
книги / Нефтяной углерод
..pdfТАБЛ И Ц А 17. Свойства сырых коксов, полученных на установках замедленного
коксования из разного сырье
Гудрон котуртепин- |
Гудрон шнрванской |
Крекинг-остаток |
Гудрон и асфальт |
Крекинг-остаток |
|||
коробковскнх и |
смеси туркменских |
смеси нефтей типа |
|||||
ской нефти |
нефти |
жнриовских |
н ферганских |
ромашкниской |
|||
Показатели |
|
|
|
нефтей |
нефтей |
|
|
|
|
|
|
|
|
|
|
>25 мм |
<25 мм |
>25 мм |
<25 мм |
>25 ММ <25 мм |
>25 мм |
<25 мм |
>25 мм <25 мм |
Выход фракций, масс. % |
41,5 |
58,5 |
40,0 |
60,0 |
35,7 |
64,3 |
45 |
55 |
45 |
55 |
|
Влажность, масс. % |
2,5— 12,5 5,0— 13,0 2,5—12,0 2,5— 16,0 |
8,0 — 16 7— 18,0 |
5,6— 12 |
5—25,0 |
2— 13 |
6,21 |
|||||
Содержание серы, масс. % |
0,52 |
0,53 |
0,55 |
0,57 |
1,20 |
1,37 |
0,90 |
0,93 |
4,0 |
4,07 |
|
Выход летучих веществ, масс. |
8,7 |
10,2 |
8,0 |
9,5 |
6,3 |
9,3 |
7,0 |
8,5 |
6,8 |
7,2 |
|
% |
|
|
|
|
|
|
|
|
|
|
|
Механическая прочность, Н/см2 |
570 |
400 |
460 |
350 |
460 |
280 |
— |
— |
600 |
530 |
|
Кажущаяся |
плотность, кг/м3 |
1000 |
940 |
1020 |
1000 |
— |
— |
1060 |
1030 |
920 |
930 |
Пикнометрическая |
1390 |
1390 |
1420 |
1420 |
1400 |
1400 |
1420 |
1420 |
1380 |
1400 |
|
к г / м 3 |
|
|
|
|
|
|
|
|
|
|
|
Пористость, |
% |
28 |
32 |
28 |
30 |
— |
— |
25,0 |
27,0 |
33,0 |
23.0 |
Зольность, |
% |
0,43 |
0,50 |
0,25 |
0,47 |
0,27 |
0,34 |
0,38 |
0,42 |
0,46 |
0,49 |
тиллята, его коксуемости и содержания в нем серы. Выход продук тов разложения в этот период относительно мал.
В дальнейшем, по мере накопления в реакторе жидкой части загружаемого продукта, подаваемый свежий продукт проходит че рез слой жидкости и в жидкой фазе начинают интенсифицировать ся деструктивные процессы. В результате плотность и вязкость дистиллята уменьшаются. Одновременно возрастают плотность и вязкость остатка в жидкой фазе вследствие увеличения доли про<- дуктов, склонных к структурированию, прежде всего асфальто смолистых веществ.
Вначальный момент в реакторе образуются две фазы: паровая
ижидкая, разделенные прочным поверхностным слоем, который обладает специфическими свойствами. Эти свойства определяются структурой и концентрацией поверхностно-активных веществ и тем пературой системы. Регулируя указанные параметры, удается из
менять структурно-механическую прочность поверхностного слоя и влиять на технологию процесса коксования. Обычно газы и пары (продукты деструкции), прорывающиеся через этот слой, вызыва ют пенообразоваиие. Если в жидкой части загрузки реактора обра зуется пена достаточно прочная, то при бурном испарении или вы делении газов в случае резкого изменения рабочих условий коксо вания (например, давления) *может произойти выброс большого количества жидкой части загрузки из реактора в колонну.
По мере достижения пороговой концентрации асфальтенов про исходит расслоение и они выделяются в отдельную фазу в виде ассоциатов. Структура ассоциатов, формируемая за счет сил меж молекулярного взаимодействия, в дальнейшем определяет структу ру твердого вещества. На этой стадии система переходит в пла стическое состояние.
На образование и степень упорядоченности ассоциатов влияет не только природа сырья, но и гидродинамические условия в реак торе. После выделения асфальто-смолистых веществ в отдельную фазу ассоциаты начинают быстро взаимодействовать друг с дру гом, что сопровождается образованием твердой фазы и сильным выделением газов. Ассоциаты сращиваются друг с другом по ме сту свободных валентностей в сложных радикалах; в дальнейшем разрозненные ассоциаты химически сшиваются таким образом в прочную сплошную массу. Выделяющиеся газы встречают при вы ходе тем большее сопротивление, чем выше вязкость пластической массы. В соответствии с этим в слое развивается давление; оно и является той силой, которая вызывает вспенивание, а иногда и выбросы продукта.
Учитывая сказанное, следует ожидать максимально возможно го вспенивания или выброса в момент образования коксового пи рога (массива) и залпового» выделения газов. Действительно, на пример, при коксовании крекинг-остатка наибольшее число выбро сов наблюдается через 2,5 ч после начала процесса, а при работе на полугудроне — через 8 —9 ч (при 490 °С), т. е. в моменты обра-
зовання первоначального коксового массива и значительного вы деления газов. Подача в этот момент поверхностно-активных ве ществ в реактор (например, силиконов) позволяет сильно ослабить поверхностную прочность слоя и снизить давление, развиваемое под слоем, а также устранить возможность выброса продукта из реактора в колонну.
После образования на начальной стадии коксового массива ос новные показатели процесса стабилизируются.
Очевидно, стабилизация основных физико-химических свойств дистиллята через определенное время после начала коксования свидетельствует о переходе процесса из первой стадии, соответст вующей первому этапу в кубах, во вторую, представляющую собой непрерывное коксование. Вторая стадия отличается от предыдущей тем, что в ней одновременно, с относительно большими скоростя ми, протекают процессы распада, конденсации и уплотнения угле водородов коксуемого! сырья. Эти процессы сопровождаются непре рывным наращиванием коксового слоя (выше которого располо жен слой вспученной массы коксующегося остатка) и равномерным выделением из реактора паров коксового дистиллята и газа. К на чалу второй стадии устанавливается равновесие в тепловом режи ме процесса и в соотношении отдельных составляющих коксую щейся массы. После отключения камеры от потока сырья (третья стадия) непрерывность процесса нарушается. В это время тепло в реактор не поступает, коксование затормаживается.
На практике на разных стадиях образуются разные слои кокса: нижний — на начальной стадии коксования (периодический про цесс) ; средний — на второй стадии (непрерывный процесс) и верх ний— после отключения камеры от потока сырья (также периоди ческий процесс). Разнородность в свойствах кокса по высоте реак ционной камеры можно значительно устранить, вводя в камеру дополнительное количество тепла извне (например, введением го рячих газов, перегретого пара, горячего потока нефтепродуктов).
На неоднородность качества кокса влияет и переменный тепло вой эффект процесса в- течение цикла коксования. Специальные исследования показали, что суммарный тепловой эффект реакции испарения, коксования и тепловых потерь по высоте не постоянен. Так, при работе на крекинг-остатке ромашкинской нефти он колеб лется от 294 до 210 кДж/кг сырья [ 1 1 2 ]. Большие значения тепло
вого эффекта наблюдаются в начале коксования (момент, когда происходит интенсивное испарение фракций сырья и повышенное образование газа и бензина). Затем, по мере установления посто янства выхода этих продуктов и увеличения доли процесса кон денсации составляющих остатка, тепловые затраты снижаются до минимального значения. Почти совпадающие, с приведенными ре зультаты по тепловому эффекту коксования в лабораторных усло виях были получены в работе £75]. В процессе коксования при 450 и 4 7 5 °С гудрона ромашкинской нефти { d f =1,007, СКОир— 18.2%,
содержание фракции до 500°С — 20,4%) общий расход тепла на
процесс испарения и деструкции составил 300—320 кДж/кг сырья. Из них около Уз тепла было израсходовано на испарение, а остальное количество (189—210 кДж/кг) — на реакцию.
Вполне понятно, что тепловой эффект существенно зависит от качества сырья, от его состава. Чем больше ароматизировано сырье, тем больше в нем коксообразующих элементов и чем благо приятнее условия для получения выхода кокса, тем выше доля экзотермических реакций. Это видно из данных, приведенных ниже [126]:
Сырье для коксования |
|
Характе |
Суммарный |
Выход |
Механи |
||
|
|
|
|
ризующий |
тепловой эф |
летучих |
ческая |
|
|
|
|
фактор |
фект процесса, |
веществ, |
прочность, |
|
|
|
|
|
кДж/кг |
% |
Н/смЗ |
Гудрон |
мангышлак- |
0,9337 |
12,1 |
—231 |
9— 10 |
300—400 |
|
ской |
нефти . |
|
|||||
Гудрон |
ширванской |
0,9688 |
11,7 |
— 186 |
8 - 9 |
500—600 |
|
нефти |
|
||||||
Гудрон котур-тепнн- |
0,9639 |
|
— 188 |
7— 8 |
700—800 |
||
ской |
нефти |
|
|
||||
Крекинг-остаток |
ко |
|
|
|
|
|
|
тур-тепинск он |
неф |
0,9690 |
11,3 |
- 1 1 9 |
7—8 |
|
|
ти |
. . |
. |
|
||||
Крекинг-остаток бит- |
0,9559 |
|
— 102 |
6—7 |
— |
||
ковской нефти |
|
1 U |
При коксовании высокопарафинистого мангышлакского гудро на перепад температур между низом и верхом камеры равен 6 0 °С, т. е. он в два раза больше, чем при коксовании крекинг-остатка битковских нефтей. При низкой температуре верха реактора (420— 425 °С) получается кокс пониженного качества (высокий выход ле тучих и низкая механическая прочность). При работе на сырье первичного и вторичного происхождения (крекинг-остаток) тепло вые эффекты сильно различаются, так же, как и перепад темпера тур в реакторе. В некоторых пределах это позволяет регулировать качество кокса, получаемого в реакторе.
Неравномерность процесса коксообразования сказывается не только на послойном отложении кокса и качестве дистиллятов и газов, покидающих камеру, но и на качестве керосино-газойлевой фракции (КГФ), выводимой с установки [76].
На рис. 55 показаны кривые изменения свойств КГФ за цикл работы установки замедленного коксования на смеси, состоящей из крекинг-остатка мангышлакских нефтей и экстракта процесса дуосол (3 :1 ).
На характер изменения свойств КГФ на первом и третьем эта пе коксования оказывает влияние также подключение на поток и отключение с потока соседних камер. Это обстоятельство должно быть учтено, например, при подаче депрессора на поток (при полу чении профилактических средств специального назначения), ко личество которого должно регулироваться не только в зависимости от количества КГФ, но и от ее качества.
рис, 65. Изменение свойств керосино-газойле- воА фракции эа цикл коксования.
Описанные этапы формирова ния коксового массива, их дли тельность, физико-химические свойства кокса, степень его неод нородности сильно зависят от па раметров процесса коксования, прежде всего от температуры. При низкой температуре коксова ния из-за повышенной прочности пластической массы и меньшей скорости выделения газов и па ров в коксующейся массе обра зуются крупные пузыри. После затвердевания такой системы по лучается кокс крупнопористой структуры. При этом некоторое
вколичество летучих (непрококсованная часть загрузки) остается
’в пластической массе в процессе ее затвердевания, в результате чего в готовом коксе возрастает содержание летучих. При повыше нии темпреатуры коксования основные процессы распада молекул протекают, очевидно, до наступления пластического состояния, когда образующиеся пары и газы легко разрывают поверхностный слой. Поэтому количество пузырьков в момент затвердевания меньше, чем при низкой температуре, в результате чего кокс полу чается менее «пористым и с меньшим выходом летучих.
Когда концентрация ассоциатов и расстояние между ними до стигают определенной величины, они под действием сил межмоле кулярного взаимодействия сращиваются. Чем ниже температура процесса, тем толще сольватный слой между ассоциатамн, тем труднее они сращиваются и тем больше времени требуется для процесса коксования. От числа и природы связей, возникающих между ассоциатамн и внутри них, зависят свойства получаемого кокса. По мере повышения температуры коксования возрастает
доля химических связей вследствие уменьшения числа нежестких ван-дер-ваальсовых и водородных связей. Поскольку энергия взаимодействия последних на один — два порядка ниже, чем у химических связей, структура кокса упрочняется.
Умеренные температуры коксования (500^505 °С) в «толстом слое» (по всей пластической массе) способствуют слипанию ассо циатов в сплошную прочную массу. При температурах выше 505 °С толщина адсорбционного слоя мала, вследствие чего связывающего материала недостаточно для сшивания ассоциатов в сплошную массу, и коксование может завершиться на поверхности разрознен ных частиц (автономное коксование). По мере подачи сырья на
этих частицах нарастает коксовый слой, в результате чего куски кокса получаются различной, преимущественно округлой формы.
Например, в |
случае замедленного |
коксования крекинг-остатка |
(dl° = 1,020) |
при температуре около |
505 °С в реакторе получается |
смесь разрозненных коксовых шаров различных размеров (от 1 до '1 0 0 мм) или шаров, соединенных друг с другом в виде гроздьев
винограда. При дроблении гроздьев отчетливо видны поверхности их раздела.
При температурах, намного превышающих 505 °С, процессы распада и конденсации составляющих жидких остатков значитель но ускоряются, коксование происходит на поверхности коксовых частиц без их слипания в течение относительно малого времени. Это обстоятельство является наиболее важным фактором, позво ляющим сравнительно просто оформлять технологические схемы непрерывного коксования на гранулированном и порошкообраз ном теплоносителях.
При непрерывном коксовании нефтяных остатков (в тонком слое) вследствие расхода тепла не только на проведение реакции и компенсацию тепловых потерь, но и на догрев сырья с 380—410 до 510—520 °С удельный расход тепла значительно больше, чем при замедленном коксовании в необогреваемых камерах, и составляет 672—838 кДж/кг сырьевой загрузки реактора. В связи с этим в систему необходимо подавать значительное количество тепла из вне. Установлено, что устойчивый ход процесса обеспечивается при массовом соотношении теплоносителя и сырья 7—8 :1 в случае по рошкообразного теплоносителя и 12—14: 1 в случае гранулирован
ного. При одних и тех же температурах время, требуемое для за вершения коксования в тонком слое, значительно меньше, чем при коксовании в необогреваемых камерах.
Рассмотренный механизм коксования показывает, что на про цесс влияют различные факторы: химический состав сырья; склоиность к межмолекулярным взаимодействиям, температура входа вторичного сырья в реактор; длительность пребывания продуктов в реакторе, давление в зоне реакции; коэффициент рециркуляции и др. Влияние этих факторов подробно описано в работе [112].
ГЛАВА VI
НАУЧНЫЕ ОСНОВЫ ОБЛАГОРАЖИВАНИЯ НЕФТЯНОГО УГЛЕРОДА
Нефтяные углероды (нефтяные леки, коксы и сажи) можно ис пользовать в народном хозяйстве в сыром виде и после «предвари тельного их облагораживания. Некоторые сорта нефтяных пеков после их формования должны с целью получения конечного про дукта пройти стадию карбонизации и графитации. При использо вании нефтяного кокса в электродной промышленности (произ водство электродов, конструкционных материалов) он должен пройти стадию прокаливания при 1100—1400 °С, в результате че го упорядочивается его структура, увеличивается тепло- и элект ропроводность, уменьшается содержание неуглеродных элементов, регулируются и улучшаются «поверхностные и другие свойства.
Для удаления из кокса гетероэлементов требуются более жест кие условия его обработки. Так, температура обессеривания сер нистых коксов находится в пределах 1400—1600 °С. Коксы с вы сокомолекулярной упорядоченной структурой и специального ка чества получают с помощью графитации при 2200—2800 °С — •превращением кристаллитов двумерной упорядоченности в кри сталлы трехмерной упорядоченности (графит). Поверхностную энергию и другие свойства сажи регулируют в процессе ее получе ния изменением температуры (1200—1500 °С) и длительности про каливания.
При всех способах облагораживания нефтяного углерода про текают сложные физико-химические процессы, изучение механиз ма и кинетики которых позволит научно обоснованно подходить к выбору сырья, технологических режимов облагораживания неф тяного углерода и активно влиять на качество готовой продукции.
ТЕРМОДИНАМИКА ПРОЦЕССОВ ОБЛАГОРАЖИВАНИЯ НЕФТЯНОГО УГЛЕРОДА
В ходе процесса облагораживания нефтяной углерод проходит че рез метастабильные состояния, стремясь к достижению равнове сия. Исследованию условий, при которых углеродистые материалы могут переходить самопроизвольно из одного состояния в другое, посвящены работы [168, 137, 138, 20, 127]. В отличие от инди видуальных углеводородов (см. с. 156) изобарно-изотермный по тенциал (AGJ в процессе облагораживания разновидностей угле родов изменяется по сложной зависимости из-за структурных пре вращений, происходящих в их массе яри деструкции.
Шулепов [137] «приводит энергетическую диаграмму, на кото рой доказано изменение тепловых эффектов и кажущихся эиер-
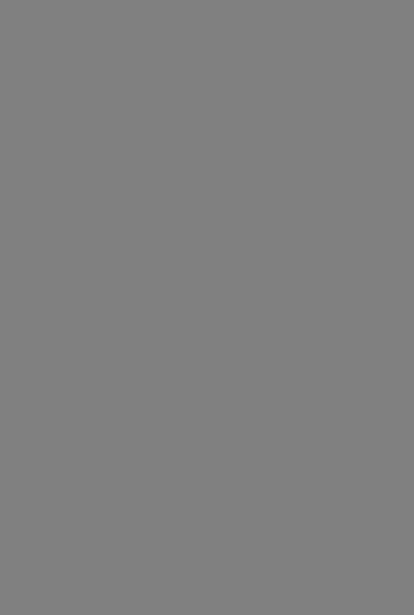
Рис. 57. Зависимость |
изобарно-изотермических |
потенциалов |
(AG) |
углеграфитового ве |
щества от температуры: |
|
|
для графита; 3 — из |
|
/-изменение ДО для |
углеграфитового вещества; 2 — изменение ДО |
|||
менение ДО для прокаленного нефтяного кокса; |
4 — разность |
изменений ДО в процессе пре |
||
вращения нефтяного кокса в графит. |
|
|
|
ную зависимость разностей изобарно-изотермических потенциалов графитируемого тела в процессе превращения* прокаленного неф тяного кокса в графит, можно сделать следующие выводы.
При температурах .прокаливания и выше (1500—2300 °С) неф тяные коксы не могут переходить самопроизвольно в графит, так как в этом интервале знак при AG всегда положителен, т. е. в этих
условиях нефтяной углерод более устойчив, чем графит. При тем пературах около 2 0 0 0 К термодинамически возможен самопроиз
вольный переход нефтяного углерода в промежуточную структуру, когда знак при AG имеет отрицательное значение (кривая 4). Про
цесс графитации термодинамически возможен при обычном дав лении и температурах выше 2600 К, когда кривая 4 пересекает
ось абсцисс (пунктирная линия) и разность изотермических потен циалов кокса и графита становится отрицательной.
Шулепов и Ярмочкина [138]!, базируясь на структурных пре вращениях нефтяного углерода, сопровождающихся на разных стадиях выделением и поглощением энергии, а также скачкооб разным изменением удельных объемов, характеризуют -процесс облагораживания нефтяных коксов как размытый фазовый пере ход первого рода.
ТЕРМОДЕСТРУКТИВНЫЕ ПРЕВРАЩЕНИЯ НЕФТЯНОГО УГЛЕРОДА
Термодинамические данные, как известно, не связаны непосредст венно с механизмом и кинетикой химико-технологических процес сов, в том числе и процессов облагораживания нефтяных углеро
дов. Для понимания путей расчета скоростей процесса облагора живания нефтяных углеродов необходимо знать о молекулярных и межмолекулярных изменениях, происходящих в нефтяном угле роде, о внутреннем сопротивлении системы, не имеющей термоди намического запрета для протекания процесса.
В соответствии с представлениями о структуре нефтяного уг лерода, изложенными на с. 148, и о неравномерности связи между атомами в кристаллитах, в процессе термодеструкции следует ожидать в первую очередь избирательного отщепления боковых структурных групп с образованием свободных радикалов различ ной активности и соответственно реакционной способности. Изме нение количества свободных радикалов в процессе превращения нефтяных остатков в нефтяной углерод подробно изучено в рабо те [30]. Показано, что концентрация ПМЦ на 1 г коксующейся
массы возрастает по мере перехода масел в асфальтены при уве личении температуры, длительности термодеструкции и измене нии других факторов.
Влияние температуры и длительности коксования на концент рацию ПМЦ в коксующейся массе (деасфальтизате) показано на рис. 58. Наличие относительного постоянства концентрации ПМЦ в температурном интервале 440—460 °С объясняется, по-видимому, интенсивными межмолекуляриыми взаимодействиями на этом участке, приводящими к формированию мезофазы и сопровожда ющимися интенсивной рекомбинацией свободных радикалов.
При данной температуре с увеличением длительности термо деструкции концентрация ПМЦ повышается неравномерно. Осо бенно резко (тем резче, чем выше заданная температура) возра стает концентрация ПМЦ в начальной стадии, затем скорость это-
Температура, °С
Рис. 58. Влияние условий коксования на концентрацию ПМЦ в коксующейся массе (деасфальтиэатс).
Длительность кохсования (в мин): 1 — 60; 2 — 90; 5 — 120.
Рис. 59. Плотность различных нефтяных коксов:
/ — из крекинг-остатка грозненской малосернистой нефтесмеси; 2 — из крекинг-остатка туймазинской сернистой нефтесмеси; 3 — пиролизный коке.