
книги / Перспективные композиционные и керамические материалы
..pdfются оксид алюминия и титанаты, занимая в общем объеме рынка 55– 59 % (рис. 1.3). В то же время, несмотря на уникальные свойства нитридкремниевой керамики, ее рынок достаточно ограничен и составляет не более 300 т в год. Главная причина – медленный возврат вложенных капиталов из-за более дорогого производственного оборудования, нежели для оксидной керамики. Трудности также связаны с отсутствием дешевого производства высококачественного исходного продукта. Например, успешный уровень роста микроволновой керамики заключается именно в том, что исходным материалом для нее являются традиционные оксидные порошки, а сфера применения очень широка.
1.3. Классификация керамических материалов
Единой общепринятой классификации, охватывающей все многочисленные виды керамики, нет. По областям применения керамику подразделяют на строительную, хозяйственно-бытовую, огнеупоры и техническую.
Техническая керамика занимает особое место среди керамических материалов, под которыми понимают все материалы на основе неорганических неметаллических соединений, изготовленных под воздействием тепла. Термин «техническая» керамика объединяет широкий спектр керамических материалов функционального и конструкционного назначения с заданными механическими, трибологическими, диэлектрическими, теплофизическими, оптическими и другими свойствами. Общим для всех видов технической керамики является базирование процессов изготовления на тонкой химической технологии, включая процессы синтеза сырья высокой чистоты, формирования структуры, нетрадиционной для обычной керамической технологии, процессы формования и консолидации порошков.
Количество керамических материалов очень велико и разнообразно по составу, структуре, свойствам и областям применения (рис. 1.4).
По составу керамические материалы делят:
–на кислородную керамику – оксиды алюминия Al2O3, циркония ZrO2, иттрия Y2O3, магния MgO, кремния SiO2, титана TiO2 и др.;
–бескислородную керамику – карбиды кремния SiC, титана TiC,
нитриды кремния Si3N4, алюминия AlN, бора BN, титана TiN и др.;
11
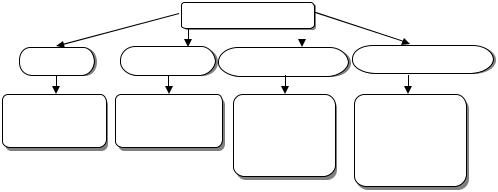
– смешанную керамику – сиалоны, представляющие собой сложные фазы Si6-xAlxOхN8-x, которые можно рассматривать как алюмосиликаты, в которых кислород частично замещен азотом, оксинитрид кремния Si2ON2, оксинитрид алюминия AlON.
|
Техническая керамика |
|
|
Состав |
Структура |
Свойства (функции) |
Область применения |
Кислородная |
Аморфная |
Электрические |
Машиностроение |
Бескислородная |
Композиты |
Механические |
Вычислительная |
Смешанная |
Кристаллическая |
Оптические |
техника |
|
|
Магнитные |
Электроника |
|
|
Биологические |
Энергетика |
|
|
|
Медицина |
Рис. 1.4. Классификация технической керамики
По структуре керамику можно подразделить на кристаллическую (шпинели, перовскиты, гранаты), аморфную (стекла), композиты – состоят из отдельных (разнородных) фаз, отличающихся составом, структурой и свойствами.
Также техническую керамику можно классифицировать по области применения на керамику для машиностроения, металлообработки, электроники и радиотехники, вакуумной техники, ядерной энергетики, медицины и т.д. (табл. 1.1).
Материалы с электрическими функциями. Большое распростране-
ние получила пьезокерамика, то есть керамика, способная поляризоваться при упругой деформации, наоборот, деформироваться под воздействием внешнего электрического поля. Пьезоматериалы нашли широкое применение в качестве электромеханических и электроакустических преобразователей.
Перспективная разновидность керамики с диэлектрическими свойствами – керамические электролиты, то есть материалы с высокой ионной подвижностью и соответственно ионной проводимостью.
Керамика широко используется как полупроводниковый материал специального назначения. Например, терморезисторы и варисторы, изменяющие электросопротивление под действием температуры и приложенного напряжения.
12
Таблица 1.1 Основные виды технической керамики и области их применения
Вид керамики |
Определяющие свойства |
Области применения |
|
|||
|
Высокое электросопротив- |
Электроизоляторы, |
корпуса |
и |
||
|
ление, низкая диэлектриче- |
|||||
|
ская проницаемость |
подложки интегральных схем |
|
|||
|
|
|
|
|
||
|
Сегнетоэлектрические свой- |
Высокоемкостные |
конденсато- |
|||
|
ства, высокая диэлектриче- |
ры, запоминающие устройства |
||||
|
ская проницаемость |
|
|
|
|
|
|
|
Пьезоэлементы, фильтры, тран- |
||||
Электротех- |
Пьезосвойства |
зисторы, ультразвуковые уст- |
||||
ническая |
|
ройства |
|
|
|
|
Электронное излучение |
Электронные |
микроскопы, |
го- |
|||
|
||||||
|
рячие катоды |
|
|
|
||
|
|
|
|
|
||
|
Полупроводниковые |
Варисторы, анализаторы влаж- |
||||
|
и сенсорные свойства |
ности, термисторы, тепловые |
||||
|
|
элементы |
|
|
|
|
|
|
Твердые электролиты, натрий- |
||||
|
Ионная проводимость |
серные аккумуляторы, анализа- |
||||
|
|
торы среды в печах |
|
|
||
|
Высокое светопропускание |
Оболочки галогенных и натрие- |
||||
|
в видимой и ИК-областях |
вых ламп, окна ядерных реакто- |
||||
Оптическая |
|
ров и др. |
|
|
|
|
Флуоресценция |
Компоненты цветных телевизи- |
|||||
|
|
онных трубок |
|
|
|
|
|
Поляризация |
Фотоэлектрические |
преобразо- |
|||
|
|
ватели |
|
|
|
|
|
Магнитная восприимчи- |
Магниты для бытовой техники, |
||||
Магнитная |
вость, магнитная проницае- |
сердечники трансформаторов и |
||||
|
мость, коэрцитивная сила |
катушек и др. |
|
|
|
|
Проводящая |
Электрическая проводи- |
Электроды, |
нагреватели для |
|||
|
мость |
электрических печей |
|
|||
Сверхпрово- |
Сверхпроводимость |
Сверхпроводящие элементы |
|
|||
дящая |
|
|
|
|
|
|
|
Высокая прочность |
Металлорежущие станки и ин- |
||||
|
струменты |
|
|
|
||
|
|
|
|
|
||
|
Стойкость к истиранию |
Волоки, фильеры, нитеводители |
||||
Конструкци- |
Высокая твердость |
Абразивные материалы и инст- |
||||
рументы |
|
|
|
|||
онная |
Низкий коэффициент трения |
Детали подшипников скольже- |
||||
|
|
ния, высокотемпературная смазка |
||||
|
Высокое отношение |
Детали двигателей, в том числе |
||||
|
прочности к плотности |
для летательных аппаратов |
|
|||
|
Высокая ударная вязкость |
Материалы для брони |
|
13
|
|
Окончание табл. 1.1 |
|
|
|
Вид керамики |
Определяющие свойства |
Области применения |
|
|
Детали химических аппаратов и |
Химическая |
Коррозионная стойкость |
ядерно-энергетических устано- |
|
вок |
|
|
Каталитическая активность |
Катализаторы и носители ката- |
|
|
лизаторов |
|
|
Устройства для биохимических |
|
Химическая инертность |
процессов, носители для связы- |
Биологическая |
|
вания энзимов |
|
Костная совместимость |
Искусственные суставы, зубные |
|
протезы |
|
|
|
Важнейшим для электронной техники керамическим диэлектриком является оксид алюминия, который доминирует на мировом рынке. Основная область применения – подложки интегральных схем.
Керамические материалы с магнитными функциями. Среди множества магнитных материалов, применяемых в технике, особое место занимают ферриты, основным компонентом которых является оксид железа. Они были разработаны как альтернатива металлическим магнитам для снижения потерь энергии на перемагничивание.
Керамические материалы с оптическими функциями. Множест-
во материалов с оптическими функциями включает оптически прозрачную керамику, керамику с люминесцентными и электрохромными свойствами, а также светочувствительные керамические материалы.
Материалы на основе прозрачного оксида иттрия, легированного ионами редкоземельных элементов (тербием, неодимом, эрбием, самарием), по интенсивности и количеству поглощения приближаются к соответствующим монокристаллам, появилась возможность использовать их для создания оптического квантового генератора. Большие надежды связывают с использованием светочувствительной керамики для создания различных типов преобразователей энергии.
Керамические материалы с химическими функциями. Химиче-
ская специфика керамики нередко проявляется в изменении физических свойств. Например, хемосорбция различных газов на поверхности керамики сопровождается пропорциональным изменением ее электропроводности, что позволяет определить концентрацию тех или иных компонентов газовой смеси. На этом принципе основано действие большого числа созданных в последнее время газовых сенсоров.
14
Другая область применения керамики, основанная на ее химической специфике, связана с развитием мембранной технологии. Мембраны позволяют избирательно выделять и концентрировать разнообразные вещества.
Керамические материалы для ядерной энергетики. В ядерных энергетических установках керамика используется в качестве теплоизоляции (Al2O3, SiO2), ядерного топлива (UO2, PuO2), материалов регулирующих узлов (B4C, Sm2O3), замедляющих и отражающих материалов (BeO2, ZrO2, Be2C), материалов нейтронной защиты (B4C, HfO3, Sm2O3), электроизоляции в активной зоне (Al2O3, MgO), оболочек тепловыделяющих элементов (SiO2, Si3N4) и т.д.
В термоядерной энергетике керамика широко используется для тепловой и электрической изоляции первой стенки плазменной камеры (SiO2, Si3N4), ограничения плазмы (SiС, Al2O3, B4C), для нейтронной защиты (бланкеты из LiAlO2, Li2SiO3, Li2O), в качестве материала для окон разночастотного нагрева плазмы (Al2O3, BeO2) и т.д.
Конструкционная керамика. Важнейшим в области материаловедения керамики явилось открытие эффекта трансформационного упрочнения в керамике на основе ZrO2, что позволило создать материалы с уровнем трещиностойкости до 15–17 МПа·м1/2 при уровне прочности более 1000 МПа. Разработка материалов на основе Si3N4, имеющих трещиностойкость более 8 МПа·м1/2, прочность более 800 МПа в интервале температур до 1400 °С, дала возможность создать двигатель внутреннего сгорания с рекордно высокой температурой рабочейкамеры.
Перспектива разработок в области керамических конструкционных материалов связана с созданием наноструктурированных композиционных материалов на основе керамики, имеющих сверхвысокие значения прочности – до 2000 МПа и более, а также керамических материалов нового поколения на основе тугоплавких карбидов, нитридов и боридов переходных металлов, имеющих температуру устойчивости твердой фазы выше 3500 °С.
1.4. Технологические процессы производства технической керамики
Важной проблемой технологии технической керамики является достижение высокой воспроизводимости эксплуатационных свойств, которые зависят от структуры керамического материала. Она в первую
15
очередь закладывается характеристиками исходных компонентов, наследуя их. Химический и фазовый составы и дисперсность исходных компонентов влияют и на технологические параметры процессов изготовления материалов, от которых также зависят структура и свойства конечного продукта.
Производство технической керамики состоит из следующих основных технологических этапов: синтез порошков заданного химического, фазового и гранулометрического составов; приготовление формовочных масс; формование, обжиг, финишная обработка; контроль качества и при необходимости ряд дополнительных видов обработки.
1.4.1. Требования к порошкам для получения технической керамики
Чтобы получить высококачественную керамику, керамические порошки должны удовлетворять ряду требований.
Дисперсность. Для получения высококачественной плотной и прочной керамики необходимо мелкое зерно в структуре материала. Наиболее высокие показатели механических свойств достигаются в материалах с ультрадисперсной структурой, размером ее фрагментов на субмикронном уровне. Дисперсность структуры обеспечивает и повышенное сопротивление хрупкому разрушению.
Контролируемый химический и фазовый состав. Примесные эле-
менты, сегрегирующие по границам зерен, создают гетерогенность на уровне нано- и микроструктур и приводят, в частности, к образованию легкоплавких, стеклообразных фаз и резкому снижению механических свойств материалов при высоких температурах. Фазовый состав порошка определяет механизмы распространения трещины при разрушении. Важным является уровень однородности взаимного распределения фаз. Фазовый состав влияет также и на технологические условия изготовления керамического материала.
Необходимая морфология и распределение частиц по размерам,
уровень их агломерирования. Для получения керамических заготовок с высокой плотностью упаковки частиц порошков и однородными по размерам порами необходимо использовать порошки узких фракций в гранулометрическом составе либо подбирать определенные сочетания фракций с обеспечением требуемого распределения порошков. Самопроизвольное агломерирование порошков ограничивает возможности достижения высокой плотности сырца, влияет на характер формирую-
16
PNRPU
щихся в процессе спекания структур, тормозит развитие процессов спекания на начальных его стадиях. Агломерирование, влияя на кинетику спекания, сказывается также на структуре и механических свойствах материала. В зависимости от характера сил связи между частицами порошка агломераты могут быть «жесткими» (ионно-ковалентные химические связи) или «мягкими» (вандерваальсовы силы). «Мягкие» агломераты легко разрушаются, например, ультразвуковой обработкой, «жесткие» в формирующейся при спекании структуре керамического материала оказывают эффект, подобный эффекту от инородных включений, приводя к снижению механических свойств. Контроль агломерируемости порошков является одной из наиболее сложных и ответственных стадий технологического процесса производства технической керамики.
Активность при спекании. Материалы на основе тугоплавких соединений, особенно тех, которые отличаются преимущественно ковалентным типом связи, спекаются плохо даже при очень высоких температурах. Одним из способов повышения активности керамических порошков является механохимическая активация.
Требуемые технологические характеристики (прессуемость, теку-
честь и т.д.).
1.4.2. Методы получения керамических порошков
Порошки, соответствующие требованиям технологии высококачественной керамики, могут быть получены только методами синтеза, а не традиционной для керамической промышленности обработкой природного сырья. В настоящее время для синтеза порошков применяют следующие методы.
Керамический метод заключается в тщательном механическом смешении оксидов и повторяющихся циклах «обжиг-помол» для полного обеспечения твердофазного взаимодействия. В ряде случаев вместо оксидов используются более легкодоступные карбонаты, нитраты или другие соли. Главный его недостаток – длительность термической обработки из-за достаточно крупной кристалличности и неоднородности смешения реагентов. При этом чаще всего имеет место неконтролируемый рост кристаллов и, как следствие, помимо химической, еще и гранулометрическая неоднородность керамических материалов, приводящая к невоспроизводимости свойств.
17
Плазмохимический синтез успешно используется для синтеза высокочистых наноразмерных порошков карбидов, нитридов, оксидов и других тугоплавких соединений. Использование ВЧ-плазменного нагрева особенно благоприятно, поскольку синтез может осуществляться в инертной, окислительной или восстановительной средах. В качестве исходных компонентов часто используют галоидные соединения, такие как TiCl4, SiCl4 и т.д., а также металлоорганические соединения в смеси с реакционными газами: С2Н2, NH3 и др. Образование частиц порошка из газовой фазы происходит в результате процессов конденсации на поверхности (стенок реактора) или за счет образования зародышей кристаллизации. Во избежание агломерирования осуществляют быстрое охлаждение реакционной смеси, что способствует увеличению числа зародышей, замедлению их роста и укрупнению.
Электрический взрыв проводника позволяет получать тонкодис-
персные порошки оксидов, нитридов, карбидов или их смесей при распылении проводников импульсами тока большой мощности длительностью 10–5–10–7 с и плотностью 104–106 А/мм2 в химически активных средах (воздух, смесь кислорода и инертного газа и др.).
Самораспространяющийся высокотемпературный синтез
(СВС) заключается в синтезе тугоплавких соединений из смеси химических веществ в результате химической реакции, протекающей за счет самопроизвольного распространения тепловой волны в объеме смеси. Схематично реакцию СВС можно представить так:
горючее + окислитель = продукт реакции + тепловой эффект.
Горючее – это, например, Ti, Zr, Hf, V, Nb, Та, Mo, W и др., окислитель – С, В, Si, N2, H2, O2, S, Se и др., продукты реакции – карбиды, бориды, силициды, нитриды и другие соединения.
Температура горения может меняться от 800 до 4000 °С, а линейная скорость – от нескольких сотых до нескольких сот сантиметров в секунду. Изменяя параметры синтеза (состав шихты, давление, температура горения, размер частиц реагентов и др.), можно управлять фазовым составом, размером частиц конечных продуктов и их структурой.
Карботермическое восстановление оксидов, проводимое в их смесях с углеродом в атмосфере инертного газа (при синтезе карбидов) или азота (при получении нитридов), является основным процессом производства бескислородных тугоплавких соединений, таких как SiC
и Si3N4.
18
Метод химического осаждения является одним из наиболее распространенных. Для введения добавок или получения сложных соединений используют соосаждение, т.е. их одновременное осаждение. При синтезе оксидных порошков осаждением готовят растворы (преимущественно водные), содержащие требуемые катионы, и смешивают эти растворы с растворами осадителя. Осадок отделяют фильтрованием и сушат, получая вещество-предшественник, которое после термообработки (термолиза) в соответствующей газовой среде образует порошок требуемого соединения.
На процесс осаждения оказывают влияние концентрации исходных веществ, температура, давление, наличие добавок поверхностно-активных веществ. В качестве осадителей наиболее часто используют растворы аммиака, углекислый аммоний, щавелевую кислоту, оксалат аммония, а в качестве осаждаемых веществ предпочтительно использовать хорошо растворимые соли азотной, соляной, уксусной и других кислот.
Гетерофазный синтез заключается в том, что высокодисперсный порошок исходного вещества помещают в жидкую фазу, где в результате гетерофазной реакции происходит внедрение ионов из жидкой фазы в твердую или ионный обмен между фазами. Чаще всего используют водорастворимые соли, которые помещают в концентрированные растворы осадителей, например в водный раствор аммиака.
В отличие об обычных методов осаждения, метод гетерофазного взаимодействия позволяет получать легко фильтруемые малогидратированные осадки, обеспечивает наследование размера, формы и даже иногда элементов кристаллической структуры.
Гидротермальный синтез основан на процессах, происходящих в водных средах при высоких температурах (100–370 °С) и давлениях (до 100 МПа), при которых реализуются химические реакции, не происходящие в обычных условиях. Используются реакции гидротермального окисления, разложения, кристаллизации и т.д. При гидротермальной кристаллизации в качестве исходных используют порошки, полученные осаждением, золь-гель технологией и т.д.
Основной особенностью гидротермальных процессов является отсутствие при сверхкритических условиях границы раздела жидкость– газ, что приводит к нулевому значению поверхностного натяжения на этой границе, исключает действие капиллярных сил и предотвращает образование агрегатов и крупных кристаллов.
19
Метод позволяет получать высокодисперсные порошки с узким распределением по гранулометрическому составу. Широкое внедрение в практику сдерживается периодичностью процесса синтеза, высокой стоимостью и сложностью эксплуатации технологического оборудования. Кроме того, возможности метода ограничены получением лишь оксидных порошков.
Золь-гель технология позволяет получать порошки высокой чистоты и дисперсности, с регулируемым распределением частиц по размерам, в том числе частиц порошков поликомпонентных составов с однородным распределением компонентов. Данная технология базируется на процессах, осуществляемых в жидкой среде с твердой фазой, не концентрирующейся под действием гравитационных сил. В золе твердая фаза дискретна, а в геле эта фаза образует трехмерный каркас в жидкой фазе.
Существует два варианта золь-гель процессов: коллоидные и полимеризационные. Гелеобразование в коллоидных системах происходит в растворах, содержащих золь одного или более компонентов, с образованием так называемого полифазного геля. Полимерный процесс включает процессы поликонденсации с формированием непрерывной полимерной структуры геля, который может содержать катионы различной природы.
Перевод золя в гель осуществляют удалением лишней воды. Коллоидные частицы твердой фазы при этом сближаются и образуют трехмерную пространственную сетку геля.
Криохимический метод заключается в очень быстром замораживании распыляемых растворов солей, шликеров, золей. Быстрота замораживания должна обеспечивать распределение компонентов и добавок, близкое к их распределению в исходном растворе. После этого лед удаляют, не допуская его расплавления, чаще всего возгонкой. Дальнейшая термообработка таких порошков в соответствующих газовых средах приводит к получению очень мелких и активных к спеканию частиц с равномерным распределением добавок. Недостатком метода является его сложность, высокая стоимость получаемого порошка.
Метод распылительной сушки – это наиболее крупномасштаб-
ный путь получения мелкодисперсных, активных порошков для производства керамических материалов. Суть метода состоит в том, что смесь растворов солей, например алкоксидов или хлоридов металлов,
20