
книги / Перспективные композиционные и керамические материалы
..pdfций Al2О3, предел прочности полученного волокна составляет 2100 МПа, модуль упругости 175 ГПа, плотность 3,15 г/см3.
Главным преимуществом этого метода является его энергоэффективность: процессы получения золя и формование композитов протекает при комнатной температуре и не требует постоянного нагрева шихты до температуры, превышающей 2000 °С. Метод позволяет контролировать состав, структуру волокон на стадии приготовления золя. Так, можно задавать предпочтительную линейную ориентацию уже на стадии золя, что отражается на механо-прочностных характеристиках волокна. Гомогенность формуемой субстанции позволяет контролировать размер и форму кристаллитов, стехиометрию и морфологию волокон и определяет узкое распределение волокон по диаметру. Недостатки метода – временная и температурная нестабильность золя – устраняются введением различных добавок.
Всоответствии с другой, пленочной технологией получения волокон оксидов исходный материал получают растворением соли металла
вкарбоновой кислоте (уксусной, муравьиной, лимонной). Раствор выливают на поверхность стекла и нагревают до 80 °С. Полученный при высыхании раствора гель рвется на полоски толщиной в несколько микрометров, шириной в 2–3 раза больше толщины и длиной до 30 мм. При нагреве волокон до 1200 °С происходит выгорание органических веществ и превращение материала в оксидную керамику. Этим методом получают волокна оксидов и их смесей толщиной 0,5–5 мкм, шириной 50–500 мкм и длиной до 40 мм. Недостаток процесса – невозможность получения волокон цилиндрической формы и непрерывных волокон.
Вряде случаев преимущества имеет метод пропитки волокнистых органических полимеров солями металлов. В качестве полимерного во-
локна используют вискозу, хлопок, шерсть, рами, ацетат целлюлозы и др. Оно может представлять собой как штапельное и непрерывное волокно, так и продукты переработки последнего: ткань, ровинг, канат
и др. Пропитку осуществляют погружением полимерного волокна в раствор соединения металла, чаще всего соли, реже − продуктов ее гидролиза. Время пропитки зависит от концентрации соединения метала и типа пропитываемого изделия. После сорбции солей волокна нагреваются для удаления органического несущего материала и других летучих компонентов, и оставшийся скелет из оксида металла консолидируется спеканием. Данный метод позволяет получить поликристал-
151
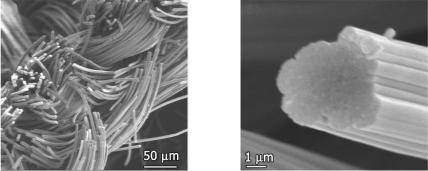
лические волокна целого ряда оксидов (Al, Zr, B, U, Ti и др.) в промышленных масштабах – Al2O3, ZrO2 (рис. 5.6). Отметим, что обжигом в восстановительной среде пропитанных полимерных волокон можно получить и карбидные волокна, например волокна карбида кремния.
а |
б |
Рис. 5.6. СЭМ-изображения волокон производства «Zircar Zirconia»
Метод формования волокон из расплавов не получил широкого распространения. Действительно, энергетически крайне неэффективно и аппаратурно лимитировано получение волокон, включающее плавление оксидов. Необходим поиск решений для плавления столь высокотемпературной шихты. Перспективным в этом смысле может стать плавление токами высокой частоты в индукционных печах. Метод имеет и важное технологическое преимущество: меньшее число стадий – получение расплава и его формование, не требуется высокотемпературная термообработка волокон на последней стадии, как в золь-гель процессе.
В Научном центре порошкового материаловедения метод получения волокон различной длины из базальта и на основе диоксида циркония методом лазерной экстракции из расплавленной капли. Для получения волокон была создана экспериментальная установка, состоящая из инфракрасного лазера, системы поворотных зеркал и объектива для транспортировки лазерного луча к месту нагрева и его фокусировки, координатного стола, устройства для вращения и подачи образца, медного диска-кристаллизатора.
Образец из керамического материала закрепляется вертикально в патроне, горизонтальный луч лазера фокусируется на нижнем конце образца. К капле расплава снизу подводится вращающийся дисккристаллизатор, при соприкосновении его с каплей расплав тонким
152
слоем намораживается на кромку диска, и под действием центробежной силы происходит отрыв закристаллизовавшегося волокна. Непрерывные волокна на основе диоксида циркония имели прочность на разрыв 1,4 ГПа, волокна из базальта диаметром 56–62 мкм имели прочность на разрыв до 0,3 ГПа и аморфную структуру.
Одним из наиболее перспективных типов упрочнителей композиционных материалов являются волокна карбида кремния. Плотность карбидокремниевых волокон равна 3,9...4,05 г/см3. Предел прочности при растяжении составляет 3000...3400 МПа, модуль упругости – 450 ГПа. Прочностные свойства волокон определяются типом и количеством локальных дефектов, имеющихся на их поверхности (утолщения, посторонние частицы, точки налипания). Карбидокремниевые волокна жаростойки и жаропрочны, они способны выдерживать длительное воздействие высоких температур. Волокна из карбида кремния обладают исключительной стойкостью к термическому удару, что делает их незаменимыми при производстве композиционных материалов для авиакосмической отрасли. Однако такие волокна резко теряют эксплуатационные характеристики из-за частичного окисления уже при 1200 °С. Кроме того, их массовое применение ограничено высокой стоимостью 150–350 долл. США за килограмм. В качестве покрытий на карбидокремниевые волокна могут наноситься карбиды вольфрама WC, тантала ТаС, гафния HfC, титана TiC. Карбид кремния может использоваться и в качестве покрытия на борных волокнах(волокна «борсик»).
Непрерывные волокна карбида кремния изготавливают двумя технологическими методами. Первый основан на химическом осаждении из паровой фазы на подложку (керн). В качестве подложки используют вольфрамовую проволоку или углеродную мононить. Для образования покрытий применяют летучие соединения кремния, чаще всего хлориды. Получение волокна из карбида кремня происходит вследствие реакции хлорида кремния с углеродом подложки либо с газообразным углеводородом, входящим в состав газовой среды. Соотношение газов в реакторе определяется исходным диаметром основы, требуемым диаметром получаемого волокна и размерами реактора.
Осаждение карбида кремния осуществляется по реакции
СН3SiСl3 ~ SiC + 3НС1
Температура подложки составляет 1100...1200 °С.
Получаемое волокно состоит из мелких кристаллитов β-SiC, плоскости которых ориентированы преимущественно вдоль его оси. В слу-
153
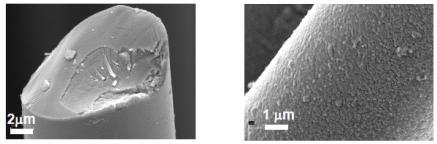
чае использования вольфрамовой подложки длительная эксплуатация при температуре выше 1000 °С приводит к реакции карбида кремния с вольфрамом, в результате чего образуются хрупкие карбид и силицид вольфрама, отрицательно влияющие на прочность волокна. Волокна чувствительны к поверхностным дефектам, и для снижения повреждаемости при трении их покрывают тонким слоем пиролитического углерода.
Другая технология получения керамических волокон основана на пиролизе полимерных волокон. Для получения волокон, содержащих такие элементы, как кремний, титан, углерод, в качестве исходных используют металлоорганические полимеры. Разработаны процессы получения волокон в системах Si-C-O, Si-C-N-O, Si-N-O. Их изготавливают по многоступенчатой технологии, включающей синтез кремнийорганического термопластичного полимера, вытягивание из него вжидком состоянии волокон, полимеризацию и отверждение полимера, пиролиз при 1100–1400 °С в инертной среде. Для получения волокон оксикарбида кремния используют поликарбосиланы, а волокна в системе Si-Ti-C-O могут быть получены из полититанокарбосиланов. Преимуществом технологий, основанных на пиролизе полимеров, является простота получения исходных полимерных волокон высокой чистоты, а также формирование волокон при более низких температурах, чем при других технологиях.
В промышленном масштабе освоен выпуск волокон карбида кремния марки Никалон и волокон системы Si-Ti-C-O марки Тиранно (рис. 5.7). Волокна типа Никалон представляют собой нити поликристаллического SiС диаметром 10–20 мкм с модулем упругости 200 ГПа и прочностью при растяжении до 2,7 ГПа. Волокна типа Тиранно имеют диаметр 8–12 мкм, модуль упругости 200–220 ГПа и прочность при растяжении до 3,0 ГПа. В табл. 5.2 приведены свойства промышленно выпускаемых волокон на основе SiC.
а |
б |
Рис. 5.7. СЭМ-изображение волокон SiC: а – марки Hi-Nicalon;
б – марки Tyranno-SAK
154
Таблица 5.2
Сравнение свойств промышленных волокон на основе SiC и керамики SiC
Свойства |
cg- |
Hi-Nicalon |
Hi-Nicalon |
Dow Sul- |
SiC кера- |
|
|
Nicalon |
|
тип S |
ramic |
мика |
|
Диаметр, мкм |
14 |
12–14 |
12 |
10 |
– |
|
Предел прочности |
2,0–3,0 |
2,8–3,4 |
2,6–2,7 |
2,8–3,4 |
~0,1 |
|
на разрыв, ГПа |
|
|
|
|
|
|
Модуль упругости, |
170–220 |
270 |
420 |
390–400 |
460 |
|
ГПа |
|
|
|
|
|
|
Плотность, г/см3 |
2,55 |
2,74 |
2,98–3,10 |
3,0–3,10 |
3,25 |
|
ТКЛР, 10–6/К |
3,2 |
3,5 |
– |
5,4 |
4,0 |
|
Теплопроводность |
1,5 |
4 |
18 |
40–45 |
100–350 |
|
при 20 °С, Вт/м К |
||||||
|
|
|
|
|
||
Содержание кисло- |
11,7 |
0,5 |
0,2 |
0,8 |
0 |
|
рода, мас.% |
||||||
|
|
|
|
|
||
Отношение C/Si |
1,31 |
1,39 |
1,05 |
1,0 |
1,0 |
Керамические монокристаллические волокна выращивают из расплава методами Вернейля, Чохральского, Тейлора и плавающей зоны.
При выращивании монокристаллов из расплава методами Вернейля исходный материал в виде тонкодисперсного порошка непрерывно подается на расплавленную верхнюю часть подложки кристалла, который нагревается. При этом не требуются тигли для расплава, что позволяет выращивать кристаллы тугоплавких материалов и веществ, для которых не удается подобрать инертный тигельный материал. Этим методом получают монокристаллы тугоплавких металлов, их карбидов, силицидов, боридов, оксидов алюминия, титана и циркония, ферритов. Недостатки метода – большие внутренние напряжения и отклонения состава кристаллов от стехиометрического из-за перепадов температуры и влияния среды плавления.
При получении непрерывных монокристаллических керамических волокон из расплава методом Чохральского в расплавленную в тигле шихту вводится затравка, ориентированная в требуемом направлении, расплав переохлаждается и затравка вытягивается через плавающую на поверхности расплава фильеру или капилляр, устанавливаемый на дне тигля. Вытягивание через капилляр обеспечивает большую стабильность процесса, постоянство диаметра в широких интервалах температур и скоростей роста кристаллов. Методом Чохральского получают
155
непрерывные монокристаллические волокна сапфира диаметром 0,04– 0,5 мкм. Метод позволяет одновременно использовать несколько капиллярных питателей и вытягивать несколько нитей. Недостатком метода является пористость волокна, которая может появиться при затвердевании расплава.
Метод Тейлора заключается в совместном вытягивании из расплава керамических нитей, покрытых стеклянной оболочкой. В кварцевый капилляр помещаются штабики или стержни исходного керамического сырья. В зоне нагрева наполнитель плавится и вместе с кварцевой оболочкой вытягивается в волокно, наматываемое на барабан. Поскольку время нагрева мало, химическая реакция между диоксидом кремния и материалом волокна протекает в незначительной степени. Метод отличается высокой производительностью. Методом Тейлора получают непрерывные волокна сапфира в кварцевой оболочке диаметром 1 мкм.
При методе плавающей зоны с помощью разогрева слитка или цилиндрической прессовки из порошка исходного вещества создается узкая расплавленная зона, которая удерживается силами поверхностного натяжения. Эта зона с постоянной скоростью перемещается вдоль прессовки, а компактное волокно вытягивается из зоны плавления. Диаметр волокна регулируется путем подбора скорости вытяжки. Методом плавающей зоны получают непрерывные монокристаллические волокна сапфира, рубина, TiC, TiB2.
Метод внутренней кристаллизации, разработанный в ЛАС ИФТТ РАН С.Т. Милейко, позволяет получать сапфировые, гранатовые и муллитовые монокристаллические волокна, а также ряд эвтектических оксидных волокон. Схематически метод внутренней кристаллизации представлен на рис. 5.8.
Молибденовый каркас с непрерывными каналами в нем, который легко получается, например диффузионной сваркой пакета, набранного из слоев молибденовой фольги и проволоки, пропитывается расплавом оксида под действием капиллярных сил. Затем расплав оксида кристаллизуется в каналах, образуя волокна. Наконец волокна извлекаются из молибденового каркаса путем растворения молибдена в смеси кислот.
Монокристаллические волокна обладают большими потенциальными возможностями для армирования КМ, особенно жаропрочных, так как имеют высокие прочность и модуль упругости, а плотность невысока (табл. 5.3). Монокристаллические волокна сапфира α-Al2O3 и рубина сохраняют высокие прочность и модуль упругости выше 1200 °С.
156
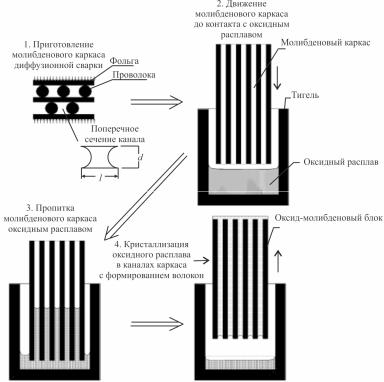
Рис. 5.8. Схема получения волокон методом внутренней кристаллизации
|
|
|
|
Таблица 5.3 |
|
Свойства керамических монокристаллических волокон |
|||
|
|
|
|
|
Материал |
Диаметр, мкм |
Модуль упругости, ГПа |
Предел прочности, МПа |
|
Al2O3 |
|
127–501 |
470–530 |
2410–4140 |
Al2O3 |
· Cr2O3 |
280 |
470 |
3400–4140 |
TiC |
|
280 |
450 |
1540 |
Нитевидные кристаллы – один из наиболее интересных типов упрочнителей в композиционных материалах. Их основными особенностями являются монокристаллическое строение и малые размеры. Часто нитевидные кристаллы из-за их формы называют усами. Диаметр нитевидных кристаллов достигает 10 мкм. Отношение длины к диаметру составляет 20...100, иногда свыше 1000.
Нитевидные кристаллы отличаются малым количеством дефектов строения, поэтому уровень их прочностных свойств достаточно высок.
157
Прочностные свойства усов диаметром менее 2 мкм близки к теоретическим значениям. Однако чем больше диаметр кристаллов, тем меньше величина предела текучести. Объясняется тем, что с ростом диаметра увеличивается количество дефектов строения кристаллов.
Для дискретного армирования керамических композиционных материалов наиболее широко используют нитевидные кристаллы карбида кремния и нитрида кремния. Нитевидные кристаллы SiC получают методами карботермического восстановления, например, диоксида или нитрида кремния углеродом, методами химического синтеза с использованием катализаторов роста, а также высокотемпературным пиролизом отходов рисопереработки.
Таблица 5.4
Свойства нитевидных кристаллов из SiC
Характеристика |
AM Matrixs, |
Tateho, |
Tokai, |
ARCO, |
|
США |
Япония |
Япония |
США |
||
|
|||||
Диаметр, мкм |
1–2 |
0,4 |
0,2–0,5 |
0,7 |
|
Длина, мкм |
20–100 |
20–200 |
40–200 |
30 |
|
Отношение длины к диаметру |
10–100 |
50–400 |
50–300 |
50 |
|
Содержание кислорода, вес.% |
0,9 |
0,6–1,2 |
1,0 |
1,2 |
|
Содержание свободного углерода, |
0,3 |
0,6 |
0,4 |
0,3 |
|
вес.% |
|||||
Прочность, ГПа |
20 |
|
3–14 |
|
|
Модуль упругости, ГПa |
|
|
700 |
|
Свойства нитевидных кристаллов определяются их фазовым составом и степенью совершенства их кристаллической структуры. Предпочтительными свойствами обладают нитевидные кристаллы β-моди- фикации карбида кремния, имеющие монокристаллическое строение. Структура и размеры нитевидных кристаллов в значительной степени зависят от технологических условий проведения процесса. Экономически наиболее эффективным является синтез высокотемпературным пиролизом отходов рисопереработки. Свойства нитевидных кристаллов SiC, производимых в США и Японии, представлены в табл. 5.4.
Промежуточный слой между матрицей и волокном
Для достижения оптимального эффекта от армирования на нитевидные кристаллы, так же как и на непрерывные волокна, наносят барьерные покрытия. Такие покрытия позволяют регулировать степень
158
химического взаимодействия армирующих элементов с керамической матрицей, структуру поверхностей раздела.
Промежуточный слой между волокном и матрицей должен выполнять несколько функций: организовать механическое взаимодействие матрицы с волокном, отклонять развивающиеся трещины в матрице от волокна; препятствовать химическому взаимодействию матрицы с волокном, ведущему к деградации свойств волокна; защитить волокно от окисления.
Композит работает хорошо, если на поверхности разрушения в условиях испытания наблюдаются выдернутые из матрицы волокна определенной длины. При этом отмечаются высокие значения вязкости
иэнергии разрушения, а также большие значения деформации композита до разрушения. Реализовать такой характер разрушения без промежуточного слоя между матрицей и волокном, какправило, не удается.
Барьерные слои обычно наносятся на волокно в виде покрытия, но могут формироваться и в процессе изготовления композита. Покрытие должно иметь однородную толщину, хорошее прилипание к волокну, быть термодинамически стабильным и совместимым с волокном и матрицей в условиях изготовления и эксплуатации композита. Для реализации «выдергивания» волокон из матрицы при разрушении покрытие должно иметь относительно низкую прочность на сдвиг и/или слабую адгезию к матрице.
Сильная связь волокна с промежуточным слоем необходима для отклонения трещин в матрице от волокна у границы матрицы с промежуточным слоем. Это способствует защите волокна от окисления, сохранению способности матрицы передавать напряжения на волокна, достижению больших значений прочности и работы разрушения композитов.
Выбор материала покрытия зависит от назначения и условий эксплуатации, типа волокна и состава матрицы, технологии нанесения покрытия и формирования композита. Наиболее исследованными и доступными являются покрытия из углерода и нитрида бора. Покрытия хорошего качества получают методами химического осаждения пара
ихимической инфильтрации пара (CVD, CVI). Углеродные покрытия на волокнах работоспособны на воздухе до 400 °С, покрытия из BN – до 1000 °С. Идеальным вариантом является многослойное, самозалечивающееся покрытие, включающее податливые слои, например, из пи-
159
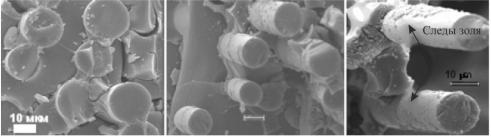
роуглерода или нитрида бора, и жесткие слои, например, из SiC, образующие при высоких температурах стекло, залечивающее трещины в покрытии. Покрытия из SiC и SiO2 могут защитить волокна до 1600 °С. Для работы при более высоких температурах потребуется создавать покрытия из более тугоплавких карбидов, боридов, оксидов и сложных систем на их основе.
Для карбидокремниевых волокон типа Никалон разработан способ получения интерфейсных покрытий на основе оксидов алюминия, циркония, титана и их смесей с использованием в качестве прекурсоров золей этих оксидов.
а |
б |
в |
Рис. 5.9. Поверхности излома Hi-Nicalon™/SiC композита: a – без интерфазы; б – с ZrO2 интерфазой; в – следы золя на поверхности модифицированных волокон
Исследование поведения волокон Никалон с покрытиями в условиях термоциклирования на воздухе при температуре 1000 °С показало, что они обладают высокой термоокислительной устойчивостью, которая достигнута благодаря однородному по толщине и микроструктуре, бездефектному и совместимому с волокном покрытию (рис. 5.9).
Основы технологии получения керамических композиционных материалов
Многие керамические композиционные материалы, такие как трансформационно-упрочненные дисперсными частицами, получают по технологии, основанной на традиционных процессах смешения компонентов, формования и спекания. Однако изготовление материалов, армированных дисперсными или непрерывными волокнами, сопровождается решением ряда специфических проблем, важнейшими из которых являются:
160