
книги / Системы, технологии и организация услуг в автомобильном сервисе. Ч. 1
.pdf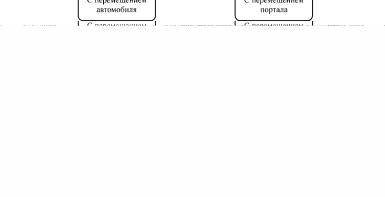
с использованием дополнительной насосной станции. Насосная станция смонтирована на тележке, где расположены емкости с моющими и полировочными составами. При использовании моечных установок низкого давления без насосной станции необходимо механическое воздействие на загрязнения, например с помощью обтирочного материала. На установках высокого давления удаляют загрязнения за счет подачи под давлением струи воздуха и воды. Такие установки эффективны при мойке днища автомобиля перед проведением антикоррозионной обработки.
Рис. 1.14. Укрупненная классификация моечных установок для автомобилей
Вода может быть нагрета с помощью теплообменника с горелкой до температуры 80 °С. При необходимости может подаваться моющий раствор. Установки высокого давления используются при санитарной обработке кузовов, мойке агрегатов и деталей, при уборке помещений. Давление водяной струи составляет 5–150 атм., паровой струи – до 230 атм. Расход воды в моечных установках высокого давления при подаче воды – 750–3000 л/ч, при подаче пара – 375–1400 л/ч.
101
Струйная моечная установка состоит из четырех меха-
низмов, установленных попарно с обеих сторон моечного поста. При въезде на пост находится рамка предварительного смачивания, при выезде – рамка ополаскивания. Автомобиль перемещается своим ходом или на конвейере. Существуют также струйные моечные установки с подвижным порталом для мойки автомобиля снизу. Недостатком струйных моечных установок этого типа является большой расход воды и более низкое качество мойки.
Щеточные и струйно-щеточные моечные установки
(рис. 1.15) более перспективны с точки зрения расхода воды и качества мойки.
Струйно-щеточные моечные установки с подвижным порталом (рис. 1.16) по сравнению с мойками с перемещением автомобилей имеют меньшую производительность. Они представляют собой П-образную рамку, перемещающуюся по направляющим, расположенным вдоль моечного поста,
иимеющую электрический привод. На портале смонтированы несколько вертикальных и одна или две горизонтальных ротационных щетки, устройство для подачи воды, моющего
иполировочного растворов. Мойка автомобиля выполняется за один полный цикл (туда и обратно), сушка и нанесение полировочного покрытия – еще один полный цикл. Производительность таких моек составляет 20–40 авт/ч.
Стационарные щеточные моечные установки имеют производительность 60–90 авт/ч. В комплексе с моечной установкой для кузова автомобиля часто применяется струйнощеточная мойка для дисков колес и мойки автомобиля снизу. Установка для сушки автомобилей часто монтируется непосредственно на портале мойки и представляет собой систему коллекторов, по которым осуществляется обдув автомобиля воздухом.
102
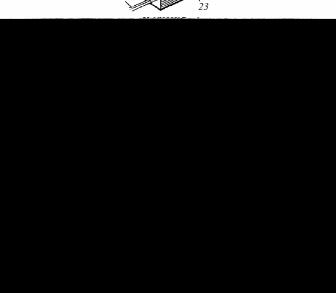
Рис. 1.15. Струйно-щеточная моечная установка для легковых автомобилей: 1 – командоконтроллер; 2 – реверсивный электромотор привода роликов портала; 3, 4, 7 – трубопроводы с форсунками для разбрызгивания воды, моющего раствора и шампуня; 5 – горизонтальная ротационная щетка; 6 – бак с шампунем; 8 – место установки фирменного знака; 9 – бак с синтетическим моющим средством; 10 – поворот распылителя воздуха; 11 – форсунки подачи моющего раствора; 12 – поворотный кронштейн; 13, 15 – электромотор привода горизонтальной щетки; 14 – электропроводка; 16 – вентилятор для сушки автомобиля; 17 – бак с полиролью I; 18 – механизм изменения наклона форсунок; 19 – съемные секционные щетиноносители; 20 – левая ротационная щетка; 21 – бак с полиролью II; 22 – противовес горизонтальной щетки; 23 – устройства для
мойки дисков колес; 24 – рельсовый путь
Для мойки агрегатов и деталей автомобиля использу-
ются специальные моечные машины, представляющие собой камеру, в которую загружают агрегаты и детали, требующие мойки. Очистка поверхностей деталей осуществляется щелочным моющим раствором в холодной или теплой воде.
103
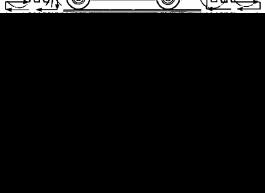
Раствор подается через форсунки, установленные на вращающемся коллекторе. В установке имеется бак для моечного раствора, электронагревательный элемент для подогрева воды. Время полного цикла в моечном шкафу – 10–30 мин в зависимости от степени загрязнения деталей.
Рис. 1 16. Принцип работы струйно-щеточной мойки
После мойки автомобилей вода поступает в систему оборотного водоснабжения, имеющую замкнутый цикл. Проходит многоступенчатая очистка, и вода вновь подается на мойку автомобилей. Добавление свежей воды в систему для компенсации естественной убыли (за счет испарения, утечки и др.) не должно превышать 10–15 % объема использованной воды.
Смазочно-заправочные работы предназначены для уменьшения интенсивности изнашивания и сопротивления в узлах трения, а также для обеспечения нормального функционирования систем, содержащих технические жидкости, смазки. Эти работы составляют значительный объем ТО-1 (16–26 %) и ТО-2 (9–18 %).
Смазочно-заправочные работы состоят в замене или пополнении агрегатов (узлов) маслами, техническими жидко-
104
стями, замене фильтров. Качество этих работ относится
кчислу значимых факторов, влияющих на ресурс узлов и агрегатов. Так, например, у большинства конструкций шаровых опор легковых автомобилей запаса «заводской» смазки хватает на весь период эксплуатации. Однако в тех опорах, где есть отверстие для масленки и смазка производится в режиме ТО-2, ресурс повышается на 20–30 %. Объясняется это тем, что внутрь опоры может проникнуть вода с грязью (абразивом), даже при наличии защитного резинового чехла. Вновь поступающая смазка очищает трущиеся поверхности. Эксплуатация двигателя с уровнем масла ниже допустимого уровня приводит к полному падению давления в системе смазки и выходу из строя вкладышей коленчатого вала. Снижение уровня тормозной жидкости приводит к попаданию воздуха в систему и ее отказу.
Основным технологическим документом, определяющим содержание смазочных работ, является химмотологическая карта (прил. 3), в которой указывают места и количество точек смазки, периодичность смазки, марку масел и смазок, их заправочные объемы.
Составной частью заправочных работ являются промывочные работы. При промывке вымываются продукты износа, что обеспечивает лучшие условия работы деталей и вновь заливаемых жидкостей. Замена, например, всего объема тормозной жидкости в системе (1 раз в год), что приравнивается
кпромывочным работам, увеличивает долговечность резиновых уплотнительных манжет в 1,5–2 раза.
Косвенно к заправочным работам относится подкачка шин. Накачивание шины грузового автомобиля в стационарных условиях должно проводиться в специальном металлическом ограждении, способном защитить обслуживающий персонал от ударов съемными деталями обода в случае их самопроизвольного демонтажа. В дорожных условиях при накачивании шина должна лежать замковым устройством к земле.
105
Норму давления для конкретной модели правильнее всего определить по надписи на боковине шины; на ней может быть указано давление в различных единицах (табл. 1.11) и дано несколько разных его значений в зависимости от нагрузки на шину. При незнании фактической нагрузки лучше ориентироваться на максимальное значение. Если на шине нет обозначения давления, надо руководствоваться каталогами, проспектами завода-изготовителя шины, в которых приводятся рекомендуемые нормы по каждой конкретной модели.
Таблица 1.11 Значения и единицы измерения давления воздуха в шине
Бар (bar) |
кПа (кРа) |
МПа (МРа) |
Индекс (PSI) |
2,1 |
210 |
0,21 |
30 |
2,4 |
240 |
0,24 |
35 |
… |
… |
… |
… |
6,6 |
660 |
0,66 |
95 |
6,9 |
690 |
0,69 |
100 и т.д. |
П р и м е ч а н и е. PSI – значение давления размерностью фунт на дюйм в квадрате (1 PSI = 6,895 кПа).
Оборудование для смазочно-заправочных работ подраз-
деляется на стационарное и передвижное. Подачу масла (жидкостей) обеспечивают нагнетательные устройства, приводимые в действие электроэнергией или сжатым воздухом. Некоторые модели оборудования имеют ручной привод.
На специализированных постах по смазке и заправке (дозаправке) автомобилей целесообразно применение стационарных универсальных механизированных установок. В большинстве случаев они имеют панель, содержащую не-
сколько барабанов с самонаматывающимися |
шлангами |
и раздаточными наконечниками (кранами) для |
моторного |
106
и трансмиссионного масел, пластической смазки, воды, сжатого воздуха. Масла и смазки поступают в раздаточные шланги с помощью пневматических насосов, установленных в резервуарах – стандартных бочках, в которых масла и смазки доставляют на АТП. При подаче жидких масел обеспечивается давление до 0,8 МПа, при подаче пластической смазки – 25–40 МПа. Необходимость столь высокого давления вызвана тем, что при несистематической смазке узлов трения, например шкворневого соединения, продукты износа забивают подводящие каналы. В некоторых странах приходится применять ручные «пробойники» – приспособления, давление в которых создается парой: цилиндр с резьбовым каналом, заполняемым смазкой, и вворачиваемый в него резьбовой шток. Кроме настенного варианта, установка может быть напольного или потолочного расположения. Некоторые модели имеют счетчики расхода масел. Есть отдельные установки для одного конкретного вида смазки. Для моторного масла бывают модели, позволяющие его разогревать. Для пластических смазок выпускают нагнетатели, имеющие индивидуальный привод. Основные отличия разных моделей установок одного назначения состоят в конструкции подающих насосов и резервуаров для масла (смазки).
Для заправки, прокачки или замены рабочей жидкости привода гидравлических тормозов выпускаются приспособления, представляющие собой бак емкостью в несколько литров, из которого тормозная жидкость под действием сжатого воздуха (0,3 МПа) через раздаточный шланг и резьбовой штуцер подается в главный тормозной цилиндр. С таким приспособлением замену тормозной жидкости или прокачку системы может проводить один исполнитель. Некоторые приспособления этого типа позволяют проверять качество тормозной жидкости.
Для нанесения жидких противокоррозионных покрытий на нижние поверхности и оперение автомобиля, в полости
107
коробчатого типа выпускаются установки, распыляющие (с давлением 0,5–1,0 МПа) противокоррозионные эмульсии (с воздухом). Вязкость покрытия 70–150 мм2/с.
Крепежные работы предназначены для обеспечения нормального состояния (затяжки) резьбовых соединений. В объеме ТО в зависимости от вида ТО и типа подвижного состава эти работы составляют 25–30 %. Так, у автомобиля КамАЗ 3,5 тыс. резьбовых соединений. При ТО-1 необходимо проверить и, если требуется, подтянуть несколько десятков соединений. При ТО-2 это количество значительно возрастает. При текущем ремонте большинство сборочноразборочных операций связано с крепежными работами. Поэтому применение правильных приемов по обслуживанию резьбовых соединений повышает эксплуатационную надежность автомобиля в целом, облегчает труд рабочих, значительно снижает трудоемкость этих работ при вторичном их выполнении.
Резьбовые соединения обеспечивают сборку узлов как посредством резьбы, находящейся непосредственно на детали (свеча зажигания, шаровые пальцы шарниров рулевого привода, регулировочные винты в механизме газораспределения), так и при помощи крепежных деталей – болтов, шпилек, гаек специального и общего назначения. Специальные применяют в ответственных узлах (шатунные болты, шпильки крепления головки цилиндров) или там, где без них технология сборки-разборки усложнится (например, квадратные гайки, устанавливаемые в пазы, где они удерживаются от прокручивания). Ответственные крепежные соединения имеют мелкий шаг резьбы и защитное покрытие.
Неисправности резьбовых соединений – это ослабление предварительной затяжки, повреждения и срыв резьбы. Ослабление резьбовых соединений и их самоотворачивание нарушают регулировку и приводят к ухудшению эксплуатационных свойств автомобиля, к потере герметичности уплотне-
108
ний, к возрастанию динамических нагрузок на детали и их поломкам. Самоотворачивание происходит в основном из-за вибраций, в результате чего снижается сила трения в самой резьбе и на контактном торце гайки или головки болта. Быстрому ослаблению креплений подвержены стартер, генератор, топливный насос, карданный вал. Вероятность самоотворачивания резко возрастает, если перед сборкой резьба была повреждена. Прилагаемое при затяжке усилие в этом случае приходилось в основном на трение в самой резьбе. Подтягивание резьбового соединения без необходимости нарушает его стабильность и снижает величину первоначального натяга. Крепежные детали, использовавшиеся 10–15 раз, сохраняют предварительную затяжку в 2–4 раза хуже, чем новые.
При выполнении требуемых объемов крепежных работ при ТО-2, например, у двигателя к 80–100 тыс. км пробега ослабевает затяжка почти у 15 % резьбовых соединений.
Срыв резьбы при ремонтах является также распространенным дефектом. Основная причина этого – затяжка соединений с усилиями, значительно превышающими нормативы технических условий на сборку.
Затянутую резьбу можно восстановить специальным режущим инструментом – плашками, метчиками. Оборвавшуюся часть болта или шпильки из резьбового отверстия удаляют сверлом меньшего диаметра.
Сборка резьбовых соединений состоит в создании в них предварительной затяжки с помощью ключей или гайковертов. Существует несколько методов контроля момента затяжки. Наиболее распространенный из них – при помощи тарированных динамометрических ключей (рукояток). В инструкциях заводов-изготовителей, в технологических картах указаны моменты затяжки для наиболее ответственных узлов.
Превышение момента затяжки может повредить (сорвать) резьбу или вызвать текучесть материала болта (шпиль-
109
ки) и ослабление затяжки. При применении динамометрических ключей надо иметь в виду, что указываемая на них величина затяжки также учитывает силу трения в резьбовом соединении, которая существенно зависит от состояния резьбы (ее загрязненности, смятия).
Обслуживание резьбовых соединений требует соблюдения ряда условий. Длина ввертываемой части болта для стальной детали должна быть от одного до двух диаметров резьбы. Увеличивать глубину ввертывания бесполезно, так как основную нагрузку воспринимают только несколько витков резьбы, расположенных у входной поверхности детали. Длинные болты сложнее отворачивать, особенно при их коррозии. При наворачивании гайки болт выбирают по длине таким, чтобы он выступал из гайки не более чем на два-три витка резьбы. Перед сборкой резьба должна быть очищена, проверена и смазана.
Особой осторожности требуют детали резьбового соединения, изготовленные из разных металлов, например свеча зажигания и алюминиевая головка блока цилиндров, так как резьба на более мягком металле может быть повреждена.
Соединения, обеспечивающие герметичность топливо-, воздухо-, водо- и маслопроводов, затягиваются плавно. Последние 60–90° поворота детали надо делать без рывков, за один прием. Надежность этих соединений проверяется визуально или на слух. Подтяжка без необходимости может вызвать потерю герметичности.
Если узел имеет уплотнительные прокладки и собирается из разукомплектованных крепежных деталей, предварительно узел следует обжать с моментом, в 1,1 раза большим предусмотренного техническими условиями усилием, затем ослабить гайки (болты) и повторно затянуть их с требуемым моментом. В противном случае неравномерность затяжки может достигнуть 25 %.
110