
книги / Перспективные композиционные и керамические материалы
..pdf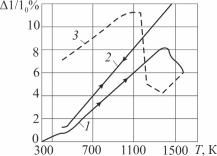
Введением определенных добавок можно предотвратить эти полиморфные превращения и сохранить при комнатной и даже более низкой температуре кубическую или тетрагональную фазу. В качестве таких добавок применяют оксиды иттрия, кальция, магния, церия или их комбинации. Стабилизаторы образуют с диоксидом циркония твердые растворы с ограниченной растворимостью (типа замещения).
Температура начала мартенситного Т→М-превращения при охла-
ждении зависит от размера зерна тетрагональной фазы, снижаясь с уменьшением размера зерна.
Для керамики на основе диоксида циркония конструкционного назначения основными требованиями являются: высокое качество порошка (высокая дисперсность), химическая активность при спекании, гомогенность и чистота.
Существует несколько способов получения ZrO2:
1.Термическая обработка при 1600–1800 °C механических смесей оксидов, содержащих ZrO2.
2.Термическая обработка при 1000–1200 °C механических смесей соответствующих гидроксидов Zr(OH)4.
3.Плавление механических смесей оксидов с последующим медленным охлаждением или высокоскоростной кристаллизациейрасплава.
4.Плазмохимический метод, разложение водных растворов солей циркония и иттрия в плазме высокочастотного разряда. Полученный порошок находится в тетрагональной модификации и состоит из полых сфер размером 0,5–2 мкм и их обломков. При этом частицы представляют собой поликристаллы с размером зерен не более 20 нм.
5.Криохимическая технология. Размер частиц порошка составляет
0,01–0,5 мкм. Удельная поверхность стабилизированного в тетрагональной модификации диоксида циркония равна 125–320 м2/г.
6.Золь-гель технология. Позволяет получать высокочистые монодисперсные порошки со сферической формой частиц, размер частиц тетрагональной модификации составляет 7,5 нм.
31
7.Гидролиз алкоголятов используют для производства высокочистых ультрадисперсных порошков с контролируемым размером, формой
исоставом частиц. Средний размер частиц порошка 0,2 мкм.
8.Совместное осаждение. Используют смеси растворов хлоридов, оксихлоридов циркония и иттрия, сульфата алюминия с едким натром, раствором аммиака и мочевиной.
9.Метод гидролиза: низкотемпературный и высокотемпературный. В основе низкотемпературного гидролиза растворов солей циркония лежит реакция разложения при комнатной температуре и атмосферном давлении. В основе высокотемпературного гидролиза лежит реакция разложения при температуре 120–250 °С и давлении несколько атмосфер. В результате образуются кристаллические частицы диоксида циркония моноклинной модификации диаметром менее 0,1 мкм.
10.Гидротермальная обработка, которая включает гидротермическое разложение циркона ZrSiO4 в присутствии гидроксидов кальция
инатрия. В результате получают гидраты силиката кальция и оксид циркония. Порошок кристаллический и не требует дальнейшего отжига. Средний размер частиц составляет 0,2–0,4 мкм.
11.Разложение растворов выпариванием. Например, по реакции взаимодействия водных растворов карбонатов аммония и солей алюминия, магния, циркония с последующим тепловым выпариванием и термическим разложением в окислительной среде производят УДП в системе Al2O3-ZrO2-MgO. Диаметр частиц составляет от 0,05 до 0,5 мкм
12.Различные виды сушки растворов (спиртом, ацетоном, керосином, распылением, вымораживанием, распылительным отжигом). Порошки состоят из сферических частиц размером 0,1–0,5 мкм.
2.3. Карбид кремния
Карбид кремния – инконгруэнтно плавящееся тугоплавкое соединение с преимущественно ковалентным типом межатомной связи, имеет строго стехиометрический состав с 50,0 ат.% (29,96 мас.%) углерода (отклонение от формульного состава не превышает 10–5 %).
Карбид кремния существует в двух полиморфных модификациях: β-SiC с кубической структурой типа алмаза и α-SiC c гексагональной (Н) или ромбоэдрической (R) структурой слоистого типа. Модификация β-SiC – соединение с низкотемпературной стабильностью, синтези-
32
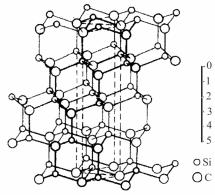
руемое при сравнительно низких температурах. Это соединение очень активно спекается. Но твердость карбида β-SiC низка, он легко окисляется, что делает его непригодным для других целей, кроме использования в качестве исходного материала для спекания. При высокотемпературной термообработке 1800–2000 °С происходит переход кубической модификации в гексагональную.
Карбид α-SiC – соединение со стабильностью высокотемпературного типа, образующееся в результате реакции при температуре выше 1800–2000 °С. У него прекрасная твердость, стойкость при высокой температуре и коррозионная стойкость. Среди видов карбида кремния, применяемых в качестве промышленных материалов, используют α-SiC. Выше температуры 2300 °С карбид кремния термически разлагается.
Для гексагональной модификации α-SiC характерно явление политипизма, при котором различные формы SiC близки друг к другу. Карбид кремния кристаллизуется по законам плотной шаровой упаковки атомов. Кристаллы SiC обладают алмазоподобными кристаллическими решетками, в которых каждый атом Si находится внутри тетраэдра из атомов С и наоборот, т.е. решетка образована из слоев тетраэдров SiC4 и СSi4. Политипы SiC отличаются друг от друга числом слоев одинаково ориентированных тетраэдров в пачке таких слоев. В разных слоях основания тетраэдров могут быть параллельны и непараллельны друг другу (рис. 2.4).
Известно более 70 политипов α-SiC с числом слоев от 2 до 500, среди которых наиболее распространенным являются политипы 15R, 6Н, 4H. Кристаллическая форма политипа зависит от физико-химических условий получения карбида кремния: температуры, газовой среды, а также добавок. Например, увеличение
содержания |
алюминия |
приводит |
|
к превращениям 6Н→15R→6Н→4Н, |
Рис. 2.4. Структура политипа |
||
а увеличение |
содержания |
бора – |
α-SiC III |
к 6Н→4Н→15R.
Примеси р-типа (В, Al, Fe) стабилизируют гексагональную структуру α-SiC, примеси п-типа (N, P) – кубическую структуру β-SiC.
33
Физические свойства: плотность α-SiC 3,166 г/см³, β-SiC – 3,214 г/см³, средний температурный коэффициент линейного расширения α-SiC
составляет 4,57 · 10–6 К–1 (при 293 К), β-SiC – 3,9 · 10–6 К–1 при 400 К.
С увеличением температуры от 673 до 1273 К значение модуля нормальной упругости α-SiC снижается от 403 до 392 ГПа, модуля сдвига – от 178 до 172 ГПа, а коэффициент Пуассона возрастает от 0,132 до
0,141.
Технический карбид кремния представляет собой смесь форм и политипов SiC. В России выпускается технический карбид кремния трех видов: зеленый, черный и электротехнический. Технология производства всех видов SiC в принципе аналогична, с той лишь разницей, что при получении зеленого карбида кремния в шихту добавляют поваренную соль, а при синтезе электротехнического SiC кристаллы последнего легируют алюминием.
При изготовлении применяемого для нужд обычной промышленности карбида α-SiC исходными материалами служат кремнезем (кварцевый песок) и кокс. Их нагревают в электропечах Ачесона до высокой температуры, где протекают сложные реакции, сводящиеся куравнению
SiO2 + 3C = SiC + 2CO
С целью выведения примесей добавляют поваренную соль, для улучшения вывода СО и обеспечения плавного хода реакции добавляют древесную муку или опилки; максимальная температура нагрева достигает 2000–2700 °C. Печь работает с периодической загрузкой. Реакция образования SiC начинается при ~1500 °C и завершается при
~1800 °C.
Образовавшийся за этот период карбид кремния представляет собой мелкий порошок, состоящий в основном из β-SiC. Поэтому стремятся поднять максимальную температуру нагрева выше 2000 °C, обеспечить рекристаллизацию и получить карбид кремния, в основном α-SiC, с достаточно развитыми кристаллами.
2.4. Нитрид кремния и сиалоны
Нитрид кремния – тугоплавкое соединение с преимущественно ковалентным типом связи, характеризующееся низкими удельной массой и температурным коэффициентом линейного расширения, высокими значениями характеристик упругости, твердости и жаростойкости. Ма-
34
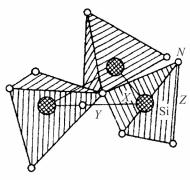
териалы на основе нитрида кремния особенно перспективны для высокотемпературных конструкционных применений.
Нитрид кремния – единственное промежуточное соединение, существующее в системе Si-N в конденсированном состоянии. Нитрид кремния существует в трех различных модификациях: α-, β- и γ-Si3N4. Модификации α и β кристаллизуются в гексагональной сингонии со структурой типа фенакита. Основным структурным элементом являются тетраэдры SiN4 (рис. 2.5). Тройки таких тетраэдров связаны общим атомом азота и расположены под углом около 120° друг кдругу. Структуры α- и β-Si3N4
отличаются пространственным расположением тетраэдров по оси и соответственно неодинаковым количеством формульных единиц в элементарной ячейке.
Из двух аллотропных форм α- и β-Si3N4 наиболее устойчива форма β-Si3N4, так как при повышении температуры α-форма необратимо переходит в β-форму. Превращение α→β интенсифицируется оксидными добавками, такими как MgO, Y2O3, Li2O, которые способствуют образованию жидкой фазы при высоких температурах. Полагают, что механизм α→β-превращения состоит в реакции растворения-осаждения, осуществляемой через жидкую фазу и контролируемой диффузией кремния или азота.
В то время как α- и β-модификации нитрида кремния могут быть получены при нормальном давлении азота и имеют большое значение
впроизводстве высокопрочной керамики, недавно обнаруженный γ-Si3N4 может быть сформирован только при сверхвысоком давлении и еще не имеет никакого практического применения. Кубическая γ-Si3N4 форма
влитературе часто называется «с-модификацией», по аналогии с кубической модификацией нитрида бора (с-BN). Таким образом, γ-модифи- кация – третий самый твердый материал после алмаза и кубического нитрида бора.
Нитрид кремния – соединение с ковалентно-ионной связью, что определяет высокие диэлектрические свойства и твердость, низкие под-
35
вижность дислокаций и диффузионную подвижность. Своеобразная кристаллическая структура накладывает отпечаток на характер взаимодействия Si3N4 с тугоплавкими соединениями и металлами, сказывается на анизотропии некоторых физических свойств. Наконец, небольшой температурный коэффициент линейного расширения и низкая плотность делают нитрид кремния особенно привлекательным в качестве термопрочного и жаропрочного материала с высокимиудельными характеристиками.
Плотность α-Si3N4 составляет 3,148 г/см³, β-Si3N4 – 3,211 г/см³; средний температурный коэффициент линейного расширения в интервале температур 0–1000 °С равен 3,64·10–6 К–1 для α-Si3N4 и 3,39·10-6 К–1 для β-Si3N4. Термическое расширение нитрида кремния анизотропно.
Микротвердость β-Si3N4 ниже микротвердости α-Si3N4. Значения микротвердости для α-Si3N4 анизотропны: максимальная микротвердость (34,85 ГПа) наблюдается для плоскостей (1010), минимальная (26,2 ГПа) – для плоскостей (0001). Зависимость твердости от температуры изучена мало, отмечена практически линейная зависимость в ин-
тервале 20–1600 °С.
Для получения порошков Si3N4 характерны обычные для порошковой металлургии приемы – методы прямого синтеза в различных вариантах, карботермическое восстановление, газофазные реакции синтеза и разложения, а также механическое измельчение как дополнительный вид обработки. В табл. 2.1 приведены этиметоды и некоторые их разновидности.
Таблица 2.1
Основные методы синтеза порошков нитрида кремния и их разновидности
Метод |
Основные реакции |
Основные разновидности |
|
метода |
|||
|
|
||
Прямой синтез |
3Si+2N2→Si3N4 |
Самораспространяющийся |
|
высокотемпературный |
|||
компонентов |
3Si+4NH3→Si3N4+6H2 |
синтез (СВС) |
|
|
|
Плазмохимический синтез |
|
Карботермическое |
3SiO2+6C+2N2→Si3N4+6CO |
– |
|
восстановление |
|||
|
3SiCl4+16NH3→ |
Плазмохимический синтез. |
|
Газофазный синтез |
Si3N4+12NH4Cl |
||
Лазерный синтез |
|||
|
3SiH4+4NH3→Si3N4+12H2 |
||
|
|
||
Диссоциация |
3Si(NH)2→ |
|
|
Si3N4+2NH3(1/n)[SiR2–NR]n→ |
Лазерное индуцирование |
||
(пиролиз) |
Si3N4+RH+H2 |
|
|
|
|
36
Синтез Si3N4 из простых веществ осуществляется взаимодействием кремния с азотом или аммиаком в печах сопротивления, плазмохимическим синтезом и самораспространяющимся высокотемпературным синтезом.
Прямое азотирование Si проводят в атмосфере N2, N2/H2 или NH3 в печах сопротивления при температурах выше 1100 °C, но ниже точки плавления кремния (1412 °С). Данная реакция является экзотермической и должна строго контролироваться, чтобы предотвратить плавление кремния.
В России для получения порошка Si3N4 большое распространение получил метод СВС, поскольку не требует сложной аппаратуры и характеризуется высокой производительностью. Особенностью продукта, получаемого в результате СВС, является его неравновесность из-за высокой концентрации структурных дефектов, возникающих в условиях значительных градиентов температуры (до 2000 К), экстремально высоких скоростей нагрева и охлаждения. При СВС-процессе выход Si3N4 определяется давлением азота и дисперсностью исходного кремния.
Метод плазмохимического синтеза (ПХС) позволяет изготавливать порошки с повышенной химической активностью по сравнению с грубодисперсными порошками, получаемыми другими методами. Высокая скорость движения компонентов в струе низкотемпературной плазмы (5000–10000 К) обеспечивает закаливание продуктов реакции, в результате чего формируются порошки с большой долей аморфного Si3N4 и нанокристаллитов α- и β-фазы (~ 20 нм).
Метод газофазного синтеза используют преимущественно для получения наноразмерных порошков нитрида кремния, широко применяя реакции взаимодействия галогенидов кремния (SiCl4, SiB4) или силана SiH4 с аммиаком, осуществляемые в условиях плазмохимического, лазерного или обычного теплового нагрева.
В реакционную камеру аммиак и смесь SiCl4 –H2 вводят раздельно. Синтез паровой фазы происходит в диапазоне температур от 800 до 1400 °C с образованием аморфного Si3N4. Кристаллизация аморфного порошка осуществляется при температуре 1300–1500 °С.
Процесс термической диссоциации диимида кремния Si(NH)2 состоит из трех основных этапов: а) синтеза Si(NH)2; б) термического разложения Si(NH)2; в) кристаллизации. На первом этапе, тетрахлорид кремния (SiCl4) и аммиак (NH3) вступают в реакцию при 1550 °C
37
ватмосфере азота с образованием Si(NH)2 и хлорида аммония. На следующем этапе Si(NH)2 термически разлагается при температуре около 1000 °C для получения аморфного порошка нитрида кремния. На заключительном этапе аморфный порошок подвергается кристаллизации
вдиапазоне температур 1300–1500 °С с образованием α-Si3N4 порошка. Карботермическое восстановление оксида кремния в среде азота
давно привлекает к себе внимание исследователей как метод, позволяющий использовать недефицитное сырье (например, рисовую шелуху). Получение Si3N4 восстановлением оксида кремния углеродом с одновременным азотированием известно с конца XIX века. В качестве исходных веществ используют либо кремниевую кислоту, либо кремнозем, а восстановителями служат: аморфный углерод, графит, карбид кремния, нефтяной кокс, смолы.
Процесс включает в себя азотирование смеси углерода и кремния в атмосфере азота при температуре в диапазоне от 1400 до 1500 °C. Характеристики порошков Si3N4, полученные в результате карботермического восстановления, зависят от многих факторов, а именно соотношения C/SiO2, скорости потока азота, температуры реакции, размера частиц и удельной поверхности диоксида кремния иуглерода и примесей.
Возможность получения высокоплотных нитридкремниевых материалов и параметры технологических процессов определяются в значительной степени характеристиками исходных порошков. Общими требованиями, предъявляемыми к порошкам Si3N4, являются следующие:
–высокая дисперсность и однородность частиц. Для большинства технологий требуются порошки с удельной поверхностью 10–25 м2/г, позволяющие получать высокоплотные материалы с мелкозернистой структурой;
–высокое содержание α-фазы, так как процессы уплотнения
иструктурообразования нитридкремниевой керамики связаны с сопут-
ствующим фазовым превращением α-Si3N4 → β-Si3N4, которое происходит по механизму перекристаллизации через жидкую фазу;
–контролируемое содержание кислорода. Кислород как основная примесь присутствует в порошке нитрида кремния в адсорбированном
виде, а также в виде SiО2. Содержание кислорода определяет количество жидкой фазы при спекании, влияет на фазовый состав и структуру
исвойства материала;
–минимальное содержание металлических примесей и углерода. Наличие в порошке железа, кальция и магния приводит к снижению вязкости жидкой фазы при спекании, повышает конечную плотность на
38
1–5 %, но способствует росту зерен Si3N4 и образованию более грубой зернистой структуры керамики, определяет уменьшение высокотемпературной прочности и увеличение скорости деформации при воздействии механических напряжений. Присутствие углерода уменьшает количество жидкой фазы и изменяет ее состав, подавляет уплотнение и способствует укрупнению структуры.
Также оговаривается содержание свободного кремния, которое может доходить до 1–2 %. Высоким содержанием свободного кремния особенно отличаются порошки, полученные азотированием кремния. Примеси галогенов могут также приводить к деградации свойств порошков. Содержание фтора и хлора для большинства марок оговаривается на уровне 0,001–0,009 мас.%.
В последнее время в связи с развитием работ в области нанокристаллических материалов особое внимание уделяется такой характеристике, как агломерируемость. Наличие агломератов сказывается на образовании в структуре спеченных материалов довольно крупных межчастичных пор, ухудшающих физико-механические и другиесвойства.
Характеристики порошка нитрида кремния определяются методом его синтеза и качеством исходных реагентов (табл. 2.2).
|
|
|
|
Таблица 2.2 |
Некоторые характеристики порошков нитрида кремния |
||||
|
|
|
|
|
Характеристика |
Прямое |
Газофазный |
Карботермиче- |
Диссоциация |
ское восста- |
||||
|
азотирование |
синтез |
новление |
Si(NH)2 |
|
|
|
|
|
Удельная |
8–25 |
3,7 |
4,8 |
1 |
поверхность, м2/г |
|
|
|
|
Содержание |
1,0–2,0 |
1,0 |
1,6 |
1,4 |
кислорода, мас.% |
|
|
|
|
Содержание |
0,1–0,4 |
– |
0,9–1,1 |
0,1 |
углерода, мас.% |
|
|
|
|
Примеси металлов, |
0,07–0,15 |
0,03 |
0,06 |
0,005 |
мас.% Σ Fe, Al, Ca |
|
|
|
|
Кристалличность, % |
100 |
60 |
100 |
100 |
Содержание |
95 |
95 |
95 |
85 |
α фазы, % |
|
|
|
|
В начале 70-х годов прошлого века появились материалы, названные по буквам составляющих элементов – Si, Al, О, N – сиалонами. Алюминий может быть заменен другими металлами – Be, Ga, Sc т.д. Поэтому этот класс соединений называют симонами.
39
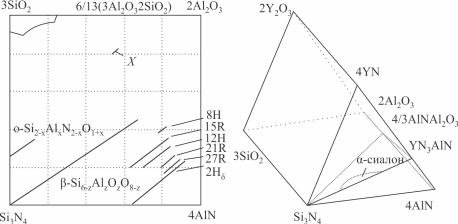
Сиалоны представляют собой сложные фазы типа (Si, Al)(O, N)4, которые можно рассматривать как алюмосиликаты, в которых кислород частично замещен азотом.
Сиалон был получен при изучении системы Si3N4-SiО2-Al2O3-AlN. В системе выделяют несколько видов сиалонов: гексагональный β-сиалон, аналогичный β-Si3N4, имеющий состав Si6-xAlxOхN8-x, где 0 < x ≤ 4,2; гексагональный α-сиалон, аналогичный α-Si3N4 (рис. 2.6). Фаза α-сиалона стабилизируется соответствующими добавками и имеет состав: Мех(Si, Al)12(O, N)16, где 0 < x ≤ 2, Me – Li, Na, Ca, Mg, Y или РЗЭ.
а |
б |
Рис. 2.6. Расположение сиалоновых фаз на диаграмме состояния: а – четырехэлементной системы Si-Al-O-N; б – пятиэлементной системы Y-Si-Al-O-N
Наиболее широко используют β-сиалоны. Структура β-сиалона представляет собой твердый раствор алюминия и кислорода в кристаллической решетке Si3N4. Практически β-сиалоны получаются синтезом из порошков Si3N4 – Al2O3 – AlN или Si3N4 – SiО2 – Al2O3 .
Сиалоновые порошки получают смешиванием с последующим спеканием компонентов, содержащих элементы сиалоновой системы
(Si, SiO2, Si3N4, Si2ON2, Al, Al2O3, AlON, AlN) в различных соотноше-
ниях в зависимости от требуемого состава сиалона. После спекания при температуре примерно 1700 °C в течение 1–3 ч полученный материал подвергается размолу.
40