
книги / Перспективные композиционные и керамические материалы
..pdfв среде из смеси азота и кислорода в герметичных туннельных печах со шлюзовой загрузкой и выгрузкой изделий. Необходимое парциальное давление создается изменением состава газа.
Составы и назначение ферритов весьма разнообразны. В нашей стране принята единая система классификации, в основу которой положена принадлежность феррита к группе материалов с определенными свойствами. Важнейшими группами ферритов являются: магнитомягкие, для СВЧ-диапазона, с прямоугольной петлей гистерезиса (ППГ) и магнитотвердые.
Магнитомягкие ферриты широко применяются в радиоэлектронике
иприборостроении. Этим материалам свойственны высокие значения начальной и максимальной магнитной проницаемости и малая коэрцитивная сила.
Магнитная керамика представляет собой обычно изделия на основе
никель-цинковых (система NiO-ZnO-Fe2O3), марганец-цинковых (система MnO-ZnO-Fe2O3) и других ферритов с начальной магнитной проницаемостью до 50000 Гс/Э, применяемых в устройствах проводной ирадиосвязи в диапазоне частот до 200 МГц. В зависимости от рабочих характеристик они служат в качестве сердечников трансформаторов, дросселей
имагнитных антенн и стабильных катушек индуктивности и т.д.
Воснове составов промышленных никель-цинковых ферритов ле-
жат твердые растворы с общей формулой NixZn1-x Fe2O4, где х изменяется от 0 до 0,7. В зависимости от состава и условий получения свойства никель-цинковых ферритов могут существенно изменяться.
Максимальное значение µн наблюдается для состава Ni0,3Zn0,7Fe2O4. С увеличением содержания цинка в никель-цинковых ферритах падает температура Кюри системы. Поэтому с целью сохранения рабочей температуры этих материалов (до 60–80 °С) содержание ZnO в них, как правило, не должно превышать 35 мол.%.
Для получения высокой магнитной проницаемости необходимо
применять сырые материалы с минимальным содержанием примесей. В то же время введением в состав феррита малых добавок некоторых окислов можно улучшить его свойства. Так, добавка Li2O увеличивает µн; введение Al2O3 или Cr2O3 улучшает температурный коэффициент магнитной проницаемости; добавка СоО улучшает частотные характеристики и повышает добротность никель-цинковых ферритов.
Температура спекания Ni-Zn-ферритов 1200–1350 °С. Охлаждение следует проводить медленно. Ni-Zn-ферриты подвержены старению,
101
т.е. с течением времени изменяется их магнитная проницаемость. Обычно основные изменения свойств наблюдаются в течение первого года после изготовления феррита. Интенсивность старения зависит от состава, структуры, условий синтеза, термической обработки. Для стабилизации параметров ферритов проводят искусственное старение при температуре 100–150 °С в течение 10–200 ч с последующим медленным охлаждением.
У плотных крупнозернистых образцов Mn-Zn-ферритов, приготовленных из очень чистых исходных материалов и спеченных в защитной атмосфере, получены значения µн до 50000 Гс/Э и выше.
Температура спекания этих ферритов, как правило, лежит в пределах 1300–1400 °С и соответствует области устойчивости шпинели. Одной из задач технологии получения Mn-Zn-ферритов с заданными параметрами является разработка оптимального режима охлаждения. Начальная магнитная проницаемость поликристаллических ферритов существенно зависит от среднего размера кристаллитов. Оптимальная величина зерна Mn-Zn-ферритов с µн ≈ 300 Гс/Э и малыми потерями составляет 5–10 мкм. Для стабилизации параметров Mn-Zn-ферритов проводят искусственное старение путем нагрева до 120–150 °С и выдержки в течение 50–70 ч.
Оптимальные электромагнитные характеристики Mn-Zn-ферритов достигаются в очень узком интервале содержания Fe2O3, которое может меняться в зависимости от физико-химических свойств порошков. Для увеличения µн и улучшения ее температурной стабильности одновременно вводят СоО и TiO2.
Магнетит Fe3O4 – единственный феррит, широко распространенный в природе в чистом виде, – является ферроферритом со структурой
обращенной шпинели. Основные характеристики магнетита: Нс = 5–200 Э, µн – до 70 Гс/Э, Тс = 585 °С, сопротивление 10–2 Ом · см. Наименьшей
коэрцитивной силой и наибольшим магнитным моментом обладает однофазный материал стехиометрического состава.
Ферритовые материалы с прямоугольной петлей гистерезиса широко применяются для изготовления различных магнитных элементов устройств автоматики и вычислительной техники.
Основными требованиями к ферритовым поликристаллическим материалам, выполнение которых необходимо для получения в них прямоугольной и квадратной петли гистерезиса, являются:
102
а) высокая степень симметрии кристаллической решетки материала; б) высокая степень структурной однородности материала – одно-
фазность, минимальная пористость; в) наличие определенного рода магнитных неоднородностей, рав-
номерно распределенных в материале.
Ферриты со спонтанной ППГ характеризуются структурой шпинели или граната.
Промышленное значение имеют Mg-Mn и литийсодержащие ферритовые материалы. В системе MgO-MnO-Fe2O3 ферритовые материалы с высокой ППГ могут быть изготовлены (иногда с добавками ZnO и СаО) с Нс ≈ 0,16–4 Э, а ферритовые материалы в системах литийсодержащих ферритов с добавками Na2O, MnO, MgO могут быть изготов-
лены с Нс ≈ 1–10 Э.
Для производства ферритовых материалов с ППГ применяют обычно керамическую технологию. При этом особое внимание уделяют выбору исходной окиси железа, как правило, модификации α – Fe2O3.
Ферритовые материалы системы MgO-MnO-Fe2O3 спекают при температуре 1200–1400 °С в воздушной среде с последующей закалкой на воздухе или медленным охлаждением в вакууме. Спекание литийсодержащих ферритов проводят при температурах 1100–1250 °С, при этом и спекание, и охлаждение проводят в кислороде. Ферриты системы Li2O-MgO-MnO-Fe2O3 спекают при температуре 800–900 °С в воздушной атмосфере с последующим быстрым охлаждением.
К ферритам для СВЧ предъявляются следующие основные требования: 1) высокое электросопротивление; 2) температурная стабильность в заданном интервале температур; 3) высокая активность, определяемая величиной минимального подмагничивающего поля.
В зависимости от вида устройства и рабочего диапазона в них используются ферриты, намагниченные до насыщения, или ферриты, находящиеся под воздействием слабого подмагничивающего поля, когда доменная структура еще не разрушена.
Намагниченность насыщения 4πМs для большинства СВЧ-ферритов лежит в пределах 400–500 Гс, температура Кюри составляет 70–700 °С, удельное электросопротивление больше 106 Ом · см.
Для СВЧ-диапазона используют различные ферриты: иттриевые феррогранаты (Y3Fe5O12) с различными добавками, твердые растворы на ос-
нове систем: MgO-Cr2O3-Fe2O3, MgO-Al2O3-Fe2O3, MgO-MnO-Fe2O3 и др.
103
Среди материалов, имеющих наибольшее распространение в технике СВЧ, особое место занимают ферриты со структурой граната. Они характеризуются малыми диэлектрическими потерями, легко управляемой величиной намагниченности насыщения. Температура Кюри
280°С, удельное электросопротивление 109–1012 Ом · см.
Внастоящее время наиболее широко распространена следующая технология изготовления феррогранатов. В шихтовой смеси должен
быть некоторый недостаток Fe2O3 по сравнению со стехиометрическим составом. В качестве исходных компонентов можно использовать Fe2O3 различной квалификации, а также окислы редкоземельных элементов и иттрия с содержанием основного вещества не ниже 99,9–99,5 %. Диффузионный отжиг проводится в брикетах при 1000–1200 °С. Оконча-
тельное спекание проводится в воздушной среде при 1480–1550 °С в зависимости от состава феррита.
Магнитотвердые ферриты, т.е. ферритовые материалы с высокой коэрцитивной силой, применяются для создания магнитных полей в устройствах различного назначения. Широкое распространение для этих целей получили гексоферриты на основе окиси бария – BaO·6Fe2O3 и стронция – SrO·6Fe2O3, а также некоторых других соединений.
Вотечественной и зарубежной промышленности для изготовления постоянных магнитов из феррита бария широко используется обычная керамическая технология.
Вкачестве исходных компонентов применяются углекислый барий BaCo3, углекислый газ и окись железа Fe2O3. Последняя и вступает
втвердофазную реакцию ферритизации с окисью бария при температурах 1100–1200 °С. Полученный нестехиометрический феррит бария подвергается дроблению, грубому измельчению, сухому помолу, а затем сверхтонкому измельчению в воде до получения порошка со средним размером частиц порядка 0,3–0,5 мкм. Полученная водная суспен-
зия порошка феррита бария отстаивается в естественных условиях в течение 3–5 суток и поступает на прессовку. Влажность суспензии при прессовании не должна превышать 30–35 %.
Анизотропные постоянные бариевые ферритовые магниты прессуют в присутствии магнитного поля, прикладываемого вдоль направления прессования или перпендикулярно ему. Процесс прессования состоит из следующих стадий: 1) впрыскивание суспензии ферритового порошка в пресс-форму специальной конструкции; 2) включение маг-
104
нитного поля и ориентации частиц порошка путем их механического поворота; 3) приложение давления при включенном магнитном поле и при постоянном удалении освобождающейся влаги с помощью ваку- ум-насоса через наконечники пуансонов с фильтрующими элементами; 4) выключение магнитного поля при достижении требуемой величины давления и распрессовка детали. Величина намагничивающего поля составляет6000–10000 Э, удельноедавление прессования 250–350 МПа.
Полученные прессовки для удаления остаточной влаги (10 %) сушат на шамотных плитках в естественных условиях. Спекание производят в интервале температур 1150–1250 °С, продолжительность спекания составляет 2–3 ч. В процессе спекания происходит не только уплотнение изделий, но и усиливается степень текстуровки вследствие преимущественного роста ориентированных при прессовке зерен за счет неориентированных.
В настоящее время для увеличения коэрцитивной силы до 2500– 3000 Э при сохранении остаточной индукции 3600–400 Гс в феррит бария принято вводить каолин Al2O3·2SiO2·2H2O в количестве 1–1,2 %.
Лучшие серийно производимые постоянные анизотропные магниты из феррита бария имеют величину максимальной магнитной энергии
до ВНmax = 4 · 106 |
Гс·э при коэрцитивной силе 1800–2300 Э. Часто |
|
в зависимости |
от |
назначения требуются магниты с более высокой |
Нс = 2800–3500 |
Э и достаточно высокой ВНmax. Наилучший эффект |
в этом случае получается при замене в составе феррита части ионов Fe3+ ионами Cr. Однако при этом наблюдается некоторое снижение индукции насыщения и точки Кюри. Другим способом получения керамических магнитов с высокими свойствами является легирование феррита бария окислами редкоземельных элементов, вводимых вместо окиси бария в количестве 0,5–1 мас.%. При этом увеличение намагниченности насыщения, коэрцитивной силы и максимальной магнитной энергии составляет 20–30 %.
Аналогичный технологический процесс применяется при получении стронциевых и свинцовых гексаферритов.
По своим магнитным характеристикам феррит стронция превосходит феррит бария. У лучших зарубежных стронциевых ферритовых магнитов максимальная энергия ВНmax достигает 5 · 106 Гс·э. Высокими свойствами обладают стронциевые ферриты с малыми добавками оксида кальция, ВНmax последних также достигает 5 · 106 Гс·э.
105
У смешанных ферритов бария, стронция и свинца с общей формулой Ba1-X·SrX·6Fe2O3 максимальная энергия ВНmax достигает 1,45 · 106 Гс·э, а у анизотропных состава Sr0,75·Pb0,25·6Fe2O3 – 4,4 · 106 Гс·э.
4.4. Светопроницаемая керамика
Керамика считается непрозрачной, однако в 1959 г. американская фирма General Electric разработала прозрачную керамику на основе оксида алюминия, которая опрокинула бытующие представления. Эта керамика получила практическое применение под фирменным названием Lucalox, в нашей стране она получила наименование Поликор. В настоящее время разработаны светопроницаемые керамики из Al2O3, MgO, Y2O3, BeO, Sc2O3, Cd2O3, CaO, ThO2, PLZT и др, а также соедине-
ний оксидов: алюмомагнезиальной шпинели MgO·Al2O3 и иттрийалюминиевого граната 3Y2O3·Al2O3.
При этом под термином «прозрачная керамика» подразумевается способность пропускать электромагнитное излучение. Но поскольку степень пропускания волн различной длины может быть разной, этот термин достаточно условен. Окно прозрачности – диапазон длин волн, которые может пропускать керамика. Таким образом, сам материал называют ИК-окном, получение которого является сложным и трудоемким процессом.
Керамика становится прозрачной, если она не имеет поглощающих
ирассеивающих центров, к которым в первую очередь можно отнести пористость и границы кристаллов. Одновременно керамика должна быть однофазной, состоять из изотропных кристаллов и иметь высокую чистоту обработки поверхности. При выполнении этих условий керамика будет обладать высокими оптическими свойствами.
Обычно оксидные керамические материалы даже с высокой плотностью, полученные твердофазным спеканием, чаще всего являются непрозрачными, что обусловлено присутствием в них закрытой пористости, которая образуется на конечной стадии спекания из-за интенсивного роста кристаллов. Как правило, поры расположены в основном внутри кристаллов; их поверхность является границей раздела твердой
игазовой фаз, что приводит к поглощению и рассеянию света при переходе от твердой фазы к газовой. Оксидная керамика с общей пористостью более 1 % становится практически непрозрачной.
106
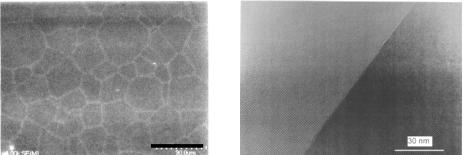
На прозрачность керамики существенно влияет строение границ кристаллов, которые являются источником поглощения света. Строение границ кристаллов у прозрачных и непрозрачных материалов неодинаково, что обусловлено разной степенью дефектности границ кристаллов, которая зависит, по-видимому, от условий формирования микроструктуры и роста кристаллов. Керамические материалы с оптически изотропными кристаллами могут достигать высокого прямого светопропускания, близкого к пропусканию стекла. Однако максимальное светопропускание зависит от величины показателя преломления, так как последний существенно влияет на отражение света от абсолютно гладкой поверхности прозрачного материала. Наиболее благоприятной кристаллической структурой является та, у которой различие коэффициентов преломления по оптическим осям равно нулю, т.е. отсутствует анизотропия (рис. 4.15).
Рис. 4.15. Микроструктура Nd:YAG керамики и изображение границы зерна
Существенное влияние на рассеивание света оказывает размер кристаллов. Максимальное рассеивание имеет место в случае, когда длина волны падающего света соответствует размеру кристалла. В связи с этим для керамического материала, пропускающего свет в видимой области спектра с длинами волн от 0,4 до 0,8 мкм, необходимо избегать наличия кристаллов с размером от 0,4 до 0,8 мкм.
В керамике, имеющей многофазное строение, рассеяние света происходит на границах раздела фаз, так как проходящий свет из-за хаотического расположения кристаллов падает не перпендикулярно к поверхности раздела фаз, а под произвольным углом. Чем более неоднороден материал по фазовому составу, тем меньше вероятность его получения в прозрачном виде. Прозрачные керамические материалы при образовании в них второй твердой фазы, даже в небольших количе-
107
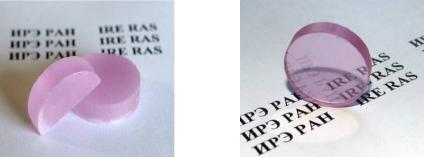
ствах, становятся непрозрачными. Так, появление в керамике из Al2O3, содержащей более 0,5 % MgO, второй фазы – шпинели MgO·Al2O3 приводит к резкому снижению прямого светопропускания.
Исходные материалы должны иметь высокую чистоту, т.е. не содержать примесей, которые при обжиге могут образовывать фазы, не растворяющиеся в основной фазе. Вводимые добавки, которые применяются при получении прозрачных материалов, должны полностью растворяться в основной фазе и не нарушать монофазность системы.
Величина светопропускания прозрачной керамики зависит от чистоты обработки поверхности. Необработанная поверхность керамики после обжига имеет значительную шероховатость. Световые лучи, падая на такую поверхность, рассеиваются, и отражение становится диффузным. Лишь после шлифования и полирования поверхности керамики до 11–13-го класса чистоты удается повысить прозрачность до максимально возможной (рис. 4.16).
Рис. 4.16. Оптически прозрачная керамика после спекания и обработки
Первым материалом, из которого была получена прозрачная поликристаллическая керамика, является Al2O3. Керамика Lucalox характеризуется высокой прочностью, беспористой структурой (относительная плотность 0,945–0,998) и почти такой же способностью пропускать свет, как стекло. Светопропускание пластины из Lucalox толщиной 0,75 мм в области видимого спектра достигает 90 %; материал сохраня-
ет прочность до 1980 °С.
Основным сырьем для получения такой керамики служит высокодисперсный Al2O3 высокой чистоты. Изделия изготавливают методом прессования и обжигают при температурах более высоких, чем обычную керамику.
108
Прозрачный материал из Al2O3 удалось получить благодаря введению в состав керамики небольших количеств 0,1–0,2 % MgO и обжигу
материала в среде водорода или в вакууме при 1700–1950 °С. При этом поры полностью удаляются, изменяется характер кристаллизации: форма кристаллов становится близкой к изометричной, при этом линейное светопропускание в ИК-области спектра достигает 78–80 %.
Рядом фирм США и Японии запатентованы прозрачные материалы на основе Al2O3, в который вводят, кроме MgO, другие добавки, позволяющие регулировать микроструктуру материала, его прозрачность и прочность. Для создания прозрачных материалов из Al2O3 с ориентированной структурой используют метод ГП. Керамика характеризуется повышенной прозрачностью в видимой и ИК-областях спектра. В интервале длин волн λ от 0,4 до 0,68 мкм пластинка толщиной 0,5 мм прозрачна на 75 %, а при толщине 3,8 мм светопропускание составляет 50 %.
В нашей стране также разработана прозрачная керамика на основе Al2O3, которая названа Поликор (ВК 100-1) и Кадор. Для изготовления этих материалов применяют Al2O3, содержащий не менее 99,5% Al2O3 (для Кадора – более чистые виды глинозема) с добавкой 0,1–0,2 % MgO. Для полного удаления пор обжиг керамики проводят в вакууме при температуре 1900 °С в течение 10–20 ч при невысокой скорости нагревания, исключающей захват пор внутри кристаллов. Светопропускание такой керамики в тонкой пластинке (0,5–1 мм) достигает 85– 90 % в видимой части спектра. Величина светопропускания Поликора не изменяется при нагреве образцов в вакууме при температурах до 1700 °С, предел прочности при изгибе не ниже 280 МПа.
Светопроницаемый оксид алюминия имеет хорошую пропускаемость как видимого, так и инфракрасного света, обладает большой жаростойкостью и коррозионной стойкостью. Это дает возможность рассчитывать на его применение в натриевых лампах свечения, для окон устройств инфракрасного контроля или же для подложек интегральных схем, трубок активной зоны реактора и т.п.
Прозрачную керамику из MgO рассматривают как перспективный материал вследствие высокого прямого светопропускания, небольшой величины теоретической плотности, повышенной теплопроводности и хорошей химической стойкости к парам щелочных металлов. Одновременно у этого материала имеется ряд недостатков, которые в определенной степени снижают его достоинства. Это способность к гидрата-
109
ции, что приводит к помутнению полированных поверхностей, сравнительно невысокая прочность, летучесть при высоких температурах.
Прозрачную керамику из MgO получают в основном методом ГП; разработана также технология методом спекания. В качестве исходных материалов в производстве прозрачной керамики из MgO применяют высокодисперсный MgO высокой чистоты, обычно получаемый путем прокаливания солей магния при температурах, близких к температурам их разложения. Для снижения температуры ГП и спекания вводят добавки, содержащие фтор. Наилучшая керамика получена с добавкой LiF, вводимой в количестве 0,1–5 %. Такая керамика имеет теоретическую плотность 3,58 г/см3, размер кристаллов 10–20 мкм; прямое пропускание пластин толщиной 2 мм при λ = 1–7 мкм составляло 70–80 %. Изделия из прозрачной окиси магния используются в качестве окон электровакуумных приборов и оптических элементов для работы в инфракрасной области (детекторов, иллюминаторов и фильтров).
Прозрачная керамика на основе Y2O3, которая получила название Yttralox, разработана фирмой General Electric. Этот материал представляет собой твердый раствор 10 % ThO2-90 % Y2O3 (молярные доли), по светопропусканию приближающийся к стеклу, но имеющий значительно более высокую температуру эксплуатации.
Yttralox – это однородная поликристаллическая керамика с размером кристаллов 10–50 мкм. Кубическая структура Y2O3 обеспечивает незначительное рассеивание света на границах кристаллов, а отсутствие второй фазы и минимальное содержание примесей в исходных материалах – высокое светопропускание материала. Поглощение света
ввидимой области спектра при толщине образца 2 мм не превышает3 %.
Вкачестве исходного сырья для получения Yttralox используют
порошок Y2O3 с содержанием примесей менее 0,01% и соль тория. Смешанные исходные компоненты прокаливают на воздухе при температуре 800 °С, затем подвергают прессованию при удельном давлении 70 МПа. Спекание проводят в восстановительной атмосфере при тем-
пературах 2000–2200 °С.
Фирмой General Electric запатентована прозрачная поликристалличе-
ская керамика на основе Y2O3 с добавкой 2–15 мол.% ThO2, HfO2, ZrO2. Из керамики с добавкой 1 мол.% Nd2O3 изготавливают элементы лазеров. Она достаточно прозрачна при длине генерируемых волн 1,074 мкм и имеет почти такие же характеристики, что и у монокристаллов для обычных лазеров.
110