
книги / Перспективные композиционные и керамические материалы
..pdfдается графитизации. Усадка материала во время карбонизации фенолоформальдегидных связующих больше, чем при использовании связующих других типов. Это ведет к возникновению значительных внутренних напряжений и снижает физико-механические свойства композитов.
Фурановые смолы по сравнению с фенолоформальдегидными отличаются меньшей технологичностью, цикл их отвердения более сложен. Достоинствами фурановых смол, объясняющими их применение при производстве УУКМ, являются меньшая по сравнению с фенолоформальдегидными связующими усадка при карбонизации, более высокая прочность и плотность каркаса. Плотность каркаса, образующегося из фенолоформальдегидных смол, составляет 1650 кг/м3, из фурановых связующих – 1850 кг/м3, из пеков – 2100 кг/м3.
Достоинствами нефтяных и каменноугольных пеков, кроме высокой плотности кокса, являются низкая стоимость, доступность, склонность к графитизации, исключение из технологического процесса растворителя. К недостаткам пеков относят:
–появление значительной пористости;
–термопластичность, приводящую к миграции связующего при термообработке материала;
–наличие в пеках канцерогенных соединений.
Введение матричного материала в армирующий каркас обычно осуществляется методом пропитки под низким давлением. Следующая стадия получения углерод-углеродного композита заключается в карбонизации матрицы в инертной среде. При необходимости реализуется и стадия графитизации материала.
Для повышения качества углерод-углеродных материалов цикл «пропитка–термообработка» может проводиться многократно. Метод получения УУКМ, основанный на пропитке каркаса под низким давлением, используется в тех случаях, когда допускается открытая пористость материала в пределах 10 %. На рис. 5.24 представлена технологическая схема метода получения УУКМ, основанная на пропитке каркаса.
Повышение свойств углерод-углеродных композиционных материалов и сокращение времени их изготовления возможны при использовании технологии пропитки армированного каркаса под высоким давлением. Основная стадия этой технологии – карбонизация материала под высоким давлением. Речь идет о термобарическом процессе из-
191
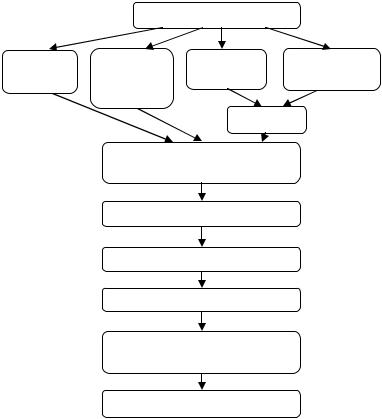
готовления высокоплотных УУКМ, т.е. процессе термообработки, выполняемой с одновременным приложением давления. В соответствии с этой технологией заготовка помещается в тонкий металлический контейнер, заливается и пропитывается жидким пеком, разогретым до 250 °С, закрывается металлической крышкой. Карбонизация под высоким давлением проводится при изостатическом давлении в газостатах или автоклавах.
|
|
Углеродные волокна |
|
Намотка |
Укладка |
Вязание |
Изготовление |
изделий |
объемных |
|
тканей |
структур
Прошивка
Пропитка полимерными связующими
Карбонизация
Повторная пропитка
Повторная карбонизация
Термостабилизация, графитизация
УУКМ
Рис. 5.24. Технологическая схема получения УУКМ с использованием метода пропитки
Для получения более термостабильного материала с высоким уровнем механических свойств после карбонизации может быть выполнена высокотемпературная обработка материала – графитизация.
Эта операция реализуется в индукционных печах или печах сопротивления в графитовой засыпке, вакууме или инертном газе, т.е. в неокисляющей среде. Степень структурных изменений при выполнении
192
этой стадии определяется в основном температурой, поэтому длительность ее по сравнению с карбонизацией невелика (несколько часов). В процессе графитизации происходят необратимые изменения формы изделий, устраняются дефекты структуры. В том случае, если для формования матрицы использовали пеки, хорошо поддающиеся графитизации, во время высокотемпературного нагрева (свыше 2473 К) наблюдается рост трехмерноупорядоченных углеродных кристаллитов вплоть до перехода к структуре графита. В материалах на основе полимерных связующих, плохо поддающихся графитизации, вплоть до 3273 К материал остается в неграфитизированной турбостратной форме.
Второй технологический процесс формования матрицы в углеродуглеродных материалах заключается в осаждении пироуглерода из газовой фазы. В качестве газов используют углеводороды (метан, бензол, ацетилен и др.) или смеси углеводородов с разбавляющим газом (инертный газ или водород). Под действием высоких температур газы в печи распадаются с образованием углерода и других компонентов. Углерод осаждается на поверхности разогретых волокон, постепенно создавая мостики между волокнами и заполняя межволоконное пространство армирующего каркаса. Другие газообразные продукты удаляются из реакционной камеры.
При химическом осаждении углерода его структурная форма и эффективность процесса образования матрицы зависят не только от температуры и давления, но и от характеристик подложки типа ее шероховатости, величины удельной площади поверхности, морфологии и размера пор. Поры должны иметь открытую проницаемую структуру, а их размер должен быть мелким.
Имеются три основных метода осаждения углерода из газовой фазы: изотермический метод, метод температурного градиента и метод градиента давления (рис. 5.25).
При изотермическом методе газ и подложку поддерживают при постоянной температуре около 1100 °С. Осаждение проводят при пониженном давлении 0,6–6 кПа. Установка содержит кожух, нагреватель (индукционную катушку), графитовый сердечник. Графитовый сердечник (сусцептор) является тепловыделяющим элементом, обеспечивающим равномерность обогрева материала в индукционной печи. Внутри графитового сердечника располагают армирующий углеродный каркас. Газы подводятся через нижнюю часть камеры, нагреваются, разлагают-
193
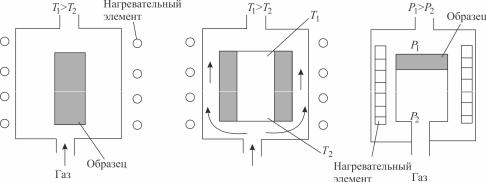
ся, проходят через межволоконное пространство упрочняющего каркаса. Углерод осаждается на поверхности волокон. Газообразные продукты реакции удаляются через отверстие в крышке печи. Метод позволяет заполнять углеродом относительно тонкие армирующие каркасы. Увеличение температуры способствует ускорению осаждения углерода. Недостаток заключается в том, что газ не успевает диффундировать в объем заготовки и при этом происходит наслоение углерода на поверхности объекта.
а |
б |
в |
Рис. 5.25. Методы осаждения углерода из газовой фазы: а – изотермический метод; б – метод температурного градиента; в – метод градиента давления
Достоинства изотермического метода получения углерод-угле- родных композитов: простота, хорошая воспроизводимость свойств материала, высокая плотность матрицы, хорошая графитизируемость матрицы, возможность одновременной обработки нескольких изделий. Недостатки этой технологии связывают с малой скоростью осаждения, плохим заполнением крупных пор, склонностью к поверхностному осаждению пироуглерода.
Осаждение углерода из газовой фазы на толстостенные заготовки осуществляется по методу температурного градиента.
Армирующий углеродный каркас помещают на обогреваемую металлическую оправку или разогревают путем прямого пропускания тока. Газ подают со стороны печи, имеющей более низкую температуру. Таким образом, в армирующем каркасе наблюдается температурный градиент. Осаждение пироуглерода происходит в более горячей зоне. Постепенное увеличение плотности заполняемого углеродом каркаса
194
приводит к изменению температурных условий осаждения и перемещению фронта осаждения в менее плотную область каркаса. Через некоторое время заготовка полностью заполняется углеродом. Плотность углерод-углеродных материалов, полученных этим методом, составляет
1700...1800 кг/м3.
Достоинствами неизотермического метода являются: большая скорость осаждения углерода, возможность заполнения крупных пор, объемное уплотнение материала. К недостаткам относят следующие факторы: необходимость использования сложной аппаратуры, возможность одновременной обработки лишь одного изделия, недостаточная плотность и графитизируемость матрицы, образование микротрещин.
В методе градиента давления газ проникает в заготовку под действием избыточного давления. Он менее распространен, чем первые два метода.
Для получения УУКМ может быть использован модифицированный вариант изотермического метода, выполняемый в режиме давле- ние–вакуум. Реализация метода заключается в попеременном заполнении реакционного объема углеводородным газом и вакуумировании. Достоинством метода является высокая степень объемного уплотнения армирующего каркаса пироуглеродом.
На практике также используются композиты с хаотичной структурой. Технология получения таких материалов заключается в следующем. На первом этапе углеродные волокна разделяют на отрезки длиной 40...60 мм. Затем в водной среде волокна измельчают до длины 0,5...10 мм. Полученный таким образом материал в необходимой пропорции смешивают с порошком фенолоформальдегидной смолы. Приготовленную суспензию заливают в форму, вакуумируют и сушат. На следующих этапах производят термическую обработку материала при 430...460 К и дополнительную термообработку при 1100...1300 К.
Кроме метода пропитки каркаса полимерным связующим и осаждения углерода из газовой фазы матрица в УУКМ может быть сформирована и комбинированными методами, сочетающими описанные выше технологии. Один из вариантов получения углеродной матрицы комбинированного типа (из полимерного связующего и пироуглерода) заключается в следующем. На первом этапе по технологии пропитки получают карбонизованный углепластик. На следующем этапе осуществляют осаждение на полученную заготовку углерода из газовой фазы.
195
Пироуглерод уплотняет поверхностный слой карбонизованного углепластика, уменьшает открытую пористость. В результате такого комбинирования двух технологических процессов значительно возрастают прочностные свойства УУКМ.
Используют и другие варианты формования комбинированных матриц. Разработана технология, в соответствии с которой на первом этапе получают углеродный армирующий каркас. Для повышения его жесткости и предотвращения деформации во время пропитки жидким связующим осуществляют осаждение углерода из газовой фазы. Оптимальная толщина углеродного слоя на моноволокне составляет 0,001...0,1 нм. В результате введения операции осаждения углерода на волокно прочностные свойства композиции возрастают.
Более сложная схема получения комбинированной матрицы предусматривает осаждение пироуглерода на двух этапах изготовления УУКМ. Эта технология, обеспечивающая значительное увеличение прочностных свойств композиционного материала, используется в следующей последовательности:
–осаждение из газовой фазы тонкого слоя углерода на углеродные волокна армирующего каркаса;
–пропитка каркаса полимерным связующим;
–формообразование заготовки;
–карбонизация материала при 1273 К;
–уплотнение карбонизованной заготовки по технологии осаждения углерода из газовой фазы;
–графитизация материала при 2273 К.
Для теплоизоляции при повышенных температурах применяют УУКМ с содержанием пор от 70 до 90 %. Для получения пористых композитов используют низкомодульные УВ длиной около 2 мм, получаемые из вискозного прекурсора. Композит делают из раствора, состоящего из волокон, фенольной смолы, связующего и воды, к которым добавляют отходы уже использованных волокон. Эту смесь перешивают и заливают в форму, после чего вакуумируют для удаления воды. В результате образуются маты, волокна в которых ориентированы преимущественно перпендикулярно направлению откачки. Затем материал сушат и карбонизируют матрицу при температуре 950 °С. В заключение проводят высокотемпературную обработку для удаления летучих продуктов.
196
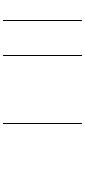
Свойства композита определяются главным образом концентрацией пор. Его прочность низка по сравнению с другими УУКМ.
5.2.6. Свойства углерод-углеродных композиционных материалов
Свойства УУКМ изменяются в широком диапазоне, так как определяются многими факторами: свойствами армирующего наполнителя
иприродой матрицы, степенью наполнения, взаимодействием на границе раздела наполнитель-матрица, условиями пропитки, отверждения, карбонизации, графитации, количеством циклов пропитка–карбониза- ция, условиями газофазного осаждения пироуглерода. Кроме того, необходимо учитывать геометрическое расположение волокон, влияющее на структуру матричного углерода, а следовательно, на свойства композита. В связи с этим сравнение свойств УУКМ необходимо производить с учетом состава, структуры армирования, технологии изготовления и направления вырезки образцов этих материалов из заготовок
идеталей. Плотность УУКМ в зависимости от указанных выше факторов может изменяться в пределах от 1,35 до 2,0 г/см3.
Втабл. 5.11 и 5.12 приведены свойства отечественных УУКМ со структурой 3D и 4D в сравнении с лучшими зарубежными аналогами. Каркасы этих материалов получены из стержней, сделанных из жгутов УВ. Технология заполнения матрицы таких структур жидким каменноугольным пеком включает карбонизацию под давлением до 200 МПа с последующей графитацией. Так, получены материалы «Десна Т-1», «Десна-3» и «Десна-4», в которых каркас сделан из отечественного высокопрочного волокна «Гранит-40».
Таблица 5.11
Физико-механические и теплофизические свойства материалов с трехмерной схемой армирования
Показатели |
«Десна Т-1» |
«Десна-3» |
IMT |
Aerolor–32 |
Тип каркаса |
3D |
3D |
3D |
3D |
Плотность, г/см3 |
1,90 |
1,90 |
1,85–2,00 |
1,90–1,95 |
Предельное сопротивление, |
|
|
|
|
МПа: |
|
|
|
|
при растяжении |
110 |
110 |
70–130 |
170 |
при сжатии |
140 |
130 |
|
120–140 |
Модуль упругости, ГПа: |
|
|
|
|
при растяжении |
53 |
50 |
|
|
при сжатии |
36 |
37 |
|
|
197
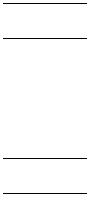
Окончание табл. 5.11
Показатели |
«Десна Т-1» |
«Десна-3» |
IMT |
Aerolor–32 |
Теплопроводность, Вт/(м· К) |
61,0 |
55,2 |
180 |
120-180 |
Максимальный диаметр за- |
550 |
700 |
760 |
|
готовок, мм |
|
|
|
|
Диаметр стержней, мм |
1,20 |
1,33 |
|
1,60 |
Таблица 5.12
Физико-механические свойства материалов с четырехмерной схемой армирования
Показатели |
«Десна-4» |
Sepcarb I |
Sepcarb II |
Тип каркаса |
4D-Л |
4D |
4D |
Плотность, г/см3 |
1,90 |
1,80–1,95 |
1,85–2,00 |
Предельное сопротивление, МПа: |
|
|
|
при растяжении |
110 |
– |
100–130 |
при сжатии |
140 |
70-120 |
80–150 |
Модуль упругости, ГПа: |
|
|
|
при растяжении |
39 |
– |
65 |
при сжатии |
50 |
50–150 |
|
Теплопроводность, Вт/(м· К) |
54 |
– |
|
Максимальный диаметр заготовок, мм |
700 |
500 |
500 |
Диаметр стержней, мм |
1,2; 1,33 |
0,7; 1,0; 1,8 |
– |
5.2.3. Области применения УУКМ
Уникальные свойства УУKM: низкая плотность, высокие удельные прочностные характеристики, стойкость к абляции, сохранение прочностных свойств при температурах до 2000–2500 °С, высокая ударная вязкость, стойкость в агрессивных средах делают эти материалы незаменимыми для жаростойких конструкций, тормозных дисков, теплозащиты возвращаемых космических аппаратов, подшипников, насосов, работающих в агрессивных средах, формующих инструментов для горячего прессования порошков тугоплавких металлов и сплавов, тиглей для плавки цветных металлов. Кроме того, УУKM перспективны для использования в медицине в качестве имплантатов для создания костей, зубных протезов и т.д. (рис. 5.26).
198
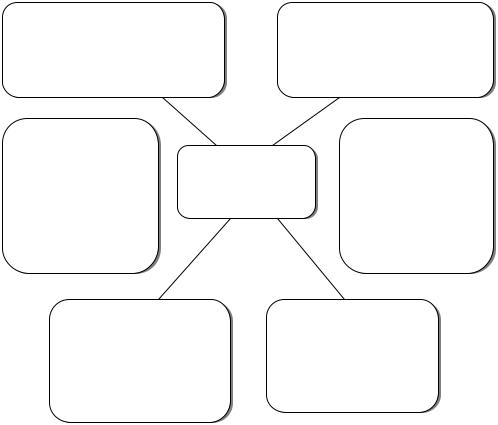
Химическая и нефтехимическая |
Металлургия |
промышленность |
Литейный припас, тигли, |
Детали насосов, подшипники |
воронки, лотки, кристаллизаторы, |
скольжения, торцевые уплотнения, |
пресс-инструмент для порошковой |
детали теплообменников |
металлургии |
Ядерная энергетика |
|
|
|
Термическое |
Элементы конструкций |
|
УУКМ |
|
оборудование |
ядерных установок, |
|
|
Нагреватели, тепловые |
|
|
в промышленности |
|
||
замедлитель, |
|
|
экраны, сусепторы, |
|
|
|
|
||
отражатель оболочки, |
|
|
|
индукторы, крепежные |
тепловыделяющие |
|
|
|
элементы, ростовые |
и поглощающие |
|
|
|
установки |
элементы |
|
|
|
для выращивания SiC |
Медицина |
Другие области |
Диафизарные пластины, |
применения |
крепежныеэлементы, протезы |
Тормозные устройства |
тазобедренных суставов, |
автомобилей, лейки |
черепа, челюсти, ребер, |
для разлива |
позвонков и других костей |
расплавленного стекла |
скелета |
|
Рис. 5.26. Перспективы применения УУКМ
В последние годы во всех промышленно развитых странах ведутся интенсивные разработки по применению целой гаммы композиционных материалов в конструкции газотурбинных двигателей, что обусловлено возможностью повышения рабочих температур, уменьшения массы, габаритов, увеличения удельной тяги двигателя и т. д. Перспективными для применения в ГТД являются углерод-углеродные композиционные материалы. Фирма «Пратт и Уитни» (США) изготавливает панели из трехмерного тканого УУКМ с ребрами жесткости для слабонагруженных конструкций с внутренним креплением, предназначенных для использования в перспективных ГТД. Из УУКМ 3D-структуры на основе вискозных углеродных волокон фирма «Аэрогент» (Франция) предлагает изготавливать выходные сопла двигателей.
199
5.3. Нанокомпозиционные материалы
Наиболее интересные перспективы открываются при использовании нанотехнологий для создания композиционных материалов. Формирование наноструктуры может происходить как за счет кластерных выделений в аморфных матрицах, так и за счет поверхностного либо объемного модифицирования наночастицами металлических, керамических и полимерных материалов. При этом можно получать материалы, обладающие уникальными свойствами: высокими каталитическими и магнитными характеристиками, селективной поглощающей способностью, триботехническими свойствами, термо- и химической стойкостью, высокими прочностью и пластичностью.
5.3.1. Нанокомпозиты с полимерной матрицей
Нанокомпозиты из керамики и полимеров
Свойства конечного нанокомпозиционного материала зависят от природы взаимодействия между фазами и строения межфазных областей, объемная доля которых чрезвычайно велика.
Очень многие материалы – от металлов и керамик до биоминералов – состоят из неорганических наночастиц (оксидов, нитридов, карбидов, силикатов и т.д.). Они входят в состав и нанокомпозитов на основе различной керамики, и полимеров. Несовместимость этих неорганических и органических компонентов – основная проблема, которую приходится преодолевать при создании таких материалов. Чрезвычайно важно также контролировать в них степень микрофазного разделения.
Наибольшие успехи в получении материалов с сетчатой структурой были достигнуты золь-гель технологией, в которой исходными компонентами служат алкоголяты некоторых химических элементов и органические олигомеры.
Сначала алкоголяты кремния (титана, циркония, алюминия или бора) подвергают гидролизу
Si(OR)4 + H2O ↔ (OH)Si(OR)3 +ROH
(OH)Si(OR)3 + H2O ↔ (OH)2Si(OR)2 +ROH
(OH)2Si(OR)2 + H2O ↔ (OH)3Si(OR) +ROH
(OH)3Si(OR) + H2O ↔ Si(OH)4 +ROH,
200