||
|
|
|
а ~ |
МЧ>.. |
|
|
где фи — объемная доля наполнителя. |
|
|
|
|||
|
В общем случае [42] |
в момент |
создания |
пластического слоя |
||
среднюю его толщину бСр можно |
установить |
экспериментально |
||||
|
|
|
* |
|
Ук |
|
|
|
|
ЬсР~ |
5удф |
|
|
где |
VK— критический объем |
пластического слоя; 5 УД — удельная поверхность |
||||
наполнителя; d |
— плотность связующего. |
|
|
Форма частиц наполнителя влияет не только на значение б, но и на прочность углеродонаполненной системы. Известно, что при введении в связующее наполнителя вязкость УНС изменяется в за висимости не только от количества наполнителя, но и от формы его частиц. Вязкость системы тем больше, чем меньше форма наполни теля отклоняется от шарообразной. При волокнистом наполнителе (коксе игольчатой формы) можно получать электродные массы одинаковой пластичности при меньшем содержании коксов, чем в случае частиц нефтяных коксов шарообразной формы.
Вработе [125] приводятся данные о влиянии формы частиц
(К)на прочностные свойства наполненной системы. Установлено, что чем выше в эллипсоидной частице отношение большой полуоси
(Ь)к малой (а) (т. е. /С=б/а), тем выше прочностные свойства углеродонаполненной системы
где оь — предел прочности при растяжении связующего.
Изменяя фактор формы нефтяных углеродов в УНС, можно в широких пределах варьировать коэффициент термического расши рения электродной массы.
Для частиц наполнителя сферической формы (iC=* 1):
Для частиц игольчатой структуры ( / ( > 1 ): |
|
<IK= <JC [l — (l —-57-) /с] |
(6) |
где aKt ая, ас — коэффициенты термического расширения компонентов (углеродо наполненной системы, наполнителя и связующего); VB — объемная доля напол
нителя в смеси.
С увеличением К коэффициент термического расширения мате
риала снижается, что и наблюдается для нефтяных коксов, имею щих игольчатую структуру. Аналогично для обеспечения электроили теплопроводности в наполненной системе более желательно иметь частицы игольчатой структуры с высоким значением К. На пример, при введении частиц меди, у которых отношение длины I к диаметру d(lld)—l( = 2 0 , степени наполнения ею 5% объемы, проводимость полиэтилена возрастает в 1 ,5 раза, а при тех же ус ловиях, но при IJd—bO— в 5 раз. Следует ожидать, что при напол
нений электродных масс углеродными частицами, имеющими повы шенное отношение Цй, многие свойства готовых углеграфитовых
изделий улучшатся.
По мнению Печковской [8 8 ], при добавлении саж в качестве
наполнителей происходит в основном физическое взаимодействие между каучуком и сажей, выражающееся в усилении УНС.
Модуль (М) и прочность (S) вулканизатов при малоактивных
сажах или при низких концентрациях активных саж могут бытьвычислены в зависимости от их объемной доли (Ун) и фактора формы первичных агрегатов (К) следующим путем:
м = м 0(1 + 0,67KV „+ 1 ,m 2vl)
s = So + 50 Ig (1 + 0,67KVH- f 1,62* 21/J)
где M0 и So — модуль и прочность наполненного вулкаиизата.
Аналогично можно рассчитать и другие свойства наполненных систем на первой стадии вулканизации. На второй стадии упрочне ния наполненной системы — при переходе физических связей в хи мические при соответствующей температуре (вулканизация, спека ние) — между молекулами связующего, а также между молекула ми связующего и наполнителя возникают пространственные связи. Молекулярная структура и соотношение компонентов в УНС, а- также соотношение в них физических и химических связей позво ляют определить механические, физико-химические и эксплуатаци онные свойства наполненной системы.
Технологический процесс изготовления УНС в общем виде делится на сле
дующие стадии:
модифицирование поверхности наполнителя (нефтяных коксов) предвари тельным прокаливанием и добавлением к ним ПАВ и при необходимости свя зующего вещества, например, пластификация натурального каучука для лучшегосмешения с наполнителем и другими компонентами (перевод каучука из жест кого состояния в мягкое);
размол и рассев углерода по фракциям;
расчет, дозирование компонентов и формирование УНС; регулирование прочности УНС путем превращения физических связей в
химические (обжиг, вулканизация).
Все указанные стадии осуществляют не всегда. Например, при изготовлении резиновых смесей второй стадии не требуется.
МОДИФИЦИРОВАНИЕ ПОВЕРХНОСТИ НАПОЛНИТЕЛЯ
Для придания нефтяным углеродам соответствующей поверхност ной активности и других свойств их модифицируют (подвергают высокотемпературной обработке). В промышленных условиях для этой цели используют прокаливание. Условия прокаливания нефтя ных углеродов зависят от свойств сырья и назначения УНС. Наи более жесткий режим (1400—1500°С, 0,02—0,07 с) применяют для модифицирования поверхности углерода, особенно при получении активных саж. В последнем случае получение сажи и модифици рование проводят в одну ступень [48, 35].
Если требуется получить углерод с высокой электропровод ностью и с необходимыми теплофизическими свойствами,-то созда ют условия для упорядочения кристаллитов кокса в течение значи тельно большего времени. При этом получение углерода и его про каливание (модифицирование поверхности) целесообразно прово дить в две стадии. Обычно это применяют при получении углерода, используемого в качестве наполнителя электродных масс. Мало сернистые коксы, как правило, прокаливают при мягком режиме с целью удаления летучих веществ и обеспечения необходимой ско рости структурирования (1000—1400 °С, 24 ч). Жесткий режим (1400— 1500 °С, 1—2 ч) обеспечивает также удаление серы из неф тяных углеродов.
Одно из важных требований, предъявляемых к электродной продукции, — обеспечение достаточной ее механической прочности (20,0—50,0 МПа). Прочность на раздавливание нефтяных коксов, получаемых в кубах и на установках замедленного коксования (4,0—15,0 МПа), в несколько раз ниже требуемой. Это обуслов лено несовершенством структуры кокса — высокой его пори стостью.
Исследования показали, что с увеличением размера кубиков нефтяного кокса с 1 0 до 80 мм предел прочности на раздавливание
снижается в 1,5 раза. Это объясняется повышением с увеличением размера кусков дефектности.
Зависимость прочности средней пробы кокса замедленного кок сования от размера кусков в первом приближении оценивается выражением:
П =58,5* а0.2- где П — прочность кокса, МПа; а — длина ребра коксового кубика, м.
По Ребиндеру, наиболее обнадеживающий путь повышения прочности любых материалов — разрушение твердого тела по всем дефектам. Прочность мелкйх частиц таких же размеров, .как и рас
стояния между дефектами, всегда выше, чем массивных кусков из того же материала, у которых слабых звеньев намного больше. Для получения монолита необходимой формы и прочности мелкие частицы в дальнейшем скрепляют при помощи специальных свя зующих веществ.
Для получения анодов и электродов исходным сырьем обычно служит крупная фракция (25—200 мм) нефтяных коксов. По скольку в таком виде коксы не могут быть прокалены на сущест вующих прокалочных агрегатах, их предварительно дробят в щековых или зубчатых дробилках до кусков размером 50—70 мм. При этом 30% и более образуется частиц размером менее 25 мм. Дроб леный кокс прокаливают в специальных печах. Основные требова ния, предъявляемые к печам, — минимальные потери сырья от вторичных реакций в процессе прокаливания; равномерность про каливания кусков кокса по всей массе; возможность прокаливания мелочи (до 6 мм); утилизация тепла отходящих газов и раскален
ного кокса; высокая производительность. Существующие прокалочные печи лишь частично удовлетворяют указанным требованиям. Они предназначены в основном для прокаливания частиц кокса размером более 25 мм.
По принципу действия прокалочные печи делятся на вращающиеся, реторт ные н электрические (электрокальцинаторы).
При производстве анодов для алюминиевой промышленности кокс прокали вают во вращающихся печах (наиболее производительных из всех существую щих). Для получения однородного материала кокс должен находиться в зоне прокаливания длительное время. Это достигается в ретортных печах. При отсут ствии жестких требований к однородности кокса после прокаливания (напри мер, при изготовлении анодной массы на электрометаллургических предприяти ях) используют электрокальцинаторы.
В промышленности наиболее распространены вращающиеся прокалочные печи (рис. 19), которые представляют собой наклонные (на 3—5°) цилиндриче-
Рнс. 19. Вращающаяся прокалочная печь:
/ — бандаж; |
2 — венцовая |
шестерня; 3 — прокалочный барабан; 4 — футеровка; 5 — перед |
|
няя |
головка; |
( — задняя |
головка; 7 — ролики; в —шестерня привода; 9 —выходное отвер |
стие; |
10 — холодильный барабан. |
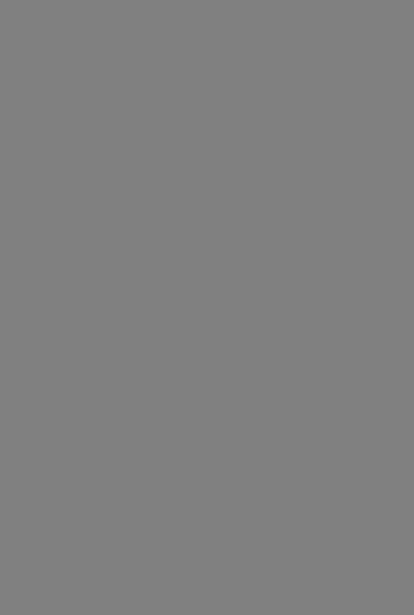
нефтяного кокса (рис. 20). Кокс попадает на поверхность наклонной вращаю щейся печи, где лопатки перемешивают его при такой скорости вращения печи, при которой достигается требуемое время контакта и равномерный нагрев кокса. Конструкция печи обеспечивает сгорание выделяющихся летучих, находящихся выше неокислительной зоны, и количество тепла, необходимого для прокалива ния, что в общем позволяет получить более высокий выход кокса, чем в гори зонтальной вращающейся печи.
Более однородный и лучший по качеству кокс получается после прокали вания в ретортных печах (1100— 1200 °С; 24 ч). Прокалочная ретортная печь может быть прямо- и противоточной. Она состоит из 8—20 вертикальных реторт,
обогреваемых с внешней стороны дымовыми газами [165]. Нормальная произво дительность одной реторты 60—65 кг/ч нефтяного кокса и до 80 кг/ч антраци та. Обычно производительность противоточных реторт примерно на 15—25% выше, чем прямоточных. Тепловой к.п.д. реторт незначителен и составляет 30— 50%. Поэтому такой способ облагораживания малоэффективен и не может быть рекомендован для крупнотоннажного производства, например производства ано дов для алюминиевой промышленности.
В электрокальцииаторах (рис. 21) кокс прокаливают путем пропускания электрического тока. Одно из основных требований, предъявляемых к сырью электрокальцинаторов,— постоянство гранулометрического состава (10—25 мм). Это необходимо для обеспечения относительного постоянства температурного ре жима прокаливания и получения более равномерно прокаленного материала. При разнородном гранулометрическом составе коксов мелкие фракции из-за вы сокого электросопротивления прокаливаются недостаточно и неравномерно.
В процессе прокаливания и охлаждения углеродистые материа лы, в особенности во вращающихся печах, в значительной степени измельчаются (табл. 8).
Качество прокаленного кокса контролируют измерением истин ной плотности, удельного электросопротивления и адсорбционной способности. В соответствии с требованиями потребителей истин ная плотность прокаленного кокса должна быть не ниже (в кг/м3) :
Для |
анодов . |
.продукции |
2030 |
Для |
графитированной |
2080 |
|
Для |
электродов крупного |
сечення |
2100 |
Удельное |
электросопротивление |
не |
должно |
превышать |
|||
600 Ом-мм2/м. |
|
|
|
|
|
|
|
ТАБЛИЦА 8. Измельчение углеродистых материалов |
|
|
|||||
в процессе прокаливания и охлаждения (в %) |
|
|
|
||||
Сернистого нефтяного кокса,, полученного при S00 °С |
Пекового кокса, полученного |
||||||
|
|
|
|
|
|
при 950—10S0 °С |
|
Размеры гра |
|
|
после прокали- |
|
|
|
после прока |
нул, мм |
|
|
|
после |
|
||
до прока |
- |
- вания во вра |
до прока |
Д О |
ливания во |
||
ливания |
щающихся |
ливания |
прокали |
прокаливания |
вращающихся |
||
|
|
|
печах н охлаж |
|
вания |
|
печах и |
|
|
|
дения |
|
|
|
охлаждения |
50 |
10,2 |
|
0 |
39,0 |
0 |
0 |
0 |
5 0 -2 5 |
52,7 |
|
4,5 |
30,0 |
40,0 |
50,0 |
68,0 |
25— 15 |
11,2 |
|
53,0 |
7,5 |
25,3 |
13,0 |
15,0 |
15—4 |
15,0 |
|
35,0 |
7,6 |
21,5 |
12,0 |
8,0 |
< 4 |
10,9 |
|
7,5 |
15,9 |
13,2 |
25,0 |
9,0 |
|
|
Лабораторные образцы |
Промышленные образцы |
||||
Нефтяной кокс |
адсорбция |
кислород* |
отношение |
адсорбция |
кислород |
отношение |
|
иска |
ные груп |
пека |
ные |
||||
|
|
на коксе, |
пы, |
А/К. |
на коксе, |
группы, |
А/К. |
|
|
мг/г, А |
ммоль/г, К |
ыг/ммоль |
мг/г, А |
ммоль/г, К |
мг/ммоль |
Сернистый |
30 |
1,02 |
29,4 |
34 |
1,11 |
|
|
из |
дистиллятного |
30,6 |
|||||
сырья |
47 |
1,16 |
40,5 |
69,5 |
|
51,8 |
|
из. |
остаточного |
1,34 |
|||||
сырья |
35,0 |
1,04 |
33,6 |
39,0 |
1,19 |
32,8 |
|
Малосернистый |
|||||||
Пековый |
23,0 |
0,78 |
29,4 |
32,0 |
0,98 |
32,6 |
Адсорбционную способность прокаленных коксов изучал
А.Ш. Ишкильдин по модифицированной методике, предложенной
А.Ф. Красюковым [64]. Он убедительно показал влияние на ад сорбционную способность прокаленных коксов не только природы исходного сырья, режима прокаливания, но и среды, в которой его прокаливали. Во всех случаях адсорбционная способность коксов
промышленного прокаливания была выше, чем коксов, прокален ных в тех же условиях в лаборатории в инертной среде.
Активированные в промышленных условиях поверхности коксов обладают повышенным содержанием кислородных групп и боль шей удельной поверхностью, чем образцы, прокаленные в печи Таммана в лабораторных условиях (табл. 9).
Удельные адсорбционные способности — количество адсорбиро ванного на поверхности кокса пека (в мг), приходящегося на 1 ммоль'кислородных групп'единицы массы кокса (A/К) для ла бораторных и промышленных образцов коксов близки; это свиде тельствует о том, что активность поверхности коксов придают в основном кислородные группы. Отличие адсорбционной способно сти лабораторных и промышленных образцов ново-уфимских кок сов из сырья остаточного происхождения объясняются, по-види мому, природой исходного сырья и неодинаковой глубиной обессе ривания коксов при прокаливании различными способами.
С поверхностной активностью кокса (как и следовало ожидать) коррелируется смачиваемость поверхности при обработке ее ка менноугольным пеком (рис. 22).
Поверхность коксов можно модифицировать не только подбо ром сырья коксования, режима и среды прокаливания кокса, но и изменением поверхностной энергии системы в результате обра ботки коксов поверхностно-активными веществами (ПАВ). С по вышением концентрации ПАВ до 1,0% масс, удельная адсорбция связующего на поверхности кокса снижается в три раза. Молеку лы ПАВ, адсорбируясь на активных центрах кокса, и снижая его поверхностную энергию, изменяют не только адсорбционную спо-
Рис. 22. Смачиваемость при 130°С каменноуголь ным пеком прокаленных коксов:
/ - ФНПЗ; 2 - НУ НПЗ; 3 - пековый.
собность кокса, но и прочность твердых материалов (эффект Ре биндера). Силы притяжения, возни кающие между ионами противопо ложных поверхностей трещин, ко торые появляются при механиче ских воздействиях на кокс, в при
Температура прокаливания, °С сутствии ПАВ ослабляются (по
верхности пассивируются), в резуль тате чего величина энергии, которая препятствует распростране нию трещин, снижается. Изменение свойств обессеренного нефтя ного кокса при размоле подтверждается изменением удельного расхода связующего на образование пластического слоя и прочно сти кокса при добавлении даже небольшого количества ПАВ. Влияние ПАВ на расход связующего и прочность нефтяного кок са показано в табл. 10.
РАЗМОЛ И РАССЕВ НЕФТЯНОГО КОКСА ПО ФРАКЦИЯМ
Кокс дробят и измельчают для получения порошка широкого гра нулометрического состава со строго определенным соотношением выходов отдельных фракций. В дальнейшем из этих фракций со ставляют наполнитель, предназначенный для изготовления элект родной массы. Крупные коксовые частицы составляют скелет — ос нову электродной продукции, более мелкие заполняют межкуско вое пространство.
Измельчение заключается в разрушении твердых тел в резуль тате воздействия механических усилий; процесс осложняется аг регацией дисперсных материалов и деформацией мелющих твер дых тел. При измельчении на частицы менее 15 мк удельная по-
ТАБЛИЦА 10. Влияние ПАВ на расход связующего и прочность нефтяного кокса при его размоле в лабораторной шаровой мельнице
Продолжитель ность измельче ния. ч
S i , -
U а и
2 5 - x'gS
с- — U
§ 5 2 ^
О я о £ c a s o
Без ПАВ
расход свя зующего. % масс, на кокс |
удельный рас ход связую щего. % масс*г/см2 |
оi Я
ВS 2
№
и-Э-s 5-
С 0,01% масс. ПАВ (СКТН)
кокса, |
свя |
связую |
-масс.г/см2 |
мм,0,05 |
поверхность раздроблен ного СМ2/Г |
расход зующего,% масс,коксна |
рас |
|
ме |
удельный ход щего, % |
содержание фракции нее % |
1 |
2460 |
38,6 |
0,01569 |
20,0 |
3070 |
38,0 |
0,01237 |
3 1,0 |
2 |
3140 |
40,1 |
0,01277 |
44,5 |
3950 |
39,2 |
0,0992 |
5 3 ,0 |
3 |
3610 |
40,7 |
0,01127 |
64,0 |
4640 |
4 0 ,4 |
0,0870 |
74,5 |
4 |
4480 |
41,5 |
0,00926 |
89 ,0 |
5460 |
4 1 ,3 |
0,0756 |
9 5 ,0 |