
книги / Перспективные композиционные и керамические материалы
..pdf•достижение равномерности распределения армирующих элементов в матрице;
•обеспечение в ряде случаев направленности армирования и, следовательно, анизотропии свойств; создание необходимой границы раздела компонентов как по составу, так и по структуре;
•достижение высокой плотности материала, компоненты которого существенно различаются по термическому расширению и усадке.
Многообразие структур композитов: слоистые, одно-, двух-, трех-
иболее направленные; применяемых материалов и назначений определяет и многообразие методов изготовления композитов. Объемное распределение волокнистого наполнителя в композитах с керамической матрицей (ККМ) осуществляется такими же приемами, как и при изготовлении полимеркомпозиционных материалов (ПКМ): выкладка, плетение, намотка, ткачество, применение ламинатов и препрегов.
Отличие технологии ККМ от технологии керамики и ПКМ обусловлено прежде всего тем, что жесткие неспекающиеся волокна препятствуют уплотнению керамической матрицы при спекании, создавая
вней растягивающие напряжения, ведущие к растрескиванию матрицы уже при нескольких процентах наполнителя. Только принудительное уплотнение методами горячего прессования (ГП) позволяет получать композиты с плотностью, близкой к теоретической.
Широкое развитие получили различные методы введения матрицы
вволокнистый каркас.
1.Физическое осаждение пара (PVD) на поверхность волокна предварительно сформованной заготовки.
2.Химическое осаждение пара (CVD).
3.Химическая инфильтрация пара (CVI, GCVI).
4.Жидкостная пропитка полимером (LPI, PIP) с последующим пиролизом и спеканием.
5.Горячее прессование и ГИП смеси порошка матрицы и наполнителя либо сформованных заготовок из наполнителя и порошка матрицы.
6.Нанесение матрицы или ее предшественника в виде пасты, шликера, геля, полимера на волокно с последующим формованием, пиролизом, спеканием.
7.Реакционное спекание компонентов матрицы, например кремния
иуглерода, сформованных вместе с волокнистым наполнителем.
161
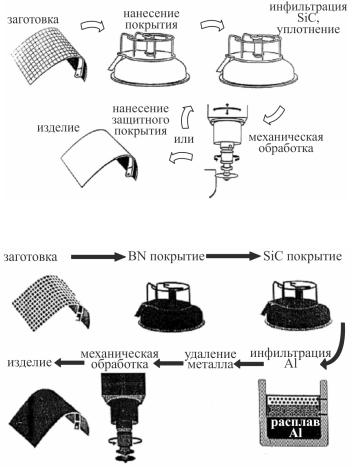
8.Пропитка волокнистой заготовки жидким металлом, например кремнием, с последующим переводом его в нитрид, карбид, оксид.
9.Пропитка волокнистой заготовки шликером, гелем с последующим спеканием.
Пять первых методов уже применяются в производстве и продолжают совершенствоваться. На рис. 5.10 представлена схема получения композитов c SiC-матрицей методом CVD, а на рис. 5.11 – схема производства композитов c Al2O3/Al-матрицей методом «прямого окисления металла».
Рис. 5.10. Схема производства композитов c SiC-матрицей методом CVD
Рис. 5.11. Схема производства композитов c Al2O3/Al-матрицей методом «прямого окисления металла»
Наиболее широко в экспериментальных исследованиях и разработках во Франции, Германии и США используется метод химической инфильтрации пара как для нанесения покрытий из пироуглерода, нитри-
162
да бора, карбида кремния, так и для формирования матрицы из карбида кремния. Используют три основных варианта технологии CVI. Первый основан на изотермическом процессе, в котором волокнистая заготовка помещается в печь, куда подают реакционные газы, и продукты взаимодействия осаждаются в заготовке. Согласно второму варианту по толщине заготовки создается градиент температуры, что предотвращает избыточное осаждение продуктов взаимодействия на поверхности заготовки. По третьему варианту создают градиент давления газов при изотермическом нагреве волокнистой заготовки.
Основным недостатком процесса CVI является высокая остаточная пористость, особенно межслойная, в конечном продукте, что не позволяет в полной мере реализовать все возможности для достижения высокого уровня механических свойств. Тем не менее данная технология успешно используется для изготовления материалов с матрицами из
SiC, Si3N4, B4C, BN, C, TiB2.
Перспективным процессом изготовления композитов, армированных непрерывными волокнами, является также пропитка волокнистых каркасов жидкой фазой с использованием золь-гель процессов или пиролиза металлоорганических полимеров, таких как поликарбосиланы, для формирования карбидкремниевых матриц. Недостатком данных процессов является высокая усадка матрицы и необходимость многократного проведения операций пропитки и последующей термической обработки.
При изготовлении композиционных материалов на основе нитрида или карбида кремния используют также технологию реакционного связывания. Например, при получении композитов с Si3N4-матрицей процесс включает формирование из кремния пористой заготовки, содержащей армирующие элементы, и азотирование до получения плотного реакционно-связанного материала. Положительными сторонами процесса являются пониженная усадка, устранение растрескивания. Недостаток такой технологии – длительность процесса при относительно высоких (> 1300 °C) температурах, что приводит к снижению свойств армирующих волокон, а также наличие остаточной пористости, уменьшающей прочность материала.
Изготовление керамических композиционных материалов, армированных дискретными волокнами или нитевидными кристаллами, включает в себя, в общем случае, следующие стадии:
163
1)обработка исходных компонентов (измельчение, окисление, травление, деагломерирование и т.д.);
2)подготовка матричных порошков и армирующих элементов
ксмешению;
3)смешение компонентов с получением однородных смесей;
4)подготовка смесейк формованию (сушка, гранулирование и т.д.);
5)формование и получение конечного продукта спеканием под давлением или без приложения давления.
Выбор оптимального варианта технологического процесса зависит от состава композита.
Одной из наиболее важных технологических операций является равномерное распределение армирующей фазы в матрице композиционного материала, поскольку от степени однородности зависят механические свойства. Например, проводят деагломерирование нитевидных кристаллов путем обработки в жидких средах: воде, бутаноле, гексаноле, этаноле, в том числе с использованием дефлоккулянтов. Для получения однородных водных суспензий необходимо обеспечить требуемое значение рН среды. Значение рН определяет величину и знак поверхностного заряда частиц и, следовательно, величину сил взаимного отталкивания, способствующих процессу диспергирования и повышению седиментационной устойчивости суспензий.
Смешение компонентов композиционного материала для получения однородных смесей представляет собой серьезную технологическую проблему. Смешение сухих компонентов вряд ли может обеспечить достаточную однородность смеси, в первую очередь из-за тенденции
кагломерированию, поэтому современные технологии основываются на смешении компонентов в суспензиях. В качестве диспергирующих сред в зависимости от состава матрицы используют воду или спирты. Для гомогенизации смеси обрабатывают в различных механических смесителях, подвергают ультразвуковой обработке.
Готовые изделия из однородных смесей матричного порошка и нитевидных кристаллов получают горячим прессованием в графитовых прессформах либо спеканием с последующим горячим прессованием.
Армирование нитевидными кристаллами
Армирование керамических матриц нитевидными кристаллами приводит к повышению трещиностойкости, прочности, износостойкости, усталости и других свойств, определяемых условиями зарождения
164
и распространения трещины. Это является результатом перераспределения нагрузки и упругой деформации нитевидных кристаллов, а также взаимодействия трещины с нитевидными кристаллами по двум основным механизмам:
1)преодоление сил, препятствующих раскрытию трещины при вытягивании нитевидных кристаллов, находящихся в матрице под действием радиальных сжимающих напряжений;
2)переориентация трещины при ее взаимодействии с границей раздела матрица/волокно, сопровождающаяся изменением локальных коэффициентов интенсивности напряжений и увеличением площади поверхности разрушения.
Протекание этих механизмов зависит от формы, размеров нитевидных кристаллов, прочности их связи с материалом матрицы, уровня остаточных напряжений.
Основными параметрами композиционного материала, армированного нитевидными кристаллами (НК), являются:
•соотношение свойств НК и матрицы;
•объемное содержание НК;
•геометрические параметры НК (радиус, длина) и размер зерна матрицы;
•состояние границы раздела НК/матрица (прочность связи);
•остаточные напряжения в матрице.
Можно проследить влияние перечисленных параметров на трещиностойкость композиционных материалов.
Установлено, что трещиностойкость композиционного материала возрастает с увеличением объемной доли дискретной армирующей фазы, однако интенсивность этого повышения зависит от соотношения свойств матрицы и армирующей фазы.
Для достижения высокой трещиностойкости композита необходимо, чтобы модуль упругости матрицы был выше модуля упругости армирующей фазы, а значения коэффициентов расширения матрицы и волокна должны различаться настолько, чтобы обеспечить в матрице растягивающие, а в волокне – сжимающие остаточные напряжения.
Величина удельной работы разрушения материалов зависит от отношения квадрата радиуса НК к его длине. Чем больше это соотношение, тем больше удельная работа разрушения композита. Существующие модельные рассмотрения показывают, что для ограничения рас-
165
пространения трещин в таких материалах оптимальные размеры волокон в сечении должны составлять 0,5–1,0 мкм при их длине 50–100 мкм
иболее.
Сувеличением размера зерна матрицы эффект армирования возрастает: для достижения одинаковой величины K1С в крупнозернистую
имелкозернистую Al2O3-матрицы требуется ввести соответственно 5
и20 об.% НК SiC.
Согласно модельным представлениям повышение трещиностойкости композитов, армированных нитевидными кристаллами, обусловлено либо образованием зоны перекрытия трещины «мостиками связи», роль которых выполняют нитевидные кристаллы, препятствующие раскрытию трещины, либо эффектами переориентации плоскости трещины при ее взаимодействии с НК.
Максимальный эффект от армирования нитевидными кристаллами SiC (20 об.%) получен для алюмооксидных матриц: достигнут уровень трещиностойкости до ~ 8–9 МПа · м1/2 и прочности более 800 МПа. При этом прочность материала не снижается до 1200 °С. Армирование нитевидными кристаллами приводит к повышению таких свойств керамических материалов, как снижение скорости эрозии при абразивном воздействии, повышение сопротивления разрушению при термоударном воздействии, снижение скорости высокотемпературной ползучести.
Аналогичный эффект продемонстрирован при введении усов карбида кремния в другие керамические матрицы: муллит, кордиерит. Так,
введение НК в количестве 30 об.% в кордиеритовую матрицу повышает ее трещиностойкость с 2,2 до 3,8 МПа · м1/2.
Одним из наиболее перспективных в практическом отношении для конструкционных применений является нитрид кремния. Для армирования Si3N4-матриц используют нитевидные кристаллы как SiC, так и Si3N4. Введение 30 об.% НК SiC в Si3N4-матрицу позволяет повысить трещиностойкость с 7,1 до 10,5 МПа · м1/2.
В ОНПП «Технология» горячим прессованием при 1750–1850 °С и давлении 20 МПа получены композиты на основе ультрадисперсных порошков из Si3N4-Y2O3 с НК SiC в количестве 20 мас.% (табл. 5.5). Структура матрицы – мелкие зерна и крупные вытянутые кристаллы длиной 6–20 мкм.
166
Таблица 5.5 Механические свойства композиционной Si3N4 керамики с 20 % SiC
|
|
|
Предел прочности при |
Трещиностойкость, |
|||||||
Марка |
Диаметр |
Длина |
изгибе, МПа, при тем- |
МПа · м1/2, при темпе- |
|||||||
НК |
НК, мкм |
НК, мкм |
|
пературе °С |
|
ратуре °С |
|
||||
|
|
|
20 |
|
1300 |
1500 |
20 |
|
1300 |
|
1500 |
Матрица |
|
|
910 |
|
775 |
820 |
7,3 |
|
8,6 |
|
9,8 |
TWS-200 |
0,3–0,6 |
5–15 |
705 |
|
770 |
760 |
9,9 |
|
10,6 |
|
8,6 |
TWS-400 |
1,0–1,4 |
20–30 |
950 |
|
775 |
775 |
9,0 |
|
7,7 |
|
8,4 |
Армирование обеспечило получение прочности при изгибе до 950 МПа и трещиностойкости до 10 МПа · м1/2, композиты сохраняют высокую прочность до 1500 °С. Также для армирования нитридкремниевой матрицы было использовано углеродное волокно. При введении
2–5 % дискретных волокон наблюдается повышение трещиностойкости до 9,8 МПа · м1/2 (у матрицы 6,6 МПа · м1/2), прочность 600 МПа.
Дальнейшее повышение механических свойств композитов в системе керамическая матрица–нитевидные кристаллы достигается при использовании матричных трансформационно-упрочненных материалов. В таких материалах обнаруживается взаимодействие двух или более механизмов диссипации энергии упругой деформации. Так, введение частиц метастабильной Т-ZrO2 фазы 20 об.% в композиционный
материал муллит 20 об.% НК SiC приводит к повышению K1С при температуре 800 °С с 7 до ~ 10,5 МПа · м1/2.
Композиционные материалы, армированные непрерывными волокнами
Армирование керамических матриц непрерывными волокнами приводит к изменению характера их деформирования и разрушения. Такие композиционные материалы проявляют нелинейную деформацию до достижения максимальной нагрузки и сохраняют несущую способность при дальнейшем нагружении, в отличие от неармированной керамики, которая разрушается катастрофически при максимальной нагрузке (рис. 5.12). При этом значительно повышается работа разрушения и, следовательно, эксплуатационная надежность материала, поскольку его разрушение не сопровождается катастрофическим неконтролируемым распространением трещины.
167
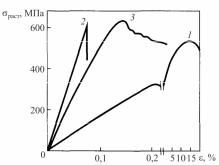
Механические свойства композитов, армированных непрерывными волокнам, зависят от многих факторов, таких как тип армирования (однонаправленное, перекрестное, армирование плоскими или объемными элементами), содержание волокон, их размеры, состояние поверхности раздела волокно-матрица. Процесс разрушения таких материалов весьма сложен и зависит от ориентации волокон по отношению к направлению действия внешней нагрузки.
Разрушение чаще всего происходит в условиях распространения как трещины нормального отрыва, так и трещин сдвига по границе раздела армирующих элементов с матрицей.
Механические свойства композитов с армированием непрерывными волокнами в значительной степени определяются состоянием поверхностей раздела волокна с матрицей, от которого зависит протекание тех или иных процессов разрушения. Для регулирования степени взаимодействия компонентов композита используют нанесение барьерных покрытий на волокна, ограничивающих образование продуктов взаимодействия на границе, либо использование относительно низкотемпературных технологий, в частности технологии инфильтрации из паровой фазы.
Положительное влияние барьерных покрытий на механические свойства обусловлено рядом причин. Нанесение покрытий влияет на взаимодействие волокна с матрицей и процессы выделения газов из волокна при высокотемпературной обработке, обеспечивая тем самым понижение пористости композита. Но значительно больший эффект, чем снижение пористости, обусловлен уменьшением прочности связи волокна с матрицей. Это приводит к возможности реализации процессов вытягивания волокна из матрицы.
Например, нанесение на волокна SiC марки Никалон покрытия нитрида бора приводит к повышению прочности композита с SiO2- матрицей до 280 МПа по сравнению с прочностью 80 МПа материала, армированного волокнами без покрытия. Наиболее сильно покрытие
168
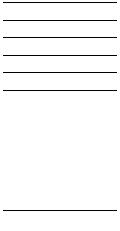
влияет на трещиностойкость, уровень которой для этих материалов составил соответственно >20 МПа · м1/2 (в отдельных случаях 50 МПа · м1/2) и ~1 МПа · м1/2.
Армирование SiC-матрицы непрерывными SiC-волокнами с покрытием позволяет получить композиты с трещиностойкостью 39– 41 МПа · м1/2. Положительное влияние на механические свойства композита SiC-SiC оказывает углеродное барьерное покрытие: достигнут уровень прочности материала 1000 МПа. В процессе разрушения происходило вытягивание волокна из матрицы на расстояние до 300 мкм.
В табл. 5.6 представлены свойства композитов SiC/SiC фирмы SEP (Франция). Матрица из SiC этих композитов формируется химическим осаждением из пара (CVD), покрытие на волокно наносится CVI-мето- дом (химическая инфильтрация пара).
Таблица 5.6 Свойства материалов, разработанных фирмой SEP (Франция)
Свойства |
Материал |
Cerasep |
|
|
Sepcarbinox |
|
|
Плотность, г/см3 |
2,1 |
|
2,5 |
Модуль упругости, ГПа |
100 |
|
175 |
Прочность на изгиб, МПа |
700 |
|
750 |
Прочность на растяжение, МПа |
350 |
|
650 |
Прочность на межслоевой сдвиг, МПа |
35 |
|
30 |
Теплопроводность, Вт/(м·К) |
|
|
|
вдоль волокон |
15 |
|
27 |
поперек волокон |
7 |
|
68 |
КТЛР, 10–6 °С–1 |
|
|
|
вдоль волокон |
2 |
|
1,5–2 |
поперек волокон |
7 |
|
3,0 |
Удельная теплопроводность, Дж/(кг· К) |
1200 |
|
670 |
Характеристики композитов фирмы Allied Signal Composites Inc. с матрицей из SiC, сформированной методом CVI в несколько стадий в волокнистой заготовке двунаправленного сатинового плетения с расположением волокон 0 и 90°, приведены в табл. 5.7. Кипа слоев выкладывалась в форму, и на волокно наносилось покрытие из пироуглерода или нитрида бора CVI-методом. Содержание волокон в композитах 35– 40 об.%, плотность 2,3 г/см3. В композите марки E-SiCf/SiC использованы волокна марки Nicalon, в композите E-SiCf(HN)/SiC использованы волокна марки Hi-Nicalon с меньшим содержанием кислорода.
169
Таблица 5.7
Свойства композиционных керамических материалов SiCf/SiC
фирмы Allied Signal Composites Inc.
Материал |
E-SiCf/Si |
E-SiCf(HN)/SiC |
Свойство/ температура, °С |
20/850 |
20/1200 |
Модуль упругости, ГПа |
125/119 |
202/212 |
Прочность на растяжение, МПа |
236/265 |
324 /256 |
Прочность на межслоевой сдвиг, МПа |
38 |
38 |
Предел пропорциональности, МПа |
76/82 |
102/122 |
Удлинение, % |
0,47/0,63 |
0,74/0,5 |
Керамические композиционные материалы, армированные непрерывными волокнами, предназначены для эксплуатации при высоких температурах. Однако при высокотемпературных воздействиях в таких материалах происходят необратимые изменения, приводящие к снижению механических свойств. В частности, может происходить образование прочной связи между волокном и матрицей в результате химического взаимодействия, окисления или спекания. Другой проблемой является предотвращение деградации свойств волокон, в связи с чем необходимо достижение высокой плотности матрицы, чтобы избежать доступа кислорода к волокнам. Существующий уровень технологических разработок позволяет создавать композиционные материалы, в том числе с объемным армированием трехмерными или комбинацией плоских армирующих элементов, обладающих высокой стабильностью механических свойств при эксплуатации в условиях воздействия высоких температур.
5.1.3. Слоистые композиционные материалы
Переориентация трещины при ее взаимодействии с ослабленными границами раздела наиболее эффективно реализуется в материалах со слоистой структурой. В этом случае при взаимодействии с границами слоев разрушение отрывом периодически меняется на разрушение сдвигом, что требует дополнительной затраты работы внешних сил. Величина эффекта зависит от прочности связи между слоями.
Керамические материалы слоистой структуры могут быть получены следующим образом. Исходные слои, например, из карбида кремния с активирующей спекание добавкой 0,4 % бора изготавливают прокат-
170