
книги / Перспективные композиционные и керамические материалы
..pdfпереведенная посредством ультразвукового распылителя в состояние аэрозоля с размером частиц 0,5–0,8 мкм, переносится газом-носителем в горячую камеру, где происходит мгновенное разложение частиц; образовавшийся продукт собирают на фильтре. В результате синтеза образуются частицы сферической формы за время, значительно меньшее 1 секунды.
1.4.3Особенности процессов формования
испекания технической керамики
Формование изделий является важным технологическим этапом при изготовлении керамики, так как строение прессовок и в первую очередь поровая структура определяют степень и равномерность ее удаления при спекании, а также получение заданной микроструктуры керамики. Основными свойствами отформованного изделия, которые в значительной степени определяют качество спекания керамики и ее микроструктуру, являются относительная плотность, равноплотность, максимальный размер пор и распределение пор по размерам.
Необходимо использовать такие методы формования изделий, которые обеспечивают равномерную укладку частиц без существенных напряжений, что позволяет получать равноплотную прессовку с примерно одинаковым размером пор. Такое строение прессовки предотвращает дифференцированное (зонное) спекание и обеспечивает рав- номерно-кристаллическую микроструктуру керамики после обжига.
В настоящее время в технологии тонкой технической керамики принципиально осуществимы все керамические методы формования: полусухое, горячее, изостатическое, в том числе горячее, прессование; литье водных суспензий в пористые формы, горячее литье под давлением, пленочное литье; пластическое формование и др.
Керамические порошки состоят, как правило, из высокодисперсных частиц, являются низкотекучими, обладают низкой пластичностью. При формовании из них заготовок, в частности, методом прессования, часто возникает потребность в применении пластификаторов или связующих веществ, обычно органической природы. Выбор связок и относительное их содержание определяются свойствами порошков, их дисперсностью и химическим составом.
Помимо пластификаторов могут быть использованы также смазки для пресс-форм и пуансонов, уменьшающие трение между ними и по-
21
тери усилия пресса. В качестве пластифицирующих веществ используют растворы органических высокомолекулярных соединений (полимеров) в воде (поливиниловый спирт – ПВС, метилцеллюлоза – МЦ и пр.), в органических растворителях (растворы каучуков в бензине, полиметилметакрилата в летучих растворителях и т.п.). Могут быть применены парафины, глицерин, различные масла. В качестве твердых пластификаторов иногда берут графит, нитрид бора и пр., если это не ухудшает эксплуатационных свойств получаемых керамических изделий. Как смазки выступают обычно некоторые из пластификаторов, а также стеариновая кислота или стеараты, пальмитаты, олеаты (мыла).
Принципиальное различие вышеперечисленных методов формования состоит, с одной стороны, в применении различного количества временных связок: при прессовании от 0 до 10 % по массе, при пластичном формовании от 7 до 15 % и при шликерном литье от 15 до 35 %, а с другой стороны, в том, что при переходе от прессования к пластическому формованию и шликерному литью увеличиваются технологические возможности изготовления сложных по конфигурации изделий.
Методы формования различаются и пределами применяемых давлений. Так, в процессе прессования обычно применяются удельные давления до 600 МПа и более. При пластичном формовании удельные давления значительно меньше: от 0,98 до 200 МПа, а при шликерном литье практически уменьшаются до 0,98 МПа.
Обжиг изделий в зависимости от их состава, формы и размеров проводят различными способами по индивидуальным режимам, используя при этом для уплотнения все известные механизмы спекания (твердофазное, жидкофазное, реакционное и др.). При обжиге керамических заготовок могут происходить различные физико-химические процессы: термическое разложение исходных сырьевых материалов, химические реакции между компонентами или с газовой средой, полиморфные превращения, эвтектическое плавление, растворение в расплаве одних твердых фаз и кристаллизация из расплава других. Эти процессы могут сопровождаться изменением массы, объема, химического и фазового состава, плотности и пористости.
Среди явлений, протекающих при обжиге, важнейшим является процесс спекания, обусловливающий превращение пористых заготовок из конгломерата слабосвязанных частиц, объединяемых преимущест-
22
венно силами трения и адгезии, в плотное, прочное тело с заданной структурой и свойствами.
Материалы на основе тугоплавких соединений, особенно тех, которые отличаются преимущественно ковалентным типом связи, спекаются плохо даже при очень высоких температурах. В связи с этим прибегают к различным способам активированного процесса уплотнения при спекании. Это механохимическая активация порошка, введение добавок, активирующих спекание, применение горячего и горячего изостатического прессований.
Одним из способов активирования процесса спекания является повышение дисперсности исходных порошков и уменьшение размера агрегатов, что позволяет существенно снизить температуру спекания керамических материалов. Порошки, состоящие из крупных агрегатов (5 мкм и более), как правило, не спекаются до высокой плотности даже при предельных температурах из-за образования пористости между и внутри агрегатов.
Можно существенно интенсифицировать процессы спекания созданием повышенной дефектности кристаллической структуры спекаемого материала и поддержанием ее в ходе спекания, что достигается методами механохимической активации исходных порошков.
Весьма существенно на процесс спекания влияют неконтролируемые примеси и контролируемое введение добавок. Некоторые добавки снижают температуру спекания, регулируют микроструктуру и свойства керамики. В зависимости от вида взаимодействия добавки подразделяют на четыре группы:
1)полностью растворимые в кристаллической решетке основного вещества; широко применяются для повышения скорости твердофазного спекания, действуют главным образом за счет изменения концентрации вакансий в катионной либо в анионной подрешетках кристалла;
2)не растворимые, а образующие жидкую фазу при спекании за счет плавления либо за счет взаимодействия с основным веществом
собразованием эвтектического расплава; ускоряют спекание в результате интенсификации процессов переноса вещества в присутствии жидкой фазы и влияют на характер микроструктуры;
3)инертные, не растворимые в основном веществе и не взаимодействующие с ним; снижают поверхностную энергию частиц и чаще всего замедляют процесс спекания. Очень перспективными являются до-
23
бавки, химически не взаимодействующие с основным веществом, вводимые в области эвтектических составов;
4) вступающие в химическое взаимодействие с основным веществом с образованием нового химического соединения; могут ускорять или замедлять процесс твердофазного спекания и влиять на процессы рекристаллизации в зависимости от вида образующегося нового соединения.
Модифицирующие добавки, образующие твердые растворы, являются наиболее перспективными для управления процессом твердофазного спекания, микроструктурой и свойствами керамики.
Спекание под давлением, или горячее прессование (ГП), находит весьма широкое применение в технологии керамики, в частности, для изготовления высокоплотных изделий из наиболее трудноспекающихся материалов (карбиды, нитриды и др.). Интенсивно применяется в технологии технической керамики метод горячего изостатического прессования, который по механизму спекания подобен ГП, а по схеме осуществления – процессу холодного изостатического прессования.
Перспективным для спекания керамики является использование микроволнового излучения, что позволяет: 1) снизить энергетические затраты, сократить продолжительность процесса спекания; 2) повысить дисперсность и однородность структуры спеченных материалов; 3) достичь более высокого уровня свойств по сравнению со свойствами материалов, спеченных с применением обычных источников нагрева.
После обжига некоторые изделия подвергают дополнительным видам обработки – механическим, металлизации, поляризации, намагничиванию и др.
Список литературы
Основная
1.Химическая технология керамики: учеб. пособие для вузов / под ред. проф. И.Я. Гузмана. – М.: Стройматериалы, 2003. – 496 с.
2.Шевченко В.Я., Баринов С.М. Техническая керамика. – М.: Нау-
ка, 1993. – 187 с.
3.Керамика для машиностроения / А.П. Гаршин, В.М. Гропянов, Г.П. Зайцев, С.С. Семенов. – М.: Научтехлитиздат, 2003. – 384 с.
24
4.Швейкин Г.П. Керамика: прогнозы развития на 2000–2005 гг. // Огнеупоры и техническая керамика. – 2000. – № 7. – С. 5–9.
5.Шевченко В.Я., Терещенко Г.Ф. Исследования, разработки и инновации в области керамических и стекломатериалов // Вестн. Рос. акад.
наук. – 2000. – Т. 70, № 1. – С. 50–56.
6.Бакунов В.С., Лукин Е.С. Особенности технологии высокоплотной технической керамики. Химические методы получения исходных порошков // Стекло и керамика. – 2008. – № 2. – С. 3–7.
7.Боровинская И.П. СВС-керамика: синтез, технология, применение // Наука – производству. – 2002. – № 6. – С. 28–35.
8.Шабанова Н.А., Попов В.В., Саркисов П.Д. Химия и технология нанодисперсных оксидов: учеб. пособие для вузов. – М.: Академкнига, 2007. – 309 с.
Дополнительная
1. Лукин Е.С. Современная высокоплотная оксидная керамика с регулируемой микроструктурой. Ч. I. Влияние агрегации порошков оксидов на спекание и микроструктуру керамики // Огнеупоры и тех-
ническая керамика. – 1996. – № 1. – С. 5–14, № 2. – С. 9–18.
2. Лукин Е.С. Современная высокоплотная оксидная керамика с регулируемой микроструктурой. Ч. IV. Технологические методы получения высокодисперсных порошков оксидов для многокомпонентной оксидной керамики // Огнеупоры и техническая керамика. – 1996. –
№9. – С. 2–10.
3.Физико-химические и технологические основы самораспространяющегося высокотемпературного синтеза / Е.А. Левашов, А.С. Рогачев, В.И. Юхвиц, И.П. Боровинская. – М.: БИНОМ, 1999. – 176 с.
4.Андриянов Н.Т. Золь-гель метод в технологии оксидных материалов // Стекло и керамика. – 2003. – № 10. – С. 17–20.
5.Bykov Yu.V., Rybakov K.I., Semenov V.E. High-temperature microwave processing of materials // J. Phys. D: Appl. Phys. – 34 (2001). – P. 55–75.
6.Суворов С.А., Туркин И.А., Дедовец М.А. Структура и свойства циркониевых материалов, полученных саморазогревом в электромагнитном поле СВЧ // Огнеупоры и техническая керамика. – 2004. –
№8. – С. 5–7.
25
Контрольные вопросы
1.Что означает термин «керамика» в узком и широком смысле?
2.Перечислите факторы, обусловливающие перспективность кера-
мики.
3.Какие направления исследований в области современной керамики наиболее перспективны?
4.Чем определяются темпы развития производства отдельных видов технической керамики?
5.Классификация технической керамики.
6.Основные области применения технической керамики.
7.Какие требования предъявляются к порошкам для производства керамических изделий?
8.Основные методы получения керамических порошков.
9.Какие процессы применяются для формования и спекания керамических порошков?
10.Способы активации процесса спекания.
26
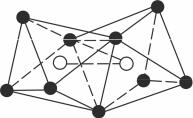
Глава 2. ИСХОДНЫЕ КОМПОНЕНТЫ В ПРОИЗВОДСТВЕ ТОНКОЙ ТЕХНИЧЕСКОЙ КЕРАМИКИ
Основой технической керамики являются неметаллические, тугоплавкие соединения с температурой плавления более 1500 °С. Для таких соединений характерен смешанный ионно-ковалентный тип межатомной связи и высокая термодинамическая стабильность. Они имеют высокую твердость, модуль упругости, химическую устойчивость и жаростойкость. Общий признак этих соединений хрупкость, обусловленная особенностью межатомного взаимодействия.
Наиболее важными в практическом отношении являются оксид алюминия, оксид циркония, двойные соединения и твердые растворы в системах: оксид алюминия–оксид магния, оксид алюминия–оксид кремния, оксид алюминия–оксид титана, оксид циркония–оксид кальция или оксид магния, или оксид иттрия (Y2O3); кордиерит, бескислородные тугоплавкие соединения: карбид бора (B4C), карбид кремния, карбид титана, карбид циркония, нитрид бора (BN), нитрид кремния (Si3N4), нитрид титана и др.; соединения и твердые растворы в системе Si-Al-O-N.
2.1. Оксид алюминия
Оксид алюминия Al2O3 (глинозем) – соединение с ионноковалентным типом межатомной связи, плавящееся при температуре (2054 ± 6) °С. Оксид алюминия существует в нескольких полиморфных модификациях. К устойчивым модификациям глинозема относятся α- Al2O3 и γ-Al2O3.
Глинозем α-модификации с гек- |
|
сагональной структурой, встречаю- |
|
щийся в природе в виде минерала |
|
корунда, является наиболее устой- |
|
чивой в широком интервале темпе- |
|
ратур полиморфной модификацией |
|
(рис. 2.1). Корунд – конечный про- |
|
дукт термической обработки всех |
Рис. 2.1. Структура α-Al2O3 |
других разновидностей глинозема. |
|
Твердость корунда по шкале Мооса 9, плотность колеблется от 3,98 до
4,01 г/см3.
27
Вторая устойчивая модификация Al2O3 – γ-Al2O3 кубической структуры является исходным сырьем в технологии корундовой керамики и получается при термической обработке (500–950 °С) гидраргиллита Al2O3·3Н2О или бемита Al2O3·Н2О. Плотность γ-Al2O3 находится в пределах от 3,47 до 3,66 г/см3. При нагревании до температур выше 1100–1200 °С γ-Al2O3 необратимо переходит в α-Al2O3. Температура перехода зависит от многих факторов, таких как содержание примесей, термическая предыстория и др. Переход этот совершается медленно, начиная с температуры 1100–1200 °С, и полностью завершается при 1450 °С. Переход из γ- в α-форму сопровождается объемным сжатием на 14,3 %.
Третья кристаллическая форма окиси алюминия – β-глинозем – представляет собой условное обозначение группы алюминатов, отличающихся весьма высоким содержанием окиси алюминия. Химический состав этих соединений может быть в общем виде представлен формулами МеО·6Al2O3 и МеО·12Н2О, где МеО может быть СаО, ВаО, SrO и другие, а Ме2О– Na2O, K2O, Li2O и др. Содержание щелочных и щелочноземельных окислов может составлять до 8–10 %. При нагревании до 1600–1700 °С β-глинозем разлагается на α-Al2O3 с выделением соответствующего окисла в газообразном состоянии. Присутствие β-глинозема в обожженном корундовом материале снижает механическую прочность и особенно его электрофизические свойства и поэтому является нежелательным.
Существуют также δ-, η-, θ-, κ-, ρ-, χ-формы глинозема. Их можно рассматривать как неустойчивые термические образования.
Технический глинозем (техническая окись алюминия) является одним из основных видов сырья для производства корундовой керамики. По минералогическому составу технический глинозем представляет собой главным образом γ-Al2O3 с примесями других безводных форм
(α- и β-Al2O3).
Сырьем для получения глинозема служат в основном минералы, содержащие естественные гидраты окиси алюминия, среди которых наибольшее значение имеет боксит. Технический глинозем получают методом Байера, который основан на разложении исходного глиноземистого сырья раствором едкой щелочи с образованием алюмината натрия. Его разлагают, выделяя чистый гидрооксид алюминия, который затем подвергают прокаливанию при высокой (> 1100 °С) температуре. Зерна технического глинозема – это скопления мельчайших кристалли-
28
ков γ-Al2O3 размером менее 0,1 мкм, образующие шарообразную форму, так называемую сферолитную структуру. В процессе производства изделий технический глинозем дополнительно обжигают при более высоких температурах для перевода его в α-форму.
Промышленность выпускает два основных вида электрокорунда – белый и нормальный. Белый электрокорунд (корракс или алунд) получают путем плавки в электрических дуговых печах технического глинозема, а нормальный (черный) путем электроплавки боксита. Содержание Al2O3 в белом электрокорунде составляет 98 % и более, а в нормальном – от 91 до 95 %. В производстве корундовой технической керамики применяют только белый электрокорунд.
Высокочистый и высокодисперсный Аl2O3 получают, используя химические методы:
1)термическое разложение сложного карбоната алюминия, который образуется из квасцов, размер частиц Al2O3 составляет 0,1–0,5 мкм;
2)гидролиз металлоорганических соединений (AlR3 или Al(OR)3, где R – алкил) до Al(OH)3 с последующим его прокаливанием до образования α-Аl2O3;
3)плазмохимический синтез, где в качестве компонента, содержа-
щего алюминий, используется порошок алюминия или хлорид алюминия. В качестве окислителя – кислород или диоксид углерода. Удельная поверхность порошка 30–40 м2/г, размер частиц – меньше 0,1 мкм;
4)газофазное осаждение с применением лазерного нагрева испаряемой мишени, состоящей из химически чистого оксида алюминия;
5)сжигание аэровзвесей алюминиевых порошков. Конечным про-
дуктом является γ-Al2O3 с размером частиц 0,03–0,3 мкм и удельной поверхностью 12,6 м2/г. Форма частиц сферическая. Химический со-
став порошка составляет оксид алюминия (Al2O3) – более 99 %.
Также для получения чистого высокодисперсного порошка оксида алюминия используют метод осаждения, гидротермальный синтез, золь-гель технологию с последующим прокаливанием.
2.2. Диоксид циркония
Диоксид циркония (ZrO2) тугоплавкое соединение с преимущественно ионной межатомной связью. Сырьем для его получения служат природные минералы – бадделеит, представляющий собой природную
29
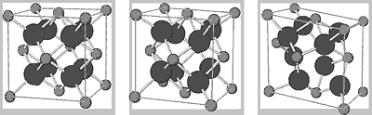
форму ZrO2 и содержащий до 91-97 % оксида; циркон ZrO2·SiO2 (ZrO2 – 67,03 %; SiO2 – 32,97 %). Всем цирконийсодержащим минералам сопутствует трудно отделяемая примесь HfO2, являющаяся химическим аналогом ZrO2.
Диоксид циркония обладает полиморфизмом. Он существует в трех определенных кристаллических модификациях: моноклинной, тетрагональной и кубической; кроме того, под высоким давлением существует орторомбическая форма (рис. 2.2). От температуры плавления (2680 °C) до 2350 °C существует фаза с кубической структурой типа флюорита CaF2. Ниже этой температуры, до 1170 °C (по другим данным – до 1150 °C), равновесной является тетрагональная фаза (плотность 6,106 г/см3), а при более низкой температуре – моноклинная (плотность 5,56 г/см3).
а |
б |
в |
Рис. 2.2. Кристаллические модификации ZrO2: а – кубическая; б – тетрагональная; в – моноклинная
Кубическо-тетрагональный переход является бездиффузионным, характеризуется двумя различными структурами: доменная структура с криволинейными границами и структура с тонкими слоями или линзами. Превращение тетрагональной фазы в моноклинную имеет мартенситный характер и сопровождается значительным объемным эффектом. Моноклинная фаза менее плотная, чем тетрагональная, и объем материала при этом превращении увеличивается на 3–5 %, что приводит к его разрыхлению.
Изменение коэффициента теплового расширения в процессе модификационного превращения носит аномальный характер. Температурные области прямого и обратного переходов при охлаждении и нагреве не совпадают, что проявляется в гистерезисе дилатометрических кривых (рис. 2.3). Поэтому из чистого диоксида циркония получить спеченные изделия невозможно.
30